Exploring the World of Wafer Electronics: From Fabrication to Application
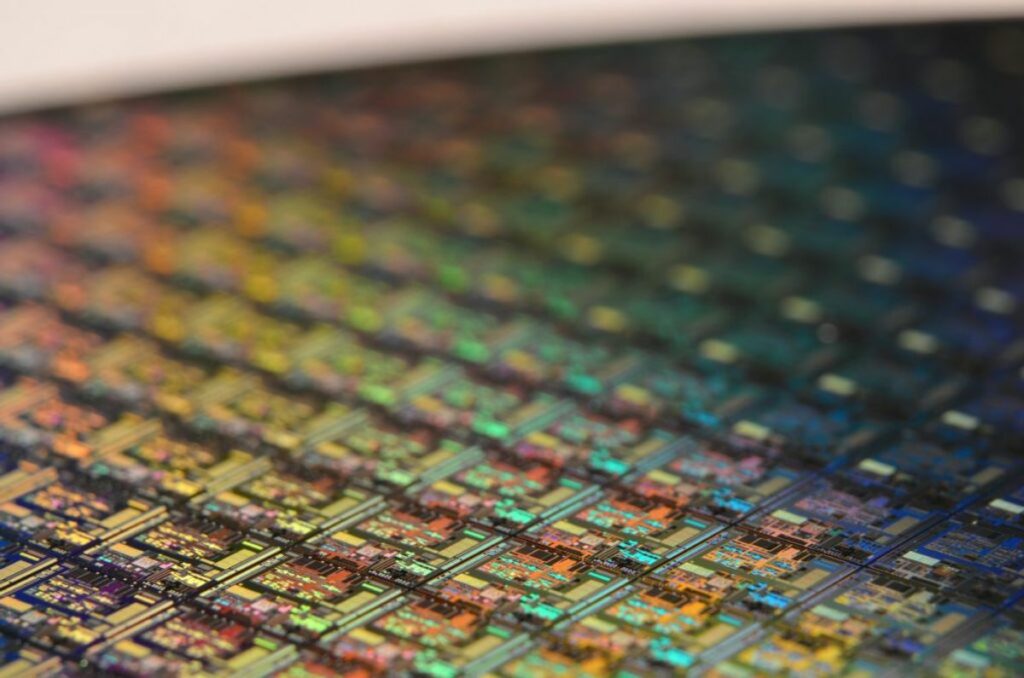
Wafer electronics represent the backbone of modern technology, with their fabrication and application spanning numerous industries and devices. This article delves into the intricate world of wafer electronics, exploring the evolution of fabrication techniques, the integration of cutting-edge materials and technologies, sophisticated packaging methods, and the diverse applications in today’s high-tech landscape. We also examine the future trends and challenges that lie ahead for this critical field.
Key Takeaways
- The production of silicon wafers and advancements in lithography have significantly evolved, enabling the miniaturization and increased complexity of electronic devices.
- Innovative materials and technologies such as nanotechnology and 3D printing are revolutionizing wafer design and functionality.
- The dicing process and new packaging methods are crucial for integrating wafers into final chip products, with thermal management playing a key role in maintaining performance.
- Wafer electronics are integral to consumer electronics, medical devices, and the automotive and aerospace industries, showcasing their versatility and reliability.
- The semiconductor industry faces the challenge of producing smaller, faster, and more efficient chips while addressing sustainability and adapting to the global demand for electronics.
The Evolution of Wafer Electronics Fabrication
Understanding Silicon Wafer Production
The production of silicon wafers is the foundational step in the fabrication of wafer electronics. Silicon is the second most abundant element in the Earth’s crust, and its semiconductor properties make it the preferred material for electronic devices. The process begins with the purification of silicon, which is then melted and formed into cylindrical ingots. These ingots are subsequently sliced into thin discs, known as wafers.
The quality of a silicon wafer is critical to the performance of the final electronic device. To ensure high purity and structural integrity, the production process includes several key steps:
- Purification: Silicon must be converted into a high-purity form, polysilicon.
- Crystal Growth: Polysilicon is melted in a crucible and a seed crystal is introduced to grow a silicon ingot.
- Slicing: The ingot is sliced into wafers using a diamond saw or a wire saw.
- Polishing: Wafers are polished to achieve a mirror-like finish, which is essential for the subsequent lithography steps.
Each of these steps must be meticulously controlled to produce wafers that meet the stringent requirements of modern electronics. As the demand for smaller and more powerful devices grows, the precision and quality of silicon wafer production continue to be of paramount importance.
Advancements in Lithography Techniques
The relentless pursuit of miniaturization in semiconductor manufacturing has led to significant advancements in lithography techniques. These techniques are crucial for defining the intricate patterns on silicon wafers that become the transistors and circuits of electronic devices.
One of the most promising developments is the evolution of ultraviolet lithography (UVL). Traditional UVL has been pushed to its limits, and new methods have emerged to enhance its resolution. For instance, evanescent near-field lithography (ENFOL) represents a leap forward by manipulating the proximity between the lithography stencil and the wafer, achieving unprecedented precision in nanostructure creation.
The table below summarizes some of the key advancements in lithography techniques:
Technique | Description | Impact |
---|---|---|
ENFOL | Utilizes near-field effects to improve resolution | Enhances precision |
Immersion Lithography | Uses a liquid medium to increase the refractive index | Extends UVL capabilities |
Extreme Ultraviolet (EUV) | Employs shorter wavelengths for finer details | Pushes the boundaries of miniaturization |
These innovations not only refine the manufacturing process but also pave the way for the next generation of electronic components, which are smaller, faster, and more efficient.
The Role of Cleanrooms in Chip Manufacturing
The significance of cleanrooms in semiconductor manufacturing cannot be overstated. These highly controlled environments are essential for minimizing the presence of dust, airborne microbes, aerosol particles, and chemical vapors, all of which can cause defects in the delicate process of chip fabrication.
Cleanrooms are classified based on the cleanliness level of the air, which is determined by the number of particles per cubic meter at a specified particle size. The International Organization for Standardization (ISO) provides a standard for these classifications, known as ISO 14644-1. For instance, an ISO 5 cleanroom allows for 3,520 particles of 0.5 micrometers in size per cubic meter of air.
The benefits of cleanrooms are numerous, including the ability to boost productivity by decreasing contamination and minimizing flaws in the final product. This leads to higher yields of functional chips and a reduction in costly wastage. The table below summarizes the key ISO cleanroom classifications and their corresponding allowed particle count:
ISO Class | Particles/m^3 (≥0.1 µm) | Particles/m^3 (≥0.5 µm) |
---|---|---|
ISO 1 | 10 | 2 |
ISO 5 | 100,000 | 3,520 |
ISO 8 | 3,520,000 | 832,000 |
Maintaining these stringent conditions requires sophisticated air filtration systems, along with strict protocols for personnel and equipment entering and exiting the space. The investment in cleanroom technology reflects the critical nature of purity in semiconductor production and the ongoing pursuit of perfection in the electronics industry.
Cutting-Edge Materials and Technologies
Exploring New Semiconductor Materials
The relentless pursuit of enhanced performance and efficiency in electronics has led to the exploration of new semiconductor materials beyond the traditional silicon. Materials such as Silicon Germanium (SiGe) and Sapphire (Al2O3) are being investigated for their unique properties that could potentially revolutionize wafer electronics.
Silicon Germanium, for instance, offers higher carrier mobility, which is crucial for faster transistor switching speeds. Sapphire, on the other hand, is known for its exceptional thermal and electrical insulation properties, making it an ideal substrate for high-frequency and high-power devices. The table below summarizes some of the key attributes of these materials:
Material | Advantages | Applications |
---|---|---|
SiGe | Higher carrier mobility | High-speed electronics |
Sapphire | Excellent insulation | High-frequency devices |
As the industry continues to innovate, the adoption of these new materials could lead to the development of devices that are not only faster and more powerful but also more energy-efficient. This shift is poised to have a significant impact on a wide range of applications, from consumer electronics to advanced medical devices.
Nanotechnology in Wafer Electronics
The integration of nanotechnology in wafer electronics marks a transformative era in semiconductor manufacturing. By manipulating materials at the atomic and molecular scale, engineers are able to create structures that are significantly smaller, more efficient, and more powerful than ever before. This miniaturization trend is not only enabling the production of ultra-compact devices but also enhancing their performance and energy efficiency.
Nanotechnology’s role extends beyond just the creation of smaller components; it also introduces new properties and functionalities to electronic devices. For instance, the use of carbon nanotubes and graphene in wafers has shown promising results in terms of electrical conductivity and thermal management. These materials, along with other nanoscale innovations, are paving the way for the next generation of electronics.
The application of nanotechnology in wafer electronics is diverse, impacting various sectors. Here’s a brief overview of its influence:
- Consumer Electronics: Nanoscale components are crucial for the ongoing miniaturization of consumer devices.
- Medical Devices: Enhanced precision and sensitivity in medical diagnostics and treatment.
- Energy Storage: Improved battery life and performance through nanomaterials.
- Telecommunications: Faster and more reliable communication with nanoelectronics.
As the industry continues to explore the potential of nanotechnology, the challenges of mass production and integration with existing manufacturing processes remain. However, the benefits of this technology are clear, and its continued development is essential for the advancement of wafer electronics.
The Impact of 3D Printing on Wafer Design
The advent of 3D printing technology has ushered in a new era for wafer electronics, enabling more complex and precise designs that were previously unattainable. 3D printing allows for the addition of intricate structures and layers to wafers, which can lead to enhanced performance and functionality of electronic devices.
Key benefits of 3D printing in wafer design include:
- Rapid prototyping of complex geometries
- Customization for specific applications
- Reduction in material waste
- Shortened development cycles
Despite these advantages, the integration of 3D printing into wafer design also presents challenges. Ensuring the compatibility of materials and the reliability of printed structures are critical areas that require ongoing research and development. As the technology matures, it is expected to become a staple in the fabrication of next-generation wafer electronics.
Integration and Packaging Techniques
From Wafers to Chips: The Dicing Process
The transformation from silicon wafers to individual chips is a critical phase in semiconductor manufacturing, known as wafer dicing or die singulation. This process involves cutting the wafer into many small square or rectangular pieces, each becoming a separate chip or die. The precision of wafer dicing is paramount, as it directly affects the yield, which is a measure of the number of usable chips obtained from a single wafer.
Wafer dicing employs various methods, such as scribing and breaking, sawing, or laser cutting. Each technique has its own set of advantages and is chosen based on the material properties and the required precision. The dicing process must be meticulously controlled to minimize damage to the wafer and ensure the highest possible yield.
- Scribing and Breaking: A less expensive method suitable for thinner wafers.
- Sawing: The most common method, offering high precision for a wide range of wafer thicknesses.
- Laser Cutting: Provides the highest precision and is ideal for complex shapes or materials that are difficult to cut.
Innovations in Chip Packaging and Integration
The landscape of chip packaging and integration has seen remarkable transformations, with innovations driving the semiconductor industry forward. Advanced chip packaging is no longer confined to traditional methods; it’s time to think outside of the box. By connecting multiple chips horizontally and vertically, we can pack more transistors into a single package, enhancing performance while reducing space.
One of the key developments in this area is the emergence of multi-die integration techniques such as 2.5D and 3D IC packaging. These methods allow for a higher density of interconnects and the ability to integrate heterogeneous systems. Here’s a brief overview of the different packaging types:
- 2.5D IC Packaging: Chips are placed side by side on an interposer, which is then connected to a substrate.
- 3D IC Packaging: Chips are stacked vertically, with connections made through silicon vias.
These advancements not only improve electrical performance but also contribute to significant size reduction, which is crucial for modern portable devices. As we continue to push the boundaries of what’s possible in chip design, the role of innovative packaging and integration becomes increasingly vital.
Thermal Management in High-Density Electronics
As electronic devices become more powerful and compact, thermal management becomes a critical aspect of semiconductor packaging. Advanced materials are key to improving thermal management, allowing for the packaging of thinner microelectronic components. These materials help dissipate heat more efficiently, ensuring that devices operate within safe temperature ranges and maintain performance reliability.
Effective thermal management strategies include both passive and active cooling techniques. Passive cooling involves the use of heat sinks and thermal interface materials, while active cooling may employ fans or liquid cooling systems. Below is a list of common thermal management solutions used in high-density electronics:
- Heat sinks and spreaders
- Thermal interface materials (TIMs)
- Vapor chambers and heat pipes
- Fans and blowers
- Liquid cooling systems
The challenge lies in integrating these solutions into increasingly smaller spaces without compromising on their effectiveness. As the industry continues to push the boundaries of miniaturization, the development of new materials and innovative cooling designs remains a top priority.
Applications of Wafer Electronics in Modern Devices
Wafer Electronics in Consumer Electronics
The ubiquity of silicon wafer technology in consumer electronics is a testament to its fundamental role in modern devices. These wafers serve as the building blocks for semiconductors, which are found in everything from smartphones to home appliances. As the demand for smarter, more connected gadgets grows, so does the reliance on high-quality wafer silicon to deliver the performance consumers expect.
Consumer electronics have evolved to offer an array of features that were once unimaginable, largely thanks to advancements in wafer electronics. The integration of these technologies has enabled devices to become more compact, efficient, and powerful. Below is a list of common electronic devices that utilize silicon wafers:
- Smartphones and tablets
- Laptops and desktop computers
- Smart home devices (e.g., thermostats, security cameras)
- Wearables (e.g., smartwatches, fitness trackers)
- Gaming consoles and virtual reality headsets
As the industry continues to innovate, the applications of wafer electronics in consumer products are set to expand even further. This progression poses both opportunities and challenges for manufacturers, who must balance the push for miniaturization with the need for increased functionality and energy efficiency.
The Role of Wafers in Medical Device Technology
In the realm of medical technology, silicon wafers play a pivotal role, serving as the foundation for a myriad of devices that enhance and save lives. These wafers are crucial in fabricating imaging sensors used in devices such as X-ray detectors, computed tomography (CT) scanners, and magnetic resonance imaging (MRI) machines, providing the high-resolution images that are essential for accurate diagnoses.
The precision and reliability of wafer electronics have enabled the miniaturization of medical devices, leading to less invasive procedures and quicker recovery times for patients. For instance, wafer-based microelectromechanical systems (MEMS) are now integral components in advanced drug delivery systems and implantable devices.
Here is a brief overview of the medical applications of wafer electronics:
- Imaging: High-resolution sensors for diagnostics
- Monitoring: Continuous health tracking with wearable technology
- Treatment: Targeted drug delivery and precision surgery
- Research: Enhanced tools for medical research and development
As the medical field continues to evolve, the integration of wafer electronics is set to expand, with new applications emerging in biotechnology and personalized medicine.
Automotive and Aerospace: High-Reliability Applications
In the realms of automotive and aerospace, the demand for high-reliability wafer electronics is paramount. These industries require components that can withstand extreme conditions, such as high temperatures, vibration, and radiation, while maintaining precision and performance.
The integration of wafer electronics into these sectors has led to significant advancements in safety and functionality. For instance, in the automotive industry, wafer-based sensors are crucial for advanced driver-assistance systems (ADAS) and autonomous vehicles. Similarly, aerospace applications leverage these electronics for navigation, communication, and monitoring systems.
Here’s a glimpse into the critical applications of wafer electronics in automotive and aerospace:
- Automotive: ADAS, Engine Control Units (ECUs), Infotainment Systems
- Aerospace: Flight Control Systems, Satellite Communications, Avionics
As technology progresses, the challenge lies in scaling these high-reliability applications while managing costs and complexity. The industry continues to innovate, seeking new materials and manufacturing techniques to meet the evolving demands.
Future Trends and Challenges in Wafer Electronics
The Push for Smaller, Faster, More Efficient Chips
The semiconductor industry is relentlessly pursuing the miniaturization of electronic components. Moore’s Law, which predicts the doubling of transistors on a chip approximately every two years, has been a guiding principle for this advancement. However, as we approach the physical limits of silicon-based technology, the challenge intensifies.
Innovations in chip design and manufacturing are crucial to overcoming these barriers. For instance, the use of new materials such as gallium nitride (GaN) and silicon carbide (SiC) has opened up possibilities for chips that operate at higher frequencies and temperatures, while consuming less power.
The table below highlights some of the recent advancements in chip technology:
Year | Breakthrough | Impact |
---|---|---|
2021 | Introduction of 3nm process technology | Increased transistor density |
2022 | Development of 2D materials for transistors | Enhanced electrical properties |
2023 | Commercialization of GaN-based chips | Improved power efficiency |
As we continue to push the boundaries, the focus is not only on making chips smaller but also on enhancing their performance and energy efficiency. This relentless innovation cycle is what drives the electronics industry forward, ensuring that the devices of tomorrow are faster, smarter, and more capable than ever before.
Sustainability and Recycling in the Semiconductor Industry
The semiconductor industry is facing a pivotal moment in its approach to sustainability and recycling. The question of whether semiconductors can truly be recycled is not just a matter of scientific possibility but also of economic and environmental practicality. The process of recycling semiconductors involves several complex steps, from the deconstruction of electronic components to the safe recovery of valuable materials.
Efforts to improve the sustainability of semiconductor manufacturing are ongoing. These include reducing waste during the fabrication process, finding ways to repurpose scrap material, and developing new methods for reclaiming precious metals. The table below outlines some of the key materials recovered from semiconductor recycling:
Material | Use in Electronics | Recycling Process |
---|---|---|
Silicon | Transistors, chips | Refinement, purification |
Gold | Conductive layers | Chemical separation |
Copper | Wiring, connections | Melting, reshaping |
As the industry evolves, the challenges and opportunities of recycling semiconductors become more apparent. Companies are exploring innovative designs and builds that facilitate easier recycling, while researchers are looking into the future of sustainable semiconductor technologies.
Emerging Markets and the Global Demand for Electronics
The global demand for wafer electronics is surging, with emerging markets playing a pivotal role in this expansion. Economic growth in these regions is driving an increased need for consumer electronics, medical devices, and automotive components, all of which rely heavily on semiconductor technology.
Emerging markets are not only consumers but also becoming significant producers of electronic components. Countries like China and India are investing heavily in semiconductor fabrication facilities, aiming to reduce reliance on imports and boost their own technological ecosystems.
The following table highlights some of the emerging markets contributing to the global demand for electronics:
Country | Region | Notable Contributions to Electronics Market |
---|---|---|
China | Asia | Massive semiconductor manufacturing base |
India | Asia | Rapidly growing consumer electronics sector |
Brazil | South America | Expanding automotive and medical industries |
South Africa | Africa | Developing technology and innovation hubs |
As these markets continue to develop, the semiconductor industry faces the challenge of meeting the rising demand while ensuring sustainability and innovation. The future of wafer electronics will be shaped by how effectively the industry can adapt to these dynamic market forces.
Conclusion
In summary, the journey through the world of wafer electronics has revealed the intricate processes of fabrication and the diverse applications that shape our modern technological landscape. From the precision required in manufacturing to the innovative uses in various industries, wafer electronics are at the heart of advancements in computing, communication, and beyond. As we’ve explored the complexities and the potential of these thin slices of semiconductor material, it’s clear that the future holds even more exciting possibilities for wafer electronics to revolutionize the way we interact with technology. The continuous evolution of this field promises to bring forth new challenges and opportunities, ensuring that wafer electronics will remain a pivotal component of our digital world.
Frequently Asked Questions
What is wafer electronics fabrication and how has it evolved?
Wafer electronics fabrication is the process of creating integrated circuits on semiconductor wafers, typically silicon. The evolution of this process has seen significant advancements in silicon wafer production, lithography techniques, and the use of cleanrooms to minimize contamination and improve yield.
What new materials are being explored for semiconductor applications?
Researchers are exploring a variety of new semiconductor materials, including gallium nitride (GaN), silicon carbide (SiC), and graphene, to improve performance and enable new applications. These materials offer superior properties such as higher thermal conductivity and greater electron mobility.
How is nanotechnology impacting wafer electronics?
Nanotechnology is revolutionizing wafer electronics by enabling the creation of structures at the nanoscale, which improves the performance and efficiency of electronic devices. It has facilitated the development of smaller, faster, and more energy-efficient components.
What role does 3D printing play in wafer design?
3D printing, also known as additive manufacturing, is being used to prototype and produce complex wafer designs with high precision. It allows for rapid iteration and customization of wafer structures, which can accelerate the development process and reduce costs.
How are wafer electronics integrated into modern medical devices?
Wafer electronics are critical in modern medical devices for diagnostics, monitoring, and treatment. They are used in a variety of applications, including wearable health monitors, implantable devices, and sophisticated imaging systems, due to their reliability and precision.
What are the challenges faced by the semiconductor industry in terms of sustainability?
The semiconductor industry faces challenges such as the high energy consumption of fabrication facilities, the use of hazardous materials, and the difficulty of recycling electronic waste. There is a growing push for more sustainable practices, including reducing energy use, minimizing waste, and improving recycling methods.