Finding a Reliable Wafer Supplier: A Comprehensive Guide
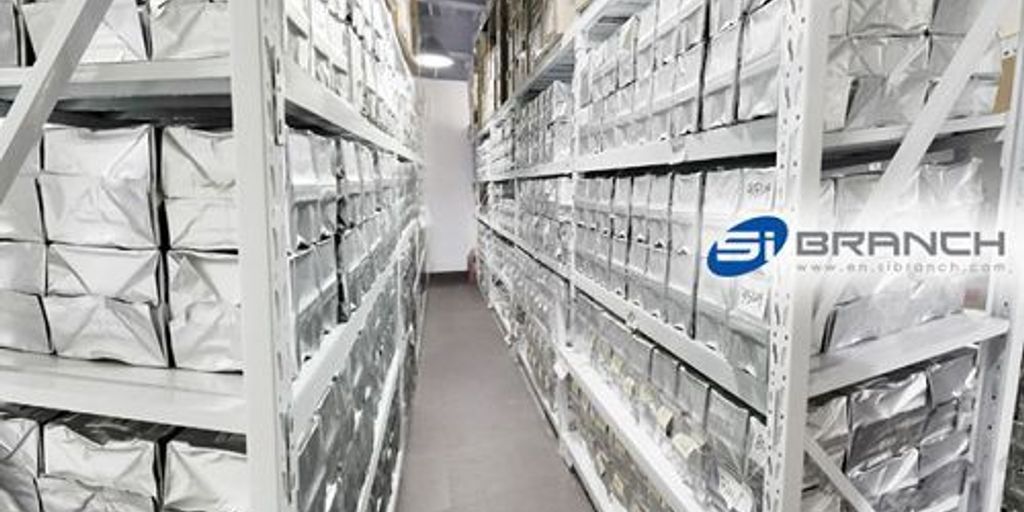
Finding a reliable wafer supplier is very important for businesses that need high-quality silicon wafers. Picking the right supplier means looking at many different factors to make sure they can meet your needs. It might seem like a lot of work, but having a good wafer supplier can really help your business run smoothly. This guide will help you choose a reliable wafer supplier.
Key Takeaways
- Good communication and strong inventory management are key traits of a reliable wafer supplier.
- Checking the size and capacity of a supplier helps ensure they can handle big orders and stay financially stable.
- Quality assurance practices, like certifications and inspections, are important to check a supplier’s reliability.
- Choosing the right wafer depends on the material and features needed for your specific use.
- Customer feedback is crucial for understanding the supplier’s performance and making a good choice.
Key Qualities of a Reliable Wafer Supplier
Finding a reliable wafer supplier is essential for ensuring the quality and consistency of your products. Here are some key qualities to look for:
Evaluating Supplier Size and Capacity
When choosing a wafer supplier, it’s important to understand their size and capacity. This helps ensure they can meet your needs consistently and efficiently.
Assessing Quality Assurance Practices
Certification Standards
When choosing a wafer supplier, it’s crucial to check their certification standards. Look for suppliers that comply with ISO 9001 Quality Management System or other industry-standard certifications. This not only ensures the quality of the wafers but also reflects the company’s commitment to high standards.
Inspection Processes
A reliable supplier will have thorough inspection processes in place. Regular inspections and equipment calibration are key to maintaining accuracy and consistency. Tools like wafer probers and probe stations are used to assess each wafer’s performance. These practices are the foundation of quality control.
Continuous Improvement
Suppliers should continually invest in improving their quality assurance practices. This includes leveraging customer feedback and investing in automation to reduce defect rates. By monitoring technology stability and keeping track of variations during the manufacturing process, suppliers can predict and address potential issues before they become problems.
Selecting the Right Wafer for Your Needs
Choosing the right wafer for a specific task is a crucial decision. Different applications need wafers with different properties. When selecting a wafer, consider factors like what material the wafer is made of and its specific features. These details are important because they affect how well the wafer will work in a particular application.
Importance of Customer Feedback
Customer feedback is crucial for understanding a supplier’s reliability and product quality. It helps you determine if your clients are satisfied with your service and detect areas where you should improve.
Steps in Wafer Testing
Initial Inspection
The first step in wafer testing is the initial inspection. Here, each wafer is carefully checked for any visible flaws or damage. Technicians look for cracks, scratches, or any irregularities on the surface. This step is crucial as physical defects can limit the performance of the wafer during further testing.
Functional Testing
Next, the wafers undergo functional testing. This involves a series of tests to ensure that the semiconductor devices on the wafer are working correctly. Various methods, such as electrical testing, are used to verify device functionality. This step is vital to confirm that the wafers meet the required specifications.
Final Quality Check
The last step is the final quality check. This is a thorough review to ensure that all previous tests were successful and that the wafers are ready for the next stage of production. This step often includes a detailed analysis using advanced techniques like Scanning Electron Microscopy (SEM) to provide detailed imaging of wafer surfaces.
By following these steps, manufacturers can ensure that each wafer meets the high standards expected in today’s technology.
Factors to Consider When Buying Wafer Processing Equipment
When buying wafer processing equipment, there are several important factors to keep in mind. Choosing the right equipment can greatly impact the quality, consistency, and cost of your final product. Here are some key considerations:
Equipment Compatibility
Ensure that the equipment you choose is compatible with your existing systems and processes. This helps avoid any disruptions in your production line and ensures smooth integration.
Cost and Budget
It’s essential to balance the cost of the equipment with your budget. While high-end equipment may offer advanced features, it’s important to assess whether these features are necessary for your specific needs. Consider both the initial purchase price and the long-term maintenance costs.
Supplier Support and Maintenance
Reliable supplier support and maintenance services are crucial for minimizing downtime and ensuring the longevity of your equipment. Look for suppliers who offer comprehensive support packages, including regular maintenance, troubleshooting, and quick response times for repairs.
Conclusion
Finding a reliable wafer supplier is essential for the success of your business. By carefully evaluating potential suppliers on factors like communication, inventory management, size, capacity, and quality assurance, you can make a well-informed choice. Although the process may take time and effort, the benefits of partnering with a dependable supplier are worth it. A good supplier will help ensure the quality and consistency of your products, leading to smoother operations and long-term growth. Remember, the right supplier is not just a vendor but a valuable partner in your business journey.
Frequently Asked Questions
Why is finding a reliable wafer supplier important?
Finding a reliable wafer supplier is crucial because it ensures you get high-quality silicon wafers that meet your business needs. A dependable supplier helps maintain smooth operations and boosts your business’s success.
What qualities should I look for in a wafer supplier?
Look for proactive communication, robust inventory management, and strong quality assurance practices. These qualities help ensure the supplier can meet your demands and provide consistent, high-quality products.
How can I evaluate a supplier’s size and capacity?
You can evaluate a supplier’s size and capacity by understanding their scale, assessing their production capabilities, and checking their financial stability. This helps ensure they can handle your orders efficiently.
What are some key quality assurance practices to consider?
Key quality assurance practices include certification standards, thorough inspection processes, and a commitment to continuous improvement. These practices help ensure the supplier delivers high-quality wafers consistently.
How do I choose the right wafer for my needs?
When choosing a wafer, consider the material, application-specific features, and supplier recommendations. These factors help ensure the wafer meets the requirements of your specific application.
Why is customer feedback important when selecting a wafer supplier?
Customer feedback provides insights into the supplier’s reliability and product quality. Gathering reviews and testimonials, analyzing customer satisfaction, and incorporating feedback into your decision-making process can help you choose the best supplier.