From Ingot to Electronics: Outlining the Silicon Wafer Manufacturing Process
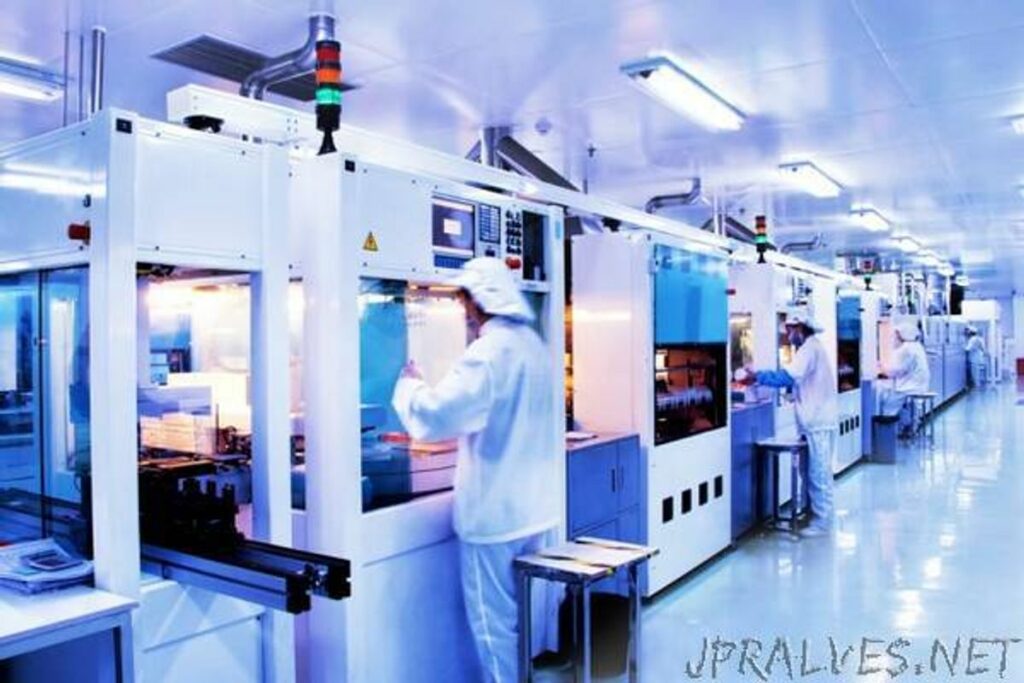
The journey of silicon from its raw form to becoming the backbone of modern electronics is a fascinating and intricate process. Silicon wafers are the fundamental substrates used in semiconductor devices, which are essential components of virtually all electronic gadgets today. This article delves into the comprehensive stages of silicon wafer manufacturing, detailing each step from the initial mining of quartz to the final production of high-precision electronic chips. Understanding this process not only highlights the marvels of modern manufacturing but also underscores the critical role of material science in advancing technology.
Key Takeaways
- Silicon wafers are crucial for semiconductor devices, serving as the platform for microchip production.
- The manufacturing process begins with mining quartz and ends with the creation of intricate electronic circuits.
- High levels of purity are paramount throughout the process, with several stages dedicated to achieving and maintaining this purity.
- Advanced techniques such as the Siemens process, crystal growth, and chemical mechanical planarization are integral to producing functional wafers.
- The transformation from a simple silicon wafer to a complex chip involves precise doping, layering, patterning, and quality control.
Understanding the Basics of Silicon Wafer Production
The Role of Silicon in Electronics
Silicon stands at the heart of the electronics industry, serving as the foundational material for a vast array of devices. Its unique properties as a semiconductor make it ideal for controlling electrical currents in applications ranging from tiny microprocessors to large power devices. Silicon’s ability to conduct electricity better than an insulator, yet not as well as a pure conductor, allows for the precise control necessary in modern electronics.
The versatility of silicon stems from its ability to be doped with impurities to alter its electrical properties. This process enables the creation of p-type or n-type silicon, each with distinct conductivity characteristics essential for creating diodes, transistors, and integrated circuits. Below is a list of key reasons why silicon is the material of choice in the electronics sector:
- Abundant availability in the Earth’s crust
- Thermal stability and durability
- Capability to form an oxide layer, useful for insulation
- Ease of fabrication into wafers and subsequent processing
Understanding the pivotal role of silicon in electronics is crucial for grasping the importance of the wafer manufacturing process that follows.
Purity Requirements for Semiconductor Manufacturing
The manufacturing of semiconductors demands an exceptionally high level of purity in silicon wafers, as even minute impurities can significantly affect the electrical properties of the final electronic devices. The required purity level for semiconductor-grade silicon is typically 99.9999% (6N purity), although for certain advanced applications, the purity might need to be as high as 11N (99.999999999%).
To achieve such high purity levels, manufacturers must control contamination throughout the production process. This includes not only the initial raw materials but also the environment in which the wafers are processed. Below is a list of common impurities and their maximum allowable concentrations in parts per billion (ppb):
- Carbon: < 0.5 ppb
- Oxygen: < 1.0 ppb
- Metals (e.g., iron, copper, gold): < 0.01 ppb
Maintaining the purity of silicon wafers is a complex challenge that requires sophisticated purification techniques and rigorous quality control measures. The industry’s relentless pursuit of purity is driven by the ever-increasing demands of modern electronics for faster, smaller, and more reliable components.
Overview of the Wafer Fabrication Process
The manufacturing process of silicon wafers is intricate and requires precise control at every stage to ensure the quality and purity necessary for semiconductor applications. After the initial stages of mining and refining, the production journey continues with the transformation of raw silicon into a form suitable for electronics.
- Mining and Refining: Extraction of raw silicon from quartz and refining it into metallurgical-grade silicon.
- Purification: Converting metallurgical-grade silicon into polysilicon through chemical processes.
- Crystal Growth: Melting polysilicon and growing single-crystal ingots.
- Slicing: Cutting the ingots into thin wafers ready for further processing.
Each step is critical, and the outcome of the process is a testament to the power of silicon wafers in modern technology. The wafers’ journey from a raw material to the foundation of electronic devices is a marvel of engineering and chemistry.
Step-by-Step Guide to Silicon Wafer Manufacturing
Mining and Refining: From Quartz to Metallurgical-Grade Silicon
The journey of silicon wafer manufacturing begins with the extraction of silicon from its most common form: quartz. Silicon is a fundamental element in the production of semiconductors, and it all starts with mining quartz or quartzite. These raw materials are then subjected to a series of processes to refine them into metallurgical-grade silicon (Mg-Si), which is typically about 98-99% pure.
The refining process involves heating the quartz in a high-temperature furnace along with carbon materials, such as coal or wood chips. This reduction process removes oxygen from the silicon dioxide (quartz), resulting in the production of carbon dioxide and molten silicon. Once the molten silicon cools and solidifies, it forms metallurgical-grade silicon, which serves as the base material for further purification.
- Metallurgical-grade silicon is the starting point for semiconductor manufacturing.
- The reduction process is crucial for removing impurities.
- The quality of the final product is highly dependent on this initial stage.
Purification Process: Creating Polysilicon
The transition from metallurgical-grade silicon to polysilicon marks a critical step in the silicon wafer manufacturing process. This stage involves purifying the silicon until it reaches semiconductor quality, which is essential for electronic applications due to its superior electrical properties.
Several methods exist for polysilicon production, but a common approach is the Siemens process. This method employs chemical reactions at high temperatures to distill the material into a form that’s suitable for electronics. The resulting polysilicon is then cast into ingots, which are the foundational blocks for silicon wafers.
The purity of polysilicon is paramount, as even minute impurities can significantly affect the performance of the final semiconductor devices. The table below outlines the typical purity levels required at different stages of silicon processing:
Stage | Purity Level |
---|---|
Metallurgical-Grade Silicon | 98-99% |
Polysilicon for Electronics | 99.9999% (6N) |
Achieving such high purity levels demands meticulous control over the entire purification process, ensuring that the final product meets the stringent standards of the semiconductor industry.
The Siemens Process: Producing High-Purity Silicon Rods
The Siemens Process is a pivotal step in the manufacturing of silicon wafers, where metallurgical-grade silicon is transformed into high-purity polycrystalline silicon, also known as polysilicon. This stage is critical as it directly affects the quality and performance of the final semiconductor devices.
The process involves chemical vapor deposition (CVD), where gases containing silicon are introduced into a reactor containing slim silicon rods. These rods serve as substrates for the deposition of additional silicon, which is derived from a chemical reaction at high temperatures. The result is ultra-pure silicon rods that are the precursor to single-crystal silicon used in wafers.
Key factors in the Siemens Process include temperature control, purity of reactant gases, and the deposition rate. These parameters are meticulously managed to ensure the production of high-quality polysilicon:
- Temperature Control: Maintains the optimal conditions for deposition.
- Purity of Reactant Gases: Ensures that the silicon deposited is free from impurities.
- Deposition Rate: Affects the crystal structure and quality of the polysilicon rods.
Crystal Growth and Ingot Formation
The crystal growth phase is pivotal in the transformation of purified silicon into a form usable for electronics. This process involves heating the high-purity silicon until it melts, after which a seed crystal with the desired crystal orientation is introduced. The seed crystal is slowly withdrawn, promoting the growth of a cylindrical single-crystal ingot, a process known as Czochralski growth.
Once the ingot has been grown to the appropriate size, it is cooled and then subjected to a series of inspections to ensure its quality meets the stringent standards of semiconductor manufacturing. The ingot’s diameter and crystal orientation are critical parameters that are closely monitored.
The following table outlines the key parameters and typical values observed during the ingot formation process:
Parameter | Typical Value |
---|---|
Diameter | 100 – 300 mm |
Crystal Orientation | <100> or <111> |
Purity Level | 99.9999% (6N) |
Cooling Rate | 1 – 5 mm per hour |
The ingot’s journey from a molten state to a solid form is a testament to the historical development of semiconductor technology, reflecting both the legacy and the recent technical advances in bulk crystal production.
Slicing Ingots into Thin Wafers
Once the ingot has been formed, it is then sliced into thin wafers using a process known as wafering. The ingots are carefully mounted and precision-cut with a wire saw or an inner-diameter (ID) saw, which uses a high-speed blade to reduce material loss. The thickness of the wafers is critical, as it influences the efficiency and performance of the final semiconductor devices.
The wafers are typically sliced to a thickness of about 200 to 300 micrometers. To ensure uniformity and minimize the potential for breakage, the slicing process must be meticulously controlled. The following table outlines the standard dimensions for silicon wafers:
Diameter (mm) | Thickness (μm) | Type of Wafer |
---|---|---|
100 | 525 ± 25 | Test & Mechanical Grade |
150 | 675 ± 25 | Prime Grade |
200 | 725 ± 25 | Prime Grade |
300 | 775 ± 25 | Prime Grade |
After slicing, the wafers undergo a series of cleaning steps to remove any surface contaminants and saw damage. This is essential for the integrity of the subsequent manufacturing processes.
Surface Preparation and Wafer Polishing
Edge Grinding for Shape and Dimension
After the ingots are sliced into thin wafers, the next critical step is edge grinding. This process ensures that the wafers are of uniform shape and size, which is essential for the subsequent manufacturing steps. Edge grinding also removes any irregularities or saw marks left from the slicing process, enhancing the overall quality of the wafer.
The edge grinding process involves several key parameters that must be carefully controlled:
- Grinding wheel speed: Determines the rate of material removal.
- Feed rate: Affects the surface finish and dimensional accuracy.
- Coolant flow: Essential for preventing thermal damage to the wafer.
By optimizing these parameters, manufacturers can achieve the desired wafer dimensions and surface quality necessary for high-performance electronics.
Lapping to Remove Surface Defects
Lapping is an essential step in the silicon wafer manufacturing process, aimed at eliminating surface irregularities and defects that may have been introduced during the slicing of ingots. This mechanical technique involves the use of a rotating pad and a polishing liquid, which together abrade the wafer surface to achieve a more uniform thickness and flatness.
The primary goal of lapping is to produce a surface that is optimally prepared for further refinement. It is a balance between removing enough material to eliminate defects and maintaining as much of the wafer as possible for efficiency and cost-effectiveness. After lapping, the wafers exhibit a dull-gray, semi-reflective finish, which is an indicator of the process’s success in smoothing the surface.
The following table outlines the key parameters typically controlled during the lapping process:
Parameter | Description |
---|---|
Pressure | The force applied to the wafer via the lapping pad. |
Speed | The rotation speed of the lapping plate. |
Abrasive | The type and size of the particles in the polishing liquid. |
Time | The duration of the lapping process. |
Etching for Surface Cleanliness
After the initial shaping and lapping of the silicon wafers, etching is employed to further clean the wafer surface. This process involves using chemical solutions to remove microscopic layers from the wafer’s surface, eliminating any remaining surface defects and impurities that could affect the performance of the final semiconductor devices.
The etching process can be categorized into two main types:
- Wet Etching: Involves immersing the wafers in a chemical bath. It is known for its simplicity and cost-effectiveness.
- Dry Etching: Uses gases or plasmas to etch the surface. This method offers greater precision and is essential for advanced manufacturing.
Each method has its own set of parameters that must be carefully controlled to achieve the desired level of cleanliness and surface quality. The choice between wet and dry etching depends on the specific requirements of the semiconductor device being manufactured.
Chemical Mechanical Planarization (CMP) for Smoothness
Chemical Mechanical Planarization, or CMP, is a critical step in the silicon wafer manufacturing process, ensuring the surface of the wafer is perfectly smooth and defect-free. This process involves both chemical slurry and mechanical polishing to achieve the desired flatness necessary for subsequent semiconductor device fabrication.
The CMP process is not only crucial for the smoothness of wafers but also plays a vital role in planarizing the layers during the multi-layered circuit formation. The following list outlines the key stages of the CMP process:
- Application of a chemical slurry to the wafer surface
- Mechanical polishing using a rotating pad
- Continuous cleaning and inspection to ensure quality
As an enabling process technology, CMP has been instrumental in the manufacture of various semiconductor devices, including those used in logic and memory applications. Its importance cannot be overstated, as it directly impacts the performance and yield of the final semiconductor products.
Doping and Layering: Tailoring Electrical Properties
Introduction to Doping Techniques
Doping is a critical step in semiconductor manufacturing, where impurities are intentionally introduced to pure semiconductor materials. This process is essential for modulating the electrical properties of the silicon wafer, allowing for the creation of p-type or n-type semiconductors, each with distinct charge carriers; holes for p-type and electrons for n-type.
The choice of dopant materials and the method of incorporation are pivotal for the desired outcome. Common dopants include boron, phosphorus, and arsenic, each providing different levels of conductivity. The following list outlines the primary doping techniques used in the industry:
- Thermal diffusion: A process where dopants are diffused into the silicon wafer at high temperatures.
- Ion implantation: A more precise method where ions are accelerated and directly implanted into the wafer’s surface.
Each technique has its own set of advantages and is chosen based on the specific requirements of the semiconductor device being manufactured.
Ion Implantation and Diffusion Processes
The precision of ion implantation is pivotal in semiconductor manufacturing, allowing for the accurate placement of dopant atoms within the silicon lattice. This process involves bombarding the wafer with high-energy ions, which are then embedded at specific depths to alter the wafer’s electrical properties.
During diffusion, the wafer is exposed to high temperatures, causing the dopants to migrate and spread out, creating the desired electrical characteristics. The temperature and duration of this process are carefully controlled to achieve the correct distribution of atoms.
Both techniques are essential for tailoring the semiconductor’s properties, and their effectiveness is often evaluated through various inspection methods:
Epitaxial Growth for Layering
Epitaxial layer growth is a sophisticated process that adds a thin layer of single-crystal silicon on top of the wafer substrate. This layer is crucial as it forms the active region of semiconductor devices. The process involves exposing the silicon wafer to a mixture of silicon gases at high temperatures, which allows the atoms to deposit in a pattern that matches the underlying crystal structure.
The quality of the epitaxial layer is paramount, as it directly affects the performance of the final semiconductor device. Manufacturers meticulously control the temperature, pressure, and gas composition during this stage to ensure uniformity and purity of the layer. The following are key factors in the epitaxial growth process:
- Temperature control to ensure proper layer deposition
- Gas flow rates to manage layer thickness
- Cleanroom conditions to prevent contamination
After the epitaxial growth, the wafers undergo various inspections to verify layer uniformity and to detect any defects that may have occurred during the process.
Inspection and Quality Control Measures
Following the intricate doping and layering processes, inspection and quality control measures are critical to ensure that the silicon wafers meet the stringent standards required for electronic devices. These measures are designed to detect any physical, chemical, or electrical defects that could impact the performance of the final semiconductor products.
The inspection process involves a series of sophisticated tools and techniques:
- Visual Inspection: Technicians and automated systems examine the wafers for surface imperfections and structural integrity.
- Electrical Testing: Probes are used to test the electrical functionality of the circuits within the wafer.
- Metrology: Precise measurements are taken to ensure that the wafer’s dimensions and the circuit patterns align with design specifications.
Quality control is not just about identifying defects; it also encompasses the implementation of corrective actions and continuous improvement practices to minimize the occurrence of these issues. The goal is to achieve a high yield of functional wafers, which is essential for cost-effective semiconductor manufacturing.
From Wafer to Chip: The Final Transformation
Photolithography: Patterning the Silicon Wafer
Photolithography is a critical step in the silicon wafer manufacturing process, where intricate circuit patterns are transferred onto the wafer surface. This process begins with the application of a light-sensitive chemical layer, known as a photoresist, to the silicon wafer. The wafer is then exposed to ultraviolet light through a photomask, which imprints the desired pattern.
The exposed areas of the photoresist are chemically altered, allowing for the development stage where the pattern becomes more pronounced. Following this, the unprotected areas of the wafer are etched away, leaving behind the patterned photoresist that defines the circuitry. The precision and accuracy of photolithography are paramount, as they directly impact the performance and yield of the final semiconductor devices.
Key steps in the photolithography process include:
- Coating the wafer with photoresist
- Aligning the photomask above the wafer
- Exposing the wafer to UV light through the photomask
- Developing the pattern on the wafer
- Etching to remove excess material
Each of these steps must be meticulously controlled to ensure the fidelity of the pattern transfer and the quality of the final product.
Etching and Deposition: Creating Circuitry
The etching process meticulously removes layers from the silicon wafer to create the intricate patterns necessary for circuitry. This is achieved through various techniques, such as wet etching, where chemicals are used to dissolve unwanted material, or dry etching, which employs gases and plasmas to achieve a more precise cut.
During deposition, additional materials are added to the wafer’s surface to build up the electronic structures. This can be done through methods like chemical vapor deposition (CVD) or physical vapor deposition (PVD), each with its own set of parameters for thickness and material properties.
The combination of etching and deposition steps is repeated multiple times to form the complex multilayered architecture of modern semiconductor devices. The precision of these processes is critical, as they define the functionality and reliability of the final product.
Assembly and Packaging of Silicon Chips
Once the silicon wafer has been patterned and etched to form the intricate circuitry of a chip, the next critical phase is assembly and packaging. This stage is crucial as it protects the semiconductor die from physical damage and environmental factors while providing the necessary electrical connections. Packaging serves as the container for the die and can vary significantly in materials and design, depending on the application.
The assembly process typically involves attaching the die to the package and connecting the die’s electrical contacts to the package’s external leads. This is done using techniques such as wire bonding or flip-chip bonding. After the die is securely in place, the package is sealed to safeguard the chip from contaminants and moisture. Outsourced Semiconductor Assembly and Test (OSAT) providers often handle this task, although some foundries offer these services as well.
The final product is a fully assembled and packaged chip, ready for integration into electronic devices. The packaging not only ensures the chip’s functionality and reliability but also plays a role in heat dissipation and signal integrity. The choice of packaging can influence the performance and cost of the final product, making it a key consideration in semiconductor engineering.
Testing and Quality Assurance
Once the silicon chips are assembled and packaged, the final and crucial phase of testing and quality assurance begins. This stage is vital to ensure that the chips meet the stringent performance and reliability standards required for electronics.
The testing process involves a series of electrical tests to verify the functionality and performance of the chips. These tests can range from simple continuity checks to more complex functional verifications. The results are meticulously recorded and analyzed to identify any deviations from the expected outcomes.
- Visual Inspection: Checking for physical defects.
- Electrical Testing: Ensuring chips meet electrical specifications.
- Environmental Testing: Assessing performance under various conditions.
- Lifetime Testing: Estimating the chip’s longevity.
Chips that pass all the tests are then cleared for shipment to customers, while those that fail are either reworked or discarded. The depth of wafer testing and the rigor of quality control measures are what ultimately deliver the reliability and performance that end-users trust.
Conclusion
The journey of silicon from a raw ingot to the sophisticated electronics that power our modern world is a testament to human ingenuity and technological advancement. Throughout this article, we have explored the meticulous and multi-step process of silicon wafer manufacturing, which is foundational to the semiconductor industry. Each phase, from purification to slicing, polishing, and intricate patterning, involves a remarkable blend of chemistry, physics, and engineering precision. Understanding this process not only highlights the complexity behind the devices we often take for granted but also underscores the importance of continuous innovation in materials science and manufacturing techniques. As we look to the future, the evolution of silicon wafer manufacturing will undoubtedly play a pivotal role in shaping the next generation of electronic devices and the further advancement of technology.
Frequently Asked Questions
What is the role of silicon in electronics?
Silicon is a semiconductor material widely used in electronics due to its ability to conduct electricity under certain conditions. It forms the base substrate for microchips and integrated circuits, making it fundamental in the manufacture of electronic devices.
Why is purity important in semiconductor manufacturing?
Purity is crucial in semiconductor manufacturing because impurities can affect the electrical properties of the silicon, leading to defects in the electronic devices. High-purity silicon is needed to ensure the reliability and efficiency of the electronic components.
What is the Siemens process?
The Siemens process is a method of producing high-purity silicon rods by chemical vapor deposition. It involves reacting purified metallurgical-grade silicon with hydrogen chloride to form trichlorosilane, which is then reduced in a reactor to produce polysilicon rods of semiconductor-grade purity.
How are silicon wafers polished?
Silicon wafers are polished using a process called Chemical Mechanical Planarization (CMP), which combines chemical etching and mechanical polishing to achieve a mirror-like surface finish. This is essential for the proper functioning of the microchips.
What is doping in the context of silicon wafer manufacturing?
Doping is the process of adding specific impurities to silicon to modify its electrical properties. By introducing dopants, manufacturers can control the conductivity of the silicon, creating p-type or n-type semiconductors necessary for electronic circuits.
What is photolithography in the semiconductor industry?
Photolithography is a process used in semiconductor manufacturing to transfer intricate patterns onto the silicon wafer. It involves coating the wafer with a light-sensitive material, exposing it to light through a mask, and then developing the image to create the circuitry of the microchips.