From Silicon to Circuits: Understanding the Wafer Manufacturing Process
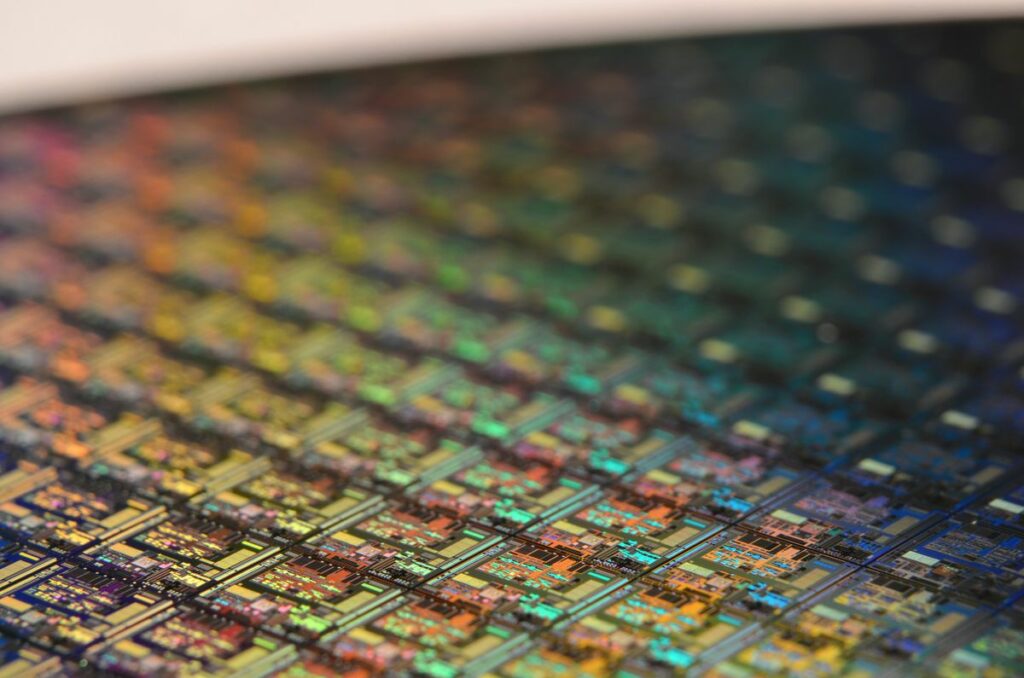
The journey from silicon to circuits is a complex and intricate process that is fundamental to the electronics industry. This article delves into the wafer manufacturing process, exploring the transformation of hyperpure silicon into the polished wafers used to create integrated circuits (ICs). We will examine the critical steps of photolithography, material deposition, doping, and the emerging field of silicon photonics, culminating in the role of semiconductor manufacturers in producing the chips that power our modern devices.
Key Takeaways
- Hyperpure silicon wafers form the cornerstone of semiconductor manufacturing, with polished and epitaxial wafers serving diverse electronic applications.
- Photolithography is a pivotal cycle in IC fabrication, facing challenges such as surface flatness and the need for ultra-clean conditions.
- Material deposition, including the addition of III-V semiconductors, and doping processes are crucial for tailoring the electrical and optical properties of wafers.
- Silicon photonics is advancing the integration of optical and electronic devices, despite silicon’s indirect bandgap limitation.
- Semiconductor manufacturers transform wafers into chips through intricate physical and chemical processes, with stringent quality assurance to meet specific market needs.
The Foundation of Electronics: Silicon Wafer Production
Understanding Hyperpure Silicon Wafers
Hyperpure silicon wafers form the cornerstone of the semiconductor industry, serving as the foundational substrate for a myriad of electronic devices. The purity of these wafers is paramount, as even microscopic impurities can significantly affect the performance of the final semiconductor products.
The production of hyperpure silicon wafers involves intricate processes to ensure the highest quality. Wafers must undergo rigorous cleaning to remove any contaminants and are often heated to around 150\u00b0C for ten minutes to eliminate moisture. An adhesion promoter, such as HMDS, is applied to enhance the bonding of photoresist layers during subsequent fabrication steps.
Siltronic AG is recognized as a key player in the wafer manufacturing landscape, offering a range of wafers with varying diameters, material properties, and surface qualities to meet the diverse needs of the global electronics industry. Their product lineup includes polished wafers, known for their perfect surfaces, and epitaxial wafers, which provide a superior basis for highly integrated components.
Polished and Epitaxial Wafers: Characteristics and Applications
Polished wafers are renowned for their perfect surfaces, offering a versatile foundation for a multitude of semiconductor applications. These wafers undergo a rigorous process to achieve an extremely flat and smooth surface, which is crucial for the subsequent layers of materials that will be added during the chip fabrication process.
Epitaxial wafers provide a superior basis for highly integrated components. An epitaxial layer is grown on top of the polished wafer, introducing a controlled level of impurities to create a semiconductor with specific electrical properties. This process is essential for devices that require precise control over their electrical characteristics.
The increasing demands on wafers necessitate that they not only meet physical and chemical requirements but also contribute to more efficient chip production. By enabling the production of more chips per wafer, they help reduce the energy and water requirements of the manufacturing process, reflecting the industry’s push towards sustainability.
- Polished Wafers: Perfect surfaces for versatile applications.
- Epitaxial Wafers: Superior basis for highly integrated components.
- Special Products: Specialized wafers for innovative technologies.
The Role of Clean Operating Conditions in Wafer Fabrication
The fabrication of silicon wafers demands an environment that is virtually free of contaminants. Clean operating conditions are critical to prevent defects that can arise from particulates or chemical impurities on the wafer surface. The initial step in ensuring cleanliness involves heating the wafer to remove any residual moisture, a process that typically involves temperatures around 150 \(\degree\)C for ten minutes.
Subsequent cleaning employs a variety of methods, such as the widely used RCA clean procedure, which utilizes hydrogen peroxide-based solutions. Alternative cleaning agents include trichloroethylene, acetone, and methanol. These substances are adept at eliminating both organic and inorganic contaminants that could compromise the wafer’s integrity.
To further enhance adhesion during subsequent processing steps, an adhesion promoter like hexamethyldisilazane (HMDS) is applied. This step is crucial for the photoresist’s ability to cling to the wafer surface, ensuring precise patterning during photolithography. The meticulous nature of these cleaning and preparation steps underscores the importance of cleanroom technology, where automated systems and robotic wafer tracks meticulously coordinate the wafer’s journey through each phase of production.
Photolithography: Patterning the Silicon Surface
The Photolithographic Cycle in IC Fabrication
Photolithography stands as the cornerstone of semiconductor fabrication, shaping the intricate patterns that form the basis of integrated circuits. This process harnesses the precision of light to imprint designs onto a silicon wafer, a critical step in the creation of solid-state memories, microprocessors, and other microfabricated systems.
The photolithographic cycle is a complex sequence of steps, each meticulously orchestrated to achieve the desired circuitry. A typical cycle involves the following stages:
- Coating the wafer with a light-sensitive photoresist.
- Exposure to light through a patterned mask, transferring the design onto the resist.
- Developing the image by removing the exposed or unexposed photoresist, depending on the resist type.
- Etching the wafer where the resist has been removed, creating the physical patterns.
- Stripping the remaining resist, preparing the wafer for the next layer or process.
In advanced IC manufacturing, a wafer may undergo this cycle upwards of 50 times, each adding to the complexity and functionality of the final chip. Despite its prevalence, photolithography is not without its limitations; it cannot be applied to non-flat surfaces and demands the utmost in clean operating conditions to prevent defects.
Challenges and Limitations of Photolithography
Despite the remarkable advancements in photolithography, this technique faces several challenges that limit its capabilities. Uniform light intensity and precise mask alignment are critical for both contact and proximity lithography, especially as wafer sizes increase. These requirements become more difficult to meet with the scaling of semiconductor devices.
Photolithography competes with other microlithography technologies, such as electron beam lithography and nanoimprinting, which offer alternative patterning methods. However, each technique has its own set of limitations. For example, contact printing is prone to damaging both the mask and the wafer, leading to its decline in high-volume production.
The following list outlines some of the key challenges faced by photolithography:
- Maintaining uniform light intensity across large wafers
- Achieving precise alignment with pre-existing wafer features
- Printing features smaller than the wavelength of light used
- Competing with alternative microlithography technologies
- Managing the cost of ownership and operational complexities
Advancements in Imaging and Etching Techniques
The relentless pursuit of miniaturization in semiconductor technology has led to significant advancements in imaging and etching techniques. Excimer laser lithography, a pivotal development, has been instrumental in scaling down feature sizes from 800 nanometers in 1990 to an astonishing 7 nanometers in 2018. This breakthrough has been a cornerstone in the evolution of nanoelectronics fabrication.
In the realm of etching, the transition from wet to dry processes marked a critical step forward. Dry etching, particularly the development of low-defectivity anisotropic dry-etch processes, allows for precise pattern transfer from the photolithographic resist to the substrate. This precision is crucial for maintaining the integrity of increasingly fine features.
Current research is not resting on its laurels, with explorations into alternatives to conventional UV lithography. Techniques such as electron beam lithography, X-ray lithography, and extreme ultraviolet lithography are on the forefront, with the latter already seeing adoption in mass production. Notably, nanoimprint lithography (NIL) and its UV-curable variant have emerged, offering both high resolution and versatility, a testament to the ongoing innovation in the field.
Material Deposition and Doping: Tailoring Wafer Properties
Depositing III-V Semiconductors for Optical Functionality
The integration of III-V semiconductors onto silicon wafers marks a pivotal step in the fabrication of photonic integrated circuits (PICs). These materials, known for their direct bandgap properties, are essential for the creation of efficient light-emitting and light-detecting elements within the PICs. Gallium arsenide (GaAs) and indium phosphide (InP) are among the most commonly used III-V semiconductors due to their superior optical characteristics at telecommunications wavelengths.
The deposition process often involves direct bonding of these materials onto the silicon substrate. This ensures that the optical sources, such as lasers, and detectors are seamlessly integrated within the circuit. The precision of this process is critical, as it directly affects the performance and reliability of the optical communication devices.
To illustrate the importance of material choice in PICs, consider the following table comparing the bandgap energies of different semiconductor materials:
Material | Bandgap Energy (eV) | Optical Application |
---|---|---|
Silicon (Si) | 1.12 | Indirect bandgap, poor emitter |
Gallium Arsenide (GaAs) | 1.42 | Direct bandgap, efficient emitter |
Indium Phosphide (InP) | 1.34 | Direct bandgap, efficient emitter |
The table highlights the superior bandgap energies of GaAs and InP compared to silicon, underscoring their suitability for optical applications. The transition from purely electronic to optoelectronic functionality in PICs is a testament to the ongoing innovation in wafer manufacturing, enabling the coexistence of electronic and photonic components on a single chip.
Doping Processes: Enhancing Electrical Characteristics
Doping is an essential process in the semiconductor industry that significantly affects the performance and functionality of the devices. The precision of doping determines the efficiency of power semiconductors, which are crucial in applications where high direct and alternating currents are converted, such as in electric vehicles and renewable energy systems.
The development of new wafer materials, like those with low oxygen content or those incorporating gallium nitride, is aimed at making devices more energy-efficient. For instance, chips with a low oxygen content can lead to power-saving effects in electric cars and between charging stations and electric vehicles.
In the realm of silicon photonics, doping must be managed with particular care to ensure the effective modulation of light traveling through photonic integrated circuits (PICs). This often involves the direct bonding of III-V semiconductor materials onto the silicon wafer, which is critical for the interaction between silicon and photons.
Single Wafer Processing for Precision Control
Single wafer processing marks a significant advancement in the semiconductor manufacturing industry, allowing for unparalleled precision and control. By processing one wafer at a time, manufacturers can closely monitor and adjust the conditions for each wafer, leading to more consistent and high-quality outcomes. This method is particularly beneficial for applications requiring extremely tight tolerances and high performance.
The advantages of single wafer processing can be summarized as follows:
- Enhanced process control for each individual wafer
- Improved yield due to personalized adjustments
- Reduction in cross-contamination between wafers
- Greater flexibility in experimenting with new processes
As part of the quality assurance, wafer testing and analysis play a crucial role in verifying that each wafer meets the stringent standards required for today’s sophisticated electronic devices. This meticulous testing ensures that any defects are identified and addressed before the wafers proceed to the next stage of manufacturing.
Silicon Photonics: Integrating Optical and Electronic Devices
The Emergence of Photonic Integrated Circuits (PICs)
Photonic Integrated Circuits (PICs) have revolutionized the way we handle data, offering high-bandwidth and energy-efficient solutions. Programmable PICs have emerged as powerful platforms in various fields, including optical communications and photonic neural networks. These circuits integrate optical functionalities like light generation, modulation, and detection onto a silicon substrate, allowing optical and electronic devices to coexist seamlessly.
The integration of PICs into data centers underscores their importance in modern technology. They are essential for operations that require rapid and voluminous data communication, which is increasingly vital as AI, cloud computing, and IoT devices become more prevalent. Innovations in PICs, such as on-chip temperature control systems, are crucial for maintaining consistent performance in varying operating environments.
Despite their advantages, the integration of PICs presents challenges, particularly in terms of cost. Packaging, assembly, and testing can account for a significant portion of the total module cost, sometimes as much as 80%. This highlights the need for continued innovation in manufacturing processes to reduce costs while maintaining the benefits that PICs offer.
Overcoming Silicon’s Indirect Bandgap Limitation
Silicon’s inherent indirect bandgap is a significant hurdle in the realm of photonic applications, particularly for light emission and detection. This limitation is a key factor in silicon’s less than ideal light detection performance and its inability to efficiently emit light, or ‘lase’. To address these challenges, the integration of materials with direct bandgap properties is essential.
Materials such as germanium are often used in conjunction with silicon in photodetectors due to their superior direct bandgap nature at telecommunications wavelengths. For the necessary optical gain in lasers on photonic integrated circuits (PICs), the deposition of III-V semiconductor materials, like gallium, is a common strategy. These materials complement silicon’s deficiencies by providing the required direct bandgap characteristics.
The table below summarizes the properties of silicon and the materials used to overcome its limitations:
Material | Bandgap Type | Optical Gain | Application |
---|---|---|---|
Silicon | Indirect | Low | Base substrate |
Germanium | Direct | Moderate | Photodetectors |
III-V | Direct | High | Lasers on PICs |
Doping processes are also tailored to enhance the interaction between silicon and photons, which is crucial for modulating light signals with high efficiency and clarity. The high thermal optical coefficient of silicon poses another challenge, as it can lead to wavelength drift due to temperature changes. To maintain optical transparency at telecommunication frequencies, materials like silicon nitride are employed.
The Future of Silicon Photonics Manufacturing
As silicon photonics transitions from a niche to a mainstream technology, the industry faces the challenge of scaling up manufacturing processes. The current manual and labor-intensive methods hinder the scalability and mass production of photonic components, which are essential for the next generation of optical communications. The intricacy and precision required in fabricating these components necessitate a shift towards more automated and repeatable processes.
To address these challenges, the industry must focus on expanding open-access foundries. These foundries are crucial for integrating electronic and photonic components with nanoscale precision, yet only a few currently have the capabilities to manufacture advanced photonics chips. Investment in these foundries will be pivotal, enabling a wider range of industry players to innovate and bring new products to market.
The path forward for silicon photonics manufacturing involves not only technological advancements but also strategic collaborations and investments. The table below outlines the key areas of focus for the industry to realize the full potential of silicon photonics:
Area of Focus | Description |
---|---|
Automation | Transition from manual processes to automated, high-volume production. |
Foundry Expansion | Increase the number of open-access foundries with advanced manufacturing capabilities. |
Collaboration | Foster partnerships between industry, academia, and government to drive innovation. |
Investment | Secure funding for research and development to overcome current manufacturing limitations. |
From Wafers to Chips: The Role of Semiconductor Manufacturers
Physical and Chemical Transformations in Chip Production
The transformation of silicon wafers into sophisticated chips is a marvel of modern engineering, involving a series of intricate physical and chemical processes. Manufacturers of semiconductors take the pristine wafers and subject them to various treatments to create the complex networks of transistors and interconnections that form the heart of integrated circuits.
The process begins with the deposition of various materials onto the wafer’s surface, followed by photolithography, which defines the intricate patterns of the circuitry. Each step must be meticulously controlled to ensure the highest quality and performance of the final product. The power consumption and efficiency of chips are directly influenced by the precision of these manufacturing steps. As a result, wafers must meet increasingly stringent requirements to enable the production of more powerful and energy-efficient chips.
To illustrate the progression of chip production, consider the following stages:
- Material deposition and removal
- Photolithographic patterning
- Doping to modify electrical properties
- Metallization to form interconnects
- Planarization to ensure a flat surface
These stages are repeated multiple times, with each iteration adding complexity to the chip. The end goal is to produce a device that offers more computing power per watt, a critical factor in today’s energy-conscious world. Manufacturers invest heavily in research and development to continuously improve these processes and meet the demands of end markets.
Quality Assurance and Testing in Semiconductor Manufacturing
In the semiconductor industry, quality assurance and testing are pivotal stages that ensure the reliability and performance of the final product. Electronic and optical testing are employed to verify the integrity of signal paths and the efficiency of optical elements on the chip. This involves a meticulous examination of waveguides for optical losses, modulators, and detectors for their efficiency, and an overall assessment of data transmission capabilities.
The testing phase can be broadly categorized into several key areas:
- Visual inspection for structural defects
- Electrical testing for circuit functionality
- Optical testing for photonic components
- Stress testing for durability under various conditions
- Final performance testing against specifications
Each category of testing is crucial for identifying potential issues that could compromise the chip’s performance in real-world applications. Manufacturers must adapt their testing strategies to meet the specific requirements of different end markets, ensuring that every chip meets the high standards expected by consumers and industries alike.
Meeting the Specific Requirements of End Markets
Semiconductor manufacturers are tasked with the critical role of ensuring that their products meet the diverse and specific requirements of various end markets. The ability to cater to the distinct needs of sectors such as smartphones, computers, servers, and automobiles is essential for the success of semiconductor companies. These manufacturers must navigate the complex buyer journey, aligning sales and marketing efforts to maximize efficiency and customer engagement.
The semiconductor industry is not just about meeting the increasing physical and chemical requirements of wafers; it’s also about leveraging these advancements to produce more chips per wafer, thereby reducing energy and water consumption for customers. This focus on sustainability is part of the broader ‘three S’s‘ strategy that includes sustainability, supply, and scalability, which are crucial for attracting investment and reaching a broader market.
To ensure quality and efficiency, semiconductor companies invest millions annually in research and development. This investment is reflected in the annual reports, which provide audited information and key figures on sustainability efforts. By prioritizing quality over quantity, these companies can navigate the buyer journey more effectively, establishing trust and authority within their respective industries.
Conclusion
The journey from silicon to circuits encapsulates a complex symphony of technological processes, each playing a vital role in the creation of the semiconductor devices that power our modern world. From the precision crafting of hyperpure silicon wafers to the intricate dance of photolithography and material deposition, the wafer manufacturing process is both an art and a science. It demands the utmost in cleanliness, control, and innovation, as manufacturers push the boundaries of what’s possible in silicon photonics and integrated circuitry. As we’ve explored the various stages of this process, it’s clear that the semiconductor industry’s relentless pursuit of advancement is not just about keeping pace with today’s demands but also about shaping the future of electronics. The wafer is the foundation upon which this dynamic and ever-evolving industry builds its dreams of a more connected, efficient, and technologically advanced society.
Frequently Asked Questions
What is a hyperpure silicon wafer?
A hyperpure silicon wafer is a highly pure form of silicon that serves as the substrate for semiconductor devices. It is the foundation upon which circuits and chips are built, and its purity is crucial for the performance of the electronic components.
How does photolithography work in IC fabrication?
Photolithography is a process used to transfer patterns onto a silicon wafer. It involves coating the wafer with a light-sensitive material, exposing it to a pattern of light, and then developing the pattern to create the desired circuitry. This process can be repeated multiple times to build complex integrated circuits.
What are the challenges of silicon photonics manufacturing?
Silicon photonics manufacturing faces challenges such as the complex integration of optical and electronic components, the need for precise material deposition to overcome silicon’s indirect bandgap limitation, and the lack of open foundries to facilitate wider innovation and production.
Why is clean operating conditions essential in wafer fabrication?
Clean operating conditions are essential in wafer fabrication to prevent contamination of the wafers, which can lead to defects and impair the performance of the semiconductor devices. Even microscopic particles can disrupt the delicate patterns and structures being created on the silicon surface.
What is the role of semiconductor manufacturers in transforming wafers into chips?
Semiconductor manufacturers play a crucial role in transforming wafers into chips through a series of physical and chemical processes. They pattern the wafers, deposit various materials, and perform doping to create the intricate circuitry of a chip, followed by rigorous testing to ensure quality.
How does single wafer processing improve semiconductor fabrication?
Single wafer processing allows manufacturers to process each wafer individually, providing greater precision and control over the fabrication process. This leads to improved uniformity and yield, as well as the ability to tailor the properties of each wafer to specific requirements.