How a Wafer Testing Machine Revolutionizes Semiconductor Manufacturing
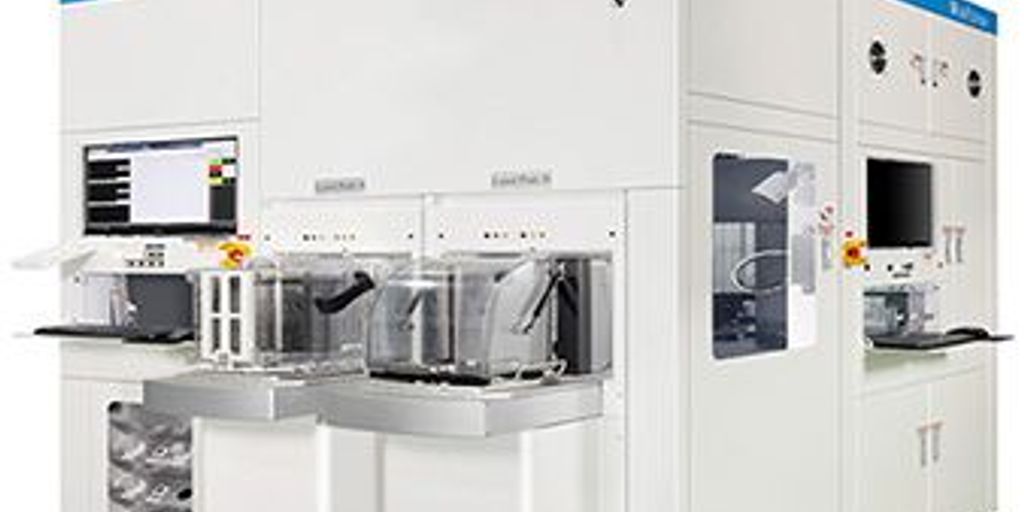
Wafer testing machines are changing the way semiconductors are made. These machines play a big role in making sure the tiny parts inside our electronics work well. They help factories make better products faster and cheaper.
Key Takeaways
- Wafer testing machines boost quality control in semiconductor manufacturing.
- They help reduce production costs and increase yield rates.
- New technologies like AI and real-time data analysis are making these machines even better.
- Using these machines can streamline manufacturing processes and minimize downtime.
- Choosing the right wafer testing machine involves considering key features and doing a cost-benefit analysis.
The Role of Wafer Testing Machines in Semiconductor Manufacturing
Wafer testing machines are essential in the semiconductor industry. They help in minimizing production defects and ensuring that only high-quality wafers move forward in the manufacturing process. By automating front-end wafer inspection and integrating advanced analytics, semiconductor manufacturers can achieve higher yields, reduce cycle times, and enhance overall efficiency.
Enhancing Quality Control
Wafer testing machines play a crucial role in enhancing quality control. They detect and address any defects early in the fabrication process, ensuring that the final products meet the required standards. This early detection is vital for maintaining the reliability and safety of complex manufacturing devices.
Reducing Production Costs
By identifying defects early, wafer testing machines help in reducing production costs. Manufacturers can avoid the expenses associated with reworking or discarding defective wafers. This cost-saving aspect is significant in a highly competitive industry where efficiency is key.
Increasing Yield Rates
Wafer testing machines contribute to increasing yield rates by ensuring that only wafers that meet quality standards proceed to the next stages of production. This selective process helps in maximizing the number of functional devices produced from each wafer, thereby improving overall productivity.
Technological Innovations in Wafer Testing Machines
Integration of AI and Machine Learning
In recent years, the integration of AI and machine learning has transformed wafer testing. These technologies enable machines to learn from data, improving their accuracy and efficiency over time. For instance, an inspection model tested on a real-world wafer map dataset achieved an average testing accuracy of 98.77% and 98.8% for different types of faults. This high level of accuracy ensures that defects are detected early, reducing waste and improving overall product quality.
Non-Destructive Testing Methods
Non-destructive testing methods have become increasingly important in wafer testing. These methods allow for the inspection of wafers without causing any damage, preserving their integrity for further processing. Techniques such as X-ray imaging and ultrasonic testing are commonly used. These methods not only save time but also reduce costs associated with wafer damage.
Real-Time Data Analysis
Real-time data analysis is another significant innovation in wafer testing machines. By analyzing data as it is collected, manufacturers can make immediate adjustments to the production process. This capability is crucial for maintaining high-quality standards and optimizing production efficiency. For example, a programmable wafer stage and probe stage can be used for efficient and accurate testing of the full wafer. Operators can program the wafer stage x and y axes and the prober z axis, allowing for precise control and quick adjustments.
Impact on Production Efficiency
Wafer testing machines have a significant impact on production efficiency in semiconductor manufacturing. These machines streamline manufacturing processes, ensuring that each step is optimized for maximum output. By minimizing downtime, they help maintain a steady flow of production, which is crucial for meeting tight deadlines and high demand.
Streamlining Manufacturing Processes
Wafer testing machines play a vital role in streamlining manufacturing processes. They integrate seamlessly with other production equipment, allowing for a smooth and efficient workflow. This integration helps in identifying and correcting defects quickly, which is essential for maintaining high-quality standards.
Minimizing Downtime
One of the key benefits of wafer testing machines is their ability to minimize downtime. By providing real-time data analysis, these machines enable quick decision-making and problem-solving. This reduces the time spent on troubleshooting and repairs, ensuring that production lines remain operational.
Optimizing Resource Utilization
Wafer testing machines also contribute to optimizing resource utilization. They use advanced techniques to monitor and control yield, ensuring that resources are used efficiently. This not only reduces waste but also helps in achieving higher yield rates, which is crucial for the profitability of semiconductor manufacturing.
Challenges and Solutions in Wafer Testing
Addressing Technical Limitations
Testing VCSEL devices on wafers presents multiple challenges. The complexity of modern semiconductor devices demands advanced automated probing solutions. Ensuring accurate and reliable testing is crucial to maintaining high manufacturing standards. One key challenge is the detection of tiny defects that can significantly impact the performance of the final product.
Overcoming Cost Barriers
The cost of implementing sophisticated wafer testing machines can be prohibitive for many manufacturers. However, investing in these machines can lead to long-term savings by reducing waste and improving yield rates. Manufacturers must weigh the initial investment against the potential benefits to make informed decisions.
Ensuring Compatibility with Existing Systems
Integrating new wafer testing machines with existing manufacturing systems can be a daunting task. Compatibility issues can lead to significant downtime and production delays. To address this, manufacturers should work closely with equipment vendors to ensure seamless integration and minimal disruption to production processes.
Future Trends in Wafer Testing Technology
Advancements in Automation
Automation in wafer testing is evolving rapidly. Robotic handling and automated material systems are becoming standard, making processes faster and more reliable. This shift is critical for meeting the demand for smaller, faster electronic devices. As technology advances, we can expect even more sophisticated automation tools to emerge.
Emergence of Smart Factories
Smart factories represent the next step in semiconductor manufacturing. These facilities use interconnected machines and real-time data to optimize production. The integration of AI and machine learning in test engineering is a key component of this trend. Smart factories can adapt to changes quickly, reducing downtime and increasing efficiency.
Sustainability and Environmental Impact
The semiconductor industry is also focusing on sustainability. New wafer testing technologies aim to reduce waste and energy consumption. Non-destructive testing methods are becoming more popular, as they minimize material waste. Additionally, companies are exploring ways to recycle and reuse materials, further reducing their environmental footprint.
Case Studies: Success Stories of Wafer Testing Machines
Leading Semiconductor Manufacturers
Several top semiconductor manufacturers have integrated advanced wafer testing machines into their production lines. These machines have significantly improved their quality control processes. For instance, a leading manufacturer reported an average testing accuracy of 98.77% for 9 types of faults, showcasing the machine’s precision.
Innovative Applications
Wafer testing machines are not just limited to traditional uses. They are now being used in innovative ways, such as predicting white pixel defects in wafers. A case study from a wafer fabrication plant demonstrated the effectiveness of machine learning approaches in identifying defects, which was published in May 2024.
Measurable Benefits
The benefits of using wafer testing machines are clear. They work seamlessly with statistical process control and reporting modules, enabling real-time data analysis. This integration helps in managing yield excursions effectively. Additionally, historical data-informed testing allows for skipping unnecessary test cycles, optimizing testing efficiency. A notable success rate of 59% was achieved, which is much higher than traditional methods.
Choosing the Right Wafer Testing Machine for Your Needs
Key Features to Consider
When selecting a wafer testing machine, it’s crucial to look at several key features. Accuracy and speed are paramount, as they directly impact production efficiency. Additionally, consider the machine’s ability to handle different wafer sizes and types. Look for machines that offer flexible testing options, such as on-wafer testing, die testing, and RF probing.
Vendor Comparison
Comparing vendors can be a daunting task, but it’s essential for making an informed decision. Create a table to compare the key features, costs, and support services offered by different vendors.
Vendor | Key Features | Cost | Support Services |
---|---|---|---|
Vendor A | High accuracy, fast speed | $$$ | 24/7 support |
Vendor B | Flexible testing options | $$ | Limited support |
Vendor C | Comprehensive testing | $$$$ | Premium support |
Cost-Benefit Analysis
Performing a cost-benefit analysis helps in understanding the long-term value of the machine. Consider not just the initial purchase price but also the maintenance costs and potential savings from increased efficiency. A machine that seems expensive upfront might save money in the long run by reducing downtime and improving yield rates.
Conclusion
In conclusion, wafer testing machines have truly changed the game in semiconductor manufacturing. They help make sure that every tiny chip is perfect, which is super important for all the gadgets we use every day. By using these machines, factories can work faster and make better products. This means we get our new phones, computers, and other tech toys quicker and with fewer problems. As technology keeps moving forward, these machines will only get better, making the future of electronics even more exciting.
Frequently Asked Questions
What is a wafer testing machine?
A wafer testing machine checks semiconductor wafers for defects during manufacturing. It ensures that the wafers meet quality standards before they are used to make electronic devices.
How does wafer testing improve semiconductor manufacturing?
Wafer testing helps find and fix defects early, which improves the quality of the final product. It also reduces costs and increases production efficiency.
What are some new technologies in wafer testing machines?
Modern wafer testing machines use AI, machine learning, and real-time data analysis. These technologies make testing faster and more accurate.
Why is non-destructive testing important?
Non-destructive testing checks wafers without damaging them. This helps maintain the quality and usability of the wafers.
What challenges do manufacturers face with wafer testing?
Manufacturers face challenges like high costs, technical limitations, and ensuring new machines work with existing systems. However, ongoing innovations are helping to address these issues.
What should I consider when choosing a wafer testing machine?
When choosing a wafer testing machine, consider key features, compare different vendors, and do a cost-benefit analysis to find the best option for your needs.