How Silicon Carbide Wafer Technology is Revolutionizing Electronics
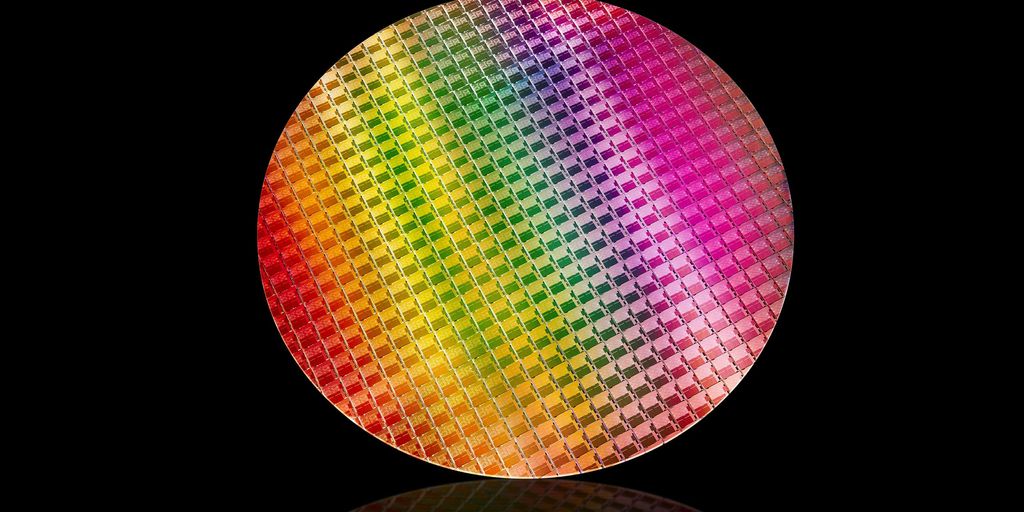
Today, with the semiconductor industry expanding at an unprecedented rate, the demand for high-quality wafers is paramount to meet the growing needs of various applications. In this landscape, Silicon Carbide (SiC) wafers emerge as indispensable components, poised to catalyze the next phase of semiconductor innovation. As the backbone of advanced power electronics and beyond, SiC wafers represent not only the foundation but also the frontier of cutting-edge semiconductor technology, shaping the trajectory of modern electronics.
Key Takeaways
- Silicon Carbide (SiC) wafers offer superior performance compared to traditional silicon wafers, with ten times the breakdown electric field strength and three times the band gap.
- SiC wafers are revolutionizing power electronics, enabling devices that operate at higher voltages, temperatures, and frequencies with greater efficiency and reliability.
- The manufacturing process of SiC wafers involves epitaxy and substrate selection, presenting challenges but also opportunities for quality control and standardization.
- Applications of SiC wafers span various sectors, including electric vehicles, renewable energy systems, industrial power supplies, telecommunications, and aerospace and defense.
- SiC wafers contribute to environmental and economic benefits by enhancing energy efficiency, reducing carbon footprint, and offering cost-effectiveness in the long run.
The Unique Properties of Silicon Carbide Wafers
Wide Bandgap and High Breakdown Electric Field
Silicon Carbide (SiC) wafers are semiconductors crafted from a compound of silicon and carbide. One of the most notable properties of SiC is its wide bandgap, which is three times that of traditional silicon. This wide bandgap results in high-temperature stability and low intrinsic carrier concentrations, allowing SiC devices to operate efficiently at elevated temperatures. Additionally, SiC boasts ten times the breakdown electric field strength of silicon, making it ideal for high-power applications.
Thermal Conductivity and Efficiency
The unique tetrahedral bonding configuration of SiC wafers contributes to their high thermal conductivity. This property ensures efficient heat dissipation, which is crucial for maintaining performance and reliability in high-power electronic devices. The high thermal conductivity of SiC also enhances the overall efficiency of electronic systems, reducing energy losses and improving performance.
Durability and Reliability
SiC wafers are known for their exceptional durability and reliability. The strong three-dimensional network of silicon and carbon atoms provides a robust structure that can withstand harsh environments and demanding applications. This durability translates to longer device lifespans and reduced maintenance costs, making SiC a cost-effective choice for various industries.
Manufacturing Process of Silicon Carbide Wafers
The manufacturing process of Silicon Carbide (SiC) wafers is intricate and requires precision at every step. By mastering these techniques and overcoming the challenges of defect control, manufacturers pave the way for the creation of high-performance SiC wafers.
Applications of Silicon Carbide Wafers in Power Electronics
Electric Vehicles and Charging Infrastructure
Silicon carbide (SiC) wafers are pivotal in the advancement of electric vehicles (EVs) and their charging infrastructure. SiC-based components, such as MOSFETs and diodes, enable higher efficiency and faster charging times. This results in extended driving ranges and reduced energy losses, making EVs more practical and appealing to consumers.
Renewable Energy Systems
In renewable energy systems, SiC wafers are used in solar inverters and wind turbine converters. These applications benefit from the high efficiency and reliability of SiC-based devices, which can operate at higher voltages and temperatures. This leads to improved energy conversion rates and lower operational costs, making renewable energy sources more competitive with traditional power generation methods.
Industrial Power Supplies
SiC wafers are also crucial in industrial power supplies and motor drives. Their ability to handle high power levels and operate efficiently under harsh conditions makes them ideal for industrial applications. This results in more reliable and durable power supply systems, which are essential for maintaining continuous industrial operations.
Impact on the Semiconductor Industry
Today, with the semiconductor industry expanding at an unprecedented rate, the demand for high-quality wafers is paramount to meet the growing needs of various applications. In this landscape, Silicon Carbide (SiC) wafers emerge as indispensable components, poised to catalyze the next phase of semiconductor innovation. As the backbone of advanced power electronics and beyond, SiC wafers represent not only the foundation but also the frontier of cutting-edge semiconductor technology.
Silicon Carbide (SiC) wafers offer numerous advantages over traditional silicon, boasting remarkable characteristics such as ten times the breakdown electric field. This innovative material provides superior performance in high-power and high-temperature applications, making it a preferred choice for modern electronics. However, challenges remain, including the scalability of SiC wafer production and the need for standardization and reliability testing.
As the demand for high-power electronic devices continues to grow, the market for SiC wafers is poised for substantial expansion. Technological advancements and economies of scale are driving down costs and improving manufacturing processes, further fueling adoption across industries. Addressing these challenges will be crucial in unlocking the full potential of SiC wafers and accelerating their widespread adoption.
Advantages of Silicon Carbide Wafers in High-Frequency Applications
Radio Frequency (RF) Devices
Silicon Carbide (SiC) wafers are transforming RF devices by enabling higher power outputs and improved efficiency. Their wide bandgap allows for operation at higher voltages and temperatures, making them ideal for RF applications that demand robust performance.
Telecommunications
In telecommunications, SiC wafers offer significant advantages, including reduced signal loss and enhanced signal integrity. These benefits are crucial for maintaining high-speed data transmission and reliable communication networks.
Aerospace and Defense
The aerospace and defense sectors benefit from SiC wafers due to their durability and reliability in extreme conditions. SiC-based components can withstand high radiation levels and temperature variations, ensuring consistent performance in critical applications.
Environmental and Economic Benefits of Silicon Carbide Wafers
Silicon Carbide (SiC) wafers are known for their exceptional energy efficiency. They enable devices to operate at higher voltages, temperatures, and frequencies, which significantly reduces energy loss. This efficiency translates to sustainable technology solutions that are crucial in today’s environmentally conscious world.
While the initial cost of SiC wafers may be higher compared to traditional silicon wafers, their long-term benefits outweigh the initial investment. The durability and reliability of SiC wafers lead to lower maintenance costs and longer device lifespans. This makes them a cost-effective choice for industries looking to optimize their operational expenses.
The use of SiC wafers in various applications contributes to a significant reduction in carbon emissions. By enhancing the efficiency of power electronic devices, SiC technology helps in lowering the overall energy consumption. This reduction in energy use directly correlates with a decrease in carbon footprint, making SiC wafers a key player in the fight against climate change.
Conclusion
Silicon Carbide (SiC) wafers are undeniably revolutionizing the electronics industry with their superior performance, efficiency, and reliability. As the semiconductor industry continues to expand at an unprecedented rate, the demand for high-quality wafers is paramount. SiC wafers, with their remarkable properties such as high breakdown electric field strength and wide bandgap, are emerging as indispensable components in advanced power electronics and beyond. Their applications span across various high-tech industries including automotive, renewable energy, aerospace, and defense, driving innovation and shaping the future of technology. In essence, SiC wafers are not just the foundation but also the frontier of cutting-edge semiconductor technology, paving the way for a brighter, more efficient future.
Frequently Asked Questions
What are Silicon Carbide (SiC) wafers?
Silicon Carbide (SiC) wafers are semiconductors made from a compound of silicon and carbide. They offer superior properties like high breakdown electric field strength and wide bandgap, making them ideal for advanced power electronics.
How do SiC wafers compare to traditional silicon wafers?
SiC wafers have ten times the breakdown electric field strength and three times the band gap of traditional silicon wafers. These properties enable higher efficiency, power density, and reliability in electronic devices.
What are the main applications of SiC wafers?
SiC wafers are used in various applications such as electric vehicles, renewable energy systems, industrial power supplies, radio frequency (RF) devices, telecommunications, and aerospace and defense.
What are the challenges in the production of SiC wafers?
The production of SiC wafers involves challenges like the need for high-quality substrates, precise epitaxy processes, and stringent quality control standards to ensure the wafers meet performance requirements.
How do SiC wafers benefit the environment?
SiC wafers contribute to energy efficiency and sustainability by enabling devices that operate at higher voltages and temperatures with lower energy losses. This helps in reducing the overall carbon footprint.
What is the future outlook for SiC wafer technology?
The future of SiC wafer technology looks promising with ongoing innovations and increasing adoption in various high-tech industries. Market trends indicate significant growth, driven by the demand for efficient and reliable power electronics.