Innovations in Semiconductor Packaging: Advancements and Trends
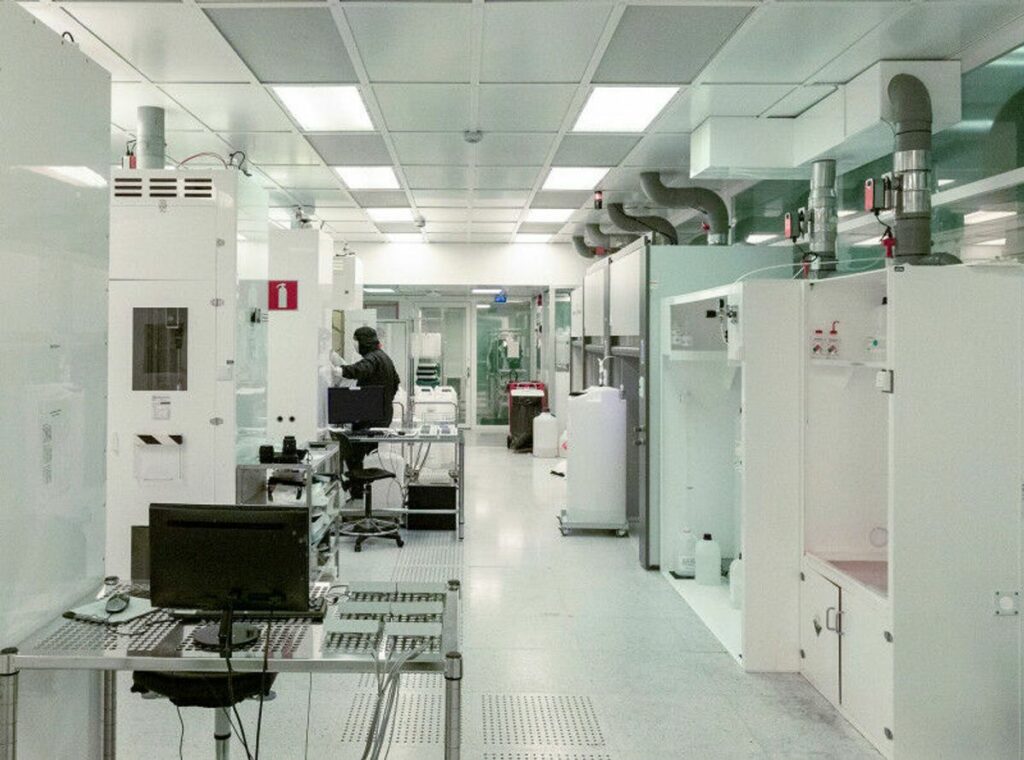
The semiconductor industry is witnessing a transformative era with significant advancements in packaging technologies. From the early days of 1D packaging on printed circuit boards (PCBs) to the sophisticated 3D integration methods of today, the evolution of semiconductor packaging has been pivotal in enhancing chip performance, efficiency, and functionality. This article delves into the latest innovations, regulatory influences, market drivers, and the future of materials and technologies shaping the semiconductor packaging landscape.
Key Takeaways
- Semiconductor packaging has evolved from 1D PCB to advanced 3D hybrid bonding, enabling ultra-fine interconnect pitches and bandwidths exceeding 1000 GB/s.
- Regulatory mandates, such as those for driver monitoring systems, are significant drivers in the development and adoption of innovative semiconductor packaging technologies.
- Dielectric materials are at the forefront of semiconductor packaging innovation, with trends indicating a focus on meeting the high bandwidth requirements of next-gen chips.
- Advanced packaging technologies are crucial for AI and HPC, with 2.5D and 3D integration, and silicon photonics leading the way in system performance optimization.
- Sustainability and miniaturization are key trends in IC packaging, with the industry moving towards eco-friendly solutions and high-density interconnects for enhanced functionality.
Evolution of Semiconductor Packaging: From 1D to 3D Integration
The Journey from PCB to Wafer-Level Packaging
The evolution of semiconductor packaging marks a significant transition from the traditional 1D PCB to sophisticated wafer-level packaging. This shift has been pivotal in enabling higher levels of integration and performance. The journey began with the basic Printed Circuit Boards (PCBs) that laid the groundwork for electronic devices, providing a platform for mounting and connecting components.
As the industry progressed, the demand for enhanced functionality and miniaturization drove the development of advanced packaging techniques. These include 3D packaging, heterogeneous integration, and fan-out wafer-level packaging (FOWLP), which have become crucial in achieving higher efficiency and system performance. The new Center for Advanced Wafer-Level Packaging Applications and Development is set to catalyze innovation, expanding domestic capabilities in this field.
The table below summarizes the progression of semiconductor packaging technologies:
Generation | Technology | Bandwidth | Energy Efficiency |
---|---|---|---|
1D | PCB | Low | Low |
2.5D | Interposer | Medium | Medium |
3D | WLP | High | High |
Continuous advancements, including through-silicon via (TSV), system-in-package (SiP), and flip-chip packaging, have enabled manufacturers to achieve unprecedented levels of integration and performance. These innovations are not just enhancing chip capabilities but are also setting the stage for the next wave of innovation in the global semiconductor industry.
3D Hybrid Bonding and Its Impact on Bandwidth and Efficiency
The advent of 3D hybrid bonding has marked a significant leap in semiconductor packaging, enabling ultra-fine pitch interconnects that are essential for high-bandwidth applications. With pitches now reaching below 10 micrometers, this technology has paved the way for expanded I/O capabilities and a substantial increase in data transmission rates.
Bandwidth, a pivotal factor in data communication, benefits greatly from the advancements in 3D hybrid bonding. The integration of metal contacts within dielectric materials, coupled with a heat treatment process, facilitates copper atom diffusion. This method not only circumvents the issues associated with soldering, such as bridging problems, but also enhances the overall reliability of the package.
Factor | Impact on Bandwidth and Efficiency |
---|---|
Interconnect Pitch | Enables higher I/O density |
Dielectric Material | Reduces RC delay and insertion loss |
Heat Treatment | Improves copper diffusion |
Metal Contact Design | Eliminates solder bridging |
Despite these advancements, challenges remain, particularly in the realm of dielectric materials. Current reliance on inorganic dielectrics like SiO2 poses difficulties in achieving fine-scale patterns, necessitating front-end manufacturing techniques. The exploration of organic dielectrics, which offer low-k properties and better resistance to copper migration, is still in the research and development phase, with temperature constraints being a significant hurdle.
Challenges and Solutions in Transitioning to Advanced Packaging
The transition to advanced semiconductor packaging presents a myriad of challenges, often rooted in the necessity for substantial investment and the rapid pace of technological change. Manufacturers may face the risk of their equipment becoming outdated or incompatible with newer semiconductor technologies. This is exacerbated by the fact that the development of corresponding packaging materials sometimes lags behind, struggling to meet the demands for performance, miniaturization, and functionality.
To address these issues, companies are exploring various strategies. Cost optimization is a key focus, with advanced packaging offering significant long-term benefits despite the potential need for initial investment. The modular nature of advanced packages allows for easier upgrades and repairs, which can reduce lifecycle costs. Moreover, the demand for environmentally sustainable packaging solutions is creating opportunities for innovation in biodegradable materials.
Here are some of the key strategies adopted to mitigate the challenges:
- Investing in specialized equipment and materials to stay ahead in the market.
- Focusing on modular designs to facilitate integration and future upgrades.
- Exploring biodegradable and eco-friendly materials for sustainable packaging solutions.
- Optimizing costs by leveraging the long-term benefits of advanced packaging technologies.
Regulatory Influences and Market Drivers in Semiconductor Packaging
Mandating Driver Monitoring Systems: A Regulatory Perspective
The landscape of automotive safety is rapidly evolving with the integration of Driver Monitoring Systems (DMS). These systems are becoming a staple in vehicle design, propelled by the increasing levels of autonomous driving as defined by the Society of Automotive Engineers (SAE) and the tightening of regulatory frameworks across major markets such as the USA, Europe, China, and Japan.
The synergy between DMS and Occupancy Monitoring Systems (OMS) marks a significant leap in in-cabin monitoring capabilities. While DMS traditionally employs 2D infrared cameras, OMS is advancing with the adoption of 3D sensing technologies, including time-of-flight (ToF) cameras and radar modules.
The push for DMS is not only a safety measure but also a response to the adoption of emerging technologies like 5G and autonomous vehicles. This regulatory drive is expected to continue shaping the semiconductor packaging industry, as these systems require sophisticated electronics to function effectively.
Market Trends Shaping the Future of Packaging Materials
The semiconductor packaging materials market is undergoing a significant transformation, driven by the demands of new technologies and the push for sustainability. In 2023, the Semiconductor Packing Market reached a value of USD 34.59 billion, and with the current pace of innovation and market demands, it is projected to surge to USD 64.22 billion by 2030. This growth is indicative of the industry’s rapid evolution and the increasing importance of advanced packaging solutions.
Emerging trends include the adoption of advanced materials for 5G and IoT applications, which are critical for the next generation of connectivity. Technologies such as fan-out wafer-level packaging (FOWLP) and system-in-package (SiP) are becoming more prevalent, offering enhanced performance and miniaturization. Moreover, there is a growing focus on eco-friendly packaging solutions, with companies exploring biodegradable materials and other sustainable alternatives to meet future industry standards.
The table below summarizes key market trends and their implications for the semiconductor packaging industry:
Trend | Implication |
---|---|
Advanced materials for 5G/IoT | Enabling next-gen connectivity |
FOWLP and SiP technologies | Enhanced performance and miniaturization |
Sustainable packaging solutions | Meeting environmental standards |
The Role of Regulations in Advancing Packaging Technologies
Regulatory frameworks play a crucial role in shaping the semiconductor packaging industry. They not only ensure safety and compliance but also drive innovation by setting standards that push the boundaries of current technologies. Regulations can accelerate the adoption of advanced packaging solutions by creating a demand for higher performance and environmentally sustainable practices.
For instance, the CHIPS Act in the United States aims to bolster domestic semiconductor manufacturing. This legislation is expected to lead to increased investment in the sector, fostering technological advancements and job creation. Such investments are crucial for the development of new packaging technologies that cater to the evolving needs of industries like automotive and consumer electronics.
The table below outlines the impact of regulatory influences on semiconductor packaging:
Factor | Influence on Packaging Technology |
---|---|
Safety Standards | Ensures reliability and user safety |
Environmental Regulations | Promotes sustainable packaging solutions |
Performance Benchmarks | Drives the need for high-efficiency packaging |
Investment Incentives | Encourages R&D in advanced packaging methods |
Adapting to these regulations requires manufacturers to navigate high costs and complex transitions. However, the long-term benefits include market growth, innovation, and alignment with future technology trends. The industry’s focus on cost-effective solutions and efficient assembly processes is essential to meet these regulatory demands while maintaining competitiveness.
Dielectric Materials: Pioneering the Next Generation of Packaging
Innovations in Dielectric Materials for Enhanced Chip Performance
The relentless pursuit of higher chip performance has led to significant advancements in dielectric materials used in semiconductor packaging. Lower dielectric constants are pivotal in this evolution, as they directly influence the efficiency and cost-effectiveness of chips. These materials are crucial for reducing parasitic capacitance, thereby enhancing signal transmission and minimizing power consumption.
In the realm of advanced packaging, the transition from traditional inorganic dielectrics to organic alternatives is gaining momentum. Organic dielectrics offer a suite of advantages, including low-k properties that are essential for reducing RC delay and insertion loss. This shift is particularly beneficial in 2.5D and 3D packaging technologies, where the reduction of RC delay is a critical factor in achieving high bandwidth and efficient data transmission between dies.
Despite the clear benefits, the integration of organic dielectrics into 3D hybrid bonding presents challenges, such as the need for lower bonding temperatures to accommodate sensitive materials. The industry is actively researching solutions to overcome these hurdles, with the goal of fully harnessing the potential of organic dielectrics in next-generation semiconductor packaging.
Meeting the Demand for High Bandwidth with Advanced Dielectrics
In the quest for higher bandwidth in semiconductor packaging, the industry is shifting focus to materials that can facilitate faster data transmission between dies. Organic dielectric materials emerge as promising alternatives, offering lower dielectric constants and cost advantages, which are essential for 2.5D and 3D packaging technologies. These materials not only provide the necessary electrical properties but also bring additional benefits such as reduced RC delay and better resistance to copper migration.
The performance of redistribution layers (RDL) is critical in 2.5D packaging, where traditional inorganic materials like SiO2, despite their ability to achieve fine Line/Space (L/S), are limited by high dielectric constants (Dk=3.9). This limitation is a significant barrier to achieving the desired high-speed communication. The table below summarizes the comparison between traditional and advanced dielectric materials:
Material Type | Dielectric Constant (Dk) | Advantages |
---|---|---|
Inorganic (e.g., SiO2) | 3.9 | Fine L/S capability |
Organic | <3.9 | Lower Dk, cost-effective, reduced RC delay |
While the benefits of organic dielectrics are clear, their application in 3D hybrid bonding is still under research and development. The challenges include managing the elevated bonding temperatures required, which can affect memory applications and other sensitive materials within the package.
Future Trends in Dielectric Technology for Semiconductor Packaging
As the semiconductor industry continues to innovate, the role of dielectric materials in packaging is becoming increasingly critical. Emerging trends in dielectric technology are poised to redefine the standards of chip performance and efficiency. With the advent of 2.5D and 3D packaging technologies, the demand for materials that can support high bandwidth and energy efficiency is surging.
The following list highlights key future trends in dielectric technology for semiconductor packaging:
- Development of low-k and ultra-low-k dielectric materials to reduce signal delay and power consumption.
- Advancements in dielectric formulations to improve mechanical strength and thermal stability.
- Integration of novel materials that enable finer interconnect pitches and higher density packaging.
These trends indicate a shift towards materials that not only enhance electrical performance but also address the thermal and mechanical challenges associated with advanced packaging. As bandwidth requirements exceed 1000 GB/s, the industry is looking towards innovative dielectric solutions to maintain the pace of progress.
Advanced Packaging for AI and High-Performance Computing (HPC)
Optimizing System Performance with 2.5D and 3D Technologies
The relentless pursuit of higher performance in AI and HPC applications has led to significant advancements in semiconductor packaging. Advanced semiconductor packaging technologies, such as 2.5D and 3D hybrid bonding, are at the forefront of this evolution. These methods not only enhance system performance but also play a pivotal role in the next wave of chip innovation.
In the realm of 2.5D packaging, the use of a silicon interposer is a game-changer. It facilitates shorter electrical paths between chipsets, which translates to increased communication speeds and reduced latency, essential for real-time data processing. Here’s a quick comparison of the two approaches:
Technology | Electrical Path Length | Performance Benefit |
---|---|---|
2.5D Interposer | Short | Speed and Latency Improvement |
3D Stacking | Vertical Integration | Space Utilization and Density |
3D stacking takes this a step further by enabling vertical chip integration. This approach not only maximizes space utilization but also leads to denser interconnects and miniaturization, which are critical for achieving unparalleled system performance. With the potential to reach single-digit micron interconnect pitches, these technologies are setting new benchmarks for bandwidth and energy efficiency in the industry.
Silicon Photonics: A Game Changer in AI and HPC Chip Design
The integration of silicon photonics into semiconductor packaging is revolutionizing the landscape of AI and HPC. This technology enables high-speed data transfer and increased bandwidth, which are essential for the complex computations required in these fields. Silicon photonics merges optical communication with silicon-based electronics, resulting in chips that can process and transmit data at unprecedented speeds.
Recent advancements in silicon photonics are upending the optical market in the data center, with significant ramifications for how future AI, cloud, and HPC applications will operate. The table below illustrates the comparative advantages of silicon photonics over traditional electrical interconnects in AI and HPC applications:
Feature | Silicon Photonics | Traditional Electrical Interconnects |
---|---|---|
Speed | Up to 100 Gbps | Up to 10 Gbps |
Bandwidth | Higher | Limited |
Power Consumption | Lower | Higher |
Integration | Easier with CMOS | More complex |
By deconstructing complex systems into smaller, optimized chipsets, advanced packaging techniques, including silicon photonics, are heralding a paradigm shift in chip design. These chipsets are interconnected using advanced packaging technologies, which is critical for fostering the next wave of AI and HPC chip innovation.
The Ecosystem of Advanced Semiconductor Packaging in AI and HPC
The ecosystem of advanced semiconductor packaging is pivotal in powering the AI and HPC revolution. By deconstructing complex systems into smaller, optimized chipsets, advanced packaging techniques such as 2.5D and 3D integration enable a new era of chip design. These chipsets are tailored for specific functions and interconnected through innovative packaging solutions, offering high performance and reduced development costs.
Advanced packaging technologies, including 2.5D and 3D hybrid bonding and silicon photonics, are at the forefront of optimizing system performance. They are instrumental in driving the next wave of innovation in AI and HPC chip design. The modular nature of these advanced packages not only facilitates integration but also simplifies upgrades and repairs, contributing to cost optimization over the product lifecycle.
Europe’s role in this technological advancement is significant, with advanced packaging revolutionizing chip design and establishing the continent as a potential powerhouse in AI and HPC. The strategic implementation of these technologies is fostering innovation and positioning Europe at the forefront of the global tech landscape.
Sustainable and High-Density Solutions in IC Packaging
Eco-Friendly Packaging Solutions for a Sustainable Future
The semiconductor industry is increasingly focusing on sustainable packaging solutions to address environmental concerns. Companies are exploring the use of biodegradable materials and other sustainable alternatives to create eco-friendly packaging options. This shift is not only a response to regulatory pressures but also a reflection of the growing consumer demand for sustainability in technology products.
Despite the environmental benefits, transitioning to sustainable packaging presents challenges. Advanced packaging techniques often require specialized equipment and materials, leading to higher manufacturing expenses. These costs can be a barrier, particularly for smaller manufacturers or those in cost-sensitive markets. However, the long-term benefits, such as reduced lifecycle costs and the potential for modular upgrades, make this investment worthwhile.
The market for semiconductor and IC packaging materials is evolving, with a projected value of $70.9 billion. This growth is driven by the adoption of advanced materials for emerging technologies like 5G and IoT, as well as a concerted effort towards eco-friendly solutions. The table below summarizes key trends influencing the market:
Trend | Description |
---|---|
Advanced Materials | Adoption for 5G and IoT applications. |
Eco-Friendly Solutions | Focus on sustainability. |
HDI & Miniaturization | Demand for high-density interconnects and flip-chip packaging. |
As the industry moves forward, the demand for environmentally sustainable packaging solutions will likely open new opportunities for innovation and market growth.
High-Density Interconnects (HDI) and Miniaturization Trends
The relentless pursuit of miniaturization in electronics has led to the rise of High-Density Interconnects (HDI) and flip-chip packaging, which are pivotal for achieving enhanced performance in ever-smaller devices. These technologies enable the integration of more components into compact spaces, addressing the industry’s demand for denser circuitry and improved functionality.
The incorporation of AI and ML algorithms into packaging processes is a burgeoning trend that promises to refine efficiency and yield rates. As devices shrink in size, the need for advanced interface materials that can withstand the rigors of high pin densities and complex interconnections becomes critical. These materials must also meet the high reliability standards required by today’s miniaturized electronics.
Trend | Impact on Packaging |
---|---|
AI and ML Integration | Improved efficiency and yield rates |
Advanced Interface Materials | Enhanced performance for compact devices |
Densification | Higher pin densities and complex interconnections |
In the context of AI and HPC, the European landscape highlights two significant packaging trends: 2.5D interposer technology and 3D stacking. The former employs a silicon interposer to create shorter electrical paths, thus accelerating communication speeds and reducing latency. The latter, 3D stacking, not only furthers miniaturization but also maximizes space utilization and provides denser interconnects, which are essential for the high-performance demands of AI and HPC applications.
Fan-Out Wafer-Level Packaging (FOWLP) and System-in-Package (SiP) Technologies
The semiconductor industry continues to innovate, with Fan-Out Wafer-Level Packaging (FOWLP) and System-in-Package (SiP) technologies at the forefront of these advancements. FOWLP, in particular, has become a popular solution due to its ability to provide enhanced functionality without significantly increasing the package footprint. This technology allows for a higher number of I/Os, improved thermal performance, and a reduction in overall package height.
SiP technology complements FOWLP by integrating multiple chip functions into a single package. This integration is crucial for applications demanding high performance and compact design, such as mobile devices and wearables. The synergy between FOWLP and SiP technologies enables manufacturers to meet the stringent requirements of modern electronics.
Emerging trends in the market include:
- Adoption of advanced materials for 5G and IoT applications.
- Focus on eco-friendly solutions to address sustainability concerns.
- Increased demand for high-density interconnects (HDI) for enhanced performance and miniaturization.
Conclusion
The semiconductor packaging landscape is undergoing a transformative phase, marked by the emergence of advanced technologies such as 2.5D and 3D hybrid bonding, fan-out wafer-level packaging (FOWLP), and system-in-package (SiP) solutions. These innovations are not only addressing the demands for higher performance, miniaturization, and energy efficiency but are also pivotal in driving the next wave of AI and HPC chip innovation. With the industry pushing towards higher bandwidth, denser interconnects, and eco-friendly materials, the future of semiconductor packaging is poised to meet the complex challenges of 5G, IoT, and beyond. As we look ahead, it is clear that the continuous evolution in packaging technologies will play a critical role in shaping the electronics industry, ensuring that semiconductor companies can keep pace with the rapid advancements in chip design and functionality.
Frequently Asked Questions
What are the emerging trends in the Semiconductor & IC packaging materials market?
Emerging trends include the adoption of advanced materials for 5G and IoT applications, eco-friendly solutions for sustainability, high-density interconnects (HDI), and technologies like fan-out wafer-level packaging (FOWLP) and system-in-package (SiP) for enhanced performance and miniaturization.
What advancements have been made in 3D semiconductor packaging technology?
Advancements in 3D semiconductor packaging technology include the development of 3D hybrid bonding, which allows for single-digit micrometer interconnecting pitches and bandwidths exceeding 1000 GB/s, while also improving energy efficiency.
How do regulations impact the advancement of semiconductor packaging technologies?
Regulations can drive innovation by mandating the adoption of new technologies such as driver monitoring systems. This, in turn, influences the development of advanced packaging technologies to meet regulatory requirements.
What role do dielectric materials play in next-generation semiconductor packaging?
Dielectric materials are crucial in semiconductor packaging as they enable higher chip performance and efficiency. Innovations in dielectrics are essential for meeting the demand for high bandwidth and enhanced chip functionality.
How is advanced packaging technology shaping AI and HPC?
Advanced packaging technologies, including 2.5D and 3D hybrid bonding as well as silicon photonics, are pivotal in optimizing system performance and driving innovation in AI and HPC chip design.
What are the challenges facing semiconductor packaging materials?
Challenges include the rapid pace of technological change outpacing the development of new packaging materials, the need for solutions that align with future trends, and the dilemma of investing in costly technologies that may quickly become obsolete.