Inside a Semiconductor Fab: How Microchips Are Made
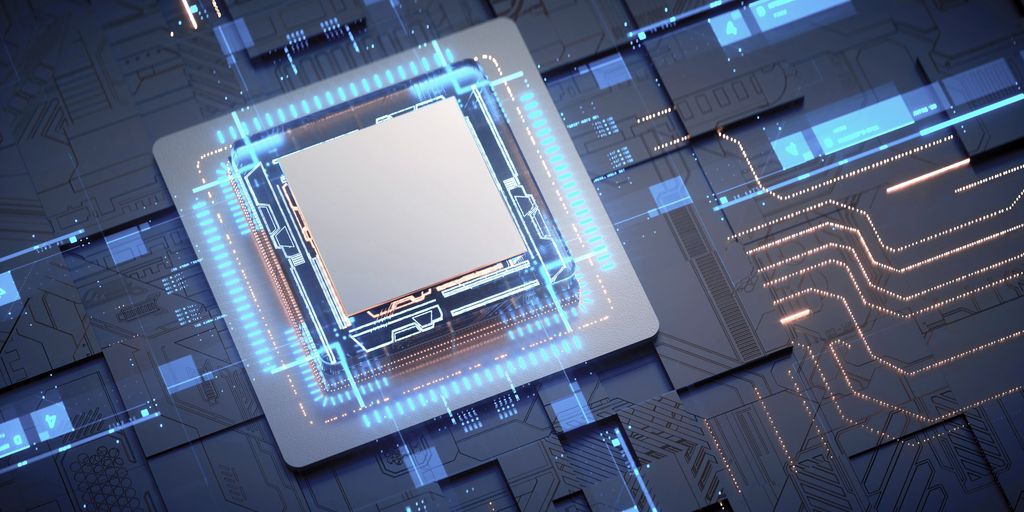
Microchips are the heart of modern electronics, powering everything from smartphones to cars. But how are these tiny marvels made? The journey begins in semiconductor fabs, where raw materials are transformed into intricate silicon wafers. Through a series of highly controlled processes, these wafers become the microchips that drive our digital world. Let’s take a closer look at the fascinating world of chip manufacturing.
Key Takeaways
- Microchips are made in specialized facilities called semiconductor fabs.
- The process starts with extracting silicon from sand and creating silicon wafers.
- Microchips are built layer by layer using techniques like deposition, photolithography, and etching.
- Strict cleanroom protocols and precise instruments are essential for maintaining quality.
- Future advancements aim to make chips smaller and production more sustainable.
The Intricate World of Semiconductor Fabs
A semiconductor fab, short for fabrication plant, is where microchips are made. These fabs are highly specialized facilities, often costing $15–20 billion to build. The central part of a fab is the clean room, where even a tiny particle can ruin a microcircuit.
Understanding Cleanroom Protocols
In a fab, the clean room is the heart of the operation. Workers must wear special suits, often called "bunny suits," to keep particles out. They also pass through an air shower to remove any dust or particles before entering.
The Role of Automation in Chip Manufacturing
Modern fabs are almost entirely automated. Machines handle the wafers, moving them from one process to the next. This automation ensures precision and efficiency, allowing fabs to produce hundreds of thousands of wafers, each containing many microchips.
Maintaining Air Quality and Temperature
Maintaining air quality and temperature is crucial in a fab. The air is filtered to remove particles, and the temperature is kept stable to ensure the delicate processes are not disrupted. This careful control helps in making sure that the microchips are made without defects.
From Sand to Silicon: The Birth of a Wafer
The journey of creating a silicon wafer begins with extracting silicon from sand. This process involves purifying the sand to obtain high-purity silicon. The purified silicon is then melted in a crucible. The molten silicon is carefully grown into a large crystal called an ingot.
Extracting Silicon from Sand
The process of transforming silica sand into high-purity silicon involves extracting and purifying the sand, followed by melting and carefully growing a large crystal.
Creating Silicon Ingots
Once the silicon is purified, it is added to a crucible and heated until molten. The crucible is rotated while a solid piece of ‘seed’ silicon is pulled up using a rod. This results in a silicon ingot or boule, which can have a diameter of up to 300mm.
Slicing Ingots into Wafers
The silicon boule is then sliced into thin discs known as wafers. These wafers are polished to a mirror-smooth finish, ready for the next steps in chip manufacturing.
Layer by Layer: Building Microchips
Microchips are built by adding layers of materials on top of each other, creating complex structures. Each step in the process happens at a microscopic level, forming three-dimensional structures that can include up to 90 layers of intricate circuits. This process requires extreme precision and control.
Deposition Techniques
Deposition is the first step in building microchips. It involves placing thin layers of materials onto the silicon wafer. These materials can be metals, insulators, or semiconductors. The goal is to create a uniform layer that will form the base for the next steps.
Photolithography and Patterning
Photolithography is like using a stencil to create patterns on the wafer. A light-sensitive material called photoresist is applied to the wafer. Then, ultraviolet light shines through a mask, transferring the pattern onto the wafer. This step is crucial for defining the tiny features of the microchip.
Etching Processes
Etching removes unwanted material from the wafer, revealing the desired pattern. This step must be carefully controlled to avoid damaging the underlying layers. As microchip designs become more complex, with some reaching up to 175 layers, etching becomes even more challenging. The depth and precision of the etching must be exact to ensure the microchip functions correctly.
Ensuring Perfection: Inspection and Testing
Measurement and Inspection Techniques
In the final stages of semiconductor fabrication, the focus shifts from making the chips to making sure they work perfectly. Every single processor is measured and inspected to ensure there are no defects. Even a tiny dust particle can ruin a chip. This is why quality control is so important.
Electroplating and Finishing
After the initial inspections, the chips go through electroplating and finishing. This step adds a protective layer to the chips, making them more durable. The chips are then marked with a laser to show their name and numbers.
Testing Microchips for Quality
The last step is testing the microchips to make sure they work correctly. This involves a series of electrical tests, often called wafer probing or wafer testing. Chips are sometimes designed with special features to make testing easier and faster. If a chip fails any of these tests, it is discarded. This ensures that only the best chips make it to the market.
Inside the Cleanroom: A Day in the Life
Working inside a semiconductor fab’s cleanroom is a unique experience. The air is filtered and recirculated continuously to keep it free of particles. Employees wear special clothing, often called ‘bunny suits,’ to maintain this pristine environment. Even a single dust particle can ruin a microchip.
Donning the Bunny Suit
Before entering the cleanroom, workers must put on their bunny suits. These suits cover them from head to toe, ensuring no particles from their bodies contaminate the air. The process is meticulous, as any mistake can compromise the cleanroom’s integrity.
Navigating the Air Shower
Once suited up, employees pass through an air shower. This chamber blows high-velocity air to remove any remaining particles from their suits. It’s a crucial step in maintaining the cleanroom’s sterility.
Working with Precision Instruments
Inside the cleanroom, workers handle precision instruments to build microchips. Each step happens at a microscopic level, creating complex structures with up to 90 layers of circuitry. The environment is so sterile that it’s 100,000 times cleaner than a hospital operating room. This level of cleanliness is essential for producing defect-free chips.
The Future of Semiconductor Fabs
Advancements in Fabrication Technology
The semiconductor industry is always changing, driven by the need for faster, smaller, and more efficient devices. New technologies are constantly being developed to improve the way microchips are made. These advancements include better materials, more precise machines, and smarter software to control the entire process.
The Push Towards Smaller Nodes
One of the biggest goals in chip manufacturing is to make the components on a chip as small as possible. This is called moving to smaller nodes. Smaller nodes mean more power and speed in a smaller space. However, making these tiny components is very hard and needs very advanced tools and techniques.
Sustainability in Semiconductor Manufacturing
Making microchips uses a lot of resources and can harm the environment. The industry is working hard to be more sustainable. This includes using less water and energy, recycling materials, and finding ways to reduce waste. By focusing on sustainability, fabs can help protect the planet while still making the technology we need.
Conclusion
Making microchips is a fascinating and complex journey that involves many steps and high-tech equipment. From the initial silicon wafer to the final chip, each stage requires precision and care. The process includes not just building layers but also testing, measuring, and inspecting to ensure each chip works perfectly. It’s amazing to think that these tiny chips, which start as simple sand, end up powering our most advanced devices. Understanding how microchips are made gives us a greater appreciation for the technology we use every day.
Frequently Asked Questions
What is a semiconductor fab?
A semiconductor fab is a factory where microchips are made. These facilities are equipped with advanced machines that build microchips layer by layer.
How clean are the cleanrooms in a semiconductor fab?
Cleanrooms in semiconductor fabs are extremely clean. They have strict protocols to control air quality and temperature, ensuring no dust particles can damage the microchips.
What is silicon, and why is it important?
Silicon is a material extracted from sand. It is important because it is used to make wafers, which are the base for microchips.
How long does it take to make a microchip?
Making a microchip can take up to four months. It involves hundreds of steps, including deposition, photolithography, and etching.
What is a bunny suit, and why is it worn?
A bunny suit is a special outfit worn by workers in cleanrooms. It prevents dust and other particles from contaminating the microchips.
Why is automation important in chip manufacturing?
Automation is crucial because it helps in handling the delicate wafers precisely and efficiently, reducing the risk of errors and contamination.