Inside the World of Semiconductor Fab: Processes and Innovations
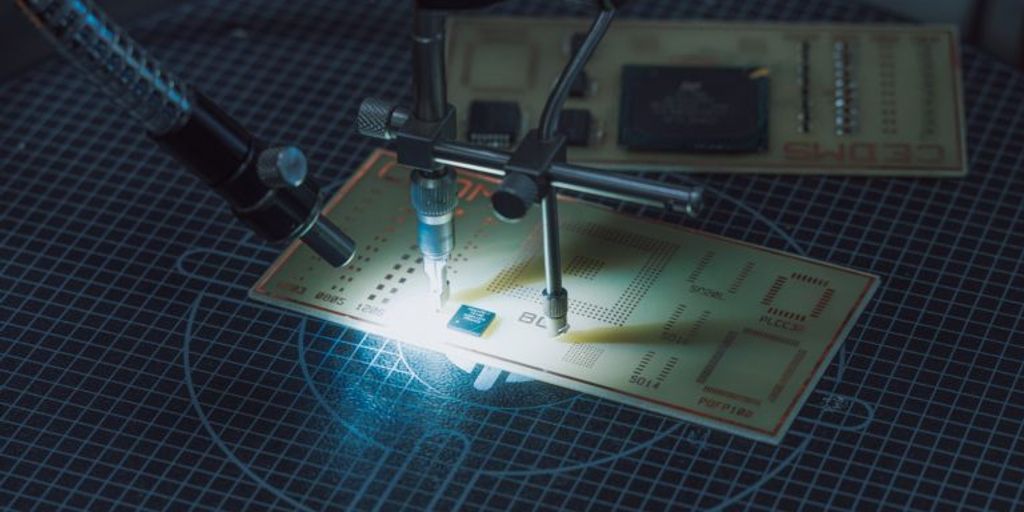
As technology continues to evolve at a rapid pace, understanding the process of semiconductor fabrication, often abbreviated as ‘fab’, becomes increasingly important. This article delves into the intricate world of semiconductor fab, exploring the key processes and innovations that drive this essential industry. From the initial stages of wafer preparation to the cutting-edge materials and technologies that enhance performance and efficiency, we uncover the complexities and challenges that shape the semiconductor landscape.
Key Takeaways
- Semiconductor fabrication is a multi-step process that includes wafer preparation, photolithography, etching, doping, and more.
- Advancements in materials such as silicon and emerging materials like carbon nanotubes are pivotal for future developments.
- Technological innovations, particularly in automation and precision, play a crucial role in enhancing fab processes.
- Environmental considerations and sustainability are increasingly important in the ongoing development of semiconductor fab.
- Collaborations between industry, academia, and cross-industry sectors are vital for driving innovation and addressing challenges.
Understanding the Semiconductor Fab Process
Wafer Preparation
The initial stage in semiconductor fabrication is wafer preparation, where a pure semiconductor crystal, typically silicon, is grown and then sliced into thin discs called wafers. These wafers serve as the substrate for subsequent fabrication processes.
Photolithography
Photolithography is a critical process where patterns are transferred onto the wafer using light-sensitive chemicals. This step defines the intricate patterns of the circuitry that will eventually form the electronic components.
Etching and Doping
Following photolithography, etching removes unwanted material to create the desired circuit patterns. Doping is then performed, where specific chemicals are introduced to alter the electrical properties of the semiconductor, a key step in forming functional electronic devices.
Advancements in Semiconductor Materials
Silicon and Beyond
Silicon has long been the backbone of semiconductor technology, but the industry is increasingly looking towards alternative materials that offer superior performance and efficiency. Materials such as gallium arsenide and silicon carbide are becoming more prevalent due to their ability to operate at higher frequencies and resist higher temperatures.
Emerging Materials
The exploration of new semiconductor materials is pivotal for the advancement of technology. Materials like aluminium nitride, carbon nanotubes, and others are under intense research due to their promising semiconductor properties. These emerging materials are expected to revolutionize the industry as they mature.
Material Properties and Performance
The performance of semiconductor materials is critically dependent on their properties such as electrical conductivity, thermal stability, and electron mobility. Advances in material science have led to the development of materials that are not only more efficient but also more adaptable to complex electronic components. The ongoing research and development are crucial for maintaining a competitive edge in the global market.
Technological Innovations in Semiconductor Fab
Automation and Precision
The semiconductor industry has seen significant advancements in automation and precision, which are crucial for maintaining the high standards required in semiconductor fabrication. Automation technologies not only enhance the efficiency of the production process but also improve the consistency and quality of the final products. Key areas of automation include robotic handling systems, precision alignment tools, and automated inspection systems.
New Fabrication Techniques
Innovative fabrication techniques are pivotal in addressing the increasing complexity of semiconductor devices. Recent developments include advanced packaging techniques like 3D stacking and wafer-level packaging, which allow for greater functionality and performance within a smaller footprint. These techniques are essential for meeting the demands of modern electronics, including smartphones and high-performance computing devices.
Quality Control Advances
Advancements in quality control are vital for ensuring the reliability and performance of semiconductors. Modern fabs utilize sophisticated metrology and testing equipment to detect any defects during the fabrication process. This proactive approach to quality control helps in minimizing the risk of failures and ensures that the semiconductors meet the stringent requirements of various applications.
Challenges in Semiconductor Fabrication
Complexity and Cost
The semiconductor fabrication process is inherently complex, involving multiple intricate steps that require precise control and specialized equipment. The escalating complexity not only drives up the cost but also extends the time required for production. This complexity is further compounded by the rapid pace of technological advancements, which necessitates continuous investments in new technologies and training.
Yield Optimization
Achieving high yields is critical in semiconductor manufacturing due to the high costs associated with the fabrication process. Manufacturers strive to minimize defects and maximize output through sophisticated quality control systems and continuous process improvements. However, the miniaturization of devices presents significant challenges in maintaining high yields, as even minor imperfections can lead to device failure.
Environmental Considerations
The semiconductor manufacturing process involves the use of hazardous chemicals and generates significant amounts of waste. Managing these environmental impacts is crucial for sustainability. Companies are increasingly adopting greener technologies and waste reduction practices to mitigate these effects. Additionally, the industry faces regulatory pressures to comply with environmental standards, which can vary significantly across different regions.
The Role of Testing in Semiconductor Fab
Wafer Testing
Wafer testing is a critical step in semiconductor fabrication, ensuring that each wafer meets the necessary specifications before moving forward in the production process. This phase involves a variety of inspection and measurement techniques to identify and correct defects, and is pivotal in maintaining high manufacturing yields.
Final Product Testing
After the wafers are processed into semiconductor devices, final product testing is conducted to verify that the devices function as intended. This includes electrical testing, where key parameters such as voltage, current, and resistance are measured. Ensuring that devices meet performance and reliability standards is crucial for their suitability in intended applications.
Reliability and Quality Assurance
Reliability assessment is an ongoing process aimed at evaluating and improving the long-term performance and stability of semiconductor devices. Techniques used include stress testing and environmental testing, which help to predict and enhance the device’s durability and operational reliability. This stage is essential for driving innovation and maintaining competitive edge in the semiconductor industry.
Future Trends in Semiconductor Fabrication
Scaling Down
The relentless pursuit of miniaturization continues to drive the semiconductor industry. The trend towards smaller, more efficient devices is not only a testament to technological progress but also a response to the growing demand for high-performance, space-efficient components. As technology advances, the semiconductor fabrication process evolves, enabling the creation of increasingly complex and powerful devices.
Integration of AI
Artificial intelligence (AI) is set to revolutionize semiconductor fabrication by enhancing automation and precision. AI’s role in predictive maintenance, process optimization, and defect detection will significantly improve production efficiency and yield rates. This integration promises a future where smart fabs can anticipate and rectify issues autonomously, leading to more reliable outputs.
Sustainability in Manufacturing
The semiconductor industry is increasingly focusing on reducing its environmental footprint. Sustainable practices in manufacturing are not just about compliance but also about improving efficiency and reducing waste. Innovations such as the use of less harmful materials and the implementation of energy-efficient processes are pivotal in driving the industry towards a more sustainable future.
Notable Collaborations and Their Impact on Semiconductor Fab
Industry Partnerships
The semiconductor industry has seen significant collaborations that have shaped the landscape of fabrication technology. One notable example is the partnership between TSMC, Robert Bosch GmbH, NXP Semiconductors, and Infineon Technologies to establish a new semiconductor plant in Germany. This collaboration, with an investment exceeding 10 billion euros, highlights the strategic alliances forming to advance semiconductor manufacturing capabilities.
Academic Contributions
Academic institutions play a crucial role in advancing semiconductor technology through research and innovation. Universities often collaborate with industry leaders to develop new materials and processes that push the boundaries of what is possible in semiconductor fabrication. These partnerships are vital for nurturing the next generation of engineers and researchers.
Cross-Industry Innovations
Cross-industry collaborations are becoming increasingly important as semiconductor technology intersects with other fields such as biotechnology and robotics. These partnerships not only enhance the capabilities of semiconductors but also enable significant advancements in various applications, making them more efficient and capable.
Conclusion
In conclusion, the semiconductor fabrication process is a highly intricate and specialized series of steps that involve a wide range of techniques and technologies. From the initial crystal growth and wafer preparation to the final packaging of the device, each stage requires careful attention to detail and precise control to ensure the production of high-quality, reliable electronic components. As we have explored in this article, the continuous advancements and innovations in semiconductor fab technology not only enhance the capabilities of electronic devices but also drive the digital revolution forward, shaping the future of technology.
Frequently Asked Questions
What are the main stages of the semiconductor fabrication process?
The main stages include wafer preparation, photolithography, etching, doping, metallization, passivation, packaging, and testing.
How has semiconductor material technology advanced?
Advances include the exploration of new materials beyond traditional silicon, such as gallium arsenide, aluminium nitride, and carbon nanotubes, which offer enhanced properties and performance.
What innovations have been made in semiconductor fabrication techniques?
Innovations include increased automation, precision in manufacturing processes, and the development of new fabrication techniques that improve efficiency and yield.
What are the major challenges in semiconductor fabrication?
The major challenges include managing complexity and cost, optimizing yield, and addressing environmental considerations during manufacturing.
How does testing play a role in semiconductor fabrication?
Testing is crucial for ensuring the quality and reliability of semiconductors. It includes wafer testing, final product testing, and ongoing quality assurance to meet stringent standards.
What future trends are expected in semiconductor fabrication?
Future trends include scaling down chip sizes, integrating artificial intelligence for improved manufacturing processes, and focusing on sustainability in production methods.