Integrating Efficiency: Advanced Industrial Automation and Control Systems Reviewed
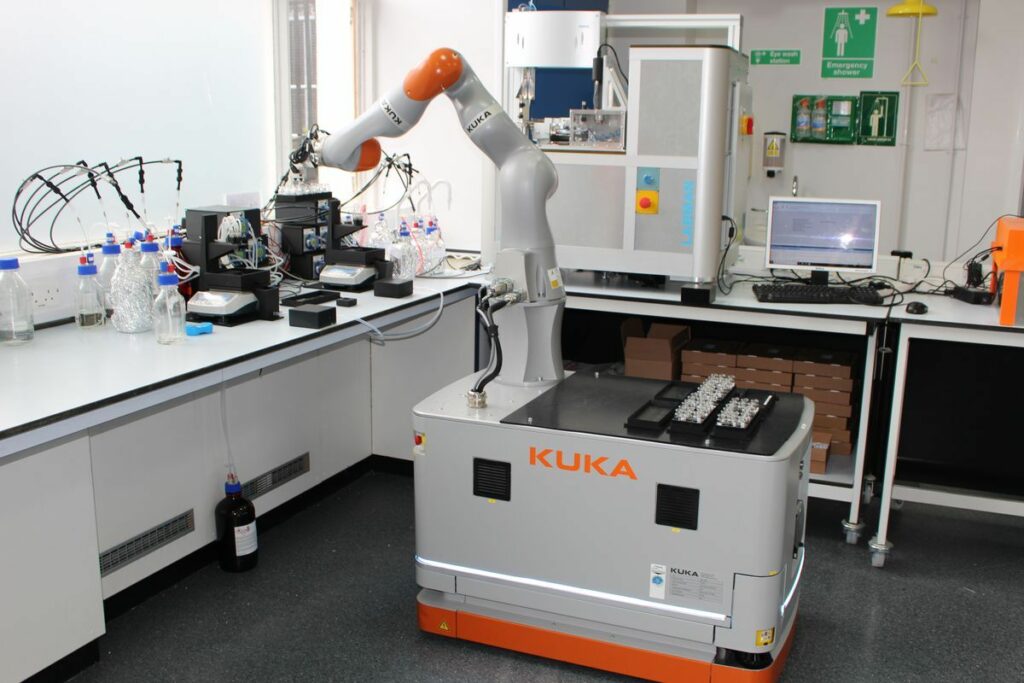
The industrial landscape is witnessing a transformative phase with the integration of advanced automation and control systems. This article delves into the nuances of industrial automation’s evolution, the optimization of production through next-generation control systems, and the advancements in motor control automation. It also addresses the crucial aspects of safety and maintenance in automated environments and looks ahead at emerging technologies and future trends that are set to redefine manufacturing efficiency.
Key Takeaways
- Industrial automation has evolved from simple mechanical aids to complex, integrated SCADA systems, paving the way for smart factories.
- Next-generation control systems offer significant benefits in production planning and scheduling, leading to optimized operations and increased efficiency.
- Advanced algorithms and energy-efficient strategies in motor control automation are crucial for improving manufacturing process productivity.
- Safety and proactive maintenance are paramount in automated environments, with diagnostics and predictive maintenance playing key roles.
- Emerging technologies, such as AI and advanced sensor components, are driving the future of industrial automation, necessitating readiness for regulatory changes.
The Evolution of Industrial Automation
Historical Perspective on Control Systems
The journey of industrial automation and control systems has been marked by continuous innovation and technological advancements. Initially, control systems were predominantly mechanical, relying on gears and levers to manage machinery. As industries grew, the need for more precise and reliable control led to the development of electrical and electronic systems, which offered greater accuracy and control over industrial processes.
The transition from mechanical to electronic control systems was a pivotal moment in industrial automation. This shift allowed for the introduction of programmable logic controllers (PLCs) and computer-based systems, which provided a new level of flexibility and efficiency. The design and architecture of these systems became crucial, with considerations such as open-loop vs. closed-loop control, and centralized vs. decentralized architecture shaping the future of industrial control.
With the advent of integrated solutions, industrial control systems began to offer real-time visibility and enhanced decision support. This integration was a significant step towards the development of smart factories, where all aspects of manufacturing operations are managed through a unified platform. The table below outlines the key milestones in the evolution of industrial control systems:
Era | Control System Type | Characteristics |
---|---|---|
Mechanical | Gears and Levers | Limited precision |
Electrical | Relays and Switches | Improved reliability |
Electronic | PLCs and Computers | Flexibility and efficiency |
Integrated | Unified Platforms | Real-time visibility |
As we continue to explore the history of industrial automation, it is clear that the evolution of control systems has been integral to the rise of modern manufacturing. The ability to adapt and scale these systems to meet future needs remains a cornerstone of industrial progress.
The Rise of Smart Factories
The transition from traditional manufacturing to the era of smart factories represents a paradigm shift in industrial operations. The integration of Industry 4.0 technologies has led to the creation of highly connected and automated environments where data-driven decision-making enhances efficiency and productivity.
Smart factories leverage a combination of sensors, automation, and advanced control systems to achieve streamlined production. These integrated solutions provide real-time visibility and foster collaboration across various manufacturing processes. As a result, businesses can respond more agilely to changes and optimize their production planning and scheduling.
The table below highlights key components that characterize smart factories and their impact on manufacturing:
Component | Impact on Manufacturing |
---|---|
Sensors | Enables real-time data exchange |
Automation | Streamlines production processes |
Control Systems | Improves decision support |
Embracing these advancements, manufacturers are not only able to increase operational efficiency but also gain a competitive edge by being more responsive to market demands and supply chain dynamics.
Integrating Advanced SCADA Systems
The integration of advanced Supervisory Control and Data Acquisition (SCADA) systems has become a cornerstone in the modernization of industrial automation. These systems offer unparalleled visibility and control over industrial processes, enhancing operational efficiency and decision-making. With the ability to monitor and manage data from a centralized platform, SCADA systems have evolved to support the flexibility required for sustainable and profitable operations.
Recent trends in SCADA software have been instrumental in advancing the Industrial Internet of Things (IIoT) implementations. These advancements include improved integration with other systems, enhanced infrastructure monitoring, and better database connectivity. The following list highlights critical areas where SCADA software is making a significant impact:
- Northward and southward integration flows
- Database integration for streamlined data management
- Infrastructure monitoring for proactive maintenance
- Support for open architecture and shared data paradigms
- Facilitation of industry 4.0 and smart manufacturing applications
As SCADA systems continue to advance, they are expected to play an even more vital role in the context of Industry 4.0, where manufacturing applications demand real-time data and adaptive control mechanisms. The integration of SCADA with other systems such as Manufacturing Execution Systems (MES) and Statistical Process Control (SPC) is already demonstrating significant improvements in operations, as seen in the case of a steel pipe manufacturer that implemented these technologies to enhance their production processes.
Optimizing Production with Next-Generation Control Systems
Benefits of Integrated Solutions
The advent of integrated solutions in industrial automation marks a significant leap forward from traditional systems. These unified platforms offer a comprehensive approach to managing various manufacturing operations, providing real-time visibility and enhanced decision-making capabilities. The integration of systems such as PlanetTogether with ERP, SCM, and MES transforms the production landscape, fostering agile and responsive planning processes.
Key benefits of integrated solutions include:
- Real-time data synchronization across departments
- Optimized production scheduling for maximum efficiency
- Seamless communication and collaboration among stakeholders
- Continuous improvement through monitoring and feedback
Engaging stakeholders early in the integration process is crucial for tailoring the solution to meet the needs of the entire organization. By leveraging best practices and learning from successful case studies, manufacturers can harness the full potential of integrated solutions to boost productivity, quality, and competitiveness in the market.
Production Planning and Scheduling Enhancements
The landscape of production planning and scheduling is transforming with the integration of advanced control systems. These systems bring about a new level of precision and efficiency, setting targets and creating detailed plans to meet customer demand in a timely and cost-effective manner.
Optimized production scheduling is a critical component in manufacturing, addressing the complex puzzle of resource constraints, lead times, and production capacities. By leveraging advanced algorithms, these integrated systems generate schedules that minimize idle time, reduce changeover costs, and maximize throughput. The result is a production plan that is not only feasible but also efficient and aligned with market demand.
Key enhancements in production planning and scheduling include:
- Seamless communication and collaboration across departments
- Adaptability to market changes and demand forecasting
- Real-time data access for agile decision-making
- Improved resource allocation and shop floor visibility
These improvements ensure that manufacturers can respond quickly to changes, maintain high levels of quality control, and optimize inventory management. The integration of predictive analytics and what-if scenarios further enhances accuracy and efficiency, enabling a proactive approach to production management.
Case Studies: Successful Integrations
The journey to successful industrial automation integration is often paved with challenges. Challenges in complex projects are inevitable, but the dedication to overcome these hurdles is a hallmark of exceptional system integration firms. For instance, the Automation Group’s commitment to solving intricate issues during integration projects has set them apart in the industry.
Best practices for successful integration involve careful planning and execution. Engaging stakeholders from various departments early in the process is crucial. Their insights and feedback are invaluable for ensuring that the integrated solution meets the needs of the entire organization. Here’s a succinct table highlighting key practices:
Best Practice | Description |
---|---|
Engage Stakeholders | Involve key stakeholders for valuable insights |
Real-time Data Synchronization | Achieve seamless data flow |
Optimize Production Scheduling | Enhance efficiency and output |
By following these best practices and learning from real-world case studies, production planners can unlock the full potential of integrated solutions. This not only keeps them competitive but also transforms their manufacturing landscape.
Advancements in Motor Control Automation
Improving Efficiency with Advanced Algorithms
The integration of advanced control algorithms has revolutionized motor control automation, enabling systems to make real-time adjustments that optimize motor performance. These algorithms are designed to analyze various parameters and adjust operations for peak efficiency, leading to enhanced productivity and reduced energy consumption.
Key benefits of utilizing advanced algorithms include:
- Enhanced efficiency: By continuously adjusting to the optimal operating conditions, systems can significantly reduce waste and increase throughput.
- Improved accuracy: Precision in motor control ensures that processes are consistent, reducing the likelihood of errors and defects.
- Cost savings: Efficient motor operation translates to lower energy costs and reduced wear and tear on equipment, extending its lifespan.
The implementation of these algorithms is not without challenges, however. It requires a deep understanding of both the manufacturing process and the capabilities of the control systems in place. As such, companies often turn to specialized software and expertise to ensure successful integration.
Energy-Efficient Strategies for Motor Control
In the pursuit of sustainability, energy-efficient motor control strategies are becoming increasingly vital. Variable frequency drives (VFDs) and intelligent power management systems are at the forefront of this movement, offering significant reductions in energy consumption. By integrating these technologies, industries can achieve cost savings, comply with stringent environmental regulations, and minimize their ecological impact.
The implementation of energy-efficient motor control solutions is not only about reducing energy usage but also about enhancing overall operational performance. Best practices in this domain include regular maintenance schedules, the use of condition monitoring sensors, and remote diagnostics software. These practices ensure the longevity and reliability of equipment, while also contributing to a more sustainable production environment.
Motor Control Technology | Description | Benefits |
---|---|---|
Motor control algorithms | Algorithms that manage motor functions | Optimizes performance and energy efficiency |
Artificial intelligence | Enhances motor control systems | Predictive maintenance and quality improvement |
Internet of Things (IoT) | Provides seamless connectivity | Real-time monitoring and predictive analytics |
The Role of PLCs in Modern Manufacturing
Programmable Logic Controllers (PLCs) have become the cornerstone of modern industrial automation, offering unparalleled flexibility and control over manufacturing processes. Their ability to integrate with various systems and sensors has made them indispensable in the pursuit of operational excellence. PLCs are particularly valued for their robustness and reliability in harsh industrial environments, where precision and uptime are critical.
The cost-effectiveness of PLC systems is another significant advantage. While initial setup costs can be substantial, the long-term benefits of improved efficiency and reduced downtime often justify the investment. Below is a table illustrating the comparative costs and benefits of implementing PLCs in manufacturing:
Factor | Without PLCs | With PLCs |
---|---|---|
Efficiency | Lower | Higher |
Downtime | More Frequent | Less Frequent |
Flexibility | Limited | Extensive |
Long-term Costs | Higher | Lower |
In addition to cost savings, the integration of PLCs with other systems such as ERP, SCM, and MES enhances real-time visibility and collaboration across the manufacturing floor. This integration facilitates agile and responsive production planning, enabling manufacturers to adapt quickly to changing market demands or operational challenges.
Safety and Maintenance in Automated Environments
Ensuring Operational Safety
In the realm of industrial automation, ensuring operational safety is not just a regulatory requirement but a foundational aspect of system design. Programmable Logic Controllers (PLCs) play a pivotal role in this context, as they are tasked with automating processes, monitoring equipment, and detecting potential hazards. By integrating safety features such as emergency stop circuits and motion detection sensors, industries can create a secure working environment that upholds productivity.
Safety compliance and traceability are critical throughout the lifecycle of industrial machines. A well-designed safety system incorporates multiple layers of protection, including:
- Emergency shutdown mechanisms
- Safety interlocks
- Redundancy in critical components
- Electrical circuit protection
These systems must adhere to stringent standards and regulations to ensure they provide effective protection against accidents and hazards. Moreover, the integration with industrial communication networks is essential for the seamless operation and safety monitoring of modern machinery.
Maintenance Best Practices
In the realm of industrial automation, maintenance is a critical factor that directly impacts production efficiency and equipment longevity. Adopting a proactive maintenance approach is essential for minimizing unplanned downtime and optimizing resource allocation. By focusing on predictive maintenance capabilities, manufacturers can anticipate potential issues before they escalate into costly disruptions.
To achieve the final goal of maintenance, which may be to increase equipment uptime, reduce maintenance costs, or improve the quality of maintenance, it is important to adhere to a set of best practices. Here are the top five maintenance best practices:
- Monitor Key Performance Indicators (KPIs) to assess the health of machinery.
- Implement continuous improvement strategies to refine maintenance processes.
- Link MES Systems for real-time monitoring and faster response times.
- Optimize resource allocation to ensure that maintenance tasks are performed efficiently.
- Identify key data points for process optimization and preventive measures.
These practices not only enhance the reliability of equipment but also contribute to a more resilient and agile production environment.
Diagnostics and Predictive Maintenance
The integration of predictive maintenance technologies has revolutionized the approach to maintenance in industrial automation. By utilizing condition monitoring sensors and advanced diagnostics software, facilities can proactively identify and address potential issues, thereby reducing the likelihood of unexpected equipment failures and costly downtime.
Predictive maintenance strategies encompass a range of techniques aimed at proactive problem solving. These strategies include predictive inventory management, asset optimization, and quality control, all of which contribute to a more efficient and reliable production process. The table below outlines some key aspects of predictive maintenance:
Aspect | Description |
---|---|
Predictive Inventory Management | Ensures availability of spare parts before they are needed. |
Asset Optimization | Enhances equipment performance and extends lifespan. |
Equipment Optimization | Improves machine efficiency and reduces wear and tear. |
Quality Control | Maintains high standards of production output. |
Proactive Decision-Making | Anticipates issues and allows for timely interventions. |
Embracing a proactive approach to maintenance not only minimizes disruptions but also facilitates better decision-making and risk mitigation. This shift towards predictive maintenance is a testament to the industry’s commitment to harnessing the power of data and analytics for improved operational efficiency.
Emerging Technologies and Future Trends
Innovations in Sensor and Component Technology
The landscape of industrial automation is being transformed by cutting-edge sensor and component technologies. High-resolution encoders, vibration sensors, and temperature sensors are now pivotal in providing real-time insights into motor performance and health. This advancement not only facilitates proactive maintenance but also significantly enhances manufacturing precision through sensor fusion techniques.
In the realm of space optimization, the trend is towards more compact and integrated systems. Consider the following developments:
- Compact components that save valuable space
- Integrated systems that combine multiple functions
- DIN rail mounting and panel layout optimization for efficient use of space
- Miniaturized sensors and actuators that maintain functionality while reducing footprint
- Modular enclosures and multi-functional devices that streamline installation and maintenance
These innovations are instrumental in driving the promise of Industry 4.0, enabling manufacturers to seamlessly integrate smart components and advanced automation into their production machinery and processes.
The Impact of AI and Machine Learning
The integration of Artificial Intelligence (AI) and Machine Learning (ML) into industrial automation has marked a significant shift in how control systems operate. AI algorithms are now essential in optimizing motor performance, reducing downtime, and enhancing production quality. These intelligent systems analyze vast amounts of data to predict maintenance needs and autonomously adjust operations, leading to unprecedented levels of efficiency and adaptability.
AI’s role extends beyond motor control to various aspects of manufacturing operations. Here are some key areas where AI contributes to industrial automation:
- AI-driven Demand Forecasting
- AI-Based Scheduling Capabilities
- Automated Decision Support
- Asset Maintenance and Reliability
- AI-Powered Analytics
As AI continues to evolve, its applications in industrial automation are expanding, offering new opportunities for innovation and improvement. The table below highlights the impact of AI in different aspects of manufacturing:
AI Application | Benefit |
---|---|
Demand Forecasting | Accelerates Response Times |
Scheduling | AI Techniques for Short Product Life Cycles |
Analytics | AI-Driven Demand Segmentation |
Maintenance | Predictive Maintenance Capabilities |
Embracing AI and ML not only enhances current processes but also prepares manufacturers for future challenges, ensuring they remain competitive in a rapidly changing industrial landscape.
Preparing for Regulatory Changes
As the industrial landscape evolves, regulatory changes play a pivotal role in shaping industry trends. Businesses must be agile, adapting to new rules and regulations that can significantly alter operational strategies. This adaptation often requires a responsive adjustment to compliance systems and processes.
To maintain a competitive edge, companies are increasingly turning to automation for regulatory compliance monitoring and documentation. Streamlined compliance and auditing can lead to enhanced resource optimization, ensuring that businesses remain within legal boundaries while pursuing efficiency. The following list highlights key areas where automation aids in regulatory adaptation:
- Regulatory compliance automation
- Streamlined compliance and reporting
- Risk management and compliance
- Enhanced traceability and compliance
In the face of these changes, scenario planning and what-if analysis become crucial for risk mitigation and continuity planning. Companies that invest in real-time analytics and reporting are better equipped to respond to regulatory shifts, maintaining compliance without sacrificing operational agility.
Conclusion
The exploration of advanced industrial automation and control systems reveals a landscape of innovation and efficiency poised to redefine manufacturing processes. From the integration of SCADA systems by system integrators to the energy-efficient strategies of advanced motor control systems, the advancements discussed underscore the transformative impact on productivity, safety, and maintenance. As we have seen, next-generation control systems like PlanetTogether’s integrated solutions offer a compelling vision for optimizing production planning. The future of industrial automation is not only about embracing new technologies but also about integrating them seamlessly to harness their full potential. The insights provided by experts and the practical applications reviewed serve as a testament to the potential gains in efficiency and competitiveness for those ready to invest in these cutting-edge solutions. As the industry continues to evolve, the integration of sophisticated automation and control systems will undoubtedly remain a critical factor in driving the success of manufacturing enterprises worldwide.
Frequently Asked Questions
What are the key benefits of integrating advanced SCADA systems in smart factories?
Advanced SCADA systems offer real-time data acquisition, enhanced monitoring and control, improved production efficiency, and better decision-making capabilities. They support the rise of smart factories by enabling predictive maintenance, minimizing downtime, and providing a platform for IoT connectivity.
How do next-generation control systems optimize production planning and scheduling?
Next-generation control systems integrate with ERP, SCM, and MES systems to provide comprehensive insights and automation capabilities. They enable more efficient resource allocation, reduce lead times, and improve overall production flow through advanced algorithms and data analytics.
What advancements in motor control automation contribute to manufacturing efficiency?
Advancements in motor control automation, such as the use of advanced algorithms and programmable logic controllers (PLCs), enhance precision and energy efficiency. They allow for better control over motor performance, reduce energy consumption, and minimize wear and tear, leading to improved productivity.
What are the best practices for maintenance in automated industrial environments?
Best practices include regular inspections, predictive maintenance using diagnostics tools, timely replacement of worn-out parts, and training staff on the latest technologies. This proactive approach prevents unexpected breakdowns, extends equipment lifespan, and ensures continuous operation.
How is the integration of AI and machine learning impacting industrial automation?
AI and machine learning are revolutionizing industrial automation by enabling predictive analytics, adaptive control systems, and intelligent decision-making. These technologies help in optimizing processes, reducing waste, and improving quality control through advanced pattern recognition and data analysis.
What future trends should manufacturers prepare for in industrial automation?
Manufacturers should prepare for increased use of IoT devices, adoption of AI and machine learning, advancements in sensor technology, and stricter regulatory compliance. Staying ahead of these trends will require continuous innovation, investment in new technologies, and upskilling of the workforce.