Investing in the Future: The Latest Industrial Automation Equipment for Modern Manufacturing
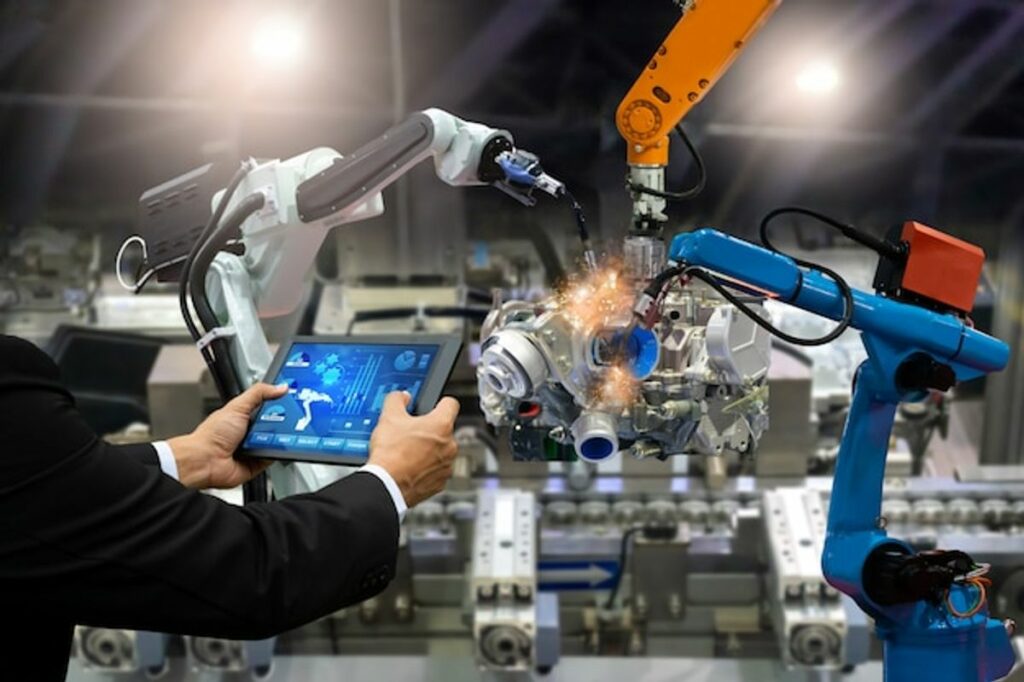
In the fast-evolving landscape of modern manufacturing, industrial automation stands at the forefront of innovation and efficiency. This article delves into the latest advancements in automation equipment and strategies, providing insights into how manufacturers can leverage these technologies to stay ahead in a competitive market. From strategic investments in automation to the integration of robotics and real-time data analytics, we explore the various facets that are shaping the future of manufacturing.
Key Takeaways
- Strategic investment in automation is critical for manufacturers to enhance efficiency and remain competitive, with capital allocation focusing on key technologies like AGVs/AMRs, remote controls, and intelligent systems.
- Technological innovations such as intelligent manufacturing systems, industrial Ethernet, and AI for predictive maintenance are revolutionizing the industry by increasing connectivity and efficiency.
- Real-time data is transforming manufacturing operations by enabling a data-centric model that turns plant floor data into actionable insights for improved decision-making.
- The integration of advanced robotics, including collaborative robots, is increasing throughput and altering workforce dynamics, signaling a shift towards more technologically synergized production environments.
- Manufacturing mergers and acquisitions are influencing automation strategies, and staying informed about these trends is essential for companies to make savvy equipment investments and maintain a competitive edge.
Strategic Automation Investment
Assessing Capital Allocation for Automation
Integrating automation into manufacturing processes is not just a trend; it’s a strategic imperative for companies aiming to enhance efficiency and remain competitive. Effective capital allocation is crucial for maximizing the benefits of automation technologies. It involves a careful analysis of current manufacturing processes to identify areas where automation can be seamlessly adopted and deliver the most impact. For instance, adopting a monorail system can be a cost-efficient way of moving products through production steps.
When considering capital allocation for automation, it’s important to focus on technologies that align with the company’s long-term goals and production needs. This may include Advanced Guided Vehicles (AGVs), Autonomous Mobile Robots (AMRs), radio remote controls, and safeguard sensors. A McKinsey & Company report highlights that automation could represent 25% of industrial companies’ capital spending over the next five years, underscoring the growing importance of strategic investment in this area.
To ensure that the allocated capital is utilized effectively, ongoing monitoring and evaluation of investments are essential. This includes tracking the performance of the automation equipment and making necessary adjustments. Additionally, investing in training programs is vital to equip the workforce with the skills needed to operate and maintain the new equipment, thereby maximizing its potential and ensuring operational efficiency.
Identifying Key Technologies for Modern Manufacturing
To thrive in the rapidly evolving manufacturing landscape, companies must pinpoint and adopt key technologies that bolster smart manufacturing. Condition monitoring and AI-powered vision systems are at the forefront, providing critical insights into production processes and ensuring quality control. Additionally, the adoption of message queuing telemetry transport (MQTT) and modern supervisory control and data acquisition (SCADA) systems is pivotal for enhancing operational flexibility and sustainability.
The integration of these technologies facilitates automated decision workflows, which streamline production and minimize human error. For instance, vision system AI can significantly improve quality assurance, while MQTT enables efficient machine monitoring. Here’s a brief overview of how each technology contributes to manufacturing excellence:
- Condition Monitoring: Vital for predictive maintenance, reducing downtime.
- Vision System AI: Enhances quality assurance through precise defect detection.
- MQTT: Facilitates real-time data communication, optimizing productivity.
- Modern SCADA Systems: Provides robust control and monitoring, improving overall quality.
Embracing these technologies not only improves repetitive tasks but also lays the groundwork for a data-driven, predictive approach to manufacturing. As the industry continues to advance, staying abreast of these developments is crucial for maintaining a competitive edge.
Ensuring Seamless Integration of New Equipment
The successful integration of new automation equipment hinges on meticulous planning and execution. Investing in training programs is crucial, as it equips the workforce with the necessary skills to operate and maintain the new technology, thereby maximizing its potential. Additionally, the integration process is streamlined when employees are adept at using the equipment, which can also reduce onboarding times for new hires.
Selecting the right equipment is foundational to a seamless automation strategy. Facility managers must source solutions that align with their production needs and long-term goals. This involves engaging with reliable vendors who offer a comprehensive portfolio of products and can guide you to the best solution for your operations. A partnership with a knowledgeable vendor ensures not only the acquisition of suitable equipment but also the proper training of staff on its operations.
The integration of automation into manufacturing processes is not just about the technology itself but also about the strategic alignment with business objectives. As automation accounts for a significant portion of capital spending, it’s imperative to locate existing pain points and address them with tailored solutions. This strategic approach ensures that automation investments deliver the desired efficiency gains and competitive edge in the market.
Technological Innovations in Industrial Automation
The Rise of Intelligent Manufacturing Systems
Intelligent manufacturing represents a transformative leap in production capabilities, characterized by the integration of advanced technologies such as condition monitoring, vision system AI, MQTT, and modern SCADA systems. These innovations are not mere futuristic concepts but are actively shaping the present landscape of industrial automation.
The maturation of predictive and real-time intelligence in manufacturing marks a natural progression towards AI applications. This evolution is not just about adopting new technologies but also necessitates organizational and operational shifts, with a strong focus on return on investment (ROI).
Key Technologies for Intelligent Manufacturing:
- Condition Monitoring
- Vision System AI
- MQTT (Message Queuing Telemetry Transport)
- SCADA (Supervisory Control and Data Acquisition)
As the industry embraces intelligent systems, the demand for skilled talent is also growing. Initiatives to nurture talent pipelines at the college level are crucial for sustaining the innovation and efficiency that intelligent manufacturing promises.
Adopting Industrial Ethernet for Enhanced Connectivity
The shift towards Industrial Ethernet is a game-changer in manufacturing, offering a unified solution that marries operational technology (OT) security with network design. This convergence simplifies the network architecture, eliminating the need for single-purpose products and paving the way for a more streamlined and secure system.
Industrial Ethernet’s modular designs, high Mean Time Between Failures (MTBF), and Power over Ethernet (PoE) capabilities contribute to sustainability by reducing the need for component replacement and energy consumption. These features, along with the ability to run visibility and security applications directly within the network, enhance the efficiency and resilience of manufacturing operations.
The integration of Time-Sensitive Networking (TSN) standards into Industrial Ethernet is particularly noteworthy. TSN ensures deterministic communication, which is essential for the precise timing required in industrial automation. The benefits of TSN include:
- Improved efficiency
- Easier network management
- Cost-effectiveness
By adopting Industrial Ethernet, manufacturers can enjoy increased automation levels, simplified cabling, and the ability to transmit vast volumes of data for real-time analysis and actionable insights.
Leveraging AI for Predictive Maintenance and Efficiency
The integration of Artificial Intelligence (AI) in industrial maintenance is revolutionizing the way manufacturers approach equipment upkeep and efficiency. By utilizing sensors for equipment health assessment, AI enables the prediction of faults before they occur, significantly reducing downtime and optimizing energy use. This proactive approach not only enhances production efficiency but also contributes to environmental sustainability through targeted improvements.
AI-driven vision systems represent another leap forward, swiftly detecting defects to streamline production flexibility. These systems minimize waste and play a crucial role in quality control, offering adaptable and scalable solutions for various manufacturing processes. The implementation of AI in predictive maintenance is supported by the backbone of modern manufacturing systems, such as the enterprise resource planning (ERP) system, manufacturing execution system (MES), or computerized maintenance management system (CMMS).
However, the practical application of predictive maintenance faces challenges, such as defining relevant measurement data, preparing the data for analysis, and establishing complex evaluation criteria for each specific application. Despite these hurdles, the potential of AI and machine learning (ML) to provide insights and predictions based on data is a game-changing force in the industry.
Optimizing Manufacturing Through Real-Time Data
Building a Data-Centric Operational Model
In the pursuit of a data-centric operational model, manufacturers are increasingly turning to advanced tools and methodologies that enable the efficient use of data. The goal is to transform raw data into meaningful insights that drive decision-making and operational efficiency.
Key components in building such a model include data integration tools, decision management systems, and in-memory computing. These elements work in tandem to provide a robust framework for data processing and analysis. Intelligent integration, along with Business Process Management (BPM), further streamline operations, ensuring that data is not only collected but also acted upon in a timely manner.
The following list outlines essential resources that support the development of a data-centric operational model:
- Data in Motion
- Smart Manufacturing for Automotive
- Center for Data Pipeline Automation
- Improving Service and Profits With Connected Products
- Center for Edge Computing and 5G
- Center for Observability and AIOps
- Continuous Intelligence Insights
- Event-Driven Architecture for the Cloud
By leveraging these resources, manufacturers can build a data infrastructure that not only supports current operations but is also scalable for future demands.
Harnessing the Power of Real-Time Intelligence
The advent of real-time intelligence in manufacturing has revolutionized the way operations are managed and optimized. By leveraging data as it is generated, manufacturers can make informed decisions swiftly, reducing downtime and enhancing productivity. This shift towards a more dynamic operational model is not just about faster data processing; it’s about transforming data into a strategic asset.
Real-time intelligence enables a proactive approach to maintenance and operations. For instance, sensor data from production lines can be analyzed instantly to predict and prevent potential issues before they escalate into costly downtime. This not only improves machinery health but also ensures consistent performance levels. The table below illustrates the benefits of real-time intelligence in manufacturing:
Benefit | Description |
---|---|
Predictive Maintenance | Anticipates machinery issues before they occur. |
Performance Optimization | Monitors and adjusts operations for peak efficiency. |
Quality Assurance | Ensures product standards are met consistently. |
Energy Savings | Identifies and eliminates wasteful processes. |
In the words of NVIDIA CEO Jensen Huang, the ‘heavy lifting’ in sectors like manufacturing and robotics is increasingly supported by real-time AI. This underscores the importance of integrating advanced technologies to stay competitive in the modern manufacturing landscape.
Transforming Plant Floor Data into Actionable Insights
The ability to transform plant floor data into actionable insights is a game-changer for modern manufacturing. This instantaneous data provides a live snapshot of the factory floor, allowing for immediate analysis and action. By leveraging technologies such as artificial intelligence (AI) and machine learning (ML), manufacturers can predict and preempt potential issues, ensuring continuous improvement and operational excellence.
To effectively utilize plant floor data, a structured approach is essential. Here are the steps to consider:
- Identify critical data points that will drive decision-making.
- Implement technologies to capture and analyze data in real-time.
- Engage with system integrators and vendors to leverage external expertise.
- Apply insights to optimize processes and prevent costly downtime.
The focus on predictive insights rather than reactive measures marks a significant shift in industrial operations. With the right tools and strategies, manufacturers can harness the power of data to drive efficiency and gain a competitive edge.
The Role of Robotics in Modern Manufacturing
Increasing Throughput with Advanced Robotics
The integration of advanced robotics into manufacturing processes is a game-changer for industries aiming to enhance productivity. Robots are not only becoming more affordable but also increasingly sophisticated, with capabilities such as ‘imitation learning’ allowing them to self-teach and improve over time. The result is a significant boost in efficiency, as these machines can operate around the clock without fatigue.
The demand for such intelligent automation solutions is driven by a combination of factors, including labor shortages and the relentless pursuit of greater efficiency. Companies like Rockwell are at the forefront, leveraging platforms like NVIDIA’s for edge AI to introduce autonomous mobile robots (AMRs) and advanced process automation to the industrial sector.
Investment in automation technology is rapidly becoming a top priority for businesses. A McKinsey & Company report highlights that automation could represent a quarter of capital spending in industrial companies within five years. This surge in investment is expected to encompass a wide range of automation equipment, from AGVs and AMRs to sophisticated sensor systems, all aimed at increasing throughput and maintaining a competitive edge.
Integrating Collaborative Robots into Production Lines
The integration of collaborative robots, or cobots, into production lines marks a significant shift in manufacturing dynamics. Cobots are designed to work alongside human operators, enhancing productivity and safety. Unlike traditional robots, cobots are equipped with advanced sensors and safety features that allow them to detect and respond to the presence of humans, reducing the risk of accidents.
Key benefits of integrating cobots into production lines include:
- Improved worker safety through precision and consistency
- Increased production flexibility
- Enhanced quality control
- Reduction in labor costs
As companies adopt cobots, they often follow a phased approach:
- Identify repetitive and ergonomically challenging tasks.
- Select appropriate cobot systems that can safely interact with workers.
- Implement cobot solutions in stages, starting with simple tasks.
- Train employees to manage and work effectively with cobots.
- Continuously monitor and optimize cobot performance.
This strategic approach ensures that the adoption of cobots leads to a harmonious and efficient collaboration between human workers and robotic systems, ultimately driving forward the modern manufacturing landscape.
Exploring the Impact of Robotics on Workforce Dynamics
The integration of advanced robotics into industrial settings has brought about significant changes in the landscape of job roles within various industries. Manufacturers are increasingly adopting smart manufacturing technologies, including collaborative robots (cobots) and autonomous mobile robots (AMRs), which are reshaping the workforce. A recent survey highlights the industry’s response to these changes:
- 95% of manufacturers are using or evaluating smart manufacturing technology.
- 94% plan to maintain or grow their workforce, focusing on repurposing workers to new roles or hiring more.
- Change management emerges as a key obstacle in workforce adaptation.
The enormous potential for robotics, particularly cobots, is evident as they become more affordable and user-friendly. The concept of ‘imitation learning’ allows robots to teach themselves, further enhancing their integration into the workforce. However, this technological shift necessitates a strategic approach to workforce management. As Cyril Perducat, senior vice president and chief technology officer at Rockwell Automation, points out, technology alone is not the solution. To stay competitive, there must be a concerted effort to foster a culture where technology and workers form a symbiotic partnership.
Navigating the Manufacturing M&A Landscape
Understanding the Drivers of Manufacturing Mergers and Acquisitions
The landscape of manufacturing mergers and acquisitions (M&A) is shaped by a myriad of factors, each playing a pivotal role in the decision-making processes of industry leaders. Deal activity in the industrial manufacturing and automotive sectors is expected to increase, driven by the need to integrate advanced automation technologies and to adapt to market challenges such as inflation.
Key drivers of M&A include the pursuit of technological synergies, expansion into new markets, and the acquisition of specialized capabilities. Companies are actively seeking to enhance their competitive edge by acquiring firms with established automation systems, which can lead to significant improvements in efficiency and throughput.
The table below summarizes the primary motivations behind manufacturing M&A:
Motivation | Description |
---|---|
Technological Synergy | Merging to combine advanced technologies and innovation. |
Market Expansion | Acquiring companies to enter new markets or regions. |
Capability Acquisition | Buying firms with specialized automation expertise. |
As the industry evolves, staying informed about global M&A trends becomes crucial. A report by PwC highlights that the industrial manufacturing and automotive sectors are gearing up for an uptick in deal activity, suggesting a strategic focus on automation as a key factor in future transactions.
Evaluating the Impact of M&A on Automation Strategies
Mergers and Acquisitions (M&A) in the manufacturing sector can significantly influence automation strategies. The alignment of automation goals post-M&A is crucial for realizing the full potential of combined operations. Companies must evaluate how the integration of different automation systems can affect overall productivity and efficiency.
Key considerations include:
- Compatibility of existing automation technologies between merged entities.
- The potential for unified process optimization and cost savings.
- Strategies for workforce adaptation and training in new automated environments.
Post-M&A, businesses often face the challenge of harmonizing disparate automation systems. A McKinsey & Company report highlights that automation accounts for a substantial portion of capital spending, underscoring the importance of strategic investment in this area. Scalable solutions that can adapt to the merged entity’s evolving needs are essential for long-term success. Additionally, investing in employee training programs is pivotal to maximize the benefits of new automation technologies and maintain operational efficiency.
Staying Ahead of Trends in Industrial Equipment Investment
To maintain a competitive edge in the dynamic landscape of industrial automation, it’s crucial for manufacturers to stay informed about the latest investment trends. Keeping abreast of emerging technologies and market shifts can guide strategic investment decisions and foster innovation. For instance, the Association for Advancing Automation provides valuable insights into the evolving robotics and automation sectors, which can be instrumental for planning future investments.
Understanding the financial landscape is equally important. Recent reports, such as the ‘Insight into Robotics & Automation Investment Trends in 2024‘, highlight the significance of venture capital in shaping the future of manufacturing technologies. As spending on Industry 4.0 solutions is projected to exceed $950 billion by 2030, manufacturers must act swiftly to avoid being outpaced by competitors who are already investing in these advanced systems.
Investment in training programs is another key trend that cannot be overlooked. Equipping the workforce with the necessary skills to operate and maintain new equipment is vital for maximizing the potential of automation investments. Automated systems also streamline the training process for new employees, reducing onboarding times and enhancing operational efficiency.
Embracing the Future of Manufacturing with Smart Automation
As we have explored throughout this article, the landscape of modern manufacturing is rapidly evolving, driven by the relentless advancement of industrial automation equipment. From AGVs and AMRs to intelligent SCADA systems and real-time intelligence, the integration of these technologies is not just a trend but a strategic imperative for businesses aiming to thrive in a competitive market. The insights provided by industry experts and the success stories of early adopters underscore the transformative impact of automation on efficiency, safety, and productivity. As capital spending on automation continues to grow, it is clear that the future of manufacturing lies in the smart, connected, and data-driven facilities that can adapt to changing demands with agility and foresight. For those willing to invest in the right equipment and embrace the potential of AI and real-time analytics, the rewards will be substantial. The era of intelligent manufacturing is here, and it is time for industry leaders to step forward and shape the future.
Frequently Asked Questions
What percentage of industrial companies’ capital spending is expected to go towards automation in the next five years?
According to a recent McKinsey & Company report, automation is set to account for 25% of industrial companies’ capital spending over the next five years.
What are some of the key technologies for modern intelligent manufacturing?
Key technologies for modern intelligent manufacturing include condition monitoring, vision system AI, MQTT, and modern SCADA systems.
How is Industrial Ethernet contributing to factory automation?
Industrial Ethernet is foundational to smart connected machines, edge and cloud-based computing, and the integration of IT-OT systems, which are all crucial for modern factory automation.
What are the benefits of real-time intelligence in manufacturing?
Real-time intelligence in manufacturing offers predictive insights, enhances operational efficiency, and supports a data-centric approach to improve short- and long-term operations.
How can robotics increase plant throughput?
Advanced robotics can increase plant throughput by enhancing precision, speed, and consistency in production lines, as well as by enabling 24/7 operations with minimal downtime.
What factors should be considered when integrating automation into manufacturing processes?
When integrating automation, it’s important to analyze current manufacturing processes to identify specific automation types that fit seamlessly, consider cost-efficiency, and align with long-term goals.