Leading Silicon Carbide Manufacturer: A Comprehensive Guide
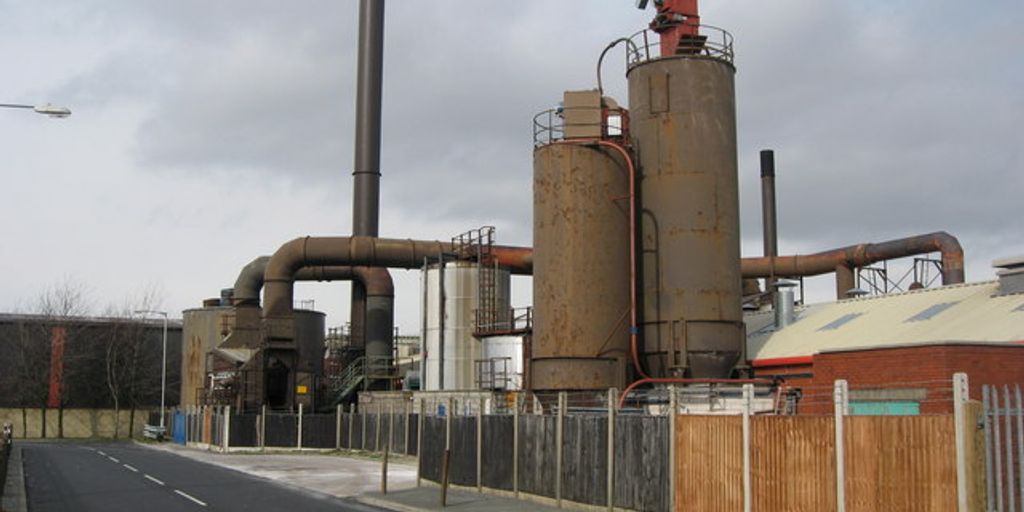
Silicon carbide (SiC) stands out as a revolutionary material in various industries due to its exceptional properties, including high thermal conductivity, mechanical strength, and electrical efficiency. This comprehensive guide delves into the key aspects of silicon carbide, from its fundamental properties to its wide-ranging applications, leading manufacturers, and future trends. Whether you’re in power electronics, automotive, aerospace, or any other sector, understanding silicon carbide’s impact and potential can significantly enhance your technological and operational capabilities.
Key Takeaways
- Silicon carbide offers superior thermal conductivity and mechanical strength, making it ideal for high-performance applications.
- The material is extensively used in power electronics, aerospace, and automotive industries due to its durability and efficiency.
- Top global companies and innovative startups are leading the silicon carbide manufacturing market, driving technological advancements.
- The manufacturing process of silicon carbide involves meticulous raw material sourcing, advanced production techniques, and stringent quality control measures.
- Future trends in silicon carbide technology indicate significant advancements in semiconductor applications and emerging industrial uses.
Key Properties of Silicon Carbide
Thermal Conductivity and Resistance
Silicon Carbide (SiC) is renowned for its high thermal conductivity and resistance to extreme temperatures. This makes it an ideal material for applications that require efficient heat dissipation and stability under high thermal stress. SiC can operate at elevated temperatures without warping or cracking, which is crucial for high-power and high-temperature applications.
Mechanical Strength and Durability
SiC boasts a Mohs hardness rating nearly equivalent to diamond, making it one of the hardest synthetic materials available. Its superior flexural strength and durability make it an excellent candidate for abrasive products like grinding wheels, paper, and cloth. Additionally, its corrosion resistance surpasses many other materials, ensuring longevity and reliability in harsh environments.
Electrical Properties
Silicon Carbide is a wide bandgap (WBG) material, which means it has a higher breakdown electric field strength and a larger band gap compared to traditional silicon. These properties enable SiC to perform exceptionally well in semiconductor applications, particularly in high-power, high-frequency, and high-temperature environments. SiC’s low electrical resistance and high thermal conductivity make it a staple in the electronics and semiconductor industry.
Major Applications of Silicon Carbide
Power Electronics
Silicon carbide is extensively used in the electronics and semiconductor industry. Its high thermal conductivity and low electrical resistance make it an excellent option for manufacturing diodes, transistors, and other electronic components. Applications include renewable energy systems like solar inverters and wind turbine converters, electric vehicle traction inverters, industrial motor drives, and high-voltage direct current (HVDC) transmission systems.
Aerospace and Defense
In the aerospace and defense industry, silicon carbide is used to manufacture parts for aircraft and spacecraft. The high strength-to-weight ratio of this material makes it ideal for producing lightweight components that can withstand high temperatures, vibrations, and pressure. Silicon carbide is also used in radomes, which are protective shells for radar antennas, and heat shields for missiles and spacecraft.
Automotive Industry
Silicon carbide is widely used in the automotive industry, especially in manufacturing engine components. Its high-temperature resistance and corrosion resistance make it suitable for making pistons, bearings, and other engine parts. Additionally, silicon carbide is used in brake systems due to its excellent thermal conductivity and stability at high temperatures, ensuring better stopping power and reduced wear and tear.
Top Silicon Carbide Manufacturers
The major players in the silicon carbide market with a significant global presence are STMicroelectronics N.V. (Switzerland), Infineon Technologies AG (Germany), and Cree, Inc. (USA). These companies lead the industry in innovation and production capacity, ensuring a steady supply of high-quality silicon carbide products.
Several startups are making waves in the silicon carbide industry by introducing cutting-edge technologies and innovative solutions. Companies like Wolfspeed and GeneSiC Semiconductor are at the forefront, pushing the boundaries of what silicon carbide can achieve in various applications.
In addition to global giants, regional market leaders play a crucial role in the silicon carbide industry. Companies such as Showa Denko K.K. (Japan) and ROHM Co., Ltd. (Japan) have established themselves as key players in their respective regions, contributing significantly to the market’s growth and development.
Manufacturing Process of Silicon Carbide
Raw Material Sourcing
The manufacturing process of silicon carbide begins with the sourcing of high-purity raw materials. Silicon carbide is typically produced from silica sand and carbon, which are subjected to high temperatures in an electric arc furnace. The quality of the raw materials directly impacts the properties of the final product.
Production Techniques
Two primary techniques dominate the scene: Physical Vapor Transport (PVT) and High-Temperature Chemical Vapor Deposition (HTCVD). These methods enable the production of high-quality silicon carbide wafers, which are essential for various applications. The commercially available fibers of beta silicon carbide are produced using a pre-ceramic polymer conversion route enabling extrusion of continuous fibers.
Quality Control Measures
Quality control is crucial in the manufacturing process of silicon carbide. Each step, from wafer slicing to surface preparation, requires meticulous attention to detail to avoid introducing defects. Growth conditions such as temperature gradients, gas flow rates, and impurity levels are precisely monitored and optimized. By mastering these techniques and overcoming the challenges of defect control, manufacturers pave the way for the creation of high-performance SiC wafers.
Advantages of Using Silicon Carbide
Cost-Effectiveness
Silicon carbide (SiC) offers significant cost advantages over traditional materials. Its high thermal conductivity and low electrical resistance reduce the need for additional cooling systems, thereby lowering overall costs. Additionally, the durability and longevity of SiC components mean fewer replacements and maintenance, further driving down expenses.
Performance Efficiency
SiC’s unique properties, such as a wide bandgap and high breakdown electric field, enable devices to operate at higher voltages, temperatures, and frequencies. This results in increased efficiency and performance, particularly in power electronics. By investing in building the advantages of SiC technology, industries can achieve higher power density and throughput.
Environmental Benefits
The use of SiC contributes to environmental sustainability. Its high efficiency reduces energy consumption, leading to lower greenhouse gas emissions. Moreover, the long lifespan of SiC components means less waste and fewer resources spent on replacements, making it an eco-friendly choice.
Future Trends in Silicon Carbide Technology
The compelling attributes of Silicon Carbide resonate with the evolving needs of the semiconductor industry, making SiC fabrication an exciting frontier for stakeholders. As we transition into a more electrified and connected world, SiC’s role becomes increasingly crucial, setting the stage for a new era of semiconductor technology. The ongoing investments and research in SiC technology signify a bright future, full of possibilities for enhanced electronic performance and sustainable energy solutions.
In the burgeoning landscape of the semiconductor industry, Silicon Carbide (SiC) emerges as a promising material, unveiling opportunities for superior electronic performance at a competitive cost. The industry’s relentless pursuit for enhanced efficiency, higher operating temperatures, and reduced system costs has brought SiC into the spotlight, making it a frontrunner in the compound semiconductor sector.
The future development and adoption of SiC wafer technology are expected to accelerate, driven by ongoing research in crystal growth techniques, epitaxial growth methods, and packaging solutions, as well as the increasing demand for energy-efficient and high-power applications.
Challenges in Silicon Carbide Manufacturing
Supply Chain Issues
The silicon carbide crystal growing industry tests for minute imperfections, making it crucial to have a reliable supply chain. If the final product cannot be inspected, it becomes challenging to identify potential imperfections in the SiC crystals and pinpoint the stage of the process where they occur. This necessitates a robust and transparent supply chain to ensure the availability of high-quality raw materials.
Technical Difficulties
Industrial production of SiC faces numerous technical challenges. Defects like micropipes, dislocations, stacking faults, and impurities can act as gremlins, sabotaging device performance and reliability. These defects create unwanted pathways for electricity to flow, leading to inefficiencies. Manufacturers must employ advanced techniques to control these defects and improve yield.
Market Competition
The compelling attributes of Silicon Carbide resonate with the evolving needs of the semiconductor industry, making SiC fabrication an exciting frontier for stakeholders. However, the market is highly competitive, with numerous players striving to innovate and capture market share. This competition drives continuous improvement but also poses challenges for new entrants trying to establish themselves.
Conclusion
Silicon carbide (SiC) stands as a transformative material in the realm of modern manufacturing and semiconductor technology. Its exceptional properties, such as high thermal conductivity, superior strength, and resistance to high temperatures and chemicals, make it an invaluable asset across various industries. From power electronics to renewable energy solutions, SiC is paving the way for enhanced efficiency and performance. As the demand for high-quality wafers and advanced power electronics continues to grow, the role of SiC becomes increasingly crucial. The ongoing research and investments in SiC technology signify a promising future, marked by innovative advancements and sustainable solutions. This comprehensive guide has aimed to shed light on the multifaceted applications and benefits of silicon carbide, underscoring its pivotal role in shaping the future of semiconductor technology.
Frequently Asked Questions
What is Silicon Carbide (SiC)?
Silicon Carbide (SiC) is a compound semiconductor made from silicon and carbon. It is known for its exceptional properties such as high thermal conductivity, high-temperature resistance, and superior strength compared to traditional materials.
What are the key properties of Silicon Carbide?
The key properties of Silicon Carbide include high thermal conductivity and resistance, excellent mechanical strength and durability, and unique electrical properties that make it suitable for high-power and high-frequency applications.
What are the major applications of Silicon Carbide?
Silicon Carbide is widely used in power electronics, aerospace and defense, and the automotive industry due to its ability to operate at high temperatures and its superior performance efficiency.
Who are the leading manufacturers of Silicon Carbide?
The leading manufacturers of Silicon Carbide include major global companies, innovative startups, and regional market leaders who specialize in producing high-quality SiC materials for various industrial applications.
What are the advantages of using Silicon Carbide?
Using Silicon Carbide offers several advantages, including cost-effectiveness, improved performance efficiency, and environmental benefits due to its durability and ability to enhance energy efficiency.
What are the future trends in Silicon Carbide technology?
Future trends in Silicon Carbide technology include advancements in semiconductor applications, emerging industrial uses, and a strong focus on research and development to further enhance the material’s capabilities.