Mastering Quality Control: Inside the Testing Factory
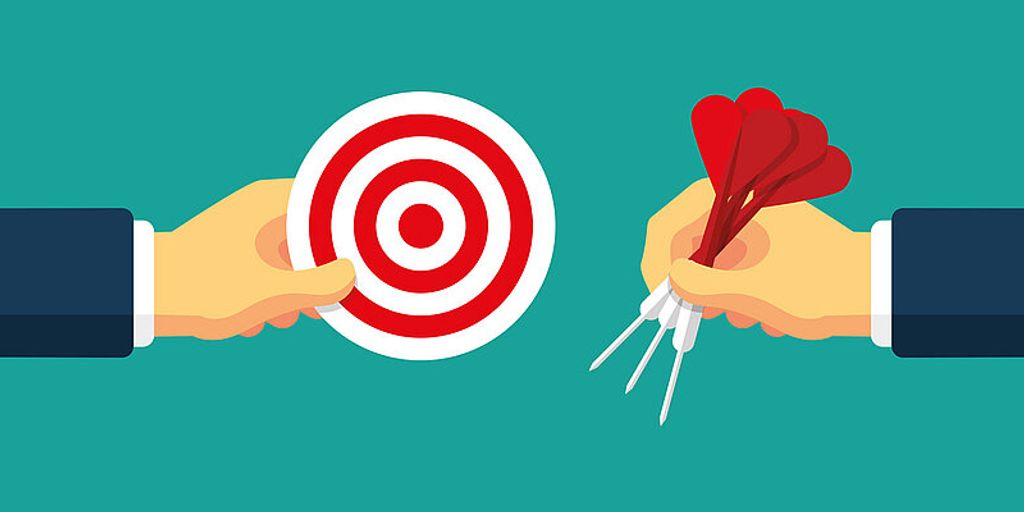
From setting standards to embracing advanced methods, let’s take a stroll through the world of quality control, where precision meets passion, and quality isn’t just a checkbox – it’s a promise to make things awesome. Ready for the journey? Let’s dive in!
Key Takeaways
- Testing factories play a crucial role in ensuring products are reliable and meet regulatory standards.
- Advanced quality control techniques like Statistical Process Control and Non-Destructive Testing are essential in modern manufacturing.
- Building quality from the ground up involves strategies like Design for Quality and Supplier Quality Management.
- Training and expertise are vital, emphasizing skill development programs and continuous improvement cultures.
- Technology and innovation, including automation and data analytics, are transforming quality control in testing factories.
The Role of a Testing Factory in Modern Manufacturing
In today’s competitive manufacturing world, delivering consistent quality is not just a luxury; it’s a must. Consumers expect products that work perfectly and meet their expectations every time. To achieve this, manufacturers depend on a strong set of quality control techniques. These methods find and fix problems during production, ensuring a steady flow of high-quality products.
Advanced Quality Control Techniques in Testing Factories
Statistical Process Control (SPC)
Statistical Process Control (SPC) is a method used to monitor and control a process to ensure that it operates at its full potential. By using statistical methods, manufacturers can identify and correct issues before they result in defective products. SPC helps in maintaining consistent quality and reducing waste, making it a cornerstone of modern manufacturing.
Non-Destructive Testing (NDT)
Non-Destructive Testing (NDT) involves evaluating the properties of a material, component, or system without causing damage. This technique is crucial for ensuring product reliability and safety. Common NDT methods include ultrasonic testing, radiographic testing, and magnetic particle testing. These methods help in detecting flaws that could lead to failures, ensuring that products meet the highest standards.
Six Sigma Implementation
Six Sigma is a set of techniques and tools for process improvement. It aims to improve the quality of the output by identifying and removing the causes of defects and minimizing variability in manufacturing processes. Six Sigma uses a data-driven approach and statistical analysis to achieve its goals. Implementing Six Sigma can lead to significant improvements in product quality and customer satisfaction.
Building Quality from the Ground Up: Prevention Strategies
In today’s competitive manufacturing world, delivering consistent quality is a must. Prevention is key to building quality into products from the start. This proactive approach helps minimize waste, reduce production costs, and boost customer satisfaction. Here are some essential strategies:
Design for Quality
Designing for quality means thinking about potential issues before they happen. By planning and testing designs early, companies can avoid costly mistakes later. This step is like a shield against problems that could arise during production.
Supplier Quality Management
Managing supplier quality is crucial. Companies need to ensure that their suppliers provide materials that meet high standards. This can be done through regular audits and feedback loops. By keeping a close eye on suppliers, businesses can prevent defects from entering the production line.
In-Process Quality Control
In-process quality control involves checking products at different stages of production. This helps catch any issues early, so they can be fixed before the product is finished. Regular inspections and tests are key parts of this strategy.
The Human Element: Training and Expertise in Testing Factories
In testing factories, the human element is crucial for maintaining high standards of quality. Training personnel is essential to ensure that everyone understands their roles and the importance of quality control. Here are some key strategies:
- Regular Training: Conduct thorough training sessions for all employees. This helps them grasp the procedures and their specific responsibilities.
- Inspection Points: Set up checkpoints in the manufacturing process. These are critical areas where inspections can occur, such as checking raw materials and various production stages.
- Randomized Testing: Implement unscheduled tests to keep employees on their toes. This encourages them to consistently follow safety and quality standards.
Additionally, experienced personnel play a significant role in producing high-quality products. By focusing on skill development programs, factories can ensure that their workforce is well-prepared to meet challenges.
Training Strategy | Description |
---|---|
Regular Training | Ongoing sessions to reinforce knowledge and skills. |
Inspection Points | Key areas for quality checks during production. |
Randomized Testing | Unscheduled tests to ensure compliance with standards. |
By fostering a culture of continuous improvement and feedback, testing factories can enhance their quality control processes and ensure that their teams are always ready to meet the demands of modern manufacturing.
Technology and Innovation in Testing Factories
Automation in Quality Control
Automation is transforming quality control in testing factories. Automated systems can perform repetitive tasks with high precision, reducing human error. This not only speeds up the process but also ensures consistent quality. For example, machine vision systems can inspect products at a much faster rate than human inspectors, identifying defects that might be missed by the human eye.
Data Analytics for Quality Assurance
Data analytics plays a crucial role in modern quality assurance. By analyzing large sets of data, manufacturers can identify patterns and trends that indicate potential quality issues. This allows for proactive measures to be taken before defects occur. Real-time insights into the entire production ecosystem empower manufacturers to make informed decisions, ensuring every product meets the highest standards.
Emerging Technologies in QC
Emerging technologies are continuously enhancing quality control processes. Technologies like digital twins, AI, and automated systems are transforming materials testing in heavy industries. Predictive quality control uses AI and machine learning to predict defects and failures, allowing manufacturers to take preemptive action. Additionally, remote inspection tools and augmented reality (AR) are becoming more common, enabling real-time production tracking and quality assessment.
Case Studies: Success Stories from Leading Testing Factories
Automotive Industry
In the automotive sector, a leading manufacturer significantly improved their quality control by implementing randomized testing. This approach provided an inside look at employee compliance with safety and quality standards. As a result, the company saw a notable reduction in defects and an increase in overall product reliability.
Electronics Manufacturing
An electronics company partnered with a quality control expert to reduce changeover time and Mean Time Between Failures (MTBF) by over 60%. This collaboration not only boosted productivity but also enhanced the confidence of the frontline workforce. The success was attributed to data-driven decisions and continuous improvement practices.
Pharmaceuticals
A pharmaceutical firm faced challenges in maintaining consistent quality across its product lines. By investing in standardized protocols and ensuring access to necessary personnel and automation tools, the company managed to overcome these hurdles. This strategic approach led to better compliance with regulatory standards and improved product quality.
Challenges and Solutions in Quality Control
Common Quality Control Issues
Quality control (QC) is a process used to ensure that products and services meet certain standards. However, manufacturers often face several obstacles in maintaining product quality. These challenges include:
- Inconsistent Standards: Different departments may follow varied protocols, leading to uneven quality.
- Resource Limitations: Lack of personnel or automation tools can hinder proper testing.
- Cost Management: Balancing the cost of quality control with budget constraints can be difficult.
Effective Problem-Solving Techniques
To overcome these challenges, businesses need to invest more resources into their quality control processes. Here are some effective techniques:
- Standardized Protocols: Implementing uniform procedures across all departments ensures consistent quality.
- Adequate Resources: Ensuring access to enough personnel and automation tools is crucial for proper testing.
- Clear Guidelines: Providing clear instructions on who is responsible for various aspects of QC helps in managing operations efficiently.
Future Trends in Quality Control
The future of quality control is evolving with advancements in technology. Emerging trends include:
- Automation: Increasing use of automated systems for more efficient and accurate testing.
- Data Analytics: Leveraging data analytics to predict and prevent defects before they occur.
- Innovative Technologies: Adoption of new technologies like AI and IoT to enhance QC processes.
By addressing these challenges and adopting effective solutions, businesses can ensure better quality products and services at lower costs.
Conclusion
In the world of manufacturing, quality control is more than just a step in the process—it’s a commitment to excellence. From setting high standards to using advanced techniques, quality control ensures that every product meets the expectations of customers. It’s about making sure that what comes off the production line is not only functional but also reliable and safe. By focusing on quality control, companies can reduce costs, improve processes, and stay competitive in the market. So, as we wrap up our journey through the testing factory, remember that quality control is the key to delivering products that people can trust and rely on every day.
Frequently Asked Questions
What is quality control in manufacturing?
Quality control in manufacturing is a process where products are checked to make sure they meet certain standards. This helps ensure that the products are reliable and safe for customers.
Why is quality control important?
Quality control is important because it helps keep customers happy, meets regulatory requirements, reduces costs, improves processes, and keeps companies competitive in the market.
What are some common quality control techniques?
Some common quality control techniques include Statistical Process Control (SPC), Non-Destructive Testing (NDT), Six Sigma, sampling, inspection, and visual checks.
How does quality control improve customer satisfaction?
Quality control improves customer satisfaction by ensuring that products are reliable and meet customer expectations. Happy customers are more likely to return and recommend the products to others.
What is Six Sigma?
Six Sigma is a method used in quality control to improve processes by identifying and removing the causes of defects. It aims to make processes more efficient and reliable.
How does technology help in quality control?
Technology helps in quality control by automating inspections, using data analytics to find issues, and applying new tools and methods to improve the quality of products.