Maximizing Efficiency with Advanced Wafer Testing Machines
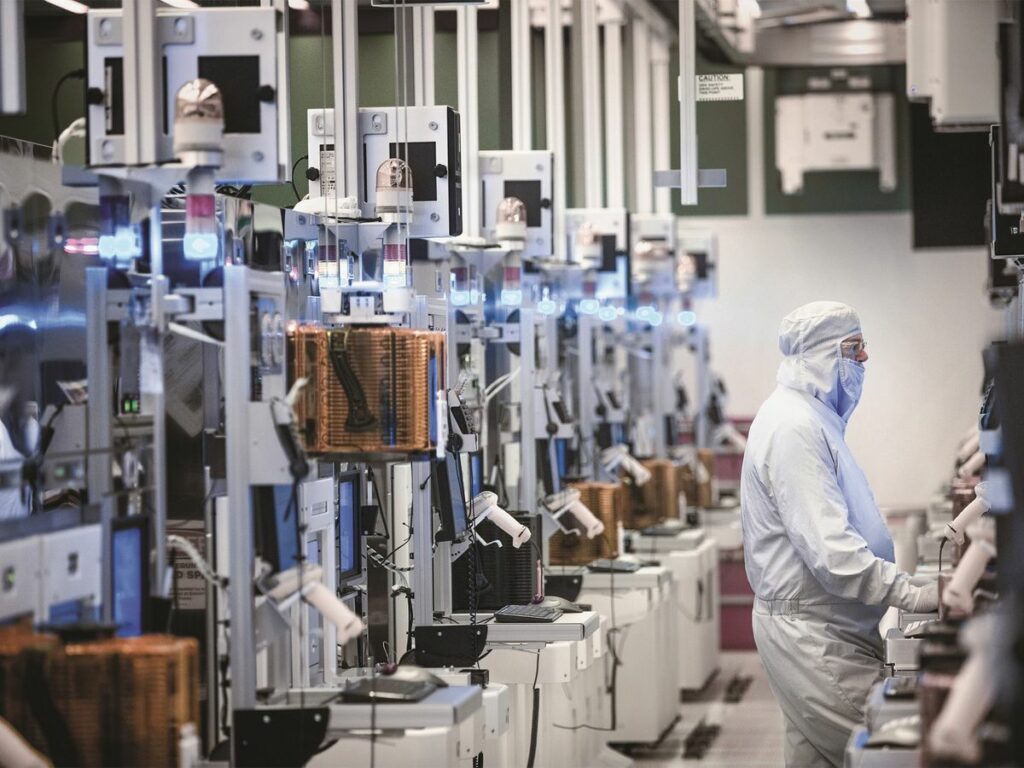
As the semiconductor industry evolves, the need for advanced wafer testing machines has become critical to ensure the quality and efficiency of integrated circuits (ICs). With the shift towards 300 mm wafers and the complexity of quantum chips, the demand for precision and scalability in testing equipment is higher than ever. This article delves into the technologies and techniques that are shaping the future of wafer testing, exploring the evolution of testing methods, surface finishing techniques, automated systems, and the challenges faced in advanced node timing signoff.
Key Takeaways
- The transition to 300 mm wafers is a response to the increasing complexity of ICs and the need for high-volume manufacturing efficiency.
- Scalable automated test equipment is becoming indispensable for ensuring chip quality in the quantum industry and beyond.
- Advanced surface finishing techniques, such as lapping, polishing, and grinding, are crucial for achieving the smoothness required for efficient wafer testing.
- International collaboration and ultraclean factories play a pivotal role in the development and operation of automated wafer processing systems.
- The challenge of balancing performance with precision in advanced node timing signoff is met with innovative solutions to manage model variation and complexity.
The Evolution of Wafer Testing: Meeting the Demands of Advanced ICs
The Shift to 300 mm Wafers in High-Volume Manufacturing
The semiconductor industry’s pivot to 300 mm wafers marks a significant evolution in high-volume manufacturing, driven by the need to accommodate more complex and advanced integrated circuits (ICs). The larger surface area of 300 mm wafers enables the production of more chips per wafer, enhancing the overall efficiency and cost-effectiveness of semiconductor fabrication.
The benefits of this transition are not just limited to increased chip yield. The 300 mm wafer format also aligns with the industry’s progression towards more sophisticated technology nodes, where precision and scale are paramount. As a result, the market has seen a dominant shift towards the 300 mm segment, particularly in Silicon On Insulator (SOI) applications.
To illustrate the advantages of 300 mm wafers over their 200 mm counterparts, consider the following table:
Wafer Size | Surface Area | Chip Yield Increase |
---|---|---|
200 mm | 314 cm^2 | – |
300 mm | 706 cm^2 | Significant |
This shift is not without its challenges, such as higher manufacturing costs and limited material availability. However, the industry continues to innovate, overcoming these hurdles to meet the demands of advanced ICs.
Scalable Automated Test Equipment for Enhanced Chip Quality
The relentless pursuit of enhanced chip quality has led to the development of scalable automated test equipment, a cornerstone in the semiconductor industry’s future. The integration of control electronics with qubit diagnostics software marks a significant leap forward, enabling automated qubit testing in R&D labs and facilitating the transition to more sophisticated quantum chip analysis.
The synergy between different testing approaches, such as the Orange QS and QuantaMap, illustrates the industry’s commitment to comprehensive quality assurance. Orange QS systems excel in end-of-line testing, while QuantaMap’s tools are adept at in-line testing during the chip’s development and fabrication stages. This complementary relationship is crucial for chipmakers aiming to expedite analysis without compromising on quality.
Testing Approach | Stage | Focus |
---|---|---|
Orange QS | End-of-Line | Final Quality Assurance |
QuantaMap | In-Line | Development & Fabrication Analysis |
As the quantum industry evolves, the collaboration between companies like Jobst and Last is setting the stage for a unified inspection and test pipeline. This partnership is not only timely but also indicative of the sector’s readiness to embrace advanced testing technologies for quantum chips, ensuring that the high standards of chip quality are met consistently.
Integrating SQUID-on-Tip Technology for Quantum Chip Analysis
The integration of SQUID-on-tip technology is revolutionizing the way quantum chips are analyzed during development and manufacturing. This innovative approach employs a superconducting quantum interference device (SQUID) at the tip of an atomic force microscope, enabling the detection of weak magnetic fields and temperature gradients with unprecedented precision. The sensitivity of SQUID-on-tip allows for the identification of various parameters that are critical to the performance of quantum chips, such as local temperature changes, leakage currents, and magnetic moments.
Quantum chips are highly susceptible to errors caused by thermal noise, electromagnetic interference, or fabrication defects. Traditional lab-based testing methods are not only time-consuming but also inadequate for the intricate nature of quantum calculations. The SQUID-on-tip technology addresses these challenges by providing a more efficient and automated testing process. By correlating multiple data points, it offers a comprehensive view of the chip’s quality, paving the way for more reliable quantum computing.
The table below summarizes the key parameters detected by the SQUID-on-tip system and their impact on chip quality:
Parameter Detected | Impact on Chip Quality |
---|---|
Local Temperatures | Identifies thermal inconsistencies |
Leakage Currents | Pinpoints electrical faults |
Stray RF Fields | Detects electromagnetic interference |
Magnetic Moments | Reveals structural defects |
As the quantum computing industry progresses, the need for advanced testing methods like SQUID-on-tip becomes increasingly vital. It not only enhances the efficiency of the testing process but also contributes to the overall advancement of quantum technology.
Surface Finishing Techniques for Silicon Carbide Wafer Efficiency
Lapping, Polishing, and Grinding: The Path to Smooth Surfaces
The pursuit of efficiency in silicon carbide (SiC) wafer production has led to the refinement of surface-finishing techniques. Lapping is a mechanical technique that removes excess silicon from a wafer substrate using a pad and polishing liquid, resulting in a semi-reflective finish. This process is essential for eliminating defects and reducing stress from the ingot-slicing phase. Following lapping, polishing employs a thermal-chemical-mechanical approach to achieve a mirror-like finish, significantly reducing surface roughness and achieving industry-leading Total Thickness Variation (TTV) values.
Surface finishing’s importance cannot be overstated, as the choice of abrasive is limited due to the hardness of silicon carbide. Diamond suspensions are the go-to solution, as they are one of the few materials harder than SiC. The combination of the pad and diamond suspension is a closely guarded secret, yielding a surface roughness of less than five nanometers. This meticulous process ensures that the wafers are prepared to meet the stringent demands of advanced wafer testing machines.
Technique | Purpose | Outcome |
---|---|---|
Lapping | Remove excess silicon and defects | Semi-reflective, stress-reduced surface |
Polishing | Reduce surface roughness | Mirror-like finish with minimal TTV |
By integrating these methods, manufacturers can produce wafers with exceptionally smooth and even surfaces, which is a prerequisite for the high precision required in advanced integrated circuits.
Innovations in Wafer-Finishing Solutions
The relentless pursuit of efficiency in wafer production has led to significant innovations in wafer-finishing solutions. One such breakthrough is the achievement of an excellent surface finish, with a surface roughness of less than five nanometers. This level of precision ensures a total thickness variation (TTV) of the wafer of less than 0.001 micron, which is critical for the performance of advanced integrated circuits.
The introduction of new materials, such as diamond suspensions, has revolutionized the polishing process, offering an economical and adaptable solution to meet customer specifications. These advancements not only enhance the quality of the silicon carbide wafers but also contribute to a reduction in the cost of ownership, a factor that is as important to manufacturers as it is to their customers.
In the context of silicon carbide wafer production, the final Chemical Mechanical Planarization (CMP) stage has traditionally been a bottleneck. However, innovative solutions like Hyperion’s have emerged to address this challenge, boosting SiC production by reducing CMP polishing time and costs. This is a pivotal development for the industry as it moves towards the next generation of 200 mm silicon carbide wafers.
Impact of Surface Finishing on Wafer Testing Accuracy
The quest for perfection in wafer production is a meticulous journey where surface finishing plays a pivotal role. The integrity of wafer testing is significantly influenced by the surface quality, which is achieved through precise lapping, polishing, and grinding. These processes aim to produce a surface with minimal roughness, ensuring that the wafers meet the stringent requirements for direct wafer bonding and other critical applications.
Surface finishing not only affects the bondability but also the overall efficiency of the wafers. A consistent and defect-free surface is crucial for the accuracy of wafer testing, as it directly impacts the reliability of the semiconductor devices produced. The table below summarizes the relationship between surface finishing techniques and their impact on wafer testing accuracy:
Technique | Surface Roughness (nm) | Total Thickness Variation (TTV) (micron) | Impact on Testing Accuracy |
---|---|---|---|
Lapping | < 5 | < 0.001 | High |
Polishing | < 5 | < 0.001 | High |
Grinding | < 5 | < 0.001 | High |
Achieving an excellent surface finish with a roughness of less than five nanometers and a TTV of less than 0.001 micron is not only a testament to the technological advancements in wafer-finishing solutions but also a necessity for maintaining high testing accuracy. This uniformity is essential for ensuring that each wafer produced can reliably host the intricate networks of semiconductor devices.
Automated Wafer Processing Systems: A Global Perspective
International Collaboration in Wafer Processing Equipment
The semiconductor industry has seen a significant shift towards international collaboration in wafer processing equipment. This trend is driven by the need to integrate diverse technological advancements and to cater to the global demand for more sophisticated integrated circuits (ICs). Collaboration among industry leaders has proven essential in sharing best practices, reducing costs, and accelerating innovation.
One such example of industry collaboration is SEMI, the global industry association representing the electronics manufacturing and design supply chain. SEMI provides a platform for members to collaborate and drive collective industry growth. The association’s efforts in setting global standards and providing market insights are crucial for the advancement of wafer processing technologies.
The table below outlines the various types of equipment used in both front-end and back-end wafer processing, highlighting the complexity and range of technologies involved in the production of semiconductor devices:
Front-End Equipment | Back-End Equipment |
---|---|
DUV Lithography | Assembly and Packaging |
EUV Lithography | Dicing |
Etching | Metrology |
Chemical Mechanical Planarization | Bonding |
Wafer Cleaning Equipment | Wafer Testing |
As the industry continues to evolve, the role of international collaboration will only become more significant, ensuring that the latest technologies are accessible across different regions and contributing to the overall efficiency of the semiconductor manufacturing process.
The Role of Ultraclean Factories in Wafer Testing
Ultraclean factories play a pivotal role in the wafer testing process, ensuring that the stringent cleanliness standards required for advanced semiconductor manufacturing are met. The purity of the crystal and the defect-free nature of the lattice structure are critical to wafer quality, and these attributes are largely influenced by the environment in which wafers are processed.
In these specialized facilities, wafers undergo a series of meticulous steps to achieve the necessary surface perfection. Surface imperfections are meticulously removed through lapping, which is essential for maintaining uniform thickness and quality across the wafer’s surface. The consistency of this process is paramount; each wafer must exhibit the same surface finish and material removal rate to ensure reliability in the final product.
The collaboration of international equipment from the Netherlands, the United States, and Japan within South Korean ultraclean factories exemplifies the global effort to maintain high standards in wafer testing. These factories utilize advanced machinery and techniques to create the precise channels needed for electron movement in semiconductor devices. The table below summarizes the key aspects of ultraclean factories in wafer testing:
Aspect | Importance in Wafer Testing |
---|---|
Purity of Crystal | Determines wafer quality and defect-free structure |
Surface Perfection | Essential for uniform thickness and quality |
Consistency of Processing | Ensures reliability and performance of semiconductor |
International Collaboration | Combines global expertise for advanced manufacturing |
The relentless pursuit of perfection in these ultraclean environments is what allows for the advancement of semiconductor technology, pushing the boundaries of what is possible in electronic devices.
Advancements in Front-End and Back-End Wafer Equipment
The relentless pursuit of miniaturization and performance in the semiconductor industry has led to significant advancements in both front-end and back-end wafer equipment. Front-end processes, which include the intricate steps of lithography, etching, and deposition, have seen remarkable innovations. These processes are critical for defining the microstructures that form the integrated circuits on the wafer. The back-end, which involves assembly, packaging, and testing, has also evolved to keep pace with the front-end’s complexity.
In the context of back-end processes, recent developments have focused on enhancing the precision and efficiency of wafer cutting and metrology. This is crucial for ensuring that the final product meets the stringent quality standards required for advanced applications. The table below provides an overview of the key equipment used in both front-end and back-end processes:
Front-End Equipment | Back-End Equipment |
---|---|
DUV Lithography | Assembly and Packaging |
EUV Lithography | Dicing |
Etching | Metrology |
Chemical Mechanical Planarization | Bonding |
Wafer Cleaning Equipment | Wafer Testing |
The integration of these advanced systems has been instrumental in improving reliability and productivity. As the industry transitions to larger wafer sizes and more complex integrated circuits, the role of sophisticated wafer equipment becomes ever more critical. It’s not just about making productivity improvements; it’s about ensuring that every step of the manufacturing process contributes to the overall excellence of the semiconductor products.
Challenges and Solutions in Advanced Node Timing Signoff
Balancing Performance with Precision in Timing Analysis
In the realm of advanced node timing signoff, engineers face the critical task of balancing the high performance of integrated circuits with the precision required in timing analysis. This balance is pivotal for ensuring that chips meet the stringent speed and reliability standards demanded by modern applications.
To achieve this, a series of design techniques and analysis tools are employed:
- Minimization of variability that could lead to failure
- Optimization of design margins to enhance yield
- Implementation of in-circuit monitors for real-time performance tracking
These strategies are increasingly important as manufacturing nodes shrink, where even atomic-level variations can have a pronounced impact on chip behavior. The table below illustrates the relationship between node size and variability impact:
Node Size (nm) | Variability Impact |
---|---|
45 | Low |
32 | Moderate |
22 | High |
14 | Very High |
10 | Extreme |
As dimensions decrease, a constant variability translates to a greater percentage change, underscoring the need for precision in timing signoff processes. The challenge is to maintain performance without compromising on the accuracy of timing analysis, which is essential for the functionality and longevity of the chip.
Model Variation and Its Impact on Cell Characterization
As semiconductor manufacturing progresses to advanced nodes, the impact of model variation on cell characterization becomes increasingly significant. Model variation represents the discrepancies between intended and actual device performance, often due to the inherent variability in manufacturing processes. This variability can lead to a range of issues, from minor performance degradation to complete device failure.
When considering the effects of model variation, it’s crucial to understand the concept of ‘process corners’. These corners represent the extremes of process variability and are used to define the bounds within which devices are expected to operate reliably. However, as the number of variables increases, so does the number of process corners, often growing exponentially. This complexity can limit the feasibility of comprehensive analysis.
Here is a summary of recent publications highlighting the significance of model variation:
- PROCESS MODEL CALIBRATION: BUILDING PREDICTIVE AND ACCURATE 3D PROCESS MODELS (Published on August 20, 2020)
- EFFECTS OF A RANDOM PROCESS VARIATION ON THE TRANSFER CHARACTERISTICS OF A FUNDAMENTAL PHOTONIC INTEGRATED CIRCUIT COMPONENT (Published on January 24, 2019)
- MODELING SEMICONDUCTOR PROCESS VARIATION (Published on April 19, 2018)
These publications underscore the importance of accurate modeling and the need for robust design techniques to mitigate the risks associated with process variation.
Ensuring Accuracy in the Face of Increasing Complexity
As semiconductor devices continue to shrink in size and increase in complexity, ensuring accuracy in wafer testing and analysis becomes a formidable challenge. The process checks the quality and performance of wafers, which are essential for the reliable functioning of electronic circuits. With the advent of advanced nodes, the margin for error narrows significantly, making precision in timing signoff a critical factor for success.
To address the variability that can lead to failures, design techniques and analysis tools are employed. These aim to minimize the impact of variability on yield. For instance, at each manufacturing node, as dimensions decrease, a constant variability translates to a greater percentage change. This is particularly significant when dimensions are measured in atomic scales, where a single atom’s difference can have substantial consequences.
Process Corner | Description |
---|---|
Fast/Fast (FF) | Represents the scenario where both NMOS and PMOS transistors are fast. |
Slow/Slow (SS) | Indicates both NMOS and PMOS transistors are slow. |
Typical/Typical (TT) | The nominal case where transistors perform as expected. |
Fast/Slow (FS) | A case where NMOS is fast and PMOS is slow. |
Slow/Fast (SF) | A case where NMOS is slow and PMOS is fast. |
The table above illustrates a simplified view of process corners, which are models that define the extremes of the manufacturing process. As the number of process variabilities increases, so does the number of corners, often exponentially. This exponential increase imposes practical limits on the number of corners that can be analyzed, thus challenging the precision of timing signoff.
Conclusion
In conclusion, the semiconductor industry’s relentless pursuit of efficiency and precision has led to the development of advanced wafer testing machines that are critical for the production of high-quality integrated circuits. The transition to 300 mm wafers and the need for high-volume manufacturing processes demand scalable automated test equipment capable of providing detailed insights into chip quality. Innovations like the ‘SQUID-on-tip’ technology and surface-finishing solutions are at the forefront of this evolution, ensuring that the wafers meet the stringent requirements of modern electronics. As the industry continues to push the boundaries of technology nodes, the collaboration between companies like Jobst and Last and the integration of their systems into industrial-scale facilities will be pivotal. The future of semiconductor manufacturing hinges on the ability to balance performance with accuracy, and the advanced wafer testing machines are the linchpins in this complex and intricate process.
Frequently Asked Questions
Why is the industry transitioning to 300 mm wafers for advanced ICs?
The industry’s transition to 300 mm wafers is driven by the need to meet the demands of high-volume manufacturing processes and advanced technology nodes, as these larger wafers are better suited for producing more complex integrated circuits efficiently.
What role does scalable automated test equipment play in chip quality?
Scalable automated test equipment is crucial for providing detailed information on chip quality, which is essential for manufacturers, especially in the quantum industry, to ensure the reliability and performance of their products.
How do surface-finishing techniques like lapping, polishing, and grinding affect wafer efficiency?
Lapping, polishing, and grinding are mechanical techniques that create a smooth and even surface on the wafer, which is critical for the efficiency and cost-effectiveness of silicon carbide wafers in the manufacturing process.
What is the significance of ultraclean factories in wafer testing?
Ultraclean factories play a vital role in wafer testing as they provide a controlled environment free from contaminants, which is necessary for the accurate and precise processing of wafers using advanced equipment from various countries.
How does model variation impact cell characterization in advanced node timing signoff?
Model variation can significantly affect cell characterization by introducing uncertainties in the performance predictions of integrated circuits, which makes it challenging to balance performance with precision during advanced node timing signoff.
What is ‘SQUID-on-tip’ technology, and how does it contribute to quantum chip analysis?
SQUID-on-tip technology involves mounting a superconducting quantum interference device on the tip of an atomic force microscope to detect weak magnetic fields and temperature gradients. It is used to scan quantum chips during development and manufacturing, providing detailed information on various parameters, including local temperature changes.