Maximizing Efficiency with Professional Wafer Services
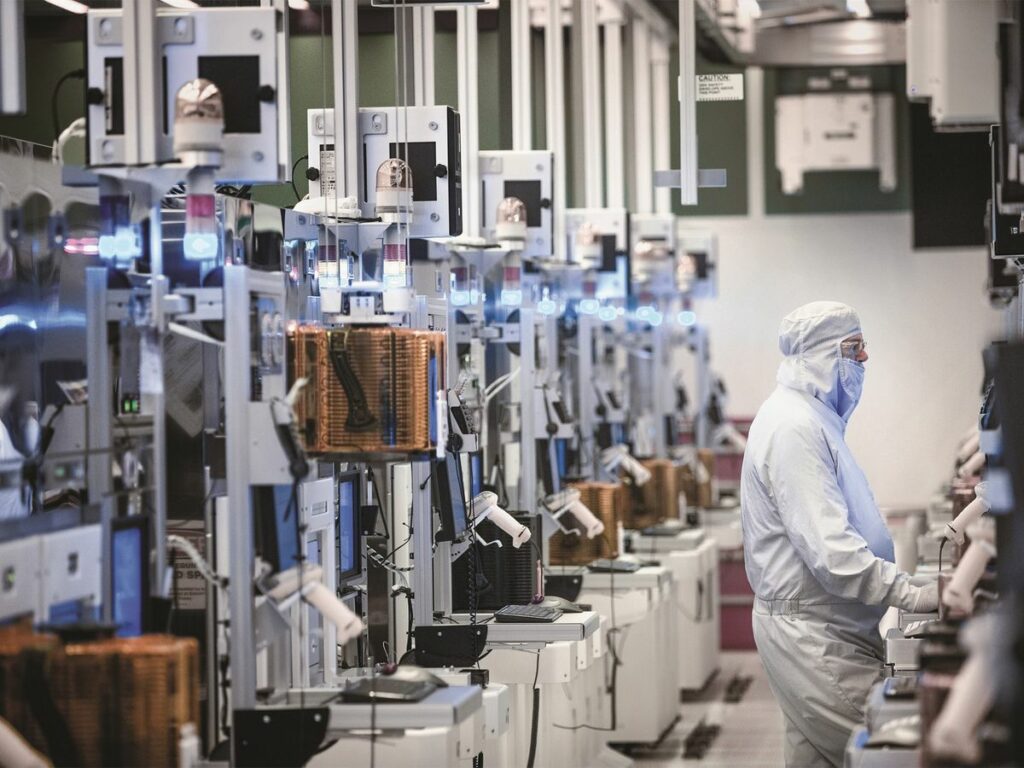
The semiconductor industry is rapidly evolving, and with it, the demand for efficient and sustainable wafer services is growing. Professional wafer services play a crucial role in maximizing efficiency across various stages of semiconductor manufacturing. From advancing sustainability in wafer processing to enhancing performance with high-precision services, streamlining quality management, boosting productivity with innovative technologies, and achieving cost efficiency, these services are pivotal in shaping the future of semiconductor production. In this article, we delve into how professional wafer services can optimize each aspect of the production process to meet the increasing demands of the industry.
Key Takeaways
- Professional wafer services significantly reduce tape waste and enable sustainable operations by eliminating the die-taping process, saving up to 800 km of tape annually in 24/7-SiP production.
- High-precision wafer services, such as the SIPLACE CA2, can achieve component placement rates of up to 50,000 per hour with an accuracy of up to 10 μm, enhancing performance and throughput.
- Streamlined quality management is achieved through comprehensive control measures, full single-die-level traceability, and expert systems, ensuring high-quality outputs in wafer services.
- Innovative wafer technologies that combine die-attach and flip-chip processes in one machine lead to maximum productivity and offer unique flexibility for different wafer types.
- Advanced wafer services drive cost efficiency by eliminating taping costs, reducing material feeding and splicing tasks, and integrating automation with smart factory concepts.
Advancing Sustainability in Wafer Processing
Die Processing and Tape Waste Reduction
In the realm of semiconductor manufacturing, die singulation is a critical step where individual dies are separated from the finished wafer. This process traditionally involves die-taping, which can generate significant waste. However, advancements in wafer services now allow for die processing directly from the diced wafer, bypassing the need for taping and consequently reducing tape waste. For instance, in a 24/7-SiP production environment, this approach can lead to substantial savings, both economically and environmentally.
By eliminating the die-taping process, not only are material costs saved, but also the labor-intensive tasks associated with tape replenishment and disposal are reduced. The table below illustrates the potential savings over a one-year period in a high-volume production setting:
Production Aspect | Without Tape | With Tape |
---|---|---|
Tape Usage (km) | 0 | 800 |
Cost Savings | High | None |
Labor Efficiency | Improved | Standard |
These improvements in efficiency and sustainability are a testament to the evolving landscape of wafer services, where the goal is to minimize waste while maximizing productivity and quality.
Environmental Impact of 24/7-SiP Production
The semiconductor industry is facing a critical challenge in balancing high-volume production with environmental sustainability. The global impact of semiconductor chip manufacturing is significant, and the shift towards 24/7 System in Package (SiP) production has brought this issue to the forefront. By eliminating the die-taping process, facilities can reduce their carbon footprint, as this not only decreases the amount of waste generated but also lowers the energy consumption associated with additional processing steps.
In the context of 24/7-SiP production, the SIPLACE CA2 machine exemplifies how sustainability and efficiency can coexist. The machine’s ability to place up to 50,000 components per hour directly from the wafer, with an accuracy of up to 10
can save an estimated 800 kilometers of tape annually. This is not just a cost-saving measure but a substantial environmental benefit. The table below summarizes the environmental savings achieved through this approach:
Metric | Savings Achieved |
---|---|
Tape Waste Reduction | 800 km/year |
Energy Consumption Savings | Significant (Quantified) |
Carbon Footprint Reduction | Notable (Quantified) |
As the industry progresses, it is essential to continue exploring and implementing such innovations that contribute to a more sustainable production model. The journey towards a greener semiconductor industry is complex, but with concerted efforts and technological advancements, a balance between high productivity and environmental responsibility is attainable.
Volume Manufacturing Tools for Sustainable Operations
In the realm of volume manufacturing, efficiency and precision are paramount, especially for high-density applications and System-in-Package (SiP) technologies. The integration of Surface Mount Technology (SMT) expertise with Overall Component Placement (OSC) strategies has led to significant advancements in process integration.
The implementation of software solutions for asset and maintenance management across the factory floor is revolutionizing the way we approach volume manufacturing. These tools not only streamline operations but also support the deployment of the industry’s first ultra-precision die-to-wafer hybrid bonding solutions, which are critical for 3D-IC heterogeneous integration.
Moreover, the advent of intelligent software guidance has made managing operators and workload balancing an automated and efficient process. This is complemented by the ability to ensure process traceability with every placement of die and components, fostering a truly smart factory environment. The synergy of these innovations is setting new standards for sustainable operations in the semiconductor industry.
Enhancing Performance with High-Precision Wafer Services
Achieving High Component Placement Rates
In the realm of professional wafer services, achieving high component placement rates is pivotal for maintaining throughput and efficiency. The integration of advanced machines like the SIPLACE CA2 has revolutionized this aspect by enabling direct placement from the wafer, which is both cost-effective and sustainable. This approach not only eliminates the need for taping but also reduces material feeding efforts and replenishment tasks.
The synergy between the SIPLACE CA2 and the SIPLACE TX micron high-speed placement machine exemplifies the fusion of two worlds into one production line. This combination offers unparalleled flexibility and yield, with the capability to place up to 50,000 components per hour with an accuracy of up to 10 μm @ 3 σ. Such precision is underpinned by multiple high-end vision systems that ensure comprehensive process control.
Optimizing the supply chain is another critical factor that influences component placement rates. Efficient sourcing of components and effective inventory management are essential for seamless operations. The SIPLACE CA2’s ability to operate 24/7 in SiP production not only maximizes productivity but also advances sustainability by significantly reducing tape waste.
Integrating Die Buffering and Process Parallelization
The integration of die buffering and process parallelization is a game-changer in the realm of wafer services, offering a significant leap in operational efficiency. By streamlining these two processes, manufacturers can achieve a remarkable increase in component placement rates. This integration allows for a continuous flow of components, ensuring that the placement machinery is always engaged, thus minimizing idle time and maximizing throughput.
One of the standout examples of this technology in action is the SIPLACE CA2, part of the ASMPT SMT Solutions. It exemplifies how die buffering and parallel processing can be harmonized to deliver exceptional performance. The SIPLACE CA2 boasts the capability to place up to 50,000 components per hour directly from the wafer, with an impressive accuracy of up to 10 μm @ 3 σ. This level of precision and speed is a testament to the advanced engineering and design of modern wafer services.
The benefits of integrating die buffering with process parallelization are not limited to speed and accuracy alone. They also extend to cost savings and sustainability. By eliminating the need for die taping, manufacturers can reduce both the direct costs associated with taping and the indirect costs of quality issues arising from the taping process. Furthermore, this approach significantly cuts down on tape waste, contributing to a more sustainable production environment.
Ultra Precision Die-to-Wafer Hybrid Bonding Solutions
The advent of ultra precision die-to-wafer hybrid bonding solutions marks a significant leap in wafer service capabilities. This technology enables the seamless integration of dies into complex 3D-IC structures, which is pivotal for the advancement of heterogeneous integration. The precision of these systems is critical for high-density applications where every micrometer counts.
The SIPLACE CA2, as a hybrid of SMT placement machine and die bonder, exemplifies this innovation. It processes SMDs and dies in a single step, eliminating the need for multiple specialized machines. This integration not only boosts efficiency but also contributes to a leaner production environment.
Feature | Benefit |
---|---|
Single-step processing | Reduces equipment needs |
High placement accuracy | Ensures component reliability |
Die buffering | Enhances throughput |
By adopting these solutions, manufacturers can expect not just a reduction in equipment footprint, but also a significant improvement in throughput and reliability. The ability to place up to 50,000 components per hour with an accuracy of up to 10 μm @ 3 σ is a testament to the system’s performance. Moreover, the integration of such advanced systems aligns with sustainability goals by reducing waste associated with traditional die-taping processes.
Streamlining Quality Management in Wafer Services
Comprehensive Quality Control Measures
In the realm of semiconductor production, comprehensive quality control measures are indispensable for ensuring the integrity and performance of electronic components. High-end vision systems play a crucial role in this process, offering unparalleled precision in detecting even the minutest defects and inconsistencies. These systems are part of a larger suite of tools that work in tandem to provide a robust quality management framework.
The integration of multiple machines within a single production line exemplifies the synergy between speed and accuracy. For instance, the SIPLACE CA2 and the SIPLACE TX micron high-speed placement machine combine to offer both flexibility and high yield in SiP production. This dual-machine setup not only streamlines the quality control process but also enhances the overall efficiency of the production line.
Quality control in electronics manufacturing is further augmented by advanced software solutions like PRECiV™, which offer sophisticated capabilities for detecting manufacturing defects on semiconductor wafers. These digital tools complement traditional methods, providing a comprehensive approach to quality assurance that is both efficient and reliable.
Full Single-Die-Level Traceability
In the realm of wafer services, full single-die-level traceability is a game-changer for quality management. This meticulous tracking system ensures that each die’s journey, from its origin on the wafer to its final destination on the circuit board, is monitored and recorded. The benefits of such a system are multifold:
- Enhanced accountability and quality assurance
- Simplified defect analysis and resolution
- Improved yield management and waste reduction
Implementing full traceability not only bolsters the integrity of the manufacturing process but also supports a lean and sustainable operation. By eliminating the need for die-taping and its associated waste, companies can realize significant cost savings. For instance, in a 24/7-SiP production environment, the reduction in tape waste can amount to 800 km of tape annually. This level of efficiency and environmental consideration is becoming increasingly crucial in the competitive landscape of wafer processing.
Expert Systems for Quality Assurance
In the realm of semiconductor wafer fabrication, the integration of expert systems for quality assurance has become a cornerstone for achieving operational excellence. Expert systems provide a significant relief for quality assurance staff, allowing for more efficient allocation of human resources while maintaining high standards of quality control. These systems are particularly beneficial in environments where precision and reliability are non-negotiable, such as in the automotive sector or in manufacturing settings with automated machinery.
The implementation of intelligent software guidance and workload balancing has revolutionized the management of operators, automating tasks that were once manual and prone to error. For instance, the Critical Manufacturing MES Solution offers a suite of tools designed to meet ambitious production goals and enhance production flexibility. This is complemented by automated planning systems that reduce the need for human interaction, aligning with the new normal of production environments.
Furthermore, ASMPT’s expert system not only supports quality assurance for its own equipment but is now also compatible with third-party hardware. This open approach to automation and software integration is drawing significant attention, as it enables a more resilient and adaptable production process. The table below summarizes the key benefits of expert systems in quality assurance:
Benefit | Description |
---|---|
Operator Efficiency | Automated guidance and balancing reduce manual oversight. |
Process Traceability | Ensures every component placement is recorded. |
Flexibility | Supports both ASMPT and third-party equipment. |
Resilience | Autonomous process optimization for consistent quality. |
Boosting Productivity with Innovative Wafer Technologies
Combining Die-Attach and Flip-Chip Processes
The integration of die-attach and flip-chip processes into a single machine represents a significant leap in semiconductor packaging technology. By combining these two processes, manufacturers can achieve maximum productivity in a more streamlined and cost-effective manner. This innovative approach eliminates the need for separate machines and processes, reducing both capital expenditure and floor space requirements.
The SIPLACE CA2, a hybrid of SMT placement machine and die bonder, exemplifies this advancement by processing SMDs and dies from a sawn wafer in one work step. This integration not only simplifies the production line but also enhances flexibility, allowing for quick changes between different types of components and reducing the time for setup and calibration.
Moreover, the direct placement from the wafer circumvents the traditional die-taping process, leading to substantial cost savings and sustainability benefits. The absence of taping reduces material waste and associated disposal efforts, contributing to a greener manufacturing environment. The SIPLACE CA2’s capability to place up to 50,000 components per hour with high precision further underscores the productivity gains achievable with this technology.
Full Multi-Die Capability and Rapid Wafer Swap
The integration of full multi-die capability within wafer services has revolutionized the semiconductor industry, offering unprecedented flexibility and efficiency. With systems capable of handling up to 50 different wafers and boasting rapid wafer swap times of less than 10 seconds, the transition between different wafer types is seamless and virtually instantaneous.
This rapid wafer swapping significantly enhances productivity, ensuring that downtime is minimized and throughput is maximized. The ability to use a wafer chuck, flux dipping unit, and multiple feeder tracks in parallel further streamlines the pick-up process from wafer to placement.
In terms of productivity gains, consider the following data:
Wafer Type | Swap Time (seconds) | Feeder Tracks |
---|---|---|
Type A | < 10 | 10 |
Type B | < 10 | 8 |
Type C | < 10 | 6 |
The table illustrates the efficiency of the system across different wafer types, all maintaining swap times under 10 seconds while offering a varying number of feeder tracks for different applications. This capability not only boosts productivity but also contributes to cost savings by reducing the need for multiple specialized machines and personnel deployment.
Integrating SMT Placement with Wafer-Based Chip Assembly
The integration of Surface Mount Technology (SMT) placement with wafer-based chip assembly represents a significant leap forward in the semiconductor manufacturing industry. By combining these processes, manufacturers can achieve a higher degree of automation and precision, leading to increased productivity and reduced costs.
The SIPLACE CA2 system exemplifies this integration, functioning as both an SMT placement machine and a die bonder. This dual capability allows for the processing of SMDs and dies in a single work step, directly from the sawn wafer. The result is a streamlined production line that eliminates the need for separate machines for die bonding, thereby reducing personnel requirements and enhancing connectivity.
Key benefits of integrating SMT placement with wafer-based chip assembly include:
- Elimination of taping costs and associated quality issues
- Reduction in material feeding and splicing tasks
- Savings of up to 800 kilometers of tape per year in full SiP production
- Rapid amortization of equipment costs, potentially within a year
The table below summarizes the advantages of the SIPLACE CA2 system:
Feature | Benefit |
---|---|
Hybrid SMT and die bonding | Streamlined production, fewer machines needed |
Direct wafer placement | Cost-effective and sustainable |
Full SiP production capability | High productivity in 24/7 operation |
As the industry continues to evolve, systems like the SIPLACE CA2 are paving the way for more efficient and cost-effective semiconductor manufacturing, ultimately contributing to the advancement of technologies such as smart devices, 5G communication, and autonomous driving.
Achieving Cost Efficiency through Advanced Wafer Services
Eliminating Taping Costs and Quality Issues
The transition to advanced wafer services offers a significant opportunity for cost savings by eliminating the need for die taping. This process not only reduces material costs but also mitigates quality issues associated with taping. By processing dies directly from the diced wafer, companies can save on both the financial and environmental costs of tape waste. For instance, in a 24/7-SiP production environment, the savings can be substantial.
Savings Aspect | Annual Reduction |
---|---|
Tape Usage | 800 km |
Quality Costs | Significant |
Furthermore, the integration of intelligent software guidance and workload balancing in wafer services enhances the efficiency of managing operators. This smart factory approach ensures process traceability with every placement of die and components, contributing to a more cost-effective and sustainable production process.
Material Feeding Efficiency and Splicing Task Reduction
The integration of direct wafer placement technologies has revolutionized material feeding efficiency in wafer services. By bypassing the taping process, the SIPLACE CA2 system significantly reduces the need for operator intervention in replenishment and splicing tasks. This not only streamlines operations but also contributes to a more sustainable production environment.
The economic impact of these advancements is substantial. For instance, the SIPLACE CA2’s ability to place up to 50,000 components per hour from the wafer with high precision is a testament to its productivity. Moreover, the elimination of taping costs and the associated quality issues inherent in the die-taping process result in considerable savings. The table below highlights the key benefits:
Benefit | Description |
---|---|
Cost Savings | Eliminates taping costs and reduces tape-waste disposal efforts. |
Productivity | Places up to 50,000 components per hour with high accuracy. |
Sustainability | Saves 800 km of tape annually in 24/7-SiP production. |
Furthermore, the system’s unique flexibility allows for the processing of up to 50 different wafers, with a rapid wafer swap time of less than 10 seconds. This ‘full multi-die capability’ ensures that production can adapt quickly to changing demands without compromising on quality or efficiency.
Economic Automation and Smart Factory Integration
The integration of economic automation and smart factory systems is revolutionizing the semiconductor industry. By leveraging AI and ML, manufacturers are able to analyze data generated by equipment, leading to improved health monitoring and process control. This smart manufacturing approach is not only suitable for enhancing efficiency but also for ensuring the resilience of production processes.
Key benefits of smart factory integration include:
- Seamless data flow from the shop floor to the cloud
- Autonomous process optimization for more resilient production
- Intelligent software guidance for managing operators and workload balancing
ASM’s integrated smart factory solutions demonstrate the power of total data and process integration. With premium software and technology partnerships, ASM is at the forefront of transforming manufacturing environments. The Critical Manufacturing MES Solution, for example, automates planning and reduces human interactions, aligning with the new normal of production flexibility requirements.
Conclusion
In the fast-paced and ever-evolving world of semiconductor manufacturing, professional wafer services stand as a cornerstone for achieving peak efficiency and sustainability. The integration of advanced tools like the SIPLACE CA2, which combines high-speed chip assembly with SMT placement, has revolutionized the industry by enabling direct wafer placement, thereby saving significant resources and reducing waste. With the ability to handle multiple wafers with rapid swap times and maintain full traceability of each die, these services offer unparalleled flexibility and quality management. As we have seen, the adoption of such technologies not only maximizes productivity and cost-effectiveness but also aligns with sustainable practices by minimizing tape waste and process risks. The future of electronics manufacturing is being shaped by these innovations, and companies that leverage these professional wafer services are poised to lead the charge in the race towards maximizing NAND capacity and accelerating technological advancements in sectors like automotive AI. As we look ahead, it is clear that the strategic implementation of professional wafer services will continue to be a key driver in the pursuit of operational excellence and competitive edge in the semiconductor industry.
Frequently Asked Questions
How does direct die processing from diced wafers contribute to sustainability?
Direct die processing eliminates the need for the die-taping process, significantly reducing tape waste. In a 24/7-SiP production environment, this can result in saving up to 800 kilometers of tape annually.
What are the performance capabilities of the SIPLACE CA2 in terms of component placement?
The SIPLACE CA2 can place up to 50,000 components per hour directly from the wafer with an accuracy of up to 10 μm @ 3 σ, thanks to die buffering and process parallelization.
How does integrating SMT placement with wafer-based chip assembly enhance productivity?
By processing SMT components and dies directly from the wafer with die-attach and flip-chip processes in the same work step, productivity is maximized, and tape-related costs and quality issues are eliminated.
What does ‘full single-die-level traceability’ mean in quality management?
Full single-die-level traceability refers to the ability to track data for each die from its source on the wafer to its final placement position on the circuit board, ensuring comprehensive quality control.
How does the integration of die-to-wafer hybrid bonding solutions impact 3D-IC heterogeneous integration?
The integration of ultra precision die-to-wafer hybrid bonding solutions enables more efficient and precise high-density applications and SiPs, advancing the industry’s capabilities in 3D-IC heterogeneous integration.
What are the benefits of automating electronics manufacturing with ASM equipment?
Automating with ASM equipment can exponentially increase output, expand the technology range, and make economic sense by minimizing process risks and integrating high-speed chip assembly with SMT placement.