Navigating the Evolving Landscape of the Wafer Industry: Current Trends and Future Directions
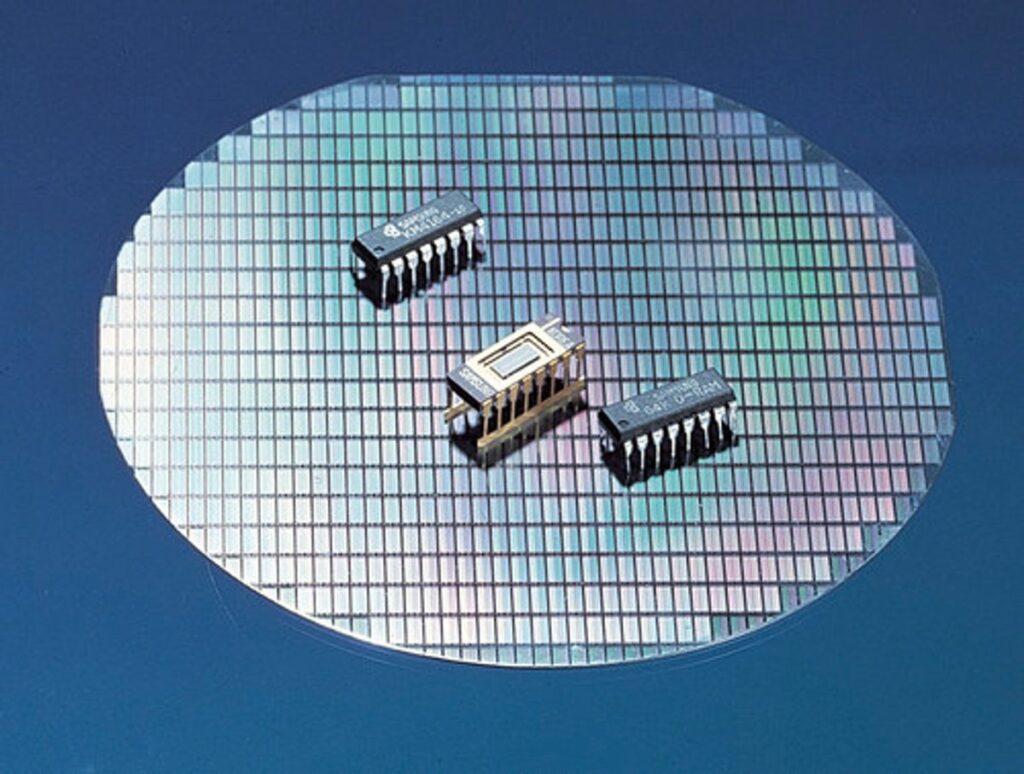
The wafer industry is undergoing a transformative phase marked by rapid technological advancements and shifting market dynamics. As companies navigate this evolving landscape, they face the challenge of integrating Industry 4.0 innovations into semiconductor manufacturing processes. This article delves into the current trends and future directions of the wafer industry, examining the impact of data management, cloud-native architectures, standardization efforts, and industry collaboration on the production of semiconductors.
Key Takeaways
- Industry 4.0 is revolutionizing semiconductor manufacturing with data-driven decision-making, automation, and smart manufacturing, leading to higher efficiency and product quality.
- The adoption of cloud-native architectures and the Sapience Manufacturing Hub are addressing the challenges of handling vast amounts of shop floor data, optimizing equipment productivity.
- New technologies are breaking down data silos and improving data extraction, enabling seamless integration with OpenAPI and enhancing interoperability among stakeholders.
- The North America Information & Control Committee is spearheading standardization efforts to tackle compatibility issues and promote collaboration in the semiconductor industry.
- Future directions for the wafer industry include anticipating technological innovations, developing strategies to maintain a competitive edge, and responding to market shifts and consumer demands.
Industry 4.0’s Impact on Semiconductor Manufacturing
Challenges of Data-Driven Decision-Making
In the realm of semiconductor manufacturing, the transition to data-driven decision-making poses significant challenges. The sheer volume of data produced during wafer fabrication is staggering, encompassing a wide range of equipment parameters critical for product quality and yield. Efficiently extracting, processing, and analyzing this data is paramount, yet traditional systems often lead to compatibility issues and isolated data silos.
The lack of proper labeling is a notable hurdle, as highlighted by an industry article on AI/ML challenges in test and metrology. Most suppliers grapple with limited data sets, a consequence of companies’ reluctance to share information. This limitation hampers the potential of machine learning algorithms, which require extensive and well-labeled data to be effective.
To address these issues, new platforms are emerging that aim to standardize data collection and enhance compatibility. For example, the Cimetrix Sapience platform utilizes data collection plan templates to harmonize data from diverse sources. This approach is crucial for enabling real-time analysis and optimization across different target destinations.
Automation and Connectivity in Wafer Production
The advent of Industry 4.0 has brought about a transformative change in wafer production, with automation and connectivity at the forefront. The integration of advanced technologies has led to significant improvements in efficiency and precision, setting new standards for semiconductor manufacturing.
To illustrate the impact of these advancements, consider the following key areas:
- Equipment Control: Precise control is crucial for high-quality output. Smart manufacturing enables equipment to adapt to changing conditions, enhancing throughput.
- Data Management: The sheer volume of data produced in wafer fabs is staggering. Efficient extraction and analysis of this data are vital for informed decision-making.
- Productivity: By leveraging automation, factories can boost both equipment and overall factory productivity, ensuring a competitive edge in a demanding market.
Despite the clear benefits, the transition to a more automated and connected production environment is not without its challenges. Companies must navigate the complexities of integrating various systems and protocols to achieve a seamless operation. The use of REST APIs and other modern approaches is facilitating this integration, allowing for better communication between different pieces of manufacturing equipment.
The Role of Smart Manufacturing in Enhancing Productivity
Smart manufacturing stands at the forefront of Industry 4.0, revolutionizing the semiconductor industry by enabling equipment to communicate and coordinate seamlessly. This interconnectedness allows for real-time adjustments across the factory floor, from material dispatch to recipe parameter changes, which are critical for maintaining high productivity levels.
The integration of smart manufacturing technologies leads to significant improvements in manufacturing KPIs, such as yield rates and equipment efficiency. Predictive maintenance, facilitated by these technologies, also plays a vital role in reducing downtime and enhancing overall factory productivity.
The human aspect of manufacturing is also evolving with Industry 4.0. Monitoring both physical and cognitive workloads of operators is becoming increasingly important in creating a human-centric manufacturing environment. This focus on operator well-being is not only ethical but also contributes to a more resilient and efficient workforce.
KPI | Before Smart Manufacturing | After Smart Manufacturing |
---|---|---|
Yield Rate (%) | 85 | 92 |
Equipment Downtime (hours/year) | 500 | 350 |
Operator Satisfaction Index | 70 | 85 |
As the table illustrates, the transition to smart manufacturing has tangible benefits. Companies that leverage these advancements can expect to see a marked improvement in both quantitative metrics and qualitative aspects of their operations.
Advancements in Data Management and Analysis
Overcoming Data Silos with New Technologies
The semiconductor industry is rapidly embracing new technologies to address the challenge of data silos. These isolated pockets of data hinder the seamless flow of information, which is crucial for informed decision-making and operational efficiency. By integrating platforms like the Cimetrix Sapience, companies can streamline data collection and analysis, ensuring consistency across various sources.
One significant advancement is the use of data collection plan (DCP) templates, which standardize the data gathering process from diverse equipment. This approach not only simplifies data integration but also facilitates real-time analysis and optimization. Moreover, cloud-native platforms like the Sapience Manufacturing Hub are revolutionizing how data is scaled and utilized, leveraging common data center tools to provide actionable insights to corporate applications.
The table below illustrates the impact of new technologies on data management in semiconductor manufacturing:
Technology | Benefit | Example |
---|---|---|
DCP Templates | Standardizes data collection | Cimetrix Sapience |
Cloud-Native Platforms | Scales data effectively | Sapience Manufacturing Hub |
As the industry continues to evolve, these technological solutions are proving to be vital in overcoming development silos and enhancing the overall productivity of semiconductor operations.
The Importance of Efficient Data Extraction
In the fast-paced world of semiconductor manufacturing, efficient data extraction is a cornerstone for maintaining high standards of quality and yield. The vast quantities of data produced during wafer fabrication must be harnessed to ensure the reliability and performance of semiconductor devices, which are foundational to modern technologies.
The transition from proprietary systems to more open and standardized interfaces has been pivotal. REST APIs, for instance, offer a uniform method to extract data across various equipment and protocols. This shift not only breaks down data silos but also facilitates real-time analysis and optimization. Platforms like Cimetrix Sapience™ utilize data collection plan templates, which standardize data extraction and enhance compatibility.
The benefits of such advancements are manifold. They provide greater visibility into equipment behavior, enable tighter process control, and support traceability at the individual device level. Moreover, the use of OpenAPI for specification language simplifies the discovery and understanding of how APIs function, streamlining the integration process.
To ensure data integrity, immediate persistence of data to disk is essential. This approach safeguards against data loss during unexpected terminations, allowing for recovery and restoration of the last saved values. Such robust data management practices are integral to the continuous improvement and innovation within the wafer industry.
Leveraging OpenAPI for Seamless Integration
The adoption of OpenAPI standards is transforming the way semiconductor manufacturers approach software integration. OpenAPI’s role as a universal language for API design is pivotal in creating a cohesive environment for various software systems to communicate effectively. This standardization is particularly beneficial in an industry where precision and reliability are paramount.
OpenAPI’s broad language support for code generation is a game-changer for developers. It allows the creation of SDKs in different programming languages, which is crucial for integrating diverse application architectures. Here’s a quick overview of the languages supported:
Language | SDK Support |
---|---|
Java | Yes |
Python | Yes |
C# | Yes |
Ruby | Yes |
Go | Yes |
Moreover, the OpenAPI ecosystem, including tools like Swagger UI, empowers developers to visualize and interact with APIs without any backend logic in place. This accelerates learning and experimentation, streamlining the development process.
The vast userbase and stability that OpenAPI enjoys, thanks to the backing of major companies, provide a solid foundation for its implementation. The collective knowledge and support available make it an invaluable asset for both new and experienced developers in the wafer industry.
The Rise of Cloud-Native Architectures in Wafer Fabs
Benefits of Cloud Adoption for Semiconductor Manufacturing
The semiconductor industry is rapidly embracing cloud technologies to stay competitive. Cloud adoption offers a multitude of benefits, including faster time to market and improved operational efficiencies. By leveraging cloud solutions, firms can streamline their design and development processes, leading to quicker product releases.
Another significant advantage is the enhancement of foundry operations and yield. The cloud enables smarter manufacturing practices by facilitating better data management and analysis. This results in higher efficiency and lower costs, as well as improved product quality. The table below summarizes the key benefits of cloud adoption in semiconductor manufacturing:
Benefit | Description |
---|---|
Faster Time to Market | Accelerates design and development processes. |
Improved Operations | Enhances foundry operations and overall yield. |
Smarter Manufacturing | Supports data-driven decision-making and process optimization. |
Cost Efficiency | Reduces expenses through streamlined workflows and better resource management. |
Embracing cloud technologies not only addresses the challenges of data-driven decision-making but also aligns with the goals of Industry 4.0. It increases visibility into manufacturing equipment and process behavior, ensuring that companies can respond swiftly to market shifts and consumer demands.
Navigating the Complexity of Shop Floor Data
The semiconductor industry is facing a Herculean task in managing the deluge of data produced on the shop floor. The Sapience Manufacturing Hub has emerged as a pivotal solution, addressing the need for actionable data to be accessible from the factory floor to the top floor. With wafers taking months to process and thousands of steps involved, the challenge of handling even a single lot of data is immense.
Fab managers, in an effort to stay afloat in this data flood, have turned to data center technologies and software architectures typically used by tech giants. These systems are designed to handle vast amounts of data, a necessity given the static nature of fab data architectures which rarely undergo complete overhauls.
The Hub’s role is to streamline the collection and aggregation of clean data, enabling milestone processes to report on key factors such as product, order, and lot. This facilitates precise cost accounting at the enterprise level, which is critical when costs rise and yields decrease. Below is a summary of the Hub’s impact on data management:
- Data Aggregation: Aggregates data for reporting by product, order, lot, etc.
- Cost Accounting: Enables accurate cost allocation for materials, labor, and rework.
- Scalability: Utilizes common data center tools for cloud-native scalability.
- Data Accessibility: Transforms shop floor data into actionable insights for decision-making.
Sapience Manufacturing Hub: A Case Study
The Sapience Manufacturing Hub represents a significant leap in the semiconductor industry’s adoption of cloud-native architectures. It is designed to bridge the gap between the factory floor and corporate decision-making by providing actionable data in real-time. The Hub’s ability to scale using well-known data center tools makes it a pioneering solution for handling the vast amounts of data generated in wafer fab production.
At the heart of the Hub’s functionality is its capability to gather and aggregate clean data from the factory floor. This data is then reported in milestone processes, which are crucial for accurate cost accounting at the enterprise level. For instance, Company X, a leading semiconductor manufacturer, has successfully implemented Sapience to streamline data collection, equipment control, and traceability across their manufacturing processes.
The table below illustrates the impact of the Sapience Manufacturing Hub on Company X’s production line:
Metric | Before Sapience | After Sapience |
---|---|---|
Data Collection Efficiency | Low | High |
Equipment Control | Manual | Automated |
Traceability | Inconsistent | Consistent |
The Hub’s integration with OpenAPI, SECS/GEM, and GEM300 standards further enhances its interoperability, making it a robust solution for the challenges faced by the semiconductor industry.
Standardization Efforts and Industry Collaboration
The Role of the North America Information & Control Committee
The North America Information & Control Committee plays a pivotal role in the standardization of semiconductor manufacturing processes. Meeting tri-annually, the committee’s task forces collaborate to address industry challenges and drive innovation. Their efforts are crucial in advancing the integration of automation standards across various stages of semiconductor production, including assembly and test.
Key initiatives include the Advanced Backend Factory Integration (ABFI) and Single Device Traceability, which aim to enhance the efficiency and traceability of semiconductor devices. The committee’s work ensures that the industry moves towards a unified approach, facilitating better control and interoperability among different equipment and software products.
The following table summarizes the committee’s recent activities:
Meeting Date | Focus Area | Outcome |
---|---|---|
Nov 6, 2023 | GEM 300 | Updates to automation standards |
Nov 7, 2023 | ABFI | Progress on backend integration |
Nov 8, 2023 | E134 Testing | Preparation for vendor test sessions |
Members and interested parties are encouraged to engage with the committee to contribute to the ongoing development of industry standards. For those looking to participate, reaching out to the task force leaders is the recommended first step.
Addressing Compatibility Issues through Standards
The semiconductor industry is making strides in addressing compatibility issues through the adoption of comprehensive standards. By standardizing application and equipment interactions, manufacturers can minimize the need for custom software, leading to enhanced reliability and performance. This approach not only simplifies integration but also supports a range of standard protocols, including SEMI EDA and OPC UA, with clear documentation facilitating rapid adoption.
The SEMI standards are evolving to become more flexible and accessible. For instance, the modification of E164 to include well-known names from the GEM 300 series is a significant step. The introduction of subordinate standards (E164.1, E164.2, …) allows for a more tailored application of EDA within various industry sectors.
Recent ratifications by the ABFI Task Force, such as the new Consumables and Durables standard and improvements to the E142 substrate mapping standard, are indicative of the ongoing efforts to enhance standardization. These updates aim to provide clarity and consistency for implementers, ensuring more consistent adoption across the industry.
The table below summarizes the recent ballot outcomes and their implications for the industry:
Ballot Number | Description | Outcome |
---|---|---|
R2924A & R6925A | New Consumables and Durables standard | Passed |
6948 | Improvements to E142 substrate mapping standard | Passed |
7114 | Clarification on E5 Stream 21 Function 17/18 sequence | Passed |
7116 | Changes/corrections to E87 | Passed |
These standardization efforts are crucial for fostering interoperability and ensuring that the industry can collectively address compatibility challenges. As companies like Valens Semiconductor and Intel Foundry Services announce strategic collaborations to accelerate the adoption of standards like MIPI A-PHY, the industry is poised to benefit from enhanced ADAS and safety features, further boosting the industry’s chiplet technology.
Fostering Interoperability Among Stakeholders
In the pursuit of harmonization of standards, stakeholders in the wafer industry are increasingly recognizing the importance of interoperability. By aligning protocols and quality standards, the industry can ensure a seamless flow of information and interaction between various applications and equipment. This standardization minimizes the need for custom software, leading to enhanced reliability and performance.
The Cimetrix Sapience platform exemplifies this approach by supporting standard protocols like SECS/GEM, SEMI EDA, and OPC UA. The platform’s documentation and framework facilitate rapid development and integration, enabling stakeholders to quickly adapt to new interfaces and maintain a competitive edge.
Protocol | Description |
---|---|
SECS/GEM | For equipment to host communication |
SEMI EDA | Equipment data acquisition |
OPC UA | Machine to machine communication |
As the industry evolves, the commitment to interoperability will be crucial for fostering innovation and maintaining global competitiveness in silicon wafer manufacturing.
Future Directions in the Wafer Industry
Predicting the Next Wave of Technological Innovations
As the semiconductor industry approaches a pivotal juncture, the anticipation of future technological breakthroughs becomes increasingly crucial. Revolutionary materials and advanced manufacturing processes are set to redefine the capabilities of semiconductor devices. Groundbreaking technologies, such as artificial intelligence (AI), robotics, big data, and the Internet of Things (IoT), are not only enhancing economic growth but also providing solutions to complex societal challenges.
Digital twin technology, for instance, is becoming vital for real-time three-dimensional space reproduction. This innovation, along with the integration of millimeter wave (mmWave) technology into unmanned aerial vehicles (UAVs), is poised to overcome current bandwidth limitations and expand potential applications. The table below outlines the main driving forces behind the adoption of advanced memory chips in the automotive sector, which is a clear indicator of the industry’s direction:
Year | Automotive Memory Chips (%) |
---|---|
2023 | 8-9% |
2028 | 10-11% |
In the era of Industry 5.0, the synergy between these technologies will likely lead to unprecedented levels of productivity and innovation. Companies are now tasked with not only keeping pace with these changes but also leveraging them to maintain a competitive edge in a rapidly evolving market.
Strategies for Maintaining a Competitive Edge
In the dynamic realm of semiconductor manufacturing, companies must leverage cutting-edge technologies to stay competitive. Adopting innovative solutions like the Cimetrix Sapience platform is crucial for ensuring competitiveness and fostering innovation. This platform, along with other industry standards such as SECS/GEM, EDA, and OPC UA, provides manufacturers with the tools needed for advanced data analysis and equipment control.
To maintain a competitive edge, companies should focus on:
- Improving yield under stringent process constraints
- Enhancing factory and equipment productivity
- Boosting data collection and information extraction
- Increasing visibility into manufacturing equipment and process behavior
These strategies are not just about keeping pace with current trends but also about setting the stage for future advancements. By doing so, manufacturers can achieve better product quality, higher efficiency, and lower costs, which are essential for thriving in the ever-changing semiconductor manufacturing landscape.
Anticipating Market Shifts and Consumer Demands
In the dynamic wafer industry, anticipating market shifts and consumer demands is crucial for sustaining growth and innovation. The recent Wafer Processing Equipment Global Market Report 2024 underscores the significance of market analysis, projecting an increase from $143.62 billion in 2023 to $153.54 billion. This growth trajectory highlights the importance of strategic planning and the adoption of emerging technologies to meet future challenges.
Understanding consumer trends and technological advancements is essential for manufacturers to align their production with market expectations. The integration of automotive memory chips in various applications, such as autonomous driving and intelligent cockpits, is a testament to the evolving demands of the automotive industry, a key consumer of semiconductor products. As the industry moves towards more complex and specialized chips, companies must invest in research and development to stay ahead.
To effectively navigate these changes, businesses should consider the following steps:
- Continuously monitor market reports and industry forecasts.
- Invest in technology that supports the development of advanced semiconductor products.
- Foster partnerships with automotive and other key industries to understand their evolving needs.
- Prioritize innovation to address the demand for higher performance and energy-efficient chips.
Conclusion
As we navigate the complex and dynamic terrain of the wafer industry, it is clear that the integration of Industry 4.0 technologies is not just a trend but a necessity for survival and growth. The semiconductor manufacturing sector is at a pivotal juncture where the ability to efficiently process and analyze vast amounts of data can make or break a company’s competitive edge. With the advent of cloud-native architectures and open APIs, there is a promising path forward to overcome the challenges of data silos and enhance decision-making processes. The future of the wafer industry hinges on its capacity to adapt to these evolving landscapes, harnessing the power of smart manufacturing to drive innovation, improve yields, and reduce costs. As we have seen, the journey is akin to navigating treacherous waters, but with the right strategies and technologies, the industry can sail towards a more efficient and profitable horizon.
Frequently Asked Questions
How is Industry 4.0 impacting semiconductor manufacturing?
Industry 4.0 is reshaping semiconductor manufacturing by introducing data-driven decision-making, automation, and connectivity. This evolution leads to improved product quality, higher efficiency, and lower costs.
What are the challenges of managing data in wafer fabs?
Wafer fabs generate massive amounts of data, presenting challenges in data extraction, processing, and analysis. Overcoming proprietary systems, compatibility issues, and data silos is crucial for efficient data management.
What is the Sapience Manufacturing Hub, and how does it address shop floor data complexity?
The Sapience Manufacturing Hub is a cloud-native solution that facilitates actionable shop floor data analysis for the semiconductor industry. It addresses the complexity of processing vast amounts of data generated during wafer fabrication.
How does cloud adoption benefit semiconductor manufacturing?
Cloud adoption in semiconductor manufacturing offers scalability, flexibility, and improved data management capabilities. It enables better collaboration and can lead to cost savings and enhanced productivity.
What is the role of the North America Information & Control Committee?
The North America Information & Control Committee plays a pivotal role in standardization efforts, addressing compatibility issues, and fostering interoperability among stakeholders in the semiconductor industry.
What strategies can companies in the wafer industry use to maintain a competitive edge?
To maintain a competitive edge, companies in the wafer industry should invest in the latest technologies, anticipate market shifts, and continuously innovate to meet consumer demands and stay ahead of the competition.