Navigating the Market: How to Choose a Reliable Silicon Wafer Supplier
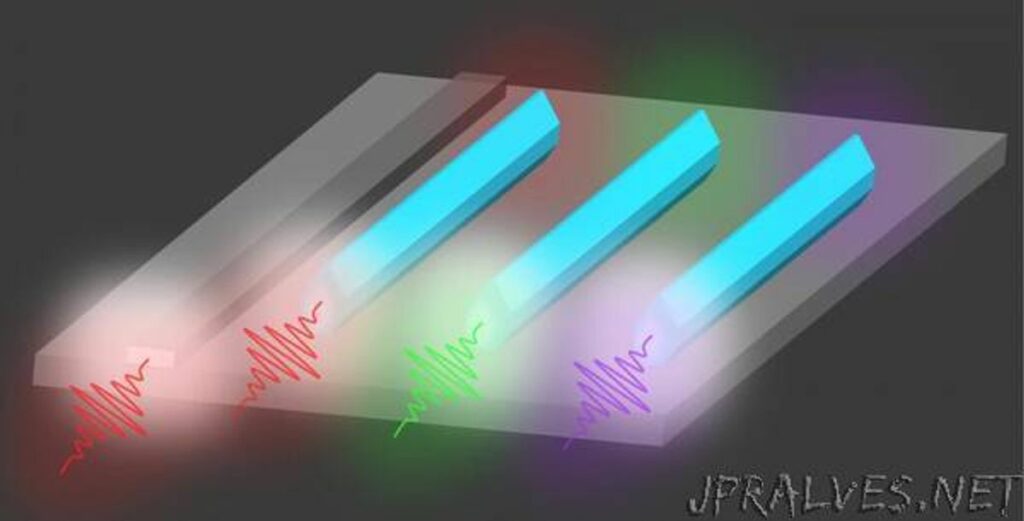
In the intricate world of semiconductor manufacturing, selecting the right silicon wafer supplier is crucial for ensuring a steady stream of high-quality components essential for electronic devices. With the dynamic nature of the industry, marked by technological advancements and shifting market trends, this article delves into the strategic approach required to identify and partner with reliable suppliers. We’ll explore the market landscape, assess supplier capabilities, consider strategic selection factors, and examine the impact of industry trends on supplier choice, ultimately guiding you to build a resilient supply chain partnership.
Key Takeaways
- Understanding the key players, market leaders, and emerging technologies is essential for navigating the silicon wafer market landscape effectively.
- Evaluating a supplier’s technological expertise, quality control standards, and financial stability is crucial for ensuring long-term reliability and performance.
- Strategic supplier selection involves aligning their strengths with your business needs, considering geographic proximity, and balancing price-performance trade-offs.
- Keeping abreast of industry trends, such as the rise of chiplets and mixed-foundry models, is vital for making informed decisions about future supplier partnerships.
- Building a resilient supply chain partnership requires fostering collaboration, diversifying sourcing to mitigate risks, and ensuring compliance with ethical standards.
Understanding the Silicon Wafer Market Landscape
Key Players and Market Leaders
The silicon wafer market is dominated by a few key players that have established themselves as market leaders. Taiwan Semiconductor Manufacturing Co. Ltd. (TSMC), for instance, is renowned for its advanced manufacturing capabilities and holds a significant share of the market. Other prominent companies include NVIDIA Corp., Intel Corp., and Broadcom Inc., each contributing to the industry with their unique technological innovations and product offerings.
Understanding the hierarchy and capabilities of these market leaders is crucial for businesses looking to secure a reliable silicon wafer supplier. The table below provides a snapshot of some of the top semiconductor companies as referenced by Investopedia:
Rank | Company Name | Notable Products/Technologies |
---|---|---|
#2 | Taiwan Semiconductor (TSMC) | Advanced manufacturing capabilities |
#3 | NVIDIA Corp. | Graphics processing units (GPUs) |
#4 | Intel Corp. | Microprocessors, chipsets |
#5 | Broadcom Inc. | Semiconductors for data center, networking |
It’s important to note that the landscape is dynamic, with emerging technologies and innovations constantly reshaping the competitive environment. Companies that invest in research and development and adapt to market shifts are more likely to maintain their leadership positions and provide long-term reliability to their clients.
Emerging Technologies and Innovations
The semiconductor industry is at a pivotal juncture, with revolutionary materials, advanced manufacturing processes, and groundbreaking technologies reshaping the landscape. As companies and countries vie for technological leadership, substantial investments are being funneled into new fabs and facilities, signaling a robust commitment to innovation.
In the realm of medical technology, advancements are particularly noteworthy. For instance, AI tools are being developed for more accurate cancer surveillance, algorithms for detecting heart defects in newborns, and haptic devices that can mimic the softness of materials like a beating heart. These innovations not only enhance the capabilities of silicon wafers but also expand their applications into critical areas such as healthcare.
The following list highlights some of the key areas where emerging technologies are making an impact:
- Advanced AI tools for healthcare applications
- Algorithms for early detection of medical conditions
- Haptic technology for material simulation
Staying abreast of these developments is crucial for suppliers aiming to maintain a competitive edge. The ability to adapt to and incorporate these innovations can be a significant differentiator in the market.
Supply Chain Dynamics and Security Concerns
The semiconductor industry’s supply chain is a complex web of interdependencies, where security and stability are paramount. Supply chain security has become a critical issue, with companies expanding into new regions to mitigate risks. This greenfield opportunity is driven by three factors: supply chain security, sustainability, and subsidies.
In the quest for a secure supply chain, companies must navigate various challenges:
- Ensuring the integrity of raw materials and components
- Protecting intellectual property throughout the supply chain
- Maintaining compliance with international trade regulations
- Building resilience against geopolitical shifts and trade disputes
Investments in new fabs and facilities underscore the industry’s commitment to supply chain security and technology leadership. However, the rising cost of power in chips and the need for faster processing add complexity to supply chain management. As companies strive for technological leadership, they must also contend with the trade-offs between speed and power consumption, which can have far-reaching implications for supply chain dynamics.
Evaluating Supplier Capabilities and Reliability
Assessing Technological Expertise
When choosing a silicon wafer supplier, assessing their technological expertise is crucial. Suppliers with advanced technological capabilities are better equipped to meet the evolving demands of the semiconductor industry. They should not only possess the latest equipment but also have a team of experts who are well-versed in cutting-edge manufacturing processes and innovations.
To gauge a supplier’s technological prowess, consider the following points:
- The range of technologies they have experience with, especially in advanced lithography such as EUV (Extreme Ultraviolet).
- Their track record in scaling up new technologies from R&D to mass production.
- The level of investment in ongoing research and development, as well as in maintaining state-of-the-art facilities.
It’s also informative to look at the supplier’s involvement in industry discussions and their contributions to setting standards. For instance, individuals from the supplier’s team may be featured in expert panels or cited in articles discussing the future of semiconductor manufacturing and the importance of technological innovation. This engagement is indicative of a supplier’s commitment to technological leadership and their ability to adapt to industry shifts.
Quality Control and Testing Standards
In the realm of silicon wafer manufacturing, quality testing is the cornerstone, acting as a gatekeeper to ensure each wafer meets the required specifications. This rigorous process is essential for maintaining high standards and minimizing defects that could impact the final product’s performance.
The implementation of advanced methodologies like Design Technology Co-optimization (DTCO) and System Technology Co-optimization (STCO) has paved the way for faster yield ramps. By integrating these approaches early in the design cycle, suppliers can enhance reliability and reduce the incidence of defects. Moreover, the advent of AI and ML tools in test and metrology is revolutionizing quality control, although their full potential will be realized through sustained time and collaboration.
To further illustrate the importance of quality control, consider the following aspects that are critical in evaluating a supplier’s testing standards:
- Adherence to industry benchmarks for wafer quality and reliability.
- Implementation of comprehensive screening to detect sources of silent data corruption.
- Continuous improvement practices in manufacturing screening to address emerging challenges.
It is imperative for suppliers to not only maintain robust quality control mechanisms but also to stay abreast of industry trends and technological advancements that can impact testing protocols and standards.
Long-term Stability and Financial Health
When selecting a silicon wafer supplier, it’s crucial to consider the long-term stability and financial health of potential partners. A supplier’s longevity in the market often reflects its ability to adapt and thrive amid industry changes. Evaluating a supplier’s financial records, market position, and growth prospects can provide insights into its future reliability.
Financial analysts and industry reports can be valuable resources for assessing a supplier’s health. For instance, Forbes’ recent article titled ‘5 Best Semiconductor Stocks For 2024: March Edition‘ highlights companies based on performance indicators and future growth potential. Such analyses can guide investors and partners in making informed decisions.
It’s also important to monitor the competitive landscape. Companies like TSMC have been noted for their diversified business models and profitability, which contribute to their market leadership and stability. In contrast, firms with less diversification may face greater risks, as seen with some companies experiencing sales declines due to overaccumulation of inventory by customers or geopolitical restrictions affecting sales in key markets.
Strategic Considerations for Supplier Selection
Aligning Supplier Strengths with Business Needs
When selecting a silicon wafer supplier, aligning their strengths with your business needs is crucial. Identify the core competencies of potential suppliers and match them against your company’s strategic objectives. For instance, if your focus is on high-volume production of advanced devices, a supplier like WaferPro, known for their high-volume manufacturing capacities, would be a suitable match.
Consider creating a supplier scorecard that evaluates various aspects such as technological expertise, quality control, and financial stability. Here’s an example of how to structure such a scorecard:
Criteria | Supplier A | Supplier B | Supplier C |
---|---|---|---|
Technological Expertise | High | Moderate | Low |
Quality Control | Excellent | Good | Satisfactory |
Financial Health | Stable | Uncertain | Risky |
Production Capacity | Large | Medium | Small |
Lastly, it’s important to assess how well the supplier can adapt to future market changes. A supplier that invests in emerging technologies and innovations will be more likely to grow with your business and meet long-term needs.
The Role of Geographic Proximity
The geographic location of a silicon wafer supplier can significantly influence the efficiency and cost-effectiveness of your supply chain. Proximity to the supplier can reduce shipping times and costs, which is particularly crucial in an industry where time-to-market can be a decisive competitive advantage. Additionally, being closer to the supplier facilitates easier communication and quicker resolution of any potential issues.
However, the benefits of geographic proximity must be weighed against other factors. For instance, suppliers in different regions may offer varying levels of technological sophistication or cost structures. Here is a comparison of potential advantages based on geographic proximity:
- Local Suppliers:
- Shorter lead times
- Lower shipping costs
- Easier communication
- Quicker issue resolution
- Distant Suppliers:
- Access to unique technologies
- Potential cost savings
- Diverse supply chain
Ultimately, the decision should align with your company’s strategic priorities, whether that’s minimizing logistics costs, accessing cutting-edge technology, or ensuring supply chain diversity.
Navigating Price Versus Performance Trade-offs
When selecting a silicon wafer supplier, one of the most critical decisions revolves around the price versus performance trade-offs. Cost-effectiveness is essential, but it should not come at the expense of the wafers’ quality and the supplier’s technological capabilities. To make an informed decision, consider the following points:
- Performance: Evaluate the supplier’s track record for delivering high-quality wafers that meet your technical specifications.
- Cost: Analyze the pricing models and long-term cost implications of partnering with the supplier.
- Balance: Aim for a supplier that offers a reasonable balance between cost and performance, ensuring that the value received justifies the investment.
It’s important to remember that the cheapest option may not always be the most beneficial in the long run. Suppliers that invest in emerging technologies and innovations may offer better performance, which can lead to greater overall savings through improved efficiency and reduced waste. A strategic approach to this trade-off involves a thorough analysis of both immediate and future needs, aligning them with the supplier’s strengths.
The Impact of Industry Trends on Supplier Choice
Adapting to Shifts in Demand for Chiplets and 3D Structures
The silicon wafer industry is witnessing a significant transformation with the increasing demand for chiplets and 3D structures. Fab capacity and wafer output, traditionally used to measure the industry’s health, are now less clear-cut indicators due to the rise of advanced packaging techniques. This shift necessitates a reevaluation of supplier capabilities to ensure they can meet the new demands of chip architecture.
Suppliers must now demonstrate proficiency in advanced packaging and integration technologies to stay competitive. The table below outlines key considerations when assessing a supplier’s readiness for the evolving market:
Consideration | Description |
---|---|
Technological Expertise | Ability to produce chiplets and 3D structures. |
Quality Assurance | Rigorous testing standards for new form factors. |
Innovation Capacity | Investment in R&D for emerging technologies. |
Supply Chain Agility | Flexibility to adapt to rapid market changes. |
As the industry moves towards customized chiplets for specific applications, such as AI, suppliers must also align with IP standards and ensure interoperability. The rise of chiplets is not just a trend but a fundamental shift in how semiconductor devices are designed and manufactured, requiring a strategic approach to supplier selection.
The Rise of Mixed-Foundry Models and Their Implications
The semiconductor industry is witnessing a paradigm shift with the rise of mixed-foundry models, where companies are increasingly leveraging the strengths of multiple foundries to optimize their production processes. This approach allows for greater flexibility and specialization, as different foundries may offer unique advantages in terms of technology nodes, capacity, or cost efficiency.
One of the key implications of this trend is the need for enhanced collaboration across the supply chain. As companies integrate various foundry services, they must navigate the complexities of coordinating design, manufacturing, and testing phases. This often requires establishing robust communication channels and shared standards to ensure seamless interoperability.
The table below highlights the revenue growth of top foundries, reflecting the industry’s expansion and the increasing relevance of strategic foundry partnerships:
Rank | Foundry | Revenue Growth (2023) |
---|---|---|
1 | Foundry A | 8.5% |
2 | Foundry B | 7.2% |
3 | Foundry C | 6.9% |
… | … | … |
10 | Foundry J | 5.4% |
In light of these developments, companies must also consider the challenges associated with heterogeneous integration, such as the need for advanced design flows and the potential for increased complexity in test and packaging processes.
Preparing for the Next Generation: 2.5D and Beyond
As the semiconductor industry advances, the transition to 2.5D and 3D packaging technologies is becoming increasingly important for silicon wafer suppliers. These advanced packaging methods allow for higher performance and functionality within a smaller footprint, addressing the insatiable demand for miniaturization and power efficiency. The evolution from traditional 1D PCB to sophisticated 3D hybrid bonding at the wafer level signifies a monumental shift in semiconductor packaging technologies.
Selecting a supplier adept in these next-generation technologies is crucial. Suppliers must not only demonstrate proficiency in current 2.5D integration techniques but also show a commitment to research and development for future advancements. The table below outlines key considerations when evaluating a supplier’s readiness for next-gen packaging:
Factor | Importance | Evaluation Criteria |
---|---|---|
Technological Expertise | High | Experience with 2.5D/3D packaging, R&D investment |
Quality Assurance | Critical | Testing standards for new packaging methods |
Scalability | Essential | Ability to meet future demand spikes |
Furthermore, the supplier’s ability to navigate the complexities of thermal integrity and the challenges associated with wire bond inspection for 3D structures is paramount. As the industry gears up for hybrid bonding and backside power delivery for sub-2nm devices, a supplier’s expertise in these areas will be a differentiator. By anticipating and preparing for these trends, businesses can ensure they are not left behind in the rapidly evolving semiconductor landscape.
Building a Resilient Supply Chain Partnership
Fostering Collaboration and Technical Exchange
In the rapidly evolving silicon wafer industry, fostering collaboration and technical exchange is crucial for innovation and growth. Partnerships between suppliers and clients can lead to shared technological advancements and a more robust product offering. For instance, workshops and conferences are pivotal in promoting industry standards and coordination, as seen with the CHIPS R&D Semiconductor Supply Chain Trust and Assurance initiative.
To illustrate the importance of collaboration, consider the following insights from industry experts:
- Nicolas Dujarrier emphasizes the growing attention on MRAM at smaller nodes.
- Erik Jan Marinissen points out that Chiplet IP standards are just the beginning of a broader collaborative effort.
- Maury Wood discusses the significant impact of chip power reduction on data center economics.
These discussions highlight the diverse areas where collaboration can yield substantial benefits. By engaging in technical exchanges, companies can stay ahead of the curve, ensuring they are well-prepared for future challenges and opportunities in the semiconductor landscape.
Mitigating Risks with Diversified Sourcing
In the quest for a resilient supply chain, diversified sourcing stands out as a strategic imperative. By spreading procurement across multiple suppliers, businesses can insulate themselves from regional disruptions, political instability, and supplier-specific risks. This approach not only enhances supply chain security but also introduces competitive pricing and innovation through a broader supplier base.
Key considerations for diversified sourcing include:
- Supplier performance track record
- Financial stability and business continuity plans
- Geographic distribution and logistical capabilities
- Alignment with industry standards and regulatory compliance
A well-structured diversified sourcing strategy can be visualized through a supplier risk assessment matrix. Below is an example of how companies might categorize their suppliers based on risk and performance:
Supplier | Risk Level | Performance | Strategic Importance |
---|---|---|---|
A | Low | High | Core |
B | Medium | Moderate | Secondary |
C | High | Low | Tertiary |
By systematically evaluating and categorizing suppliers, companies can make informed decisions on which partnerships to nurture for long-term stability and which to keep at arm’s length for risk mitigation.
Ensuring Compliance and Ethical Standards
In the competitive landscape of silicon wafer suppliers, ensuring compliance and ethical standards is not just a legal obligation but a strategic advantage. Suppliers who adhere to stringent ethical guidelines and compliance protocols are more likely to foster trust and secure long-term partnerships with clients. To ensure that our results are measurable and therefore accountable, we follow multiple sustainability reporting frameworks such as the Sustainability Accounting Standards Board (SASB) and the Global Reporting Initiative (GRI).
Adherence to these standards can be assessed through various means, including but not limited to:
- Corporate sustainability reports, which provide transparency on a company’s environmental, social, and governance (ESG) efforts.
- Certifications and audits from recognized industry bodies.
- Commitment to international labor and human rights standards.
It is crucial for businesses to verify that their suppliers not only claim to follow these standards but also provide evidence of their compliance. This due diligence is essential in building a resilient supply chain that is robust against legal and reputational risks.
Conclusion
In the intricate dance of the semiconductor market, selecting a reliable silicon wafer supplier is a pivotal step that can determine the success of your technological endeavors. Throughout this article, we’ve explored various facets of the decision-making process, from understanding the importance of supply chain security to recognizing the role of industry leaders like TSMC and Micron. As we’ve seen, factors such as diversification, profitability, and market leadership are crucial when considering long-term investments in this sector. It’s imperative to stay informed about the latest trends, such as the shift towards chiplets in automotive and the rise of silicon carbide in power semiconductors. Whether you’re pondering a significant investment or strategizing for your company’s future, the insights from industry experts and the evolving landscape underscore the need for a meticulous approach. By applying the knowledge and considerations discussed, you’ll be better equipped to navigate the market and choose a silicon wafer supplier that aligns with your technical requirements and business objectives.
Frequently Asked Questions
What are the key factors to consider when choosing a silicon wafer supplier?
When selecting a silicon wafer supplier, consider their technological expertise, quality control, financial stability, alignment with your business needs, geographic proximity, and how they balance price and performance.
How does the rise of mixed-foundry chiplets affect supplier selection?
The trend towards mixed-foundry chiplets requires suppliers that are versatile and can integrate different technologies. Suppliers must be able to collaborate with various foundries and ensure compatibility across chiplets.
What is the significance of thermal integrity challenges in 2.5D integration?
Thermal integrity is crucial in 2.5D integration due to increased power density. Suppliers must provide wafers that can withstand high thermal stresses and work with advanced cooling solutions.
What role does geographic proximity play in choosing a silicon wafer supplier?
Geographic proximity can affect lead times, shipping costs, and ease of communication. Close proximity allows for quicker response times and potential cost savings, but should not override quality and technological capability considerations.
How can businesses ensure a resilient supply chain when sourcing silicon wafers?
To ensure a resilient supply chain, diversify your sourcing, establish collaborative relationships with suppliers, and enforce compliance with ethical and industry standards.
What are the challenges in navigating price versus performance trade-offs with silicon wafer suppliers?
Navigating this trade-off involves assessing the long-term value of higher-quality wafers against the immediate cost savings of more affordable options, ensuring that the choice supports your business’s strategic goals and quality requirements.