Optimizing Efficiency: The Impact of Semiconductor-driven Industrial Automation Systems
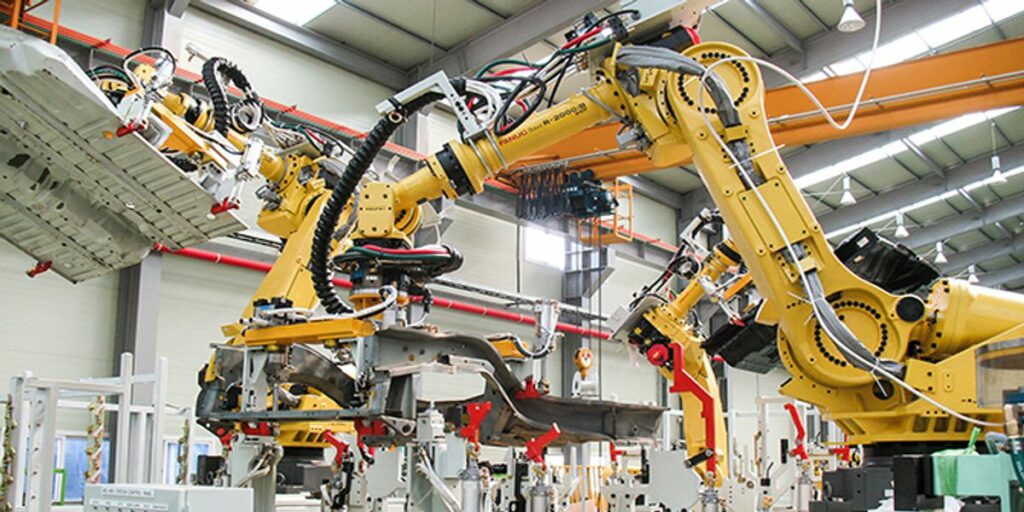
The integration of semiconductors into industrial automation systems has revolutionized the way industries operate, leading to significant gains in efficiency and productivity. This article explores the multifaceted impact of semiconductor-driven industrial automation, including the role of Programmable Logic Controllers (PLCs) and Supervisory Control and Data Acquisition (SCADA) systems, the intersection of artificial intelligence (AI) with semiconductor efficiency, the transformative influence of the Internet of Things (IoT), and the optimization of energy at the system level. We will delve into how these technological advancements optimize performance and provide a competitive edge in the fast-paced industrial sector.
Key Takeaways
- Semiconductors are pivotal in industrial automation, enhancing precision in power delivery and manufacturing to ensure consistent product quality and efficient processes.
- The synergy of AI and IoT with semiconductors drives innovation in supply chains, product development, and predictive maintenance, leading to faster time-to-market and improved yields.
- Advanced semiconductor technologies in PLCs and SCADA systems are instrumental in boosting operational efficiency, productivity, and quality control in various industries.
- Optimizing energy at the system level through machine learning, hardware optimization, and low power-high performance solutions is crucial for sustainable and efficient manufacturing.
- Semiconductor switching technologies like IGBTs and MOSFETs offer superior efficiency, enabling industries to maintain a competitive edge through high-speed, energy-efficient operations.
The Role of Semiconductors in Advancing Industrial Automation
Programmable Logic Controllers (PLCs) and Their Impact
Programmable Logic Controllers (PLCs) are the cornerstone of modern industrial automation, providing the real-time control necessary for efficient operations. PLCs are known for their robustness and reliability, ensuring consistent performance even in the most demanding industrial environments. Their modular architecture, typically comprising a central processing unit (CPU), memory, input/output (I/O) modules, and communication interfaces, allows for a flexible and scalable approach to managing complex processes.
The adaptability of PLCs is a key feature that significantly enhances industrial automation. Engineers can easily reprogram PLCs to adjust control logic, implement new features, or incorporate safety protocols, all without extensive hardware modifications. This reprogrammability not only saves time and resources but also enables industries to respond swiftly to changing market demands or production requirements.
Feature | Description |
---|---|
Real-time Control | Executes control tasks based on sensor input and actuator output |
Robustness | Operates reliably in harsh industrial conditions |
Modularity | Consists of CPU, memory, I/O modules, and communication interfaces |
Reprogrammability | Allows for easy updates and process adjustments |
By streamlining control tasks and offering a high degree of customization, PLCs have become an indispensable part of industrial automation systems, driving efficiency and productivity across various sectors.
Supervisory Control and Data Acquisition (SCADA) Systems
SCADA systems are pivotal in the realm of industrial automation, offering a sophisticated layer of supervision, data acquisition, and analysis for complex industrial operations. These systems are designed to monitor a multitude of devices and processes, ensuring that anomalies are detected promptly and that decisions are made on a solid foundation of comprehensive data.
The architecture of SCADA is intricate, comprising various components such as remote terminal units (RTUs), programmable logic controllers (PLCs), SCADA Master Stations, and human-machine interfaces (HMIs). This distributed setup allows for the seamless collection of data from field sensors, which is then processed and analyzed at the Master Station. Control commands are issued based on this analysis, optimizing the performance and safety of industrial processes.
SCADA systems not only gather and manage data but also provide advanced features like remote access, data analytics, and integration with broader enterprise systems. This integration offers a holistic view of operations, facilitating more effective control and optimization strategies. The table below summarizes the key functions of SCADA components:
Component | Function |
---|---|
RTUs/PLCs | Collect data from sensors; control field actuators |
SCADA Master Station | Acquire, process, and analyze data; send control commands |
HMI | Interface for operators to monitor and interact with the system |
Communication Network | Connects all components for data transfer |
Historian | Stores data for trend analysis and reporting |
Alarm & Event Management | Manages alerts and logs significant events |
Understanding the differences between PLC and SCADA systems is essential for optimizing industrial automation. While both are critical, they serve unique functions and possess distinct characteristics that, when leveraged correctly, can significantly enhance operational efficiency.
Enhancing Precision in Power Delivery and Manufacturing
Semiconductors find extensive use in industrial automation, where precise control over power delivery is crucial for optimizing manufacturing processes and ensuring consistent product quality. The ability to handle robust power efficiently is a preferred choice in industries where reliability and precision are paramount.
Machine learning is becoming a transformative force in this domain. By analyzing manufacturing data, semiconductor systems can predict potential issues, identify component failures, and suggest optimal layouts for integrated circuits (ICs), thereby enhancing yield and efficiency.
The following table illustrates opportunities for power saving during design stages:
Design Stage | Power Saving Opportunity |
---|---|
Initial Design | Identification of power-hungry components |
Optimization | Layout adjustments for better power distribution |
Final Review | Ensuring all components meet power efficiency standards |
Leveraging Artificial Intelligence for Semiconductor Efficiency
Optimizing Supply Chains and Logistics with AI
The integration of machine learning algorithms into supply chain management has revolutionized the way businesses forecast demand, manage inventory, and streamline logistics. By analyzing historical data and identifying patterns, these algorithms can predict demand fluctuations with high accuracy, leading to more efficient inventory management and reduced costs.
For example, AI-powered routing algorithms optimize logistics, resulting in faster and more cost-effective deliveries. Retail giants like Walmart have demonstrated the effectiveness of AI in enhancing supply chain resilience and decision-making capabilities. Similarly, in manufacturing, AI-driven inventory management systems utilize historical sales data and market trends to maintain optimal stock levels, minimizing carrying costs while ensuring product availability.
The application of AI in supply chain management is not limited to forecasting and inventory. AI-powered Robotic Process Automation (RPA) is also making strides in automating manual processes, increasing operational efficiency, and improving supply chain visibility. A case in point is a global manufacturer of heavy construction and mining equipment that improved its supply chain visibility by 60% through the implementation of an AI-driven logistics and supply chain management system.
Data Analytics and Machine Learning in Product Development
The integration of artificial intelligence (AI) and machine learning (ML) in product development has revolutionized the way manufacturers approach new product creation. By analyzing extensive datasets, AI enables the identification of market trends and customer preferences, which are crucial for designing products that meet market needs. This data-driven approach not only aligns product features with consumer demands but also streamlines the development process, leading to a more efficient path from concept to market.
Predictive maintenance, powered by AI, is transforming the manufacturing landscape. Utilizing digital twins and advanced analytics, companies can anticipate equipment failures and optimize maintenance schedules. This not only boosts operational efficiency but also contributes to significant cost savings. Similarly, AI-driven predictive quality assurance allows for the early detection of potential defects, ensuring that quality issues are addressed before they affect the final product.
In the realm of supply chain management, AI and ML are indispensable tools. They enhance demand forecasting, optimize inventory, and improve logistics. For example, an automotive parts manufacturer might employ ML models to predict the demand for spare parts, thereby optimizing stock levels and minimizing costs. This predictive capability is a testament to the power of AI in making data-driven decisions that refine product development and manufacturing processes.
Fostering Innovation and Collaboration through AI
The integration of semiconductors with artificial intelligence (AI) is not just enhancing the capabilities of industrial systems but is also pivotal in fostering a culture of innovation and collaboration. AI’s role in the semiconductor industry transcends operational efficiency; it facilitates knowledge sharing and the creation of feedback loops that are essential for continuous improvement and innovation.
In the realm of industrial automation, the synergy between cobots (collaborative robots) and AI epitomizes the collaborative strategy. Cobots, designed to work alongside human operators, leverage AI to navigate complex environments and assist in tasks such as picking and packing. This human-machine coordination is crucial for achieving operational excellence and is a testament to the transformative impact of AI in manufacturing.
Appinventiv’s custom AI solutions exemplify the potential of AI to revolutionize manufacturing. By partnering with IT consulting services, companies can harness the power of AI and machine learning to transform their operations, ensuring they remain competitive in a dynamic business landscape.
Internet of Things (IoT): A Catalyst for Semiconductor Innovation
IoT-Driven Data Analytics for Semiconductor Layout Optimization
The integration of IoT in semiconductor manufacturing has ushered in a new era of layout optimization. By harnessing IoT-driven data analytics, companies are able to streamline the design process, enhance precision, and ultimately boost yields. This is achieved through the continuous collection and analysis of data from various stages of the semiconductor production cycle.
IoT sensors and advanced analytics work in tandem to provide actionable insights. These insights enable engineers to make informed decisions about layout adjustments that can lead to significant improvements in performance and efficiency. For instance, data on thermal patterns and electrical performance can guide the placement of components to minimize heat dissipation and power loss.
The table below illustrates the impact of IoT data analytics on key performance indicators (KPIs) in semiconductor layout optimization:
KPI | Before IoT Analytics | After IoT Analytics |
---|---|---|
Yield Rate | 85% | 92% |
Design Cycle Time | 12 weeks | 8 weeks |
Power Efficiency | 90% | 95% |
Embracing these emerging technologies not only accelerates the optimization process but also paves the way for more complex and capable semiconductor devices. As the industry continues to evolve, the role of IoT in layout optimization becomes increasingly critical, positioning companies that adopt these strategies at the forefront of innovation.
The Synergy of IoT and Semiconductors in Industrial Automation
The Internet of Things (IoT) is revolutionizing industrial automation by transforming everyday products into interconnected smart devices. This synergy is not only enhancing the capabilities of industrial systems but also driving the demand for advanced semiconductors. As IoT applications proliferate across various sectors, from retail to healthcare, the need for sensors, microcontrollers, and integrated circuits is surging, promising sustained growth for the semiconductor industry.
IoT’s transformative impact on the semiconductor sector is evident in the shift towards manufacturing processes tailored for IoT chips. These chips, essential for the operation of IoT devices, are spurring innovation in semiconductor fabrication. Moreover, the integration of cloud computing, artificial intelligence, and IoT is setting a new benchmark for precision and efficiency in the industry.
The following table illustrates the projected increase in demand for semiconductor components due to IoT proliferation:
Component | 2021 Demand | 2025 Projected Demand |
---|---|---|
Sensors | 1.2 Billion | 3.5 Billion |
Memory | 2.3 Billion | 6.1 Billion |
Microcontrollers | 0.9 Billion | 2.4 Billion |
This anticipated growth underscores the critical role of semiconductors in enabling the vast network of IoT devices, which is set to expand even further in the coming years.
Predictive Maintenance and Yield Enhancement with IoT
The integration of the Internet of Things (IoT) with predictive maintenance strategies is revolutionizing the manufacturing sector. Predictive maintenance, powered by IoT, allows for real-time monitoring and analysis of equipment performance. This proactive approach not only reduces downtime but also extends the lifespan of machinery, leading to significant cost savings and yield enhancement.
Digital twins play a pivotal role in this process. They serve as virtual models that mirror physical assets, providing a platform for simulations that predict equipment failure before it occurs. By combining these twins with IoT sensor data, manufacturers can detect anomalies and schedule maintenance more effectively.
Factor | Impact on Maintenance | Impact on Yield |
---|---|---|
Real-time Monitoring | Reduces downtime | Enhances production continuity |
Anomaly Detection | Prevents unexpected failures | Maintains consistent quality |
Maintenance Scheduling | Optimizes repair tasks | Increases equipment availability |
Ultimately, the synergy of IoT and predictive analytics fosters a data-driven manufacturing environment. This environment is not only adaptive to changes but also capable of making informed decisions that streamline operations and boost productivity.
Optimizing Energy at the System Level in Semiconductor Applications
Machine Learning for Energy Efficiency in Manufacturing
The integration of machine learning tools in the semiconductor manufacturing process marks a significant leap towards energy efficiency. Machine learning algorithms excel in prediction, analysis, and optimization, enabling the industry to set new benchmarks in energy management. These tools engage in data mining activities to identify patterns and trends that inform energy optimization strategies, effectively sifting through redundant data to uncover actionable insights.
Pre-processing of data is a crucial step in this context, as it ensures the quality and relevance of the information fed into machine learning models. By doing so, manufacturers can fine-tune their systems to operate at peak efficiency, reducing waste and lowering energy consumption. The application of these advanced analytical techniques is not just about conserving energy; it’s also about enhancing the overall performance and productivity of the manufacturing process.
The benefits of applying machine learning to energy efficiency in manufacturing are manifold. Here’s a glimpse into the potential improvements:
- Predictive maintenance to anticipate and prevent equipment failures.
- Dynamic adjustment of machine parameters for optimal performance.
- Real-time monitoring and analysis to detect and address quality issues.
- Data-driven decision-making for continuous process improvement.
Hardware Optimization and Power Management
In the realm of semiconductor applications, power management is not just a feature but a fundamental aspect that drives system-level optimization. Hardware optimization encompasses a range of strategies aimed at reducing power consumption while maintaining performance. This includes macro-architecture decisions, micro-architecture tuning, algorithmic adjustments, and software enhancements.
At each stage of design, there are distinct opportunities for power saving:
- Macro-architecture level: Big-ticket tradeoff analysis and selection of dedicated processing elements.
- Micro-architecture level: Optimization of the instruction set and execution units for the target application.
- Algorithmic level: Selection and optimization of algorithms for computational efficiency and memory accesses.
- Software level: Feedback to developers on optimizing software for power and energy, including compiler optimizations and code refactoring.
The future of hardware optimization also considers the accuracy of results as a potential area for improvement. Techniques such as approximate computing, which introduces a tolerable level of imprecision for applications like multimedia processing, can lead to substantial power savings. By leveraging these various levels of optimization, semiconductor-driven systems can achieve a delicate balance between energy consumption and performance.
Low Power-High Performance Solutions for Industrial Systems
In the realm of industrial automation, the quest for low power yet high-performance solutions is more than a trend; it’s a necessity. As industries increasingly rely on advanced semiconductor technologies, the focus has shifted towards sustainable system design. This involves not only optimizing hardware during implementation but also considering the entire lifecycle of energy consumption.
Semiconductor attributes play a pivotal role in this context. They find extensive use in industrial automation, where precise control over power delivery is crucial for optimizing manufacturing processes and ensuring consistent product quality. Advanced, computationally intensive system topologies are being developed for sustainable applications, which paradoxically may increase energy consumption by operating at higher power levels.
To address this, a multi-faceted approach is essential. It includes the following strategies:
- Designing energy-efficient semiconductor architectures that reduce power consumption without compromising performance.
- Implementing smart power management systems that dynamically adjust energy use based on real-time demands.
- Developing low power modes for idle or low-activity periods to minimize energy waste.
These strategies ensure that the semiconductor-driven systems not only meet the robust power handling requirements of today’s industries but also contribute to a more sustainable future.
Performance Optimization in Semiconductor-Driven Systems
Improving Operational Efficiency with Advanced Semiconductor Technologies
The relentless pursuit of operational efficiency in the semiconductor industry has led to significant advancements in both front-end and back-end processes. While previously it was common to make productivity improvements through advances in front-end processes, the focus has now expanded to include back-end processes such as wafer cutting, which are critical for reliability and productivity.
Artificial Intelligence (AI) plays a pivotal role in enhancing operational efficiency. By utilizing AI for data analytics and machine learning, semiconductor companies can optimize their supply chains and logistics, leading to faster time to market and reduced expenses. Moreover, AI facilitates data-driven decision-making, which is essential for innovation in product development within the semiconductor manufacturing sector.
The integration of newer semiconductor technologies, such as insulated gate bipolar transistors (IGBTs) and metal-oxide-semiconductor field-effect transistors (MOSFETs), has also contributed to efficiency gains. These technologies surpass older ones like thyristors in terms of switching speed and power losses, offering higher switching frequencies and lower conduction losses. This results in improved energy efficiency, especially in applications that demand rapid switching, thereby enhancing overall operational efficiency and better coordination across various industrial processes.
Quality Control and Productivity Enhancement
In the realm of semiconductor manufacturing, automation plays a pivotal role in quality control and inspection. Programmable Logic Controllers (PLCs) are at the forefront, controlling sophisticated inspection and testing equipment such as vision systems, leak testers, and coordinate measuring machines. This automation ensures products meet stringent quality standards and adhere to specifications.
Supervisory Control and Data Acquisition (SCADA) systems complement these efforts by collecting and analyzing inspection data. This analysis aids in identifying trends, refining process controls, and minimizing the incidence of defects, thereby enhancing overall productivity.
The integration of Artificial Intelligence (AI) into quality control processes has marked a significant leap forward. AI-powered Quality Control (QC) systems are capable of detecting flaws with greater accuracy, ensuring consistency in the final product. In the fast-paced electronics sector, companies like Foxconn leverage AI to maintain high-quality production at scale. Similarly, smart manufacturing utilizes AI to monitor processes in real-time, allowing for immediate adjustments that maximize efficiency and reduce waste.
Robotic Process Automation (RPA) is another tool that has been adopted by industry leaders such as Whirlpool. RPA aids in maintaining uniformity and accuracy during quality evaluations, streamlining operations, and upholding a high standard of product quality. The future of semiconductor manufacturing automation, shaped by AI and robotics, promises even greater precision and efficiency.
Competitive Edge through High-Speed Semiconductor Switching
The relentless pursuit of efficiency in industrial systems has led to the adoption of advanced semiconductor technologies that offer significant advantages over traditional components. High-speed semiconductor switching is pivotal in achieving a competitive edge, as it directly correlates with the system’s overall performance and responsiveness.
Semiconductor technologies such as IGBTs and MOSFETs have revolutionized the landscape with their ability to operate at higher switching frequencies and with lower conduction losses compared to older technologies like thyristors. This not only enhances energy efficiency but also contributes to the miniaturization of systems, allowing for more compact and integrated solutions.
Technology | Switching Speed | Power Losses | Efficiency Gain |
---|---|---|---|
IGBTs | High | Low | Significant |
MOSFETs | Very High | Very Low | Substantial |
Thyristors | Moderate | Moderate | Moderate |
Despite the emergence of these newer technologies, thyristors still hold their ground in high-power applications where robustness and reliability are crucial. Their cost-effectiveness and suitability for certain use cases ensure that they remain relevant in the industry, complementing the high-speed alternatives where necessary.
Conclusion
In the journey towards industrial excellence, semiconductor-driven automation systems have emerged as pivotal elements in enhancing efficiency and innovation. The integration of advanced semiconductor technologies, such as IGBTs and MOSFETs, has revolutionized the control and optimization of power delivery, leading to significant improvements in manufacturing processes and product quality. The synergy between AI, IoT, and robotics within these systems has not only streamlined operations but also accelerated the path to market for new semiconductor designs. By harnessing the power of data analytics and machine learning, the industry is witnessing a transformation in predictive maintenance, supply chain management, and energy optimization at the system level. As we have explored throughout this article, the impact of semiconductors on industrial automation is profound, offering a competitive edge to those who adeptly integrate these technologies into their operations.
Frequently Asked Questions
How do semiconductors contribute to industrial automation?
Semiconductors find extensive use in industrial automation, where precise control over power delivery is crucial for optimizing manufacturing processes and ensuring consistent product quality. They are integral to devices like Programmable Logic Controllers (PLCs) and Supervisory Control and Data Acquisition (SCADA) systems, which improve overall operational efficiency and coordination between various parts of the industrial process.
What role does AI play in enhancing semiconductor efficiency?
Artificial Intelligence enhances operational efficiency and innovation in the semiconductor industry by optimizing supply chains, logistics, inventory management, and customer service. AI uses data analytics and machine learning to generate insights and recommendations, fostering a culture of innovation and collaboration through knowledge sharing, experimentation, and feedback loops.
In what ways is the IoT transforming the semiconductor industry?
IoT is revolutionizing the semiconductor industry by enabling AI-based analytics that optimize semiconductor layouts, reduce expenses, and increase yields. This transformation demonstrates how IoT and AI support data-driven decision-making and innovation in product development processes within semiconductor manufacturing.
How can energy be optimized at the system level in semiconductor applications?
Energy optimization at the system level involves not just hardware optimization during implementation but also leveraging machine learning for energy efficiency in manufacturing. This approach allows for the identification of component failures, prediction of potential design issues, and proposal of optimal layouts to enhance IC design yield.
What advantages do advanced semiconductor technologies offer in operational efficiency?
Advanced semiconductor technologies like IGBTs and MOSFETs offer higher switching frequencies and lower conduction losses compared to older technologies such as thyristors. This results in improved energy efficiency, especially in applications that require rapid switching, thereby improving operational efficiency in industrial systems.
How do PLC and SCADA systems improve industrial automation?
PLC and SCADA systems are essential components of modern industrial automation. They control, monitor, and optimize various processes in industries such as manufacturing, energy, and water management. By leveraging both PLC and SCADA systems, manufacturers can enhance efficiency, productivity, and quality of operations, gaining a competitive edge in the market.