Optimizing the Semiconductor Manufacturing Process: Best Practices
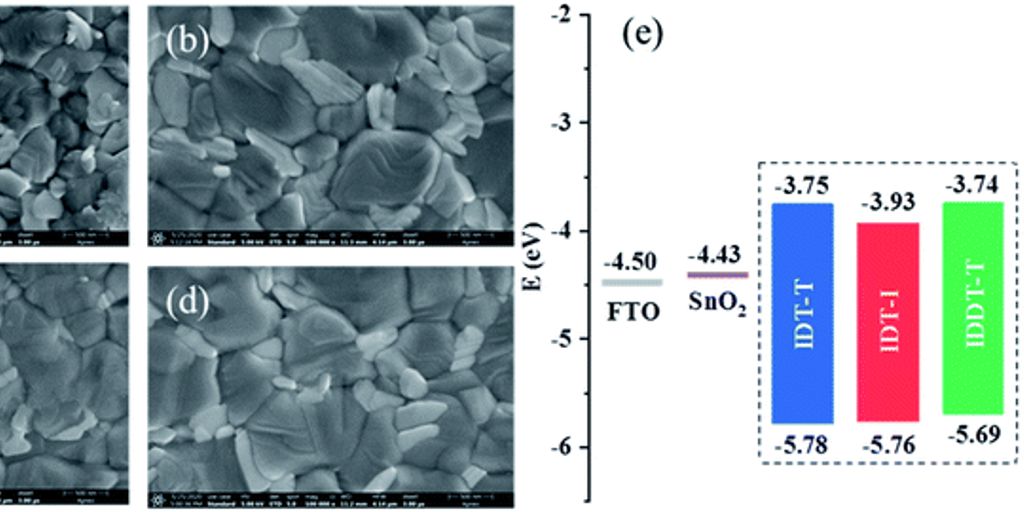
In the ever-evolving world of semiconductor manufacturing, optimizing processes is crucial for maintaining competitive advantage and ensuring high product quality. By designing products with optimized layouts, material choices, and process tolerances, manufacturers can streamline production, minimize yield-limiting issues, and enhance overall efficiency. This article explores best practices and strategies for optimizing semiconductor manufacturing processes, from integrating modern technologies to applying lean principles and proven process improvement techniques.
Key Takeaways
- Integrating AI and digital transformation can significantly enhance semiconductor manufacturing optimization.
- Material selection plays a crucial role in minimizing defects and balancing cost and performance.
- Advanced photolithography techniques and equipment optimization are essential for reducing defects.
- Implementing Statistical Process Control (SPC) helps in monitoring and controlling process variation.
- Leveraging case studies from industry leaders provides valuable insights for successful optimization.
Strategies for Semiconductor Manufacturing Optimization
In the quest for semiconductor manufacturing optimization, several strategies stand out as particularly effective. These include the integration of AI and digital transformation, the application of lean manufacturing principles, and the use of proven process improvement techniques.
Material Selection and Its Impact on Yield
Material selection is a critical factor in semiconductor manufacturing, directly influencing the gross die yield. Various factors influence gross die yield, including material quality, fabrication techniques, and equipment calibration. For instance, photolithography, etching, and deposition process variations can introduce defects that reduce yield. Additionally, the circuit design’s complexity and the precision of the manufacturing equipment play significant roles.
Enhancing Photolithography Processes
Advanced Photolithography Techniques
The precision of photolithography is vital for defining accurate circuit patterns. Emerging semiconductor technologies, like extreme ultraviolet lithography (EUV), are key to creating finer patterns for advanced chips. EUV enables more precise patterning on silicon wafers, which is essential for producing smaller, more complex integrated circuits.
Reducing Photolithography Defects
Optimizing fabrication processes underpins yield improvement efforts. Each aspect is critical, and the precision of photolithography is no exception. By integrating advanced techniques and maintaining stringent process controls, manufacturers can significantly reduce defects. This includes regular equipment calibration and maintenance to ensure accuracy.
Optimizing Photolithography Equipment
Equipment accuracy and maintenance are directly linked to yield. Proper calibration and regular maintenance of photolithography equipment are essential. This ensures that the equipment operates at peak performance, reducing the likelihood of defects and improving overall yield. Key practices include:
- Regular calibration schedules
- Preventive maintenance routines
- Immediate troubleshooting and repairs
By adhering to these practices, manufacturers can maintain high precision in photolithography processes, ultimately enhancing the quality and yield of semiconductor devices.
Implementing Statistical Process Control (SPC)
Monitoring Process Variation
Statistical process control (SPC) methods are key to continuous improvement. By applying statistical techniques to analyze yield data, manufacturers can detect trends and anomalies that may suggest process variances or potential issues before they escalate into larger problems. Leading companies integrate several best practices to maximize gross die yield. Adopting statistical process control (SPC) is critical, allowing firms to monitor process variability and make necessary adjustments in real-time.
Controlling Process Parameters
SPC systems enable end-to-end data analysis and real-time alerts, optimizing microcontroller production. By integrating external data, manufacturers can enhance their real-time anomaly detection and alert systems. This proactive approach ensures consistent quality and helps in maintaining control over process parameters.
Benefits of SPC in Semiconductor Manufacturing
Implementing SPC in semiconductor manufacturing offers numerous benefits:
- Real-time monitoring of process variation using statistical methods.
- Ensuring consistent quality through continuous data analysis.
- Proactively identifying potential process failures and assessing their impact on production quality.
- Driving continuous improvement efforts across the organization’s processes.
By leveraging these benefits, manufacturers can maintain a high standard of quality and efficiency in their production processes.
Design of Experiments (DOE) for Process Optimization
Setting Up Effective Experiments
Design of Experiments (DOE) is a powerful statistical tool used to identify the relationship between factors affecting a process and the output of that process. By systematically varying the input factors, DOE helps in understanding the cause-and-effect relationships. This is crucial for the optimization of a semiconductor manufacturing process. Key steps in setting up effective experiments include:
- Defining the objective of the experiment.
- Selecting the factors and levels to be studied.
- Choosing the appropriate experimental design (e.g., full factorial, fractional factorial).
- Conducting the experiments while maintaining control over external variables.
- Collecting and analyzing the data.
Analyzing Experimental Data
Once the experiments are conducted, the next step is to analyze the data to draw meaningful conclusions. This involves using statistical methods to interpret the results and determine the significance of the factors studied. Techniques such as Analysis of Variance (ANOVA) are commonly used to identify which factors have a significant impact on the process. The insights gained from this analysis can then be used to make informed decisions about process adjustments.
Applying DOE Results to Manufacturing
The ultimate goal of DOE is to apply the findings to improve the manufacturing process. This involves implementing the optimal settings identified during the experiments and continuously monitoring the process to ensure the desired outcomes are achieved. By leveraging DOE, manufacturers can achieve significant improvements in yield, quality, and efficiency, thereby driving overall process optimization and sensitivity.
Failure Mode and Effects Analysis (FMEA)
Failure Mode and Effects Analysis (FMEA) is a prospective reliability management instrument extensively utilized to manage failure modes of systems, products, and processes. This proactive approach ensures that potential issues are identified and mitigated before they can impact production, safety, and efficiency.
Identifying Potential Failures
FMEA helps in anticipating and mitigating potential failure points, making it a robust risk management tool. By systematically analyzing possible failure modes, evaluating their effects, and prioritizing corrective actions, manufacturers can significantly reduce the likelihood of defects and errors.
Assessing Failure Impact
Once potential failures are identified, the next step is to assess their impact. This involves evaluating the severity, occurrence, and detection of each failure mode. By understanding the impact of each failure, manufacturers can prioritize which issues to address first, ensuring that the most critical problems are resolved promptly.
Preventing Failures Through FMEA
Preventing failures is the ultimate goal of FMEA. This is achieved by implementing corrective actions based on the analysis. The process includes:
- Identifying potential failure modes.
- Evaluating the effects of these failures.
- Prioritizing corrective actions.
- Implementing solutions to mitigate risks.
By following these steps, manufacturers can enhance the reliability and efficiency of their processes, leading to higher yield rates and improved product quality.
Leveraging Case Studies for Best Practices
Successful Optimization Case Studies
Case studies provide an up-close and detailed examination of challenges faced within a real-world manufacturing environment along with proven solutions. These real-world examples offer invaluable insights into effective strategies and techniques.
Lessons Learned from Industry Leaders
Industry leaders often share their experiences and lessons learned through various resources such as presentations, blogs, and best practices documents. These resources can be instrumental in understanding the nuances of semiconductor manufacturing optimization.
Applying Case Study Insights to Your Process
To apply insights from case studies to your own processes, consider the following steps:
- Identify relevant case studies that align with your specific challenges.
- Analyze the solutions and strategies implemented in these case studies.
- Adapt and tailor these solutions to fit your unique manufacturing environment.
- Monitor the results and make necessary adjustments to optimize outcomes.
By leveraging the knowledge gained from case studies, manufacturers can enhance their processes and achieve better results.
Conclusion
In conclusion, optimizing the semiconductor manufacturing process is a multifaceted endeavor that requires a strategic blend of modern technologies, lean principles, and proven process improvement techniques. By designing products with optimized layouts, material choices, and process tolerances, manufacturers can streamline production processes and minimize yield-limiting issues. Leveraging AI, digital transformation, and statistical process control, among other strategies, can significantly enhance production efficiency and product quality. As the industry continues to evolve, staying abreast of technological advancements will be crucial for manufacturing managers to capitalize on new opportunities and maintain a competitive edge. Ultimately, the successful implementation of these best practices will lead to maximized production value and sustained growth in the semiconductor sector.
Frequently Asked Questions
How can AI and digital transformation improve semiconductor manufacturing?
AI and digital transformation can streamline production processes, reduce defects, and enhance overall efficiency by providing real-time data analysis and predictive maintenance.
What are the benefits of applying lean manufacturing principles in semiconductor production?
Lean manufacturing principles help in minimizing waste, improving process efficiency, and ensuring better resource utilization, leading to higher yield and reduced costs.
Why is material selection crucial in semiconductor manufacturing?
Choosing the right materials is essential as it affects the device’s functionality, reliability, and defect rates. Proper material selection can significantly enhance yield and performance.
How does Statistical Process Control (SPC) benefit semiconductor manufacturing?
SPC helps in monitoring and controlling process variations, ensuring consistent product quality, and identifying areas for process improvement.
What role does Design of Experiments (DOE) play in process optimization?
DOE helps in systematically planning experiments to understand the effects of various factors on the process, enabling data-driven decisions for process optimization.
What is Failure Mode and Effects Analysis (FMEA) and its importance?
FMEA is a systematic approach to identify potential failures, assess their impact, and implement preventive measures, thereby enhancing the reliability and quality of semiconductor products.