Precision and Challenges: Exploring the World of Wafer Testing
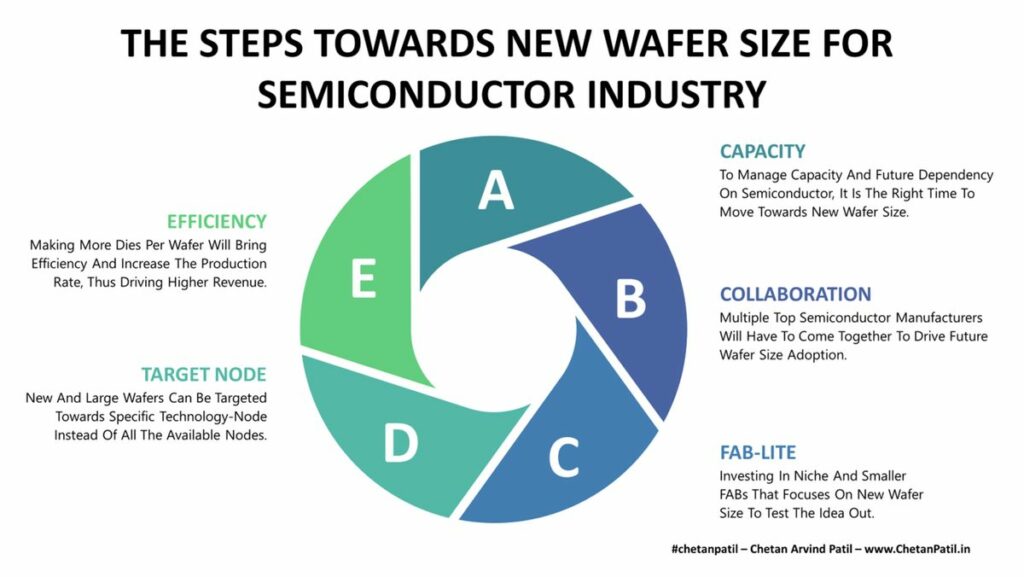
Wafer testing is a critical step in semiconductor manufacturing, ensuring that each chip meets the required standards before being packaged and shipped. This article delves into the intricacies of wafer testing, covering the foundational aspects, technological advancements, and the challenges faced by the industry. We also explore the future trends that are shaping semiconductor testing and the importance of global collaboration in driving innovation in this field.
Key Takeaways
- Automated Test Equipment (ATE) and probe cards play crucial roles in achieving precise and accurate wafer testing, which is essential for high-quality semiconductor production.
- Innovations such as air-floating chuck technology and environment testing in vacuum and temperature-controlled conditions are pushing the boundaries of wafer testing capabilities.
- The semiconductor industry is tackling challenges like chiplet cleaning, the skills crisis, and the need for sustainable manufacturing practices with solutions like AI and advanced cleaning technologies.
- The future of semiconductor testing is being shaped by emerging trends such as quantum processing units, real-time aerosol particle monitoring, and Angstrom Era fabrication techniques.
- Global events and collaborations, like SEMISHARE’s gatherings and SEMICON West, play a pivotal role in sharing knowledge, fostering innovation, and addressing industry-wide challenges in wafer testing.
The Fundamentals of Wafer Testing
Understanding Automated Test Equipment (ATE)
Automated Test Equipment (ATE) is essential for the semiconductor industry, enabling efficient and accurate testing of wafers at high speeds. ATE systems are designed to quickly identify defects and verify the functionality of semiconductor devices before they are packaged and shipped. This process is critical for ensuring the quality and reliability of electronic components that power today’s technology.
ATE integrates various technologies to perform its tasks, including precision instruments that transmit stable signals to the wafer surfaces. The goal is to achieve reliable measurement results that support the rapid attainment of technical objectives. The equipment’s ease of operation and mechanical stability contribute to a low-cost, high-output testing solution, catering to the diverse needs of fabs, packaging, and testing plants.
The following list highlights key components typically found in ATE setups:
- Precision instruments for signal transmission
- Probe cards for making contact with the wafer
- Software for efficient test generation
- Mechanical systems for stable probe-to-wafer contact
By leveraging machine learning and other advanced methodologies, ATE systems can elevate the precision of tests, shortening verification cycles and enhancing the overall quality of semiconductor devices.
The Role of Probe Cards in Precision Testing
Probe cards are critical components in wafer testing, serving as the interface between the test equipment and the semiconductor devices. They ensure that electrical signals are accurately transmitted to and from the wafer’s circuitry for thorough testing of the device’s functionality. The mechanical stability of the probe card is paramount; any misalignment can lead to faulty readings and compromised test results.
The probe holder, a mechanical device, plays a significant role in maintaining the precision of the probe card. It connects the probe to the signal cable and allows for fine adjustments in the X-Y-Z directions, ensuring that the probe makes precise contact with the wafer. This precise contact is essential for the equipment’s ease of operation and mechanical stability, providing a cost-effective and high-output testing solution.
Here is a brief overview of the types of tests performed using probe stations:
- I-V (Current-Voltage) Characterization
- C-V (Capacitance-Voltage) Characterization
- Optical Signal Analysis
- RF (Radio Frequency) Testing
- 1/F Noise Analysis
As the semiconductor industry evolves, the demand for more sophisticated probe card technologies grows, necessitating continuous innovation to meet the diverse testing needs of fabs, packaging, and testing plants.
Mechanical Stability and Its Impact on Test Accuracy
Mechanical stability is a cornerstone of wafer testing, where the slightest deformation can lead to inaccurate results. Maintaining the necessary thickness during high-temperature processing is crucial to prevent such deformations, aligning with the trend towards miniaturization in semiconductor design. This stability not only enhances robustness against variations in the fabrication process but also ensures higher yields and reliability of the final product.
The precision of wafer testing is also heavily reliant on the mechanical stability of the testing equipment. Advanced verification techniques have increased the accuracy and reliability of the process, marking a significant advancement in ensuring circuit design integrity and performance. As we push the boundaries of technology, the role of mechanical stability becomes even more pronounced.
Here are some key points highlighting the importance of mechanical stability in wafer testing:
- It reduces the dependency on extensive simulations.
- Enhances performance and efficiency in equivalence checking processes.
- Addresses critical issues such as electromigration and thermal effects.
- Ensures manufacturability by mitigating variability in fabrication processes.
Innovations in Wafer Testing Technology
Advancements in Signal Transmission and Measurement
The relentless pursuit of precision in wafer testing has led to significant advancements in signal transmission and measurement. Stable signal transmission from precision instruments to wafer surfaces is crucial for achieving accurate and reliable measurement results. This stability is paramount for customers aiming to reach their technical goals swiftly and efficiently.
In the realm of optoelectronics, factors such as anti-vibration, shielding, and stable temperature environments, including vacuum conditions, are vital. They facilitate the electrical-optical and optical-electrical conversion process, which is significant for the development of new optoelectronic devices and the enhancement of existing ones.
Core technologies have evolved to meet the demands of rapidly advancing fields like 5G communications, aerospace, and artificial intelligence. The Hall Effect System exemplifies this evolution, being an integrated software system designed for high-precision measurement of semiconductor materials. The system’s capabilities are a testament to the ongoing innovation in wafer testing technology.
Exploring Vacuum and Temperature Environment Testing
The pursuit of high reliability and performance in semiconductor devices, particularly those used in aerospace applications, has led to the development of specialized vacuum and temperature environment testing technologies. These technologies are crucial for simulating the extreme conditions that devices will encounter in space.
Vacuum high and low temperature environment testing allows for the assessment of a device’s behavior in conditions ranging from ultra-high vacuum to varying temperature extremes. SCG’s series of high and low temperature vacuum probe stations exemplify the innovation in this field, offering automatic control and laser simulation capabilities.
Key features of temperature chucks used in these testing environments include:
- Ability to reach temperatures as low as -10℃ without a cooling machine
- Air-only operation, eliminating the need for liquids or Peltier elements
- Modular systems that can be customized for individual testing requirements
- Compatibility with major production and analytical probes
- Integration of complete hardware and software solutions
These advancements ensure that semiconductor devices can be tested with greater precision, contributing to the overall quality and reliability of aerospace components and other high-performance applications.
The Emergence of Air-Floating Chuck Technology
The advent of air-floating chuck technology marks a significant leap in wafer testing, where precision and minimal contact are paramount. This innovation allows wafers to be held and maneuvered without physical contact, reducing the risk of damage and contamination that can occur with traditional methods.
Key benefits of air-floating chuck technology include:
- Enhanced accuracy in wafer positioning
- Reduced particle contamination
- Improved repeatability of tests
- Minimized mechanical stress on wafers
As the semiconductor industry continues to scale down chip sizes and increase wafer diameters, the demand for non-contact handling systems grows. The air-floating chuck technology addresses this need by providing a stable yet gentle grip on the wafers, ensuring that the integrity of the delicate structures is maintained throughout the testing process.
Challenges and Solutions in Wafer Testing
Addressing the Chiplet Cleaning Challenge
The miniaturization of semiconductor devices has led to the advent of chiplets, which pose unique cleaning challenges due to their intricate designs and susceptibility to contamination. Effective cleaning is critical to ensure the reliability and performance of these multi-die packages.
To tackle this issue, industry leaders are exploring various innovative solutions. Some of the key strategies include:
- Utilizing advanced cleaning fluids that are less abrasive and more environmentally friendly.
- Implementing precision cleaning equipment that can handle the delicate nature of chiplets.
- Developing new protocols for contamination inspection to ensure thorough cleaning.
These efforts are crucial in maintaining the integrity of chiplets and, by extension, the devices they power. As the industry continues to evolve, the cleaning methodologies must adapt to meet the stringent standards required for next-generation semiconductor technologies.
Overcoming the Semiconductor Skills Crisis with AI
The semiconductor industry is witnessing a paradigm shift with the introduction of AI-native circuit representation learning. This innovative approach is revolutionizing talent acquisition by enabling more efficient and effective design optimization processes. AI-driven solutions, particularly in the Electronic Design Automation (EDA) domain, are augmenting existing methodologies, repurposing deep learning models to meet the unique complexities of electronic circuits.
Recent advancements have seen the integration of multimodal learning, which significantly enhances the effectiveness of AI in circuit design. This shift from AI4EDA to AI-native EDA represents a new horizon in semiconductor design, where AI is not just a tool but an integral part of the design process itself. For instance, in the realm of analog sizing, AI is advancing optimization efforts through machine learning as surrogate models and reinforcement learning for direct optimization.
The table below outlines the areas where AI is making an impact in semiconductor design:
AI Application Area | Description |
---|---|
Standard Cells | AI for optimizing the design of standard cells in semiconductor circuits. |
Datapath Circuits | Leveraging AI for enhanced efficiency and performance in datapath circuit design. |
Analog Circuits | Utilizing AI in analog sizing to approximate circuit performance metrics. |
Ensuring Sustainability in Semiconductor Manufacturing
As the semiconductor industry continues to expand, manufacturers have recognized a new imperative to balance increasing demand with the need to decrease energy use and emissions. This shift towards sustainability is not just an environmental concern but also a competitive differentiator in the market.
Key sustainability initiatives include:
- Implementation of energy-efficient technologies
- Reduction of greenhouse gas emissions
- Adoption of sustainable manufacturing practices
- Investment in renewable energy sources
These efforts are crucial for the industry’s long-term viability, as they address both regulatory pressures and consumer expectations for environmentally responsible products. The challenge lies in integrating these sustainable practices without compromising on the high precision and performance standards that semiconductor manufacturing demands.
Future Trends in Semiconductor Testing
The Shift Towards Quantum Processing Units
The semiconductor industry is on the cusp of a transformative shift with the steady advancement of quantum semiconductor research. Quantum computing promises to revolutionize the landscape of high-performance computing by harnessing the peculiar properties of quantum bits, or qubits, to perform operations at speeds unattainable by classical computers.
This shift is not without its challenges, however. The design and fabrication of quantum processing units (QPUs) require precision at an atomic scale, and the integration of these units into existing semiconductor processes is a complex task. Researchers and engineers are exploring quantum architecture design and leveraging large language models (LLMs) to optimize computational efficiency and address these challenges.
The table below outlines some of the recent contributions to quantum semiconductor research:
Reference | Focus Area | Year |
---|---|---|
[181] GPT4AIGChip | AI Accelerator Design | 2023 |
[182] Yan et al. | Compute-in-Memory DNN Accelerators | 2023 |
[183] Liang et al. | Quantum Architecture Design | 2023 |
[184] SpecLLM | VLSI Design Specification | 2024 |
Real-Time Aerosol Particle Monitoring in Fabrication
The semiconductor industry is witnessing a significant transformation with the introduction of real-time aerosol particle monitoring systems in fabrication environments. These advanced systems are crucial for maintaining the purity of air in cleanrooms, where even the smallest particles can lead to defects in wafer production.
NanoAir™ 10 Aerosol Particle Counter represents a leap forward in the Future of Cleanroom Air Filtration. This technology not only detects but also categorizes particles by size, allowing for immediate corrective actions. The table below illustrates the capabilities of such systems:
Particle Size (nm) | Detection Efficiency (%) |
---|---|
>10 | 99.9 |
>20 | 99.99 |
>50 | 99.999 |
Incorporating these systems into the manufacturing process aligns with the industry’s push towards more sophisticated air filtration standards. As we delve into the intricacies of these systems, it becomes clear that they are redefining the standards for cleanroom environments, ensuring the production of high-quality semiconductors.
Angstrom Era Fabrication: Transformational Approaches
The advent of Angstrom Era fabrication marks a pivotal shift in semiconductor testing, where traditional methods are being outpaced by the need for more advanced and precise techniques. This era is characterized by a revolution in design tools, which are not only enhancing design productivity but also redefining the benchmarks of electronic systems’ capabilities. These tools are expected to optimize circuit performance, power, and area (PPA) through significant leaps rather than incremental improvements.
In this transformative landscape, the role of AI-native Large Circuit Models (LCMs) is becoming increasingly prominent. LCMs, which are inherently multimodal, are designed to decode the complex semantics and structures of circuit data. This fosters the development of more resilient, efficient, and inventive design methodologies, potentially leading to a profound ‘shift-left’ in electronic design philosophy.
The table below outlines some of the key innovations and their impact on semiconductor fabrication:
Innovation | Description | Impact |
---|---|---|
Quantum Processing Units | Enhanced computing and sensing capabilities | Redefines performance benchmarks |
Real-Time Aerosol Monitoring | Improved environmental control within process tools | Enhances production process quality |
AI-Native LCMs | Advanced circuit data interpretation and design | Accelerates design productivity |
As we embrace these transformational approaches, the semiconductor industry is poised to overcome current innovation plateaus, ushering in a new epoch of electronic design and testing.
Global Collaboration and Events in Wafer Testing
SEMISHARE’s Global Gatherings for Advanced Solutions
SEMISHARE, recognized as a professional manufacturer of wafer probe stations, has been a prominent figure in the semiconductor industry, focusing on the needs of each customer to maximize their investment returns. The company’s commitment to research and development is evident through its eight distinct R&D systems, ensuring a continuous evolution of wafer testing technologies.
In recent years, SEMISHARE has actively participated in global events to showcase their advanced solutions. For instance, the 2023 CSIF Summit Forum was a grand occasion where SEMISHARE presented their third-generation semiconductor test solutions, drawing attention from nearly a thousand visitors. Moreover, SEMISHARE’s presence at the PSECE 2023 in the Philippines significantly increased their exposure, highlighting their advanced wafer testing solutions to a global audience.
SEMISHARE also extends invitations to industry professionals to join them in various locations such as Chongqing, Munich, and Guangzhou to discuss the future of wafer testing. These gatherings are crucial for fostering collaboration and driving innovation within the semiconductor sector.
SEMICON West: A Hub for Industry Collaboration
SEMICON West stands as a pivotal event where the semiconductor industry converges to celebrate innovation, forge partnerships, and showcase cutting-edge technologies. It’s a YES for Advanced Technology Center! This sentiment echoes the enthusiasm that permeates the event, highlighting the industry’s commitment to progress and collaboration.
The conference features a diverse array of focus areas, each spotlighting a unique facet of semiconductor technology. For instance, the ‘SEMICON WEST FOCUS’ sessions cover topics ranging from ACM RESEARCH to MEMSSTAR, and from PLASMA-THERM to ADVANTEST, reflecting the breadth of expertise and innovation within the industry.
Education and collaboration are the twin pillars that support SEMICON West’s mission to enable innovation. The event not only provides a platform for sharing knowledge but also fosters an environment where industry professionals can connect, discuss challenges, and brainstorm solutions. The following list highlights some of the key focus areas from recent SEMICON West events:
- SEMICON WEST FOCUS: ACCELOVANT
- SEMICON WEST FOCUS: COLLABRATECH SOLUTIONS
- SEMICON WEST FOCUS: DSV INVENTORY MANAGEMENT
- SEMICON WEST FOCUS: NSTAR GLOBAL SERVICES
- SEMICON WEST FOCUS: KITEROCKET
As the industry looks to the future, events like SEMICON West will continue to play a crucial role in driving growth, fostering global collaboration, and sparking innovation.
International Perspectives on Wafer Testing Innovations
The semiconductor industry is a global enterprise, and wafer testing innovations are no exception. Innovation is key to the continuing success of this sector, with seismic shifts in technology promising rich rewards for those who can drive the next generation of semiconductor test solutions. From the strategic importance of chip design to the resilience of the supply chain, international collaboration is critical.
Countries around the world are contributing to the advancements in wafer testing, each bringing unique perspectives and strengths. For instance, the United States is expanding its focus on memory test solutions targeting the NAND Flash/NVM market, while Europe is making strides in metrology with investments in companies like Infinitesima. Asia continues to be a force in layer transfer technology and power management performance.
To encapsulate the global efforts, SEMISHARE invites industry professionals to gather in Chongqing, Munich, and Guangzhou to discuss advanced wafer testing solutions. These gatherings underscore the strategic importance of collaboration and knowledge exchange in driving innovation and addressing the challenges faced by the semiconductor industry.
Conclusion
As we have explored throughout this article, the world of wafer testing is one marked by precision and fraught with challenges. From the deployment of various Automated Test Equipment (ATE) testers to the intricate processes of making contact between probe cards and wafers, the industry continues to innovate to provide cost-effective and high-output solutions. Events like SEMISHARE’s gatherings underscore the collaborative spirit driving the sector forward. The advancements in technologies such as inline X-ray inspection and the development of new optoelectronic devices demonstrate a relentless pursuit of accuracy and reliability. As the semiconductor industry evolves, with sustainability and AI integration becoming increasingly central, wafer testing remains a critical component in ensuring the performance and advancement of electronic devices. The future of wafer testing is not only about maintaining precision at scale but also about embracing the changes that come with technological progress and environmental considerations.
Frequently Asked Questions
What is Automated Test Equipment (ATE) and how does it relate to wafer testing?
Automated Test Equipment (ATE) is a system that automates the process of testing semiconductor wafers for defects or functionality issues. It ensures high precision and efficiency in the testing process, which is critical for the mass production of semiconductors.
How do probe cards contribute to the precision of wafer testing?
Probe cards are essential components of ATE systems. They make precise contact with the semiconductor wafer, allowing electrical tests to be conducted accurately. This precise interfacing is crucial for detecting any defects or issues at the wafer level.
What role does mechanical stability play in the accuracy of wafer tests?
Mechanical stability is vital for maintaining consistent contact between the probe card and the wafer during testing. Any instability can lead to inaccurate test results, making it a critical factor for ensuring the reliability of the testing process.
What recent innovations have been made in wafer testing technology?
Recent innovations include advancements in signal transmission and measurement for more stable and accurate results, vacuum and temperature environment testing for extreme conditions, and air-floating chuck technology to reduce physical contact and potential damage during testing.
What are some challenges faced in wafer testing and how are they being addressed?
Challenges include chiplet cleaning, the semiconductor skills crisis, and sustainability. Solutions involve new cleaning techniques, leveraging AI to enhance process development, and implementing sustainable practices such as advanced wastewater treatment and carbon emission assessments.
How is global collaboration advancing the field of wafer testing?
Global collaboration, through events like SEMICON West and SEMISHARE’s global gatherings, facilitates the exchange of ideas and advancements in wafer testing. This collaboration accelerates innovation and addresses industry-wide challenges, leading to more advanced and efficient testing solutions.