Revolutionizing Manufacturing: The Latest Trends in Industrial Automation Solutions
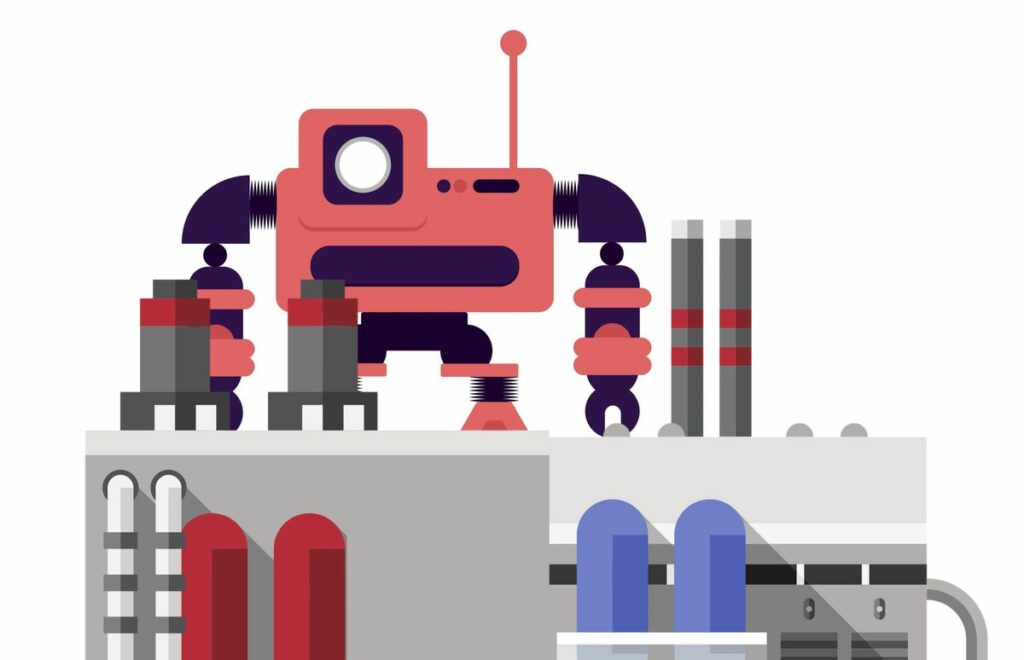
The manufacturing industry is undergoing a transformative phase with the advent of advanced industrial automation solutions. These innovations are not only enhancing efficiency and productivity but are also reshaping the workforce and operational models. This article delves into the latest trends that are revolutionizing the manufacturing landscape, from the rise of collaborative robots to the integration of artificial intelligence and the adoption of the Industrial Internet of Things (IIoT). We explore the cutting-edge advancements in additive manufacturing and the growing emphasis on sustainable practices within automated production environments.
Key Takeaways
- Collaborative robots, or cobots, are becoming integral to smart factories, improving human-robot interaction, safety, and operational flexibility.
- Artificial intelligence is transforming production lines with capabilities such as predictive maintenance, quality control through machine learning, and enhanced real-time decision-making.
- The Industrial Internet of Things (IIoT) is driving connectivity and smart operations, significantly impacting supply chain management while presenting unique challenges and opportunities.
- Additive manufacturing is advancing rapidly, offering new materials and methods for 3D printing, facilitating customization, and impacting supply chain and inventory management.
- Sustainable practices are increasingly important in automated manufacturing, with a focus on energy-efficient technologies, waste reduction, and green automation case studies.
The Rise of Collaborative Robots in Smart Factories
Enhancing Human-Robot Collaboration
The integration of collaborative robots, or cobots, into smart factories marks a significant shift in the manufacturing landscape. Cobots are designed to work alongside human operators, enhancing efficiency and productivity without compromising safety. Unlike traditional robots, cobots are equipped with advanced sensors and control systems that allow for a more intuitive interaction with human workers.
Key benefits of human-robot collaboration include increased flexibility in production processes, reduced ergonomic strain on workers, and the ability to quickly adapt to new tasks. This synergy between humans and robots leverages the strengths of both: the precision and endurance of robots with the cognitive and problem-solving abilities of humans.
To illustrate the effectiveness of cobots in smart manufacturing, consider the following table showing the impact on productivity and safety:
Metric | Before Cobot Integration | After Cobot Integration |
---|---|---|
Production Output | 100 units/hr | 150 units/hr |
Worker Injury Rate | 5 incidents/year | 1 incident/year |
As the title "An Overview of Human-Robot Collaboration in Smart Manufacturing" suggests, the digitalization and adoption of Industry 4.0 technologies are crucial. They not only enhance the sustainability of production sectors but also address the growing need for advanced manufacturing solutions.
Safety and Flexibility in Cobots
The integration of collaborative robots, or cobots, into the manufacturing sector has been a game-changer in terms of safety and flexibility. Cobots are designed to work alongside humans, enhancing the safety of workers by taking over dangerous or repetitive tasks. This not only minimizes the risk of injuries but also allows for a more diverse and adaptable workforce.
Flexibility is another hallmark of cobots. They can be easily reprogrammed and fitted with different tools to perform a variety of tasks. This adaptability makes them ideal for small batch production and customization, which are becoming increasingly important in today’s market. Below is a list of key features that contribute to the safety and flexibility of cobots:
- Ease of programming: Cobots come with user-friendly interfaces that allow for quick reprogramming.
- Sensitive sensors: Equipped with advanced sensors, cobots can detect the presence of humans and adjust their movements to avoid collisions.
- Small footprint: Their compact size allows them to be integrated into existing production lines with minimal disruption.
- Force-limited joints: These joints ensure that cobots exert minimal force, making them safer to interact with.
The implementation of cobots has led to a significant reduction in workplace accidents and has provided manufacturers with the agility to quickly respond to changing market demands.
Case Studies: Cobots in Action
The integration of collaborative robots (cobots) in manufacturing has led to significant improvements in efficiency and quality. One notable example is the implementation of 10 UR cobots at SEAT Components, which has revolutionized their production line. These cobots are instrumental in ensuring ‘just in time’ manufacturing, a method that reduces inventory costs and enhances production flow.
Another case that stands out is the deployment of a Cobot Welder, which has delivered a tenfold increase in production. This leap in productivity demonstrates the transformative potential of cobots when integrated into existing workflows. The table below summarizes the impact of cobots in these scenarios:
Case Study | Cobot Model | Improvement Factor |
---|---|---|
SEAT Components | UR Series | Just in Time Manufacturing |
Cobot Welder | Not Specified | 10x Production Increase |
Integrating Artificial Intelligence in Production Lines
AI for Predictive Maintenance
The integration of Artificial Intelligence (AI) in predictive maintenance is transforming the manufacturing landscape. By leveraging AI algorithms, manufacturers can now anticipate equipment failures before they occur, ensuring uninterrupted production flows. This proactive approach to maintenance is pivotal in reducing downtime and maintenance costs, ultimately leading to increased operational efficiency.
AI-driven predictive maintenance utilizes vast amounts of data collected from sensors and machinery. This data is then analyzed to identify patterns and predict potential breakdowns. For instance, an AI system might analyze the vibration patterns of a motor to detect irregularities that precede a failure. By addressing these issues early, manufacturers can schedule repairs during planned downtime, rather than dealing with unexpected breakdowns.
The benefits of AI in predictive maintenance are quantifiable and significant. Below is a table showcasing the impact of AI-driven maintenance strategies on key performance indicators:
Performance Indicator | Before AI | After AI Implementation |
---|---|---|
Downtime Reduction | 25% | 45% |
Maintenance Cost Savings | 15% | 30% |
Equipment Lifespan Increase | 10% | 20% |
Embracing AI for predictive maintenance not only enhances the longevity of machinery but also fosters a culture of continuous improvement within the manufacturing sector.
Machine Learning for Quality Control
The integration of machine learning (ML) into quality control processes has marked a significant shift in how manufacturers maintain product standards. By leveraging ML algorithms, companies can now predict and detect defects with greater accuracy and speed than traditional methods. This predictive capability not only enhances the efficiency of the production line but also reduces waste and increases customer satisfaction.
One of the key applications of ML in quality control is the classification of products into acceptable and defective categories. For instance, an AI solution for quality control can be framed as a classification problem, where the system learns from historical data to identify patterns and anomalies. The table below illustrates a simplified example of how ML classification can improve defect detection rates over time:
Month | Defect Detection Rate (%) | Improvement (%) |
---|---|---|
Jan | 75 | – |
Feb | 78 | 4 |
Mar | 82 | 5 |
Apr | 85 | 4 |
Continuous learning and adaptation are at the heart of ML, allowing the system to become more accurate as more data is processed. This ongoing improvement is crucial for industries where quality is paramount, and even minor defects can have significant repercussions.
Real-time Data Analysis and Decision Making
The integration of real-time data analysis into production lines has been a game-changer for industrial automation. Manufacturers can now make informed decisions on-the-fly, optimizing operations and reducing downtime. This dynamic approach leverages the latest in sensor technology and data analytics to provide a continuous stream of actionable insights.
Key benefits include:
- Improved product quality through immediate feedback loops
- Enhanced operational efficiency by identifying and resolving issues promptly
- Increased machine utilization by predicting and preventing potential failures
Benefit | Impact on Production |
---|---|
Immediate feedback on quality | Higher consistency and control |
Prompt issue resolution | Reduced downtime and costs |
Predictive failure prevention | Better asset management |
The ability to analyze and act upon data in real time is not without its challenges, however. It requires a robust IT infrastructure and the capacity to handle large volumes of data quickly and securely. Despite these challenges, the advantages for manufacturers who successfully implement these systems are substantial, leading to a significant competitive edge in the market.
Adoption of the Industrial Internet of Things (IIoT)
Connecting Devices for Smart Operations
The integration of the Industrial Internet of Things (IIoT) is transforming manufacturing facilities into smart factories. By connecting devices and machinery, operations become more efficient, data-driven, and adaptable to changes in demand or production conditions.
One of the primary applications of IIoT is in remote operations. Operators can monitor and control equipment from a distance, reducing the need for physical presence on the factory floor. This not only improves safety but also allows for more flexible staffing and maintenance scheduling.
The benefits of a connected device network are numerous, including:
- Real-time monitoring of production processes
- Enhanced predictive maintenance capabilities
- Improved energy management
- Greater supply chain visibility
As IIoT continues to evolve, the potential for innovation in manufacturing operations expands, offering a competitive edge to those who embrace these smart technologies.
IIoT in Supply Chain Management
The integration of the Industrial Internet of Things (IIoT) into supply chain management has been a game-changer for the manufacturing industry. By connecting devices and systems across the entire supply chain, companies are able to gain unprecedented visibility and control over their operations.
Real-time tracking of goods ensures that inventory levels are optimized, reducing waste and improving efficiency. This level of granularity in monitoring allows for a more responsive and agile supply chain, capable of adapting to changes in demand or potential disruptions.
The benefits of IIoT in supply chain management are not just theoretical; they are measurable. Here’s a succinct table showcasing some of the key improvements observed:
Metric | Before IIoT | After IIoT Implementation |
---|---|---|
Inventory Accuracy | 75% | 95% |
Lead Time | 14 Days | 7 Days |
Asset Utilization | 65% | 85% |
However, the adoption of IIoT is not without its challenges. Ensuring data security and managing the complexity of integrating various systems are significant hurdles that companies must overcome. Despite these challenges, the opportunities for efficiency, cost reduction, and enhanced customer satisfaction make IIoT an indispensable part of modern supply chain management.
Challenges and Opportunities in IIoT Implementation
The Industrial Internet of Things (IIoT) represents a transformative shift in manufacturing, offering unprecedented levels of connectivity and data-driven insights. However, the path to fully realizing IIoT’s potential is fraught with challenges that must be navigated carefully.
One of the primary hurdles is ensuring cybersecurity. As factories become more connected, they also become more vulnerable to cyber-attacks. Protecting sensitive data and maintaining uninterrupted operations is paramount. Another significant challenge is interoperability between devices from different manufacturers. Without standardized protocols, the promise of seamless communication remains unfulfilled.
On the flip side, the opportunities are immense. IIoT enables a safer work environment by monitoring conditions in real-time and predicting equipment failures before they happen. It also facilitates optimized resource utilization, reducing waste and improving efficiency. To illustrate, consider the following table summarizing key opportunities:
Opportunity | Description |
---|---|
Safer Work Environment | Real-time monitoring to prevent accidents |
Predictive Maintenance | Anticipating equipment issues to reduce downtime |
Enhanced Productivity | Data analytics for streamlining processes |
Embracing IIoT is not without its challenges, but the benefits it brings to the table can revolutionize the way industries operate. As we look to the future, the integration of IIoT will continue to be a major focus for those seeking to stay competitive in the ever-evolving landscape of industrial automation.
Advancements in Additive Manufacturing
3D Printing Materials and Methods
The landscape of 3D printing materials has expanded significantly, offering a sustainable alternative to traditional manufacturing. Innovations in materials not only allow for a wider range of applications but also enhance the functional properties of printed objects. For instance, the development of advanced polymers, metals, and composites has led to 3D printed parts that can withstand extreme temperatures and mechanical stress.
Methods in 3D printing have also evolved, with techniques such as stereolithography (SLA), fused deposition modeling (FDM), and selective laser sintering (SLS) becoming more refined. Each method has its own set of advantages, influencing the choice based on the desired finish, strength, and precision of the final product. Below is a list of common 3D printing methods and their typical applications:
- SLA: Ideal for smooth surface finishes and intricate details, commonly used in dental and jewelry applications.
- FDM: Widely used for prototyping and hobbyist projects due to its cost-effectiveness and ease of use.
- SLS: Preferred for strong and durable parts, often utilized in aerospace and automotive industries.
The ability to produce parts on-demand and localize manufacturing is a key trend shaping the 3D printing landscape, as highlighted in the report ‘7 Trends Shaping the 3D Printing Landscape in 2024 and Beyond’. This trend not only streamlines the production process but also reduces the need for extensive inventory, leading to cost savings and a reduction in waste.
Customization and Rapid Prototyping
The advent of additive manufacturing has revolutionized the way products are designed and produced. Rapid prototyping, a process that quickly creates physical parts or models using three-dimensional (3D) printing technology, allows for a high degree of customization previously unattainable with traditional manufacturing methods.
With rapid prototyping, businesses can iterate designs swiftly, making adjustments based on real-world testing and feedback. This agility significantly reduces the time and cost associated with product development cycles. Moreover, the ability to produce prototypes on-demand means that companies can respond to market changes with unprecedented speed, offering tailored solutions to their customers.
The following table illustrates the comparative advantages of rapid prototyping over traditional manufacturing in key areas:
Aspect | Traditional Manufacturing | Rapid Prototyping |
---|---|---|
Time to Market | Weeks to months | Days to weeks |
Customization Level | Low to moderate | High |
Cost of Alterations | High | Low to moderate |
Production Volume | High | Low to medium |
Embracing rapid prototyping not only enhances the product development process but also fosters innovation by allowing designers and engineers to experiment without prohibitive costs or time constraints.
Impact on Supply Chain and Inventory Management
Additive manufacturing, commonly known as 3D printing, is revolutionizing supply chain dynamics and inventory management. By enabling on-demand production, companies can reduce the need for large inventories, cutting down on storage costs and minimizing waste from unsold products.
The ability to rapidly prototype and produce parts locally accelerates the supply chain, allowing for quicker response times to market changes and customer needs. This shift towards a more agile and responsive supply chain model is a significant advantage in today’s fast-paced market.
The following table illustrates the contrast between traditional and additive manufacturing in terms of inventory management:
Aspect | Traditional Manufacturing | Additive Manufacturing |
---|---|---|
Inventory Levels | High | Low |
Production Lead Time | Longer | Shorter |
Customization | Limited | High |
Storage Costs | Higher | Lower |
Adopting additive manufacturing also means a transformation in how companies approach inventory management, moving from a ‘just-in-case’ to a ‘just-in-time’ strategy. This change not only reduces overheads but also enhances the ability to customize products, which is increasingly important for customer satisfaction.
Sustainable Practices in Automated Manufacturing
Energy-Efficient Technologies
The integration of energy-efficient technologies in automated manufacturing is not just a trend; it’s a necessity for sustainable growth. By leveraging automation, manufacturers are able to optimize energy use, leading to significant reductions in power consumption and operational costs.
Key technologies include advanced motors and drives, smart sensors, and energy management software. These innovations allow for precise control and monitoring of energy usage across various stages of production. For instance, smart sensors can detect when machines are idle and automatically power them down, while energy management systems provide insights into energy consumption patterns, enabling further optimization.
- Advanced motors and drives: Improved efficiency and reduced energy waste
- Smart sensors: Real-time monitoring and idle machine detection
- Energy management software: Analytics for optimizing energy usage
Embracing these technologies not only contributes to a lower carbon footprint but also aligns with global efforts to combat climate change. Manufacturers who adopt such practices are often seen as industry leaders, setting benchmarks for others to follow.
Waste Reduction Strategies
In the realm of industrial automation, waste reduction is not just an environmental concern but also a significant economic driver. By leveraging advanced technologies, manufacturers are able to minimize waste output, leading to cost savings and improved sustainability.
Key strategies include:
- Precision manufacturing: Automation allows for more accurate production, reducing overruns and material waste.
- Process optimization: Data analytics can identify inefficiencies in production processes that lead to waste.
- Resource recovery: Automated systems can sort and recycle materials that would otherwise be discarded.
These strategies are supported by a range of technologies, from sensors that detect material inconsistencies to software that optimizes cutting patterns. The table below highlights the impact of waste reduction strategies on both the environment and the bottom line:
Strategy | Environmental Impact | Economic Benefit |
---|---|---|
Precision Manufacturing | Reduced resource depletion | Lower material costs |
Process Optimization | Less energy and water waste | Increased production efficiency |
Resource Recovery | Decreased landfill use | Revenue from recycled materials |
Case Studies: Green Automation
The pursuit of sustainability in automated manufacturing has led to the implementation of various innovative practices. Companies are increasingly integrating green automation technologies to reduce their environmental footprint while maintaining efficiency.
One notable example is the use of energy-efficient robots that consume less power and are designed with recyclable materials. These robots not only contribute to energy conservation but also minimize waste during their lifecycle.
Another significant development is the optimization of manufacturing processes to reduce emissions. Advanced software solutions enable factories to monitor and adjust operations in real-time, leading to a substantial decrease in energy consumption and greenhouse gas emissions.
The following table showcases a selection of enterprises that have successfully implemented green automation, highlighting the key benefits they have achieved:
Company | Technology Used | Energy Savings | Waste Reduction |
---|---|---|---|
EcoRobo Inc. | Energy-efficient robots | 25% | 15% |
GreenTech Solutions | Process optimization software | 30% | 20% |
SustainaBuild Co. | Recyclable material robots | – | 30% |
These case studies serve as a testament to the potential of green automation in revolutionizing manufacturing practices. They offer valuable insights and can inspire enterprises to embark on their own intelligent automation initiatives.
Conclusion
The landscape of manufacturing is undergoing a seismic shift as industrial automation solutions continue to evolve at a rapid pace. From the integration of AI and machine learning to the adoption of collaborative robots and the Internet of Things (IoT), these trends are not only revolutionizing production processes but also paving the way for unprecedented levels of efficiency, safety, and customization. As we have explored, the synergy between human ingenuity and robotic precision is creating a new era of manufacturing that promises to meet the growing demands of a dynamic global market. While challenges such as cybersecurity and workforce adaptation remain, the potential benefits of these advanced technologies are clear. Companies that embrace these innovations are set to lead the charge in a highly competitive landscape, ensuring that the future of manufacturing is as bright as it is automated.
Frequently Asked Questions
What are collaborative robots (cobots) and how are they changing manufacturing?
Collaborative robots, or cobots, are designed to work alongside human workers, enhancing collaboration and productivity. They are equipped with sensors and safety features that allow them to operate in close proximity to humans without safety cages. Cobots are revolutionizing manufacturing by making automation more flexible and accessible.
How is artificial intelligence utilized in modern production lines?
Artificial intelligence (AI) is being integrated into production lines to improve efficiency and reduce downtime. For example, AI algorithms are used for predictive maintenance to anticipate equipment failures before they occur, and machine learning models are employed for quality control to detect defects and anomalies in products.
What is the Industrial Internet of Things (IIoT) and its role in manufacturing?
The Industrial Internet of Things (IIoT) refers to the network of interconnected devices and machinery in a manufacturing environment. IIoT enables smart operations by collecting and analyzing data from various sources, leading to improved efficiency, predictive maintenance, and better supply chain management.
What are the latest advancements in additive manufacturing?
Additive manufacturing, commonly known as 3D printing, has seen significant advancements in materials, methods, and applications. These include the development of new printing materials, more precise and faster printing techniques, and the use of 3D printing for rapid prototyping and on-demand production, impacting supply chain and inventory management.
How are automated manufacturing processes becoming more sustainable?
Automated manufacturing is adopting more sustainable practices through the implementation of energy-efficient technologies, the reduction of waste, and the optimization of resource usage. This includes the use of renewable energy sources, recycling materials, and designing processes that minimize environmental impact.
Can you provide examples of how cobots and green automation are being used in industry?
Cobots are being used in various industries for tasks such as assembly, packaging, and inspection, often resulting in higher productivity and improved worker safety. Green automation examples include companies utilizing energy-efficient robots, implementing waste reduction programs, and using sustainable materials in their manufacturing processes.