Silicon Wafer Technology: The Foundation of Electronics
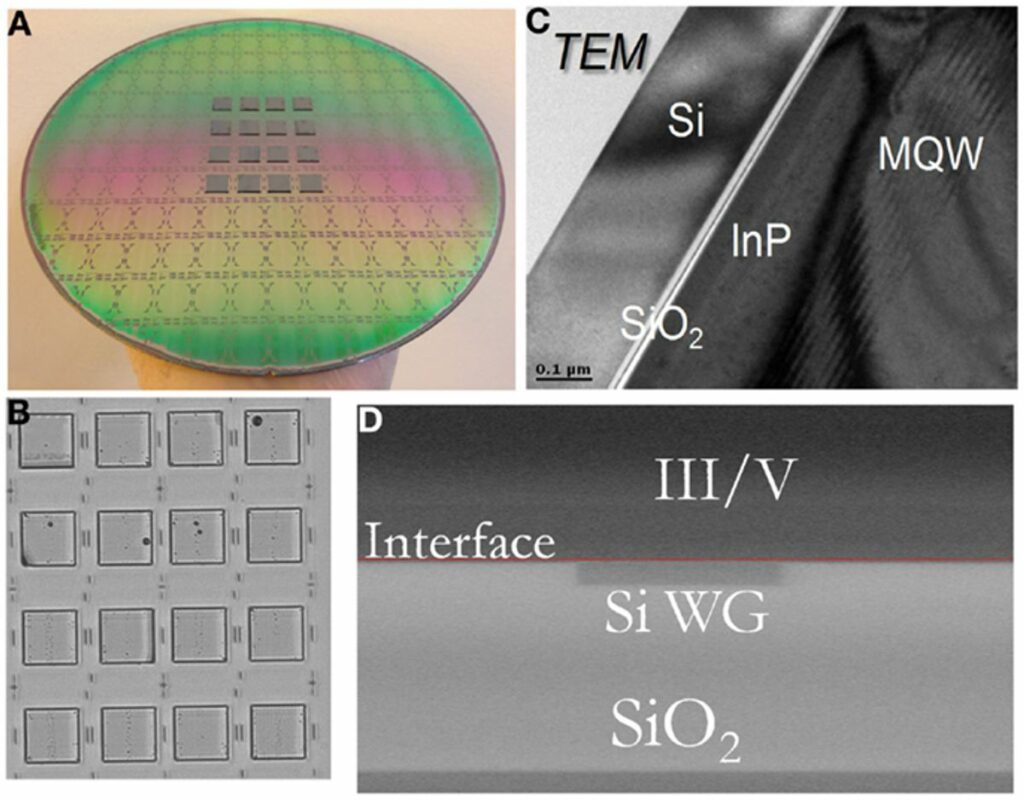
Silicon wafer technology is a cornerstone of the electronics industry, providing the platform for the intricate electronic circuits that power our modern world. From the production of hyperpure silicon to the precision of photolithography, this technology has evolved to meet the demands of an ever-growing array of applications across various industries. As we explore the evolution, applications, specialized products, and market dynamics of silicon wafer technology, we unveil the foundational role it plays in shaping the future of electronics.
Key Takeaways
- Silicon wafer technology has undergone significant evolution, with hyperpure silicon and advanced fabrication techniques enabling the miniaturization of electronic components.
- Silicon wafers are integral to a multitude of industries, including consumer electronics, automotive, and healthcare, revolutionizing products and services within these sectors.
- The market offers specialized silicon wafer products such as polished and epitaxial wafers, tailored to various applications and the development of integrated components.
- Photolithography is an essential process in wafer patterning, utilizing photoresist materials, masks, and etching to create precise circuitry on silicon substrates.
- The semiconductor silicon wafer market is experiencing growth, with a projected value of USD 16.83 billion by 2030, driven by digitalization, IoT, and the automotive industry’s evolution.
The Evolution of Silicon Wafer Technology
The Rise of Hyperpure Silicon
The quest for hyperpure silicon has been a pivotal chapter in the evolution of semiconductor technology. This material serves as the cornerstone for the vast majority of semiconductor devices, underpinning the global electronics industry. The transition to hyperpure silicon has enabled the production of highly integrated microprocessors and memory components, essential for the miniaturization of electronic devices.
Hyperpure silicon wafers come in various diameters, material properties, and surface qualities, catering to the diverse needs of the semiconductor industry. The meticulous process of refining silicon to achieve hyperpurity has been instrumental in advancing the capabilities of electronic components, allowing for more complex and compact structures.
The market for semiconductor silicon wafers has seen substantial growth, with projections indicating a rise from USD 12.2 billion in 2022 to USD 16.83 billion by 2030. This growth trajectory is supported by a steady Compound Annual Growth Rate (CAGR) of 4.11% from 2023 to 2030:
Year | Market Value (USD billion) | CAGR (%) |
---|---|---|
2022 | 12.2 | – |
2023 | – | 4.11 |
2030 | 16.83 | – |
The semiconductor industry’s reliance on hyperpure silicon wafers is a testament to their critical role in the ongoing advancement of electronics, driving innovation across various applications from consumer gadgets to automotive and healthcare technologies.
Advancements in Fabrication Techniques
The relentless pursuit of enhanced performance and efficiency in semiconductor devices has been the driving force behind significant advancements in fabrication technologies. These technologies serve as the canvas for the fabrication of integrated circuits (ICs) and microelectronic devices, pushing the boundaries of wafer manufacturing to new heights of precision and uniformity.
Fabrication is a complex and precise process, involving a series of steps that transform a bare silicon wafer into a bustling landscape of transistors and interconnects. The environment within a semiconductor fab facility is meticulously controlled, with clean rooms designed to eliminate dust and vibrations, and to maintain temperature and humidity within strict limits.
Key fabrication techniques include:
- Deposition processes such as chemical vapor deposition (CVD) and physical vapor deposition (PVD), which add thin layers of materials to the wafer.
- Etching methods to remove unwanted materials, shaping the intricate circuitry of semiconductor devices.
- The use of various metrology tools for the essential inspection and measurement of features on the wafer.
The Impact of Miniaturization on Wafer Design
The relentless pursuit of miniaturization in electronics has had a profound impact on silicon wafer design. As devices shrink, the demand for wafers with extremely fine features increases, necessitating the creation of intricate circuitry. This has led to the development of advanced fabrication techniques, such as chemical vapor deposition (CVD) and physical vapor deposition (PVD), which allow for the addition of thin material layers with high precision.
The quality of the wafer is paramount; any irregularities can significantly impact the performance of the semiconductor devices they are used to produce. The market for semiconductor silicon wafers is foundational to modern electronics, serving as the substrate for integrated circuits (ICs) and microelectronic devices. The drive for miniaturization has pushed the boundaries of wafer manufacturing, enhancing the performance and efficiency of semiconductor devices.
Despite the potential for growth, the industry faces challenges, including the complexities and costs associated with manufacturing processes. However, with strategic collaborations and technological innovations, the sector continues to advance, striving to deliver perfect wafers that meet the sophisticated demands of the dynamic semiconductor industry.
Silicon Wafer Applications Across Industries
Consumer Electronics: The Heart of Modern Gadgets
Silicon wafers are indispensable in the realm of consumer electronics, providing the essential platform for the microprocessors, memory chips, and sensors that power our everyday devices. From the smartphones in our pockets to the laptops on our desks and the smart appliances in our homes, these wafers are the unsung heroes behind the scenes. Their role is pivotal in enabling the creation of more powerful and energy-efficient computer chips, which are integral to the cutting-edge power semiconductors that drive innovation in this sector.
The semiconductor silicon wafer market is vast, reflecting the critical importance of these components in a multitude of devices. Here’s a glimpse into the variety of gadgets that rely on silicon wafer technology:
- Smartphones
- Laptops
- Tablets
- Wearable technology
- Smart home devices
- Gaming consoles
As the digital era progresses, the demand for advanced semiconductor devices continues to surge, supported by the rapid digitization and the expanding Internet of Things (IoT) ecosystem. The relentless pursuit of miniaturization and performance enhancement ensures that silicon wafers remain at the forefront of consumer electronics development.
Automotive Innovations: Driving the Future
The automotive industry is undergoing a transformative shift with the integration of advanced semiconductor devices. These devices are crucial for the functionality of electric vehicles (EVs) and the development of autonomous driving technologies. Semiconductors enable the analysis of engine temperature and pressure sensor data, which is essential for optimizing fuel injection and combustion efficiency.
The demand for semiconductor silicon wafers in the automotive sector is driven by the need for power electronics and sensor applications. As vehicles become more connected and electrified, the reliance on high-quality silicon wafers increases. Siltronic, a key player in the industry, is committed to maintaining its technology leadership by delivering perfect wafers that meet the sophisticated demands of this dynamic sector.
Market projections indicate a significant growth potential for silicon wafer technology in the automotive industry. The table below summarizes the expected market valuation for semiconductor devices in the automotive sector:
Year | Market Valuation (USD Billion) |
---|---|
2025 | 45.6 |
2030 | 65.8 |
2035 | 89.4 |
Continuous innovation and cost reduction programs are essential for companies like Siltronic to grow and compete effectively in this evolving market. The company’s dedication to safe working conditions and environmental protection aligns with the industry’s move towards sustainable and responsible manufacturing practices.
Healthcare Breakthroughs: Silicon in Medicine
The integration of silicon wafers into the healthcare industry has marked a significant advancement in medical technology. Silicon wafers are crucial in developing medical imaging devices, implantable sensors, and diagnostic equipment, which have transformed patient care and medical diagnostics. These wafers enable the creation of highly sensitive and precise instruments that are essential for modern medicine.
Silicon’s role in healthcare extends beyond just equipment. It is the material of choice for the semiconductor components found in complex medical devices. As the demand for more compact and integrated medical devices grows, the use of hyperpure silicon wafers becomes increasingly important. They are at the heart of microprocessors and memory components that process vast amounts of information, critical for patient monitoring and treatment.
The following table illustrates some of the key applications of silicon wafers in the medical field:
Application Area | Description |
---|---|
Medical Imaging | Used in MRI, CT scans, and other imaging technologies. |
Implantable Devices | Components for pacemakers, cochlear implants, and biosensors. |
Diagnostic Equipment | Essential for blood analysis machines and other diagnostic tools. |
Silicon Wafer Products and Their Specializations
Polished Wafers: Versatility in Applications
Polished wafers are a testament to the precision and adaptability of modern semiconductor technology. With their perfect surfaces, they serve as the foundation for a multitude of applications across the electronics industry. These wafers are produced with hyperpure silicon, ensuring the highest quality for semiconductor elements.
The versatility of polished wafers is evident in their wide range of diameters, material properties, and surface qualities. This diversity meets the specific requirements of various electronic devices, from the simplest to the most complex. The production process of polished wafers adheres to the latest design rules, reflecting the industry’s aspirations for innovation and technological leadership.
In addition to their traditional use in consumer electronics, polished wafers are increasingly finding applications in sectors such as healthcare. They are crucial in the development of medical imaging devices, implantable sensors, and diagnostic tools, thereby revolutionizing patient care and medical diagnostics.
Epitaxial Wafers: The Foundation for Integrated Components
Epitaxial wafers represent a pinnacle in the evolution of silicon wafer technology, where a precise crystalline layer is grown on top of the wafer surface. This process enhances the electrical properties of the wafer, making it an ideal substrate for highly integrated components. The epitaxial layer is meticulously engineered to have specific electrical characteristics that complement the underlying wafer, thereby optimizing the performance of the final semiconductor device.
The fabrication of epitaxial wafers involves sophisticated techniques such as chemical vapor deposition (CVD), which allows for the precise control of layer thickness and dopant levels. This level of control is crucial for the production of advanced integrated circuits (ICs) that power today’s technology.
Property | Advantage |
---|---|
Purity | High-quality semiconductor devices |
Layer Uniformity | Consistent electrical properties |
Customization | Tailored to specific applications |
The epitaxial wafer’s role in the semiconductor industry is underscored by its presence in a wide array of applications, from consumer electronics to automotive and healthcare devices. As the demand for more powerful and efficient electronics grows, the importance of epitaxial wafers in meeting these technological demands continues to rise.
Special Products: Pioneering New Technologies
In the realm of silicon wafer technology, special products stand at the forefront of innovation, catering to the ever-evolving needs of the semiconductor industry. These specialized wafers are designed to meet the unique requirements of cutting-edge applications, often involving complex manufacturing processes and advanced materials.
Siltronic, a key player in the market, is renowned for its Advanced Production Technologies and has a rich history of innovation, underscored by a portfolio of over 1,870 patents. Their commitment to quality and continuous improvement is evident in their specialized products, which are integral to the success of the top semiconductor companies.
The following table highlights the top 5 silicon wafer manufacturing companies projected for 2024, showcasing their prominence in the industry:
Rank | Company | Specialization |
---|---|---|
1 | WaferPro | Advanced Production Technologies |
2 | Siltronic | Single-crystal growth, wafer slicing |
3 | Company C | Customized wafer solutions |
4 | Company D | High-purity wafer manufacturing |
5 | Company E | Innovative wafer design and materials |
These companies, through a process-based approach and close collaboration with industry leaders, are shaping the future of technology by delivering specialized wafers that push the boundaries of what’s possible.
Photolithography: The Art of Silicon Wafer Patterning
The Role of Photoresist in Circuitry
In the intricate dance of semiconductor fabrication, photoresist plays a pivotal role. This photosensitive material is meticulously applied to the silicon wafer, forming a thin layer ready to capture the complexities of electronic circuitry. Upon exposure to light through a carefully designed mask, the photoresist undergoes a transformation, with select areas becoming soluble to developers. The subsequent etching process removes these areas, leaving behind a raised pattern that serves as a blueprint for the device’s architecture.
The application of photoresist is a nuanced process, involving a series of steps to ensure precision and uniformity. The sequence begins with the preparation of the wafer’s surface, followed by the deposition of the photoresist, and culminates in the exposure and development stages. Each step is critical, as the quality of the photoresist and its application directly influence the fidelity of pattern transfer and, ultimately, the performance of the semiconductor device.
The table below outlines the key steps in the photoresist application process:
Step | Description |
---|---|
1. Surface Preparation | Cleaning and priming the wafer for photoresist adherence. |
2. Photoresist Deposition | Applying a uniform layer of photoresist onto the wafer. |
3. Soft Bake | Pre-exposure heating to remove solvents and improve adhesion. |
4. Mask Alignment and Exposure | Aligning the mask and exposing the photoresist to light. |
5. Development | Developing the pattern by dissolving exposed or unexposed areas. |
6. Hard Bake | Post-development heating to harden the photoresist pattern. |
7. Etching | Removing the unprotected areas of the wafer to create the circuitry. |
8. Photoresist Removal | Stripping away the remaining photoresist after etching. |
Masking and Etching: Defining Features
The masking and etching processes are pivotal in the photolithography sequence, shaping the intricate designs that form the backbone of semiconductor devices. Initially, a mask is aligned and placed over the silicon wafer, which has been coated with a photosensitive material, or photoresist. This mask defines the areas that will either be exposed or protected from light during the exposure step.
Following exposure, the wafer undergoes the etching process. Here, the exposed or unexposed areas of the photoresist are selectively removed, depending on the type of photoresist used. The underlying silicon is then etched, using techniques such as chemical vapor deposition (CVD) or physical vapor deposition (PVD), to create the desired features on the wafer. This meticulous process enables the creation of transistors, interconnects, and other critical elements of a semiconductor device.
- Key Steps in Masking and Etching:
- Alignment of the mask with the silicon wafer
- Exposure of the wafer to light through the mask
- Development of the photoresist to reveal the pattern
- Etching of the silicon to form the circuit features
The precision of these steps is paramount, as they define the functionality and efficiency of the final electronic components. Semiconductor fabrication facilities, or fabs, maintain highly controlled clean room environments to ensure the integrity of these processes.
The Precision of Pattern Transfer
The culmination of the photolithography process is the precision of pattern transfer, which is fundamental to the semiconductor industry. This meticulous process involves transferring the intricate designs from the photomask to the silicon wafer with exacting accuracy. The success of this step is critical as it defines the functionality and efficiency of the final semiconductor device.
The pattern transfer is achieved through a series of well-orchestrated steps, including the application of photoresist, exposure to light, development, and etching. Each step must be executed flawlessly to ensure the integrity of the microscopic features that form the complex circuitry of electronic components. The following list outlines the key stages in the pattern transfer process:
- Application of a uniform layer of photoresist
- Alignment and exposure to a patterned light source
- Development of the exposed photoresist
- Etching to remove unprotected areas
- Inspection and quality control
Advancements in photolithography equipment and techniques continue to push the boundaries of what is possible, enabling the creation of ever-smaller and more complex devices. As the industry strives for greater miniaturization and performance, the role of precision in pattern transfer remains at the forefront of semiconductor fabrication.
Market Dynamics and Future Projections
Current Market Valuation and Growth Potential
The Silicon Wafers Market size was valued at USD 18.91 Bn in 2023 and is projected to reach USD 29.38 Bn by 2030, growing at a CAGR of 9.72% from 2024-2030. This robust growth trajectory underscores the market’s significant expansion potential and the increasing reliance on silicon wafers across various industries.
In comparison, the Semiconductor Silicon Wafer Market was valued at a lower USD 12.2 billion in 2022, with expectations to grow to USD 16.83 billion by 2030, at a CAGR of 4.11%. The difference in growth rates between these markets highlights the diverse dynamics and potential within the semiconductor sector.
Year | Silicon Wafers Market (USD Bn) | Semiconductor Silicon Wafer Market (USD Bn) |
---|---|---|
2022 | – | 12.2 |
2023 | 18.91 | – |
2030 | 29.38 | 16.83 |
The data suggests a vibrant future for the industry, with strategic planning and risk management being crucial for navigating the evolving landscape effectively.
Drivers of Demand in the Semiconductor Industry
The semiconductor industry is experiencing a surge in demand, driven by several key factors. Technological advancements and continued innovation are at the forefront, pushing the boundaries of what’s possible in electronics. The relentless pursuit of miniaturization and performance enhancement has led to an ever-increasing need for advanced semiconductor devices.
The market dynamics are also influenced by the growing demand for electronic equipment across various sectors. This is particularly evident in the burgeoning IoT ecosystem and the rapid adoption of 5G technology, which are creating new opportunities for semiconductor applications. Additionally, the automotive sector is undergoing a transformation with the advent of electric vehicles (EVs) and autonomous driving technologies, further fueling the demand for power electronics and sensor applications.
Here’s a snapshot of the market’s growth potential:
Year | Market Value (USD Billion) | CAGR (%) |
---|---|---|
2022 | 12.2 | – |
2030 | 16.83 | 4.11 |
As we look at the regional landscape, North America continues to lead, thanks to its robust semiconductor manufacturing capabilities and technological prowess. The Asia-Pacific region, especially China, Japan, and South Korea, is witnessing significant growth due to the escalating demand for consumer electronics and the expansion of automotive and industrial sectors. Europe’s contribution, with Germany and France at the helm, is notable in semiconductor production and innovation. However, the industry must navigate through geopolitical tensions and trade disputes that pose challenges to growth in certain regions.
Challenges and Opportunities Ahead
The semiconductor silicon wafer market is poised at a critical juncture where challenges and opportunities coexist. Global supply chain disruptions have emerged as a significant hurdle, underscoring the need for robust risk management and strategic planning. The complexities and high costs associated with silicon wafer manufacturing processes further accentuate the challenges faced by the industry.
However, amidst these challenges lie unprecedented growth opportunities. Stakeholders are encouraged to pursue strategic collaborations and technological innovations. Proactive research and development efforts are essential to harness these opportunities and maintain a competitive edge. The market dynamics suggest that with careful navigation, the potential for expansion and success in the US Silicon Wafer Manufacturing Market remains substantial.
- Global Supply Chain Disruptions: A critical challenge affecting market stability.
- Strategic Collaborations: A pathway to overcoming industry hurdles.
- Technological Innovations: Key to unlocking growth prospects.
- Proactive R&D: Essential for long-term competitiveness.
Conclusion
In summary, the semiconductor silicon wafer market is an indispensable pillar of the global electronics industry, providing the foundational substrate for a multitude of advanced electronic devices. The market’s growth, driven by relentless innovation and escalating demand across various sectors, underscores the critical role of silicon wafers in enabling the digital age. From consumer electronics to healthcare, and from automotive to telecommunications, the influence of silicon wafer technology is pervasive. As we look towards a future marked by further technological breakthroughs and integration, the importance of silicon wafers is only set to increase, ensuring their position as the bedrock upon which the electronics revolution continues to build.
Frequently Asked Questions
What is the role of silicon wafers in modern electronics?
Silicon wafers are the substrate for integrated circuits (ICs) and microelectronic devices, forming the canvas for the fabrication of complex electronic circuits that are fundamental to modern electronics.
How have fabrication techniques for silicon wafers evolved?
Fabrication techniques have seen significant advancements, including the production of hyperpure silicon and the development of compact structures, allowing for increasingly integrated and sophisticated semiconductor components.
In which industries are silicon wafers applied?
Silicon wafers are used across various industries, including consumer electronics, telecommunications, automotive, and healthcare, for the production of microprocessors, memory chips, sensors, and medical imaging devices.
What are epitaxial wafers, and why are they important?
Epitaxial wafers are specialized silicon wafers with an additional layer of single-crystal silicon, providing a superior basis for highly integrated components and enabling the creation of complex semiconductor devices.
How does photolithography contribute to silicon wafer technology?
Photolithography is a pivotal process in semiconductor fabrication where patterns are transferred onto silicon wafers using a photoresist and a mask, allowing for the precise definition of features and intricate circuitry.
What are the market projections for the semiconductor silicon wafer industry?
The semiconductor silicon wafer market is expected to grow from USD 12.2 billion in 2022 to USD 16.83 billion by 2030, with a CAGR of 4.11% from 2023 to 2030, driven by demand in digitization, IoT, 5G technology, and the automotive sector.