The Art and Science of Wafer Fabrication: From Silicon to Circuits
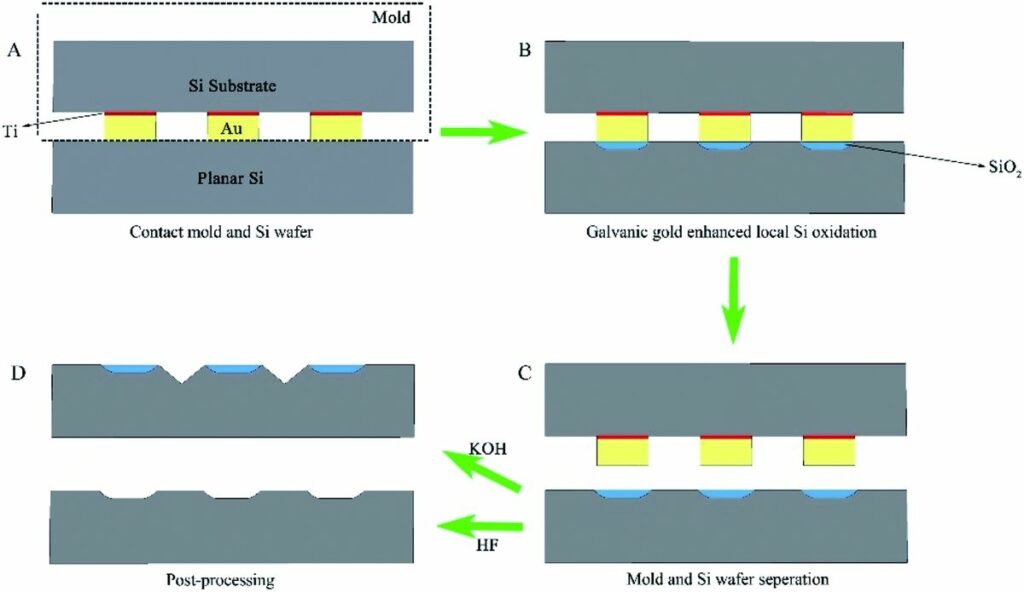
The journey of transforming pure silicon into complex integrated circuits is an intricate blend of art and science. Wafer fabrication is the foundational process in semiconductor manufacturing, where the interplay of materials science, chemistry, and physics comes to life. This article delves into the sophisticated world of wafer fabrication, exploring the fundamental techniques, recent advancements, and emerging trends that are shaping the future of electronics.
Key Takeaways
- Wafer fabrication is a complex process that begins with the creation of silicon wafers and involves various techniques like photolithography, etching, and doping to construct intricate circuits.
- Advancements in wafer inspection and metrology, including defect detection and process control, are crucial for maintaining the high quality and reliability of semiconductor devices.
- Interconnect technologies have evolved from traditional wirebonding to sophisticated 3D integration, impacting the performance and functionality of integrated circuits.
- Optimizing the performance of semiconductors involves addressing challenges in power consumption, noise reduction, and computing capabilities, with techniques like in-memory computing gaining traction.
- Emerging trends such as silicon photonics, advancements in lithography, and the miniaturization of devices through MEMS are driving the semiconductor industry towards new frontiers.
The Fundamentals of Wafer Fabrication
Materials and Silicon Wafer Creation
The journey of a silicon wafer begins with the meticulous selection of materials, primarily high-purity silicon. This elemental silicon is first transformed into a polycrystalline form, which is then subjected to a purification process to achieve the semiconductor-grade quality required for wafer fabrication.
Following the purification process, the next step in silicon wafer production is creating a silicon cylinder, known as a silicon ingot. The Czochralski method is a widely used technique for this purpose, where a single silicon crystal is pulled from a molten bath of pure silicon under controlled conditions. This method ensures the orientation and size of the crystal structure meet the precise specifications for subsequent processing.
Once the ingot is formed, it is sliced into thin discs, or wafers, with a process called wafering. The wafers are then polished to achieve a mirror-like surface, which is essential for the photolithography steps that follow. The quality of the wafer surface is critical, as any imperfections can lead to defects in the final integrated circuits.
Photolithography: Patterning the Silicon
Photolithography stands as a cornerstone in the manufacturing of integrated circuits, transforming a plain silicon wafer into a complex network of electronic pathways. This process involves coating the wafer with a light-sensitive material called photomask, which is then exposed to a source of light. The light selectively hardens the photoresist according to the desired circuit pattern, allowing the unexposed areas to be washed away.
The precision of photolithography is paramount, as it dictates the fidelity of the pattern transfer and ultimately the performance of the final electronic components. To enhance the resolution and accuracy, techniques such as optical proximity correction (OPC) and multiple patterning are employed. These methods correct for the diffraction and interference effects that can distort the pattern as it is projected onto the wafer surface.
Below is a list of key terms associated with photolithography in wafer fabrication:
- Photomask: A template for transferring the circuit pattern onto the wafer.
- Photoresist: A light-sensitive material that coats the wafer surface.
- Optical Proximity Correction (OPC): A technique to compensate for optical distortion during patterning.
- Multiple Patterning: A method to increase the pattern density beyond the limits of the photolithography equipment.
Etching and Deposition Techniques
The precision of etching and deposition techniques is crucial in semiconductor fabrication, as they define the intricate patterns that form the electronic circuits on a wafer. Etching processes remove material to create these patterns, while deposition adds layers of material to build the circuit structures.
Deposition techniques vary, with Chemical Vapor Deposition (CVD) and Physical Vapor Deposition (PVD) being the most common. CVD uses chemical reactions to produce high-purity, high-performance solid materials, which are essential for creating semiconductor devices. PVD, on the other hand, involves physical processes such as sputtering or evaporation to deposit thin films.
Advanced methods like Atomic Layer Deposition (ALD) allow for the construction of layers atom by atom, providing exceptional control over film thickness and composition. This level of precision is vital for the production of high-quality semiconductors. The table below summarizes the key characteristics of these deposition methods:
Technique | Material Coverage | Thickness Control | Application |
---|---|---|---|
CVD | Uniform | Moderate | General |
PVD | Directional | High | Metals |
ALD | Conformal | Atomic-level | Advanced |
Understanding these techniques is fundamental to the semiconductor manufacturing process, as they directly impact the performance and reliability of the final product. As technology advances, the industry continues to innovate, seeking even more precise and efficient ways to pattern and build the complex structures required by modern electronics.
Doping: Modifying Electrical Properties
Doping is a critical step in wafer fabrication that alters the electrical properties of silicon, transforming it from a poor conductor into a semiconductor capable of controlling electron flow. This process involves introducing small amounts of impurities, known as dopants, into the silicon wafer. Depending on the type of dopant used, the silicon can become either n-type, with an abundance of electrons, or p-type, with an abundance of ‘holes’ where electrons are absent.
The choice of dopant and the concentration levels are meticulously controlled to achieve the desired electrical characteristics. Here’s a simplified overview of common dopants and their effects:
- Phosphorus (P): Introduces extra electrons, creating n-type silicon.
- Boron (B): Creates holes by accepting electrons, resulting in p-type silicon.
- Arsenic (As): Similar to phosphorus, it donates electrons to form n-type silicon.
The precise control of doping is essential for the creation of p-n junctions, which are the building blocks of most semiconductor devices. By carefully manipulating the doping process, manufacturers can produce silicon wafers with the exact specifications needed for a wide range of electronic applications.
Advancements in Wafer Inspection and Metrology
Defect Detection and Wafer Inspection
In the intricate process of wafer fabrication, defect detection and wafer inspection are critical for ensuring the quality and reliability of semiconductor devices. This method assists in identifying the root causes of defects, enabling manufacturers to implement corrective measures and enhance the overall yield of the production process.
The inspection process involves a variety of sophisticated techniques, each designed to uncover different types of defects that may occur during the manufacturing stages. Some of the common inspection methods include:
- Visual inspection using high-resolution microscopes
- Automated defect classification systems
- Laser scattering for sub-surface defect detection
- E-beam inspection for high-resolution imaging
These methods contribute to a comprehensive quality assurance strategy, which is essential in an industry where the cost of failure is exceedingly high. As technology advances, the inspection techniques become more refined, allowing for the detection of even the most minute imperfections.
Metrology and Process Control
In the intricate process of semiconductor manufacturing, metrology and process control play pivotal roles in ensuring the quality and consistency of the final product. Wafer metrology tools are essential for designing and manufacturing integrated circuits (ICs), as they allow for precise control over film properties, linewidths, and potential defect levels. These tools facilitate the measurement and analysis of various parameters that are critical to the success of semiconductor devices.
The following list highlights some of the key metrology tools and techniques used in the industry:
- Self-Aligned Double Patterning (SADP)
- Atomic Layer Deposition (ALD)
- Chemical Vapor Deposition (CVD)
- E-beam Inspection
- Optical Inspection
Advancements in metrology have also led to the integration of artificial intelligence and machine learning to tackle variability and enhance process control. These technologies are becoming increasingly prevalent in fabs, aiming to reduce water usage and waste, while improving yield management systems (YMS) and the overall manufacturing execution system (MES).
The Role of E-Beam and Optical Inspection
In the intricate process of wafer fabrication, electron-beam (E-beam) and optical inspection systems play a pivotal role in ensuring the integrity of the microscopic features that define modern integrated circuits. E-beam inspection, in particular, has been a cornerstone technology for decades, offering the precision required to measure and inspect nanostructures on the wafer surface.
The table below outlines key differences between E-beam and optical inspection methods:
Inspection Type | Resolution | Throughput | Surface Penetration |
---|---|---|---|
E-beam | High | Low | Deep |
Optical | Moderate | High | Shallow |
Optical inspection, while not as precise as E-beam, compensates with its higher throughput, making it suitable for rapid defect detection across the wafer. Both methods are integral to maintaining the quality control standards that are critical in semiconductor manufacturing. As feature sizes on wafers continue to shrink, the demand for advanced inspection techniques that can keep pace with the innovative ways to make and measure nanostructures is ever-increasing.
Interconnect Technologies: Wirebonding to 3D Integration
Wirebonding Techniques and Challenges
Wirebonding remains a critical step in semiconductor device fabrication, connecting the intricate circuitry of an IC to the outside world through tiny wires. This process involves precision and accuracy to ensure reliable electrical connections without damaging the delicate silicon wafer or the IC itself.
The challenges in wirebonding are multifaceted, ranging from material selection to the intricacies of the bonding process. For instance, the choice of wire material—often gold, aluminum, or copper—has significant implications for the performance and longevity of the semiconductor device. Additionally, the shift towards finer geometries and the introduction of new materials in the backend-of-the-line (BEOL) processes have necessitated advancements in wirebonding techniques.
To illustrate some of the common issues faced in wirebonding, consider the following points:
- Ensuring consistent wire loop height for reliable connectivity
- Minimizing wire sweep during the encapsulation process
- Controlling intermetallic compound formation
- Adapting to the increasing use of copper wires, which are harder to bond than gold
Addressing these challenges requires a combination of skilled technicians, advanced machinery, and ongoing research into new wirebonding methods and materials.
Wide I/O and Memory Interface Standards
The Wide I/O standard is a pivotal development in memory interface technology, particularly for 3D integrated circuits (ICs). It offers a significant leap in data bandwidth by providing a wide interface to memory, which is essential for applications demanding high-speed data processing. This standard utilizes ‘voltage islands’ to reduce power consumption, a technique that involves using multiple voltages within the same chip to optimize power efficiency.
Wide I/O’s architecture is designed to work seamlessly with 3D ICs, where memory stacks are vertically integrated with logic dies using through-silicon vias (TSVs). This integration allows for faster and more energy-efficient data transfer between the processor and memory. The standard also addresses the challenges of off-chip communications by minimizing the distance data must travel, thus reducing latency and power usage.
Here are some key features of the Wide I/O memory interface standard:
- High-bandwidth memory (HBM) integration
- Support for 3D stacking with TSVs
- Voltage islands for power reduction
- Enhanced data transfer rates and reduced latency
X Architecture and its Impact on IC Interconnects
The X Architecture represents a significant shift in IC interconnect design, aiming to improve chip performance by optimizing the layout of interconnects. This architecture departs from the traditional Manhattan style of IC design, which uses right-angle interconnections, by incorporating diagonal routes. This allows for shorter wire lengths and potentially higher speeds, but it also introduces unique challenges in X Verification and signal propagation.
One of the critical issues with X Architecture is the X Propagation problem, which can lead to signal integrity issues and impact the overall yield of the semiconductor manufacturing process. To address this, a Yield Management System (YMS) is often employed. YMS is a data-driven approach that monitors various process parameters and outcomes, enabling manufacturers to identify and rectify yield-impacting factors more efficiently.
The table below summarizes the benefits and challenges of X Architecture:
Benefit | Challenge |
---|---|
Shorter wire lengths | Complex verification |
Potential for higher speeds | Signal integrity issues |
Improved chip performance | Yield management |
Adopting X Architecture requires careful consideration of these trade-offs to ensure that the benefits outweigh the challenges in a given application.
Optimizing Performance: Power, Noise, and Computing
Implementation Power Optimizations
In the realm of semiconductor manufacturing, power optimization is a critical aspect that directly influences the efficiency and performance of the final product. Techniques such as power gating and power domain shutdown are employed to reduce power consumption by turning off parts of a design when they are not in use. This not only conserves energy but also mitigates heat generation, which is a significant concern in high-density integrated circuits.
The implementation of power optimizations requires a careful balance with other design considerations, often referred to as PPA (Power, Performance, Area). These trade-offs are fundamental in semiconductor design and necessitate a holistic approach to achieve the desired outcomes. For instance, power gating retention involves using special flops or latches to retain the state of a cell when its main power supply is shut off, ensuring that functionality is not compromised.
To systematically address power issues, the industry adheres to standards such as IEEE P2416, which provides a framework for power modeling and enables system-level analysis. The table below summarizes key power optimization techniques and their impact:
Technique | Description | Impact on PPA |
---|---|---|
Power Gating | Reducing power by turning off inactive parts | Lowers power |
Power Domain Management | Controlling power across different sections | Balances performance |
Dynamic Voltage Scaling | Adjusting voltage based on workload | Optimizes area |
As the demand for energy-efficient electronics continues to rise, the importance of implementation power optimizations becomes ever more pronounced. By using advanced techniques and adhering to industry standards, manufacturers can ensure that their products meet the stringent requirements of modern electronic devices.
Induced Gate Noise and Thermal Management
As semiconductor devices continue to scale down, managing induced gate noise and thermal effects becomes increasingly critical. Thermal noise, also known as Johnson-Nyquist noise, arises from the inherent thermal agitation of charge carriers within a semiconductor channel. This type of noise is a fundamental limit to the performance of electronic circuits and was first characterized by J.B. Johnson in 1928.
Effective thermal management strategies are essential to maintain device reliability and performance. Below are some common techniques used in the industry:
- Utilization of heat sinks and cooling systems to dissipate excess heat.
- Implementation of power gating to reduce power consumption and heat generation in idle circuit blocks.
- Design of power delivery networks (PDN) to ensure stable and efficient power distribution across the chip.
These methods, along with advanced materials and device structures, help mitigate the adverse effects of thermal noise and heat on semiconductor devices.
In-Memory Computing and ISA
In-memory computing represents a paradigm shift in how data processing is performed. By performing functions directly in the fabric of memory, this approach eliminates the need for data to travel between the processor and memory, reducing latency and increasing efficiency. The Instruction Set Architecture (ISA) plays a crucial role in this context, as it defines the set of operations that the computer’s hardware can execute directly.
The ISA is particularly important for in-memory computing because it can be optimized to take advantage of the memory’s computational capabilities. For instance, certain ISAs are designed to support operations like vector processing or complex arithmetic directly within the memory array, which can significantly accelerate specific workloads.
Below is a list of key considerations when integrating in-memory computing with ISA:
- Ensuring compatibility between the ISA and the memory’s computational features.
- Optimizing the ISA to leverage the full potential of in-memory computation.
- Balancing the trade-offs between computational power and energy consumption.
- Evaluating the impact of in-memory computing on overall system architecture, including off-chip and on-chip communications.
Emerging Trends in Semiconductor Manufacturing
Silicon Photonics and SOI Wafers
Silicon photonics is rapidly advancing, leveraging the unique properties of SOI (Silicon-On-Insulator) wafers to push the boundaries of optical communication and computing. SOI wafers are pivotal in this evolution, offering a platform that supports the integration of thousands of photonic components on a single chip. The transition to larger wafer diameters, such as 200-mm and 300-mm, facilitates the fabrication of more chips and enhances control over critical parameters like thickness uniformity.
The architecture of photonic SOI substrates is designed to optimize the value proposition for photonic devices, circuits, and subsystems. Enhanced uniformities in both wafer-to-wafer (W2W) and within-wafer (WiW) metrics, as well as reduced surface roughness, are crucial for achieving high yield and performance. The top silicon layer’s optical properties, including defects and microdefects, play a significant role in the efficiency of the final photonic components.
Advancements in SOI technology have also led to the development of a BMD-free zone, which is essential for creating high-quality etching for fiber-attach V-grooves or electrical through-silicon vias (TSVs). This innovation is a testament to the ongoing efforts to refine the substrate properties to meet the demands of next-generation silicon photonics applications.
The Evolution of Lithography and its Economic Impact
The evolution of lithography techniques has been pivotal in shaping the semiconductor industry. Extreme Ultraviolet Lithography (EUV), for instance, represents a significant leap forward, allowing for smaller feature sizes and increased circuit density. This advancement has been met with substantial investments from semiconductor giants, driven by the escalating demands of consumer electronics and high-performance computing sectors.
The economic impact of these advancements is multifaceted. On one hand, the cost of implementing cutting-edge lithography technologies like EUV is high, reflecting on the overall wafer costs. On the other hand, the efficiency gains and the ability to produce more complex integrated circuits (ICs) can lead to a reduction in cost per function, which is a critical metric in the industry. The table below summarizes the impact of lithography on wafer costs across different nodes:
Node (nm) | Optical Lithography Cost | EUV Lithography Cost |
---|---|---|
130 | Low | N/A |
65 | Moderate | N/A |
10 | High | Very High |
As the industry continues to push the boundaries of miniaturization, the role of lithography in cost and innovation remains a central theme. The k1 coefficient in lithography is a testament to the increasing complexity and difficulty of the patterning process as feature sizes shrink, further emphasizing the need for ongoing research and development in this area.
MEMS and Beyond: The Future of Miniaturization
As we look beyond the current landscape of microelectromechanical systems (MEMS), the trend towards miniaturization continues to drive innovation in the semiconductor industry. This relentless push for smaller, more efficient devices is not only redefining the capabilities of the Internet of Things (IoT) but also opening new frontiers in technology.
The development of monolithic 3D chips, for instance, represents a significant leap in this direction. By stacking transistors within a single chip, engineers are able to achieve higher transistor density without increasing the chip’s footprint. This approach not only enhances performance but also reduces power consumption, a critical factor in mobile and wearable technologies.
Advancements in materials science, such as the use of metamaterials, are also pivotal in the miniaturization trend. These artificial materials, with their unique properties, are enabling the creation of components that were once thought impossible. As we continue to explore the potential of these and other emerging technologies, the future of semiconductor manufacturing promises to be as exciting as it is challenging.
Conclusion
The journey from a bare silicon wafer to a complex integrated circuit is a marvel of modern engineering, combining the precision of science with the creativity of art. Throughout this article, we have explored the intricate processes of wafer fabrication, including the critical role of wafer inspection, the advancements in memory interface standards such as Wide I/O for 3D ICs, and the enduring relevance of wired communications in ensuring stable data transfer. We delved into the nuances of wirebonding, the challenges and innovations in wireless data transmission, and the significance of X architecture in IC interconnects. The article highlighted the importance of uniformity and surface roughness in SOI substrates for silicon photonics, the impact of lithography on wafer costs, and the various optimization techniques that contribute to the efficiency of integrated circuits. As we conclude, it is evident that the art and science of wafer fabrication are not only foundational to the semiconductor industry but also to the technological advancements that shape our daily lives. The continuous evolution of fabrication techniques and the relentless pursuit of perfection in the microscopic world of silicon wafers underscore the incredible human ingenuity behind the electronic devices we often take for granted.
Frequently Asked Questions
What is wafer inspection and why is it important?
Wafer inspection is the science of finding defects on a silicon wafer. It is crucial for ensuring the quality and reliability of semiconductor devices, as defects can lead to failures or reduced performance.
What is the Wide I/O memory interface standard?
Wide I/O is a memory interface standard designed for 3D integrated circuits (ICs). It enables higher bandwidth and lower power consumption by providing a wide data interface between memory and the logic die.
How does wirebonding contribute to IC packaging?
Wirebonding involves creating electrical interconnects between the integrated circuit (IC) and its package using a thin wire. It’s a common technique for establishing connections in semiconductor devices.
What advancements have been made in SOI wafers for silicon photonics?
Advancements in SOI wafers for silicon photonics include enhanced wafer-to-wafer uniformity, reduced surface roughness, and the creation of a defect-free zone known as the denuded zone, which allows for effective etching and the integration of optical and electrical interconnects.
How does the evolution of lithography impact wafer costs?
The evolution of lithography directly impacts wafer costs, with newer techniques like extreme ultraviolet (EUV) lithography enabling more intricate patterns but often at a higher cost. This affects the overall economics of semiconductor manufacturing.
What is in-memory computing and how does it differ from traditional computing?
In-memory computing involves performing computational functions directly within the memory substrate, as opposed to processing data in a separate CPU. This can lead to faster processing speeds and reduced energy consumption.