The Art of Precision: Crafting Excellence in Semiconductor Design
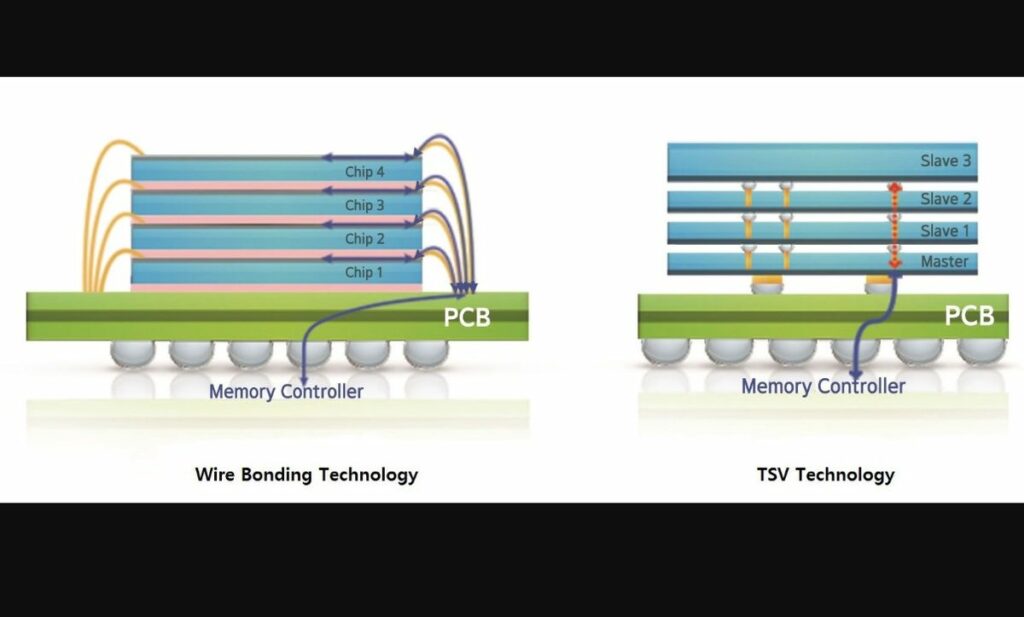
In the highly specialized field of semiconductor design, the quest for precision is relentless. This article, ‘The Art of Precision: Crafting Excellence in Semiconductor Design,’ delves into the meticulous processes and innovative technologies that shape the world of microelectronics. From the foundational principles of semiconductor design to the cutting-edge advancements in fabrication and patterning technology, we explore the strategies and tools that have become indispensable in addressing the nuanced challenges presented by each component type, enhancing the precision and performance of chip designs.
Key Takeaways
- Semiconductor design is a complex process that begins with the fundamental understanding of doping silicon, p-n junctions, and various types of transistors, including FETs and CMOS.
- Integrated Circuit (IC) design methodologies encompass analog, digital, and mixed-signal design techniques, each requiring a unique approach to achieve optimal performance.
- Advancements in semiconductor fabrication, such as the development of Sculpta technology, are revolutionizing EUV patterning, thereby reducing costs and improving chip yields.
- Electronic Design Automation (EDA) tools are critical in optimizing semiconductor design, enabling designers to balance area, power, and speed in layout design for enhanced integration.
- The semiconductor design industry continuously evolves, with innovations in fabrication and EDA tools addressing the increasing complexity and performance demands of modern electronics.
Fundamentals of Semiconductor Design
Understanding Doping Silicon
Doping is a fundamental process in semiconductor design, where impurities are intentionally introduced to pure silicon to modify its electrical properties. Careful doping profile design is crucial as it determines the behavior of the semiconductor in various applications. For instance, doping can increase the silicon’s dielectric constant significantly, which is essential for the device’s performance.
The process involves adding either electron-rich (n-type) or electron-deficient (p-type) dopants to create regions within the silicon that either have an excess or deficiency of electrons. This alteration allows for the engineering of the electrical characteristics of the semiconductor, enabling the creation of devices with specific functions. The table below summarizes the effects of doping on silicon’s properties:
Property | Pure Silicon | N-type Doped | P-type Doped |
---|---|---|---|
Electrical Conductivity | Low | Increased | Increased |
Charge Carrier | None | Electrons | Holes |
Dielectric Constant | Moderate | High | High |
It’s important to note that excessive doping can lead to issues such as channel punchthrough, where the electric field can bridge the gap between source and drain in a transistor, leading to device failure. Therefore, precision in doping is not just an art; it’s a necessity for crafting excellence in semiconductor design.
Exploring the p-n Junction
At the heart of semiconductor technology lies the p-n junction, a critical component that enables the flow of electrical current in one direction while blocking it in the opposite. This property is fundamental to the operation of diodes, solar cells, and various types of transistors. The creation of a p-n junction involves the process of doping, where impurities are intentionally introduced into the silicon to create regions with an excess of positive (p-type) or negative (n-type) charge carriers.
The behavior of the p-n junction under different conditions is pivotal for semiconductor design. When forward-biased, the junction allows current to pass, while a reverse bias effectively stops the flow. This selective conductivity is harnessed in numerous applications, from rectifying alternating current to detecting light. The p-n junction’s efficiency and reliability are influenced by factors such as the doping concentration and the quality of the semiconductor material.
Understanding the intricacies of the p-n junction is essential for advancing semiconductor technology. It is the cornerstone upon which complex circuits are built, and its optimization can lead to significant improvements in device performance. The following list highlights key aspects of the p-n junction’s role in semiconductor devices:
- Acts as a one-way valve for electric current
- Enables the conversion of light to electricity in photovoltaic cells
- Forms the basis of transistor operation
- Influences the switching speed and power consumption of integrated circuits
The Role of Field-Effect Transistors
Field-effect transistors (FETs) are pivotal in the realm of semiconductor design, acting as the gatekeepers of electron flow within a device. Their ability to control the flow of electricity through a semiconductor is fundamental to modern electronics. FETs have replaced vacuum tubes in many applications due to their smaller size, greater efficiency, and higher reliability.
The design and optimization of FETs are crucial for achieving greater functionality and efficiency in electronic devices. These transistors are at the heart of numerous applications, from the amplification of signals to the switching required in digital circuits. The following list outlines the key attributes of FETs that make them indispensable:
- Low power consumption
- High input impedance
- Fast switching speeds
Advancements in FET technology have led to the development of nanoscale structures that are essential for high-frequency transistors and LEDs. The ongoing research and development in FETs are instrumental in driving the electronics industry forward, enabling the creation of more powerful and compact devices that are integral to our modern lifestyle.
Enhancement-mode FETs: A Closer Look
Enhancement-mode Field-Effect Transistors (FETs) are pivotal in the semiconductor design for their ability to operate as switches, amplifying the capabilities of electronic circuits. Their conductive properties are induced by the application of a voltage, which enhances the flow of electrons or holes, depending on the type of FET.
The design intricacies of enhancement-mode FETs allow for greater functionality and efficiency in electronic devices. These FETs are commonly used in logic gates, which are the building blocks of digital circuits. The performance of these transistors is often gauged by their electron mobility, which is crucial for high-speed operation.
Understanding High-Electron-Mobility Transistors (HEMTs), also known as HEM FETs, is essential as they represent a significant advancement in FET technology. HEMTs utilize a heterojunction of materials with different band gaps, which results in improved electron mobility and, consequently, faster switching speeds. This makes them ideal for use in applications that require rapid signal processing, such as in the realms of power electronics and photonics, where they contribute to the development of nanoscale structures in LEDs and high-frequency transistors.
Complementary Metal-Oxide Semiconductors (CMOS)
Complementary Metal-Oxide Semiconductors, or CMOS, stand as a cornerstone in modern semiconductor design, enabling the creation of highly efficient and compact integrated circuits. CMOS technology harnesses the attributes of both n-type and p-type MOSFETs to achieve low power dissipation, making it ideal for a myriad of applications ranging from microprocessors to memory chips.
The versatility of CMOS is evident in its widespread use across various domains. For instance, in the realm of memory applications, CMOS technology extends to both volatile and non-volatile memory, playing a pivotal role in the development of Flash memory and RF capacitors. Additionally, CMOS is integral to the integration of advanced low-k materials and copper interconnects, which are essential for the miniaturization and performance enhancement of modern electronics.
The design of standard cells, which are the fundamental building blocks of digital designs, is a testament to the adaptability of CMOS. These cells encompass basic logic gates and complex combinational functions that dictate the overall chip performance and power efficiency. The continuous evolution of CMOS design is driven by the development of new precursors and delivery systems, as well as the integration of high-k oxides and metal electrodes with high-mobility channel materials.
Bipolar Transistors and Their Applications
Bipolar transistors, or Bipolar Junction Transistors (BJTs), are the workhorses of semiconductor devices, pivotal in the evolution of integrated circuits since their invention in 1947. Their ability to amplify current makes them indispensable in both digital and analog applications, from simple switches to complex processing units.
BJTs operate on the principle of charge carrier injection and control within a semiconductor crystal. They are characterized by three regions: the emitter, base, and collector. The precise control of electron flow through these regions is what allows BJTs to amplify signals. Heterojunction Bipolar Transistors (HBTs) expand upon this concept by using varied semiconductor materials at the junctions, enhancing performance in high-frequency applications.
The applications of BJTs are vast and diverse, including but not limited to:
- Power electronics
- Signal amplification
- Switching circuits
- Audio amplifiers
- Radio frequency (RF) applications
Advancements in semiconductor materials and fabrication techniques continue to optimize the performance of BJTs, ensuring their relevance in modern electronics.
Integrated Circuit Design Methodologies
Analog Design Principles
Analog circuit design is an art that melds intricate knowledge of device physics with the subtleties of the intended application. LCMs for analog circuits must capture this depth of knowledge, translating it into models that can navigate the analog design space with its continuous variables and stringent performance metrics. These models could predict analog behavior from device-level up to system-level specifications, assist in layout generation, and automate the tedious tuning process of analog circuits.
A major challenge in analog design is performance optimization, marked by its nonlinearity and the lack of clear functional expressions. Despite these obstacles, the EDA community has significantly advanced the automation of analog IC design over the years. Efforts have covered various areas, such as topology selection or exploration, analog sizing, and analog placement-and-route.
Analog EDA shares similarities and differences with digital EDA. Like digital workflows, analog EDA encompasses front-end netlist design and back-end layout design. However, analog circuits exhibit distinct data structures and performance evaluations compared to their digital counterparts, which are primarily logic-driven. In analog circuits, device-level topology and physical implementation are crucial.
Digital Design Techniques
In the realm of digital circuit design, the evolution of front-end design and verification tools has been pivotal. These tools have not only streamlined the design process but also expanded what is possible, becoming indispensable for innovation and optimization in digital systems.
Physical design transforms the logical circuit representations into physical layouts through partitioning, floorplanning, placement, and routing. This stage is marked by its complexity and the need to solve numerous NP-hard combinatorial optimization problems, making it both complex and time-consuming.
The design journey for digital circuits often begins by defining the design space for a target application. This includes the architectural design and the intricate interplay of components within the datapath circuits. The goal is to achieve seamless integration and peak efficiency, a task that is increasingly challenging as electronic designs scale and feature sizes shrink.
The Fusion of Mixed-Signal Design
The fusion of mixed-signal design marks a significant milestone in the evolution of integrated circuits, blending the precision of digital techniques with the nuance of analog signals. Harmonious integration of these two realms enables designers to capture the intricate relationships among circuit components, leading to enhanced optimization and streamlined verification processes.
In the realm of mixed-signal design, verification plays a pivotal role. Traditional methods often saw the analog team running transistor level simulations separately, which could lead to inefficiencies and a disjointed final product. However, recent methodologies advocate for a more integrated approach, aligning the verification process with the overall design flow. This strategy aims to bridge the gap between analog and digital modalities, fostering a seamless circuit design environment.
The table below outlines key aspects of mixed-signal design and their impact on the design process:
Aspect | Impact on Design Process |
---|---|
Analog Precision | Enhances signal integrity |
Digital Efficiency | Accelerates computation |
Unified Verification | Reduces time-to-market |
By adopting such a unified approach, designers are not only able to accelerate design generation but also enhance optimization efforts, embodying a leap forward in circuit design methodology.
Advances in Semiconductor Fabrication
Creating the Base Wafer: Foundation of ICs
The journey of semiconductor fabrication begins with the creation of the base wafer, which serves as the substrate for all subsequent layers of the integrated circuit (IC). This foundational element is typically made from a high-purity silicon crystal, grown and cut into thin, polished discs. The quality of the base wafer is critical, as it influences the performance and yield of the final semiconductor devices.
The process of building upon the base wafer involves a series of intricate steps. These include various methods of deposition to add layers, etching to create patterns, and implantation to modify the electrical properties of the layers. Each step must be executed with precision to ensure the integrity of the ICs. The table below summarizes the key stages in the base wafer fabrication process:
Stage | Description |
---|---|
Deposition | Adding layers using chemical or physical methods |
Etching | Patterning the wafer by removing material |
Implantation | Altering electrical properties by introducing dopants |
Once the base wafer has been prepared and processed, it becomes the canvas upon which the complex network of transistors and interconnections are formed. This intricate dance of adding and removing material, all while maintaining the purity and structure of the silicon, is what allows for the miniaturization and integration of electronic components that was once thought impossible.
Building Layers: Deposition, Etching, and Implantation
The intricate process of building layers on a semiconductor wafer involves several critical steps, each contributing to the final device’s performance and reliability. Deposition techniques, such as Atomic Layer Deposition (ALD), are employed to apply ultra-thin layers that are essential for the device’s functionality, particularly in insulating layers and gate dielectrics of transistors. ALD’s counterpart, Atomic Layer Etching (ALE), offers precise etching capabilities, which are indispensable for creating the intricate details required in modern semiconductor devices.
During the deposition phase, both chemical and physical methods are utilized to coat the wafer. Chemical methods include techniques like Chemical Vapor Deposition (CVD), while physical methods encompass sputtering and evaporation. The choice of method depends on the material properties and the desired layer characteristics. Etching, on the other hand, is the process of removing material from the wafer to create the desired pattern, often using a chemical solution or plasma.
Implantation is the final step in this phase, where ions are embedded into the wafer to alter its electrical properties. This step is crucial for doping the semiconductor and defining the active regions of the device. The precision and control achieved in each of these steps are vital for the success of the semiconductor manufacturing process.
Photolithography: Patterning the Microscopic Landscape
Photolithography stands as a cornerstone in the manufacturing of integrated circuits, utilizing light to imprint intricate patterns onto a substrate. This process is critical for defining the minute features that form the electronic pathways of semiconductor devices.
Advancements in photolithography have been pivotal in pushing the boundaries of what’s possible in IC fabrication. Recent studies, such as those published in IEEE Transactions and the Journal of Micro/Nanolithography, have explored the use of convolutional neural networks and generative adversarial networks to enhance lithography simulation models and hotspot detection, respectively.
As the industry marches towards the ‘angstrom era’, the role of photolithography grows increasingly complex. The integration of Extreme Ultraviolet (EUV) and High-NA EUV lithography techniques is essential for patterning the smallest features, necessitating a robust ecosystem of software, design tools, and advanced metrology systems to support this evolution.
Packaging the Final Product: Ensuring Integrity and Performance
The final stage in semiconductor fabrication is the packaging of the chip, which is crucial for protecting the delicate internal structures and ensuring the device’s functionality in real-world applications. Effective packaging enhances robustness against variations in the fabrication process, leading to higher yields and reliability. This is particularly important as the complexity and density of printed circuit boards (PCBs) increase, along with the use of 3D devices and intricate packages like BGAs, QFNs, and QFPs.
Quality assurance plays a pivotal role in this phase, with zero-defect strategies becoming a standard due to the continuous miniaturization of components and higher packing densities. The challenges posed by these developments necessitate high-precision quality control measures. The table below outlines the key aspects of semiconductor packaging that contribute to its integrity and performance:
Aspect | Description |
---|---|
Protection | Shields the semiconductor from physical damage and environmental factors. |
Connectivity | Ensures electrical connections are maintained with the PCB. |
Heat Dissipation | Manages thermal performance to prevent overheating. |
Size & Weight | Minimizes footprint for more compact device integration. |
To achieve these objectives, a combination of process technology, meticulous planning, and cooperation with system and material partners is essential. Dispensing systems, for instance, must be perfectly set up for the specific project to ensure reliable performance. As the industry moves forward, the pursuit of perfection in packaging not only secures the chip’s functionality but also combats potential issues like counterfeiting, which becomes more attractive as component costs rise with complexity.
Optimizing Semiconductor Design with EDA Tools
Defining the Design Space for Target Applications
In the realm of semiconductor design, the definition of the design space is a critical step that sets the stage for the entire development process. It encompasses a wide array of parameters, from CPU tasks like SPEC2017 benchmarks to GPU tasks such as matrix multiplication, each tailored to specific architectural needs. The design space is a complex matrix that diverges into two main domains: the application space, which includes application-specific parameters like dataflow patterns, and the architectural domain, which focuses on the underlying hardware structure.
The intersection of these parameters forms what is known as a ‘design point’. This point, once established, undergoes rigorous evaluation and validation using advanced EDA tools. The process is iterative, exploring and refining new design points to meet exploration goals. These tools not only facilitate the optimization of datapath circuits for seamless integration but also enable the assessment of multiple objectives such as performance, area, and robustness to process variations.
To illustrate the optimization process, consider the IT-DSE framework proposed by Yu et al. This framework uses a surrogate model pre-trained on historical design data to refine the search process. It demonstrates how accumulated design knowledge can be effectively reused to optimize new projects, highlighting the importance of interdependencies among various objectives across different design fidelities.
Datapath Circuit Refinement for Enhanced Integration
The refinement of datapath circuits is a pivotal step in semiconductor design, where EDA tools play a crucial role in enhancing integration and efficiency. These tools facilitate the optimization of adders, multipliers, and MAC units, which are integral to performing arithmetic and logical operations within microarchitectures.
Optimization of these circuits involves a delicate balance of power, performance, and area (PPA). Large Circuit Models (LCMs) act as surrogate models during the design space exploration, aiding in the bit-level optimization that is essential for meeting timing and power constraints. Tailored LCMs for datapath circuits leverage specialized architectures that comprehend the intricacies of arithmetic operations, thereby improving logical efficiency and optimizing the physical layout.
The following table summarizes the key parameters in datapath circuit design and their impact on the overall semiconductor performance:
Parameter | Impact on Design |
---|---|
Power | Reduces energy consumption and heat generation |
Performance | Enhances speed and throughput |
Area | Minimizes chip size and cost |
Through iterative refinement and the use of advanced EDA tools, designers can achieve a harmonious integration of datapath circuits, ultimately leading to more powerful and efficient semiconductor devices.
Balancing Area, Power, and Speed in Layout Design
In the intricate dance of semiconductor design, balancing area, power, and speed is akin to achieving harmony. The layout phase is pivotal, as it determines how well the final design aligns with the stringent constraints of performance, power, and area. This phase is a testament to the evolving demands of semiconductor technology and the prowess of modern EDA tools.
Optimization of PPA (Performance, Power, and Area) and other design factors is central to EDA. As designs scale up and complexities burgeon, achieving the right balance becomes increasingly arduous. EDA tools employ predictive modeling, heuristic algorithms, and other sophisticated techniques to navigate these challenges.
Placement is another critical aspect of layout design. It involves the strategic positioning of standard cells or IP blocks within the floorplan. The goal is to enhance performance, reduce wire length, alleviate congestion, and mitigate timing and thermal impacts. This is achieved through algorithms that strive for an optimal configuration, ensuring the final product meets the desired SWaP, EMC, and manufacturability requirements.
Factor | Consideration |
---|---|
Area | Minimize footprint by efficient component placement and integration |
Power | Optimize consumption through voltage scaling and power gating techniques |
Speed | Maximize through careful timing analysis and signal integrity measures |
Innovations in Patterning Technology
Sculpta: Revolutionizing EUV Patterning
The introduction of Sculpta by Applied Materials marks a significant leap in EUV patterning technology. Its ability to refine EUV patterning has been embraced by leading logic chipmakers, notably reducing the need for double patterning steps and effectively addressing common defects. This innovation is not just a technical achievement; it’s a cost-saving measure that simultaneously enhances chip yields.
As the industry marches towards the ‘angstrom era’ of chipmaking, the demand for advanced patterning capabilities escalates. Sculpta is at the forefront of this shift, forming a critical component of the ecosystem required for High-NA EUV lithography. This ecosystem encompasses a range of tools and technologies, from software and design tools to advanced metrology systems.
Applied Materials’ commitment to the advancement of semiconductor technology is evident in its expanding patterning solutions portfolio. By tackling the challenges of EUV lithography head-on, the company is setting new industry benchmarks and propelling angstrom era chipmaking capabilities to new heights. The Producer XP Pioneer CVD patterning film, another innovation from Applied Materials, complements Sculpta’s capabilities by providing high-fidelity pattern transfer and enhanced resistance to etch chemistries, crucial for advanced process nodes.
Reducing Double Patterning Steps and Defects
The evolution of patterning technology has been marked by significant strides in reducing the complexity and cost associated with double patterning. Applied Materials’ Sculpta technology stands at the forefront of this transformation, offering a robust solution that streamlines the patterning process. By minimizing the number of patterning steps, Sculpta not only cuts down on production time but also diminishes the likelihood of introducing defects during fabrication.
Efficiency in the patterning process is crucial for maintaining high chip yields and overall manufacturing quality. The reduction of double patterning steps is a testament to the industry’s commitment to enhance robustness against variations in the fabrication process. This advancement ensures that each chip meets the highest standards of reliability, a critical factor in the competitive semiconductor market.
The table below summarizes the impact of reducing double patterning steps on the overall production process:
Aspect | Before Reduction | After Reduction |
---|---|---|
Steps Required | Multiple | Fewer |
Defect Probability | Higher | Lower |
Production Time | Longer | Shorter |
Chip Yield | Variable | Improved |
As the industry continues to push the boundaries of what’s possible in semiconductor design, technologies like Sculpta are instrumental in achieving improved chip yield and cost-effectiveness. The focus on minimizing defects and rework is a clear indicator of the industry’s dedication to excellence.
Impact on Patterning Costs and Chip Yields
The relentless pursuit of miniaturization in semiconductors has placed lithography and metrology at the forefront of yield enhancement. Applied Materials’ Sculpta technology exemplifies this trend, significantly reducing double patterning steps and associated defects, such as bridge defects. This innovation is not only a testament to the company’s commitment to advancing semiconductor technology but also a critical factor in lowering patterning costs and improving chip yields.
In the context of manufacturability, variability in fabrication processes poses a substantial challenge. Applied Materials addresses these concerns by expanding its patterning solutions portfolio, including the Producer XP Pioneer CVD patterning film and the Sym3 Y Magnum etch system. These technologies are instrumental in navigating the complexities of angstrom era chipmaking, ensuring that performance and yield are not compromised by fabrication inconsistencies.
The table below summarizes the impact of advanced patterning technologies on costs and yields:
Technology | Cost Reduction | Yield Improvement |
---|---|---|
Sculpta | Significant | Notable |
Producer XP Pioneer | Moderate | Moderate |
Sym3 Y Magnum | Moderate | Moderate |
By integrating these advanced solutions, chipmakers can achieve a delicate balance between cost-efficiency and high-quality output, driving the industry towards the next generation of semiconductor devices.
Conclusion
In the pursuit of semiconductor perfection, the art of precision is not just a goal but a continuous journey. From the basic design principles of doping silicon and crafting field-effect transistors to the intricate processes of analog, digital, and mixed-signal design, each step is a testament to the meticulous craftsmanship required in semiconductor design. The evolution of EDA tools and groundbreaking technologies like Applied Materials’ Sculpta pattern-shaping have revolutionized the way we approach layout optimization, enabling designers to overcome the challenges of area, power, and speed with unprecedented efficiency. As we have explored, the synergy between advanced manufacturing techniques and innovative design strategies has become indispensable in addressing the nuanced challenges presented by each component type, enhancing the precision and performance of chip designs. As the semiconductor industry continues to advance, the commitment to crafting excellence remains the cornerstone of innovation, driving us towards the next frontier of electronic capabilities.
Frequently Asked Questions
What is doping in silicon and why is it important in semiconductor design?
Doping in silicon involves introducing impurities into the silicon crystal to alter its electrical properties, making it more conductive. It’s crucial for creating p-type and n-type semiconductors, which are essential for the function of devices like transistors and diodes.
How does a p-n junction work and what is its role in electronics?
A p-n junction is formed by joining p-type and n-type semiconductors, creating a depletion region at the interface. This junction allows current to flow in one direction, acting as a diode, and is fundamental in rectifying and switching applications.
What are Field-Effect Transistors (FETs) and how are they used?
FETs are transistors that control the flow of current by applying voltage to an electric field. They are used in various applications, including as switches and amplifiers in digital and analog circuits.
What is CMOS technology and why is it significant in IC design?
CMOS, or Complementary Metal-Oxide-Semiconductor technology, uses both p-type and n-type MOSFETs. It’s significant for its low power consumption and high noise immunity, making it the preferred choice for integrated circuits in computers and other electronics.
How do EDA tools optimize semiconductor design?
EDA (Electronic Design Automation) tools assist designers in creating complex semiconductor circuits by automating layout, simulation, and verification processes. They optimize design for area, power, and speed, enhancing the precision and performance of chip designs.
What advancements does Sculpta technology bring to EUV patterning?
Sculpta technology revolutionizes EUV patterning by reducing the need for double patterning steps and decreasing defects. This results in lower patterning costs and improved chip yields, making it a significant advancement in semiconductor fabrication.