The Essential Guide to Finding High-Quality Silicon Wafers for Sale
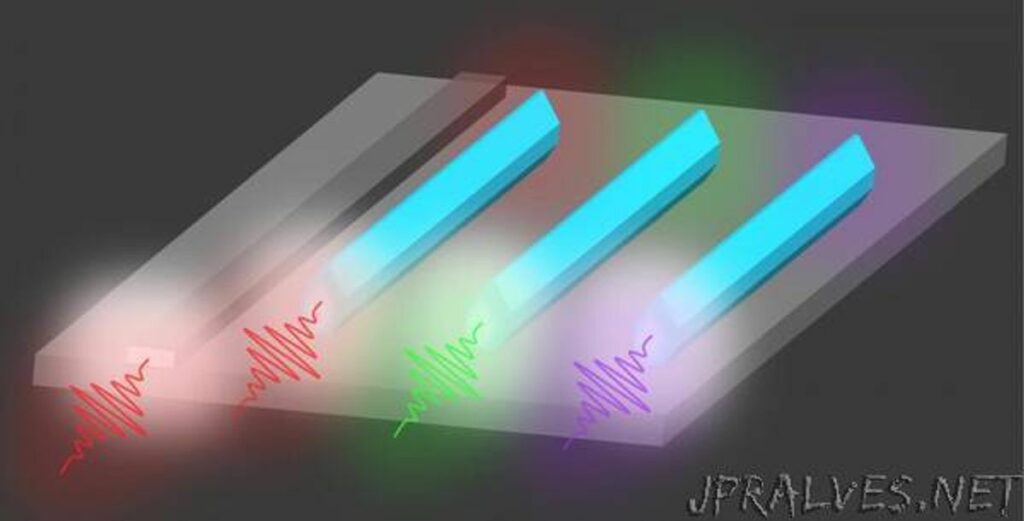
The semiconductor industry is continually advancing, with silicon wafers at the heart of this technological evolution. High-quality silicon wafers are crucial for the production of reliable and efficient electronic devices. This guide offers an in-depth look at the essential factors that influence silicon wafer quality, the latest innovations in wafer processing, how to select the best supplier, and the future trends in wafer technology.
Key Takeaways
- High-quality silicon wafers are characterized by material purity, defect-free lattice structures, and uniform surface thickness, which are achieved through precise lapping, polishing, and grinding techniques.
- Innovations in surface-finishing solutions, such as advanced materials and processing for silicon carbide wafers, are enhancing wafer efficiency and reducing overall costs.
- When selecting a silicon wafer supplier, it is important to consider the provider’s quality standards, domestic versus international production capabilities, and the total cost of ownership and performance.
- The semiconductor industry is transitioning to larger wafer sizes and exploring the next generation of materials, such as wide-bandgap semiconductors, which offer superior performance compared to traditional silicon.
- Companies like Pureon are at the forefront of providing solutions for high-performance electronics, focusing on the efficiency and economic aspects of silicon carbide wafer processing.
Understanding Silicon Wafer Quality and Manufacturing
The Importance of Material Purity
The quest for high-quality silicon wafers begins with an understanding of the critical role that material purity plays in their performance. Impurities in the silicon can significantly alter its electronic properties, which are vital for the intended application of the wafer. Ensuring the purity of the crystal and a defect-free lattice structure is paramount for the functionality of semiconductor devices.
The process of achieving a pure and uniform silicon wafer involves meticulous steps. Surface imperfections, which can arise on both the front and rear sides of the wafer, are addressed through wafer lapping. This technique not only smooths the surface but also contributes to the overall thinness of the wafer, enhancing its quality. Backside lapping, in particular, is a delicate process that incrementally reduces the wafer’s thickness, ensuring uniformity and flatness.
In the pursuit of excellence, state-of-the-art surface labs play a crucial role. These facilities allow for comprehensive testing and trials, which are essential for validating the purity and quality of the wafers. By conducting all necessary tests in-house, suppliers can offer solutions that not only improve the quality of the wafers but also reduce process time and the cost of consumables.
Lapping, Polishing, and Grinding Techniques
The process of lapping involves the mechanical removal of excess silicon from a wafer substrate. Utilizing a pad and polishing liquid, this technique achieves a semi-reflective finish and is essential for eliminating surface faults and reducing stress from the slicing phase. Polishing, on the other hand, is a multi-faceted process combining thermal, chemical, and mechanical actions to significantly reduce surface roughness, resulting in a mirror-like finish. This meticulous process is applied to both sides of the wafer, ensuring the industry’s lowest TTV (Total Thickness Variation) values.
Surface finishing of silicon wafers is a delicate task, as not all abrasives are suitable for the job. The hardness of silicon carbide, for instance, necessitates the use of diamond suspensions. The combination of the pad and diamond suspension is a closely guarded secret, tailored to produce an exceptionally smooth surface with roughness less than five nanometers.
The table below summarizes the key aspects of each technique:
Technique | Purpose | Outcome |
---|---|---|
Lapping | Remove excess material and faults | Dull-gray, semi-reflective finish |
Polishing | Reduce surface roughness | Mirror-like finish with low TTV |
It’s crucial to select the appropriate surface-finishing solutions to improve wafer efficiency and manage costs effectively.
Identifying Defect-Free Lattice Structures
The quest for defect-free lattice structures in silicon wafers is pivotal for semiconductor performance. The organized crystal lattice structure of silicon enables efficient electron flow, which is essential for the functionality of electronic devices. Any disruptions in this structure, such as point defects or dislocations, can significantly impede carrier mobility, leading to reduced device performance.
To ensure the integrity of the lattice structure, advanced techniques like Selected-area Electron Diffraction (SAED) are employed. SAED can reveal the crystalline quality of active regions by displaying regular and bright spots, indicative of a well-ordered lattice, as opposed to diffraction rings that suggest imperfections.
The process of wafer lapping plays a crucial role in maintaining a defect-free surface. This technique incrementally removes material from the wafer, resulting in a smoother and thinner substrate. It is through meticulous processes like these that high-quality, defect-free silicon wafers are produced, setting the foundation for reliable and efficient electronic devices.
Innovations in Surface-Finishing Solutions
The Role of Surface Finishing in Wafer Efficiency
Surface finishing is a critical step in the production of high-quality silicon wafers, as it directly impacts the efficiency and performance of the final semiconductor devices. The goal of surface finishing is to achieve an excellent surface finish, typically aiming for a surface roughness of less than five nanometers. This meticulous process ensures a total thickness variation (TTV) of the wafer of less than 0.001 micron, which is vital for the uniformity and reliability of electronic components.
The process of lapping, polishing, and grinding not only removes surface imperfections but also contributes to the overall wafer thinness and flatness. Backside lapping, for instance, incrementally reduces the wafer’s thickness, enhancing its functionality. These techniques are not only about achieving a defect-free surface but also about adhering to stringent quality standards and testing protocols that confirm essential factors like resistivity, carrier lifetime, and surface properties.
Innovations in surface-finishing solutions have made the process more economical and adaptable to customer specifications. The continuous improvement in these techniques is a testament to the industry’s commitment to optimizing wafer efficiency and cost-effectiveness.
Cutting-Edge Materials and Their Applications
The evolution of materials used in the production of silicon wafers has significantly enhanced the capabilities and applications of these critical components in the semiconductor industry. Innovative materials such as silicon carbide and gallium nitride have emerged, offering superior thermal and electronic properties that are essential for high-performance electronics.
The precision in wafer slicing and polishing is paramount, and the use of a diamond saw is a testament to the industry’s commitment to excellence. The diamond saw’s hardness allows for precise and clean cuts, ensuring the thickness of the wafer surface meets exact specifications. This precision is not only crucial for the wafer’s performance but also optimizes material usage, reducing waste and production costs.
Advanced cutting systems, like those provided by Messer, play a critical role in the renewable energy sector. These systems offer reliable and consistent cutting solutions, ensuring that each component meets the stringent quality standards required for sustainable future technologies.
Advancements in Silicon Carbide Wafer Processing
Silicon carbide (SiC) wafers are at the forefront of semiconductor technology, offering high performance for power applications. Their ability to operate at higher voltages and temperatures makes them superior to traditional silicon in many aspects. The processing of SiC wafers involves a series of meticulous steps to ensure their exceptional quality and performance.
The steps in SiC wafer processing include multi-wire sawing (MWS), double side polishing (DSP) both coarse and fine, and chemical mechanical polishing (CMP). Each step is crucial in achieving the desired surface finish and structural integrity. The hardness of SiC, approximately 2,600 Vickers, necessitates the exclusive use of diamond in these processes.
Innovations in wafer processing are not just about the methods used but also about the economics of the process. Providers are focusing on reducing the cost of ownership while enhancing efficiency. The industry is eagerly anticipating the next generation of 200 mm SiC wafers, which promises to further revolutionize high-power electronics.
Selecting the Right Silicon Wafer Supplier
Criteria for High-Quality Wafer Providers
When it comes to selecting a high-quality silicon wafer provider, several criteria must be meticulously evaluated to ensure that the wafers meet the stringent requirements of semiconductor manufacturing. Consistency in wafer production is paramount; each wafer should exhibit uniform surface finish, material removal rates, and minimal sub-surface damage. This uniformity is crucial for the reliability of the wafers and, consequently, the devices they will become a part of.
The purity of the crystal and a defect-free lattice structure are fundamental indicators of wafer quality. Providers must implement rigorous wafer testing and analysis to verify these attributes. The testing process is not just a formality but a critical step that underpins the high standards expected in today’s advanced technology sectors.
Providers should also offer comprehensive surface finishing solutions, as the surface quality directly impacts the efficiency of the final semiconductor devices. Techniques such as lapping, polishing, and grinding are employed to achieve the desired surface characteristics. The table below summarizes the key aspects to consider when evaluating silicon wafer suppliers:
Aspect | Importance |
---|---|
Purity of Crystal | Essential for minimizing electronic interference |
Defect-Free Lattice | Critical for structural integrity |
Uniform Surface Finish | Necessary for device reliability |
Wafer Testing & Analysis | Ensures quality and precision |
By carefully assessing these factors, buyers can make informed decisions and select a supplier that aligns with their quality standards and production goals.
Domestic vs. International Suppliers
When selecting a silicon wafer supplier, the choice between domestic and international options is pivotal. Domestic suppliers often have a cost advantage, which is particularly attractive for manufacturing facilities and clients establishing production lines in new plants. This preference can extend to the point where domestic equipment replaces foreign alternatives in existing production lines.
However, the international landscape is shifting. Chinese companies, for instance, are increasingly competitive, offering products that can replace foreign-made ones. Despite a quality gap, these companies are rapidly improving and offering significant cost savings. For example, a high-end product from a Shenzhen-based firm is sold at just one-third the price of its Japanese competitors.
The decision between domestic and international suppliers also involves strategic considerations. A focus on ‘buying local’ and reducing dependency on foreign supply chains is becoming more pronounced. This trend is partly driven by geopolitical factors, such as U.S. sanctions, which have encouraged the use of materials from local suppliers. As a result, Chinese companies are overcoming barriers such as formulating material prescriptions, a process that once favored established international suppliers.
Evaluating Cost of Ownership and Performance
When selecting a silicon wafer supplier, it’s crucial to evaluate the cost of ownership and performance. This involves considering not just the initial purchase price, but also the long-term operational costs. Suppliers like Pureon, with their state-of-the-art surface labs, offer in-house testing that can significantly reduce both process time and consumable costs.
Efficient infrastructure integration and optimized resource use are key factors that contribute to lower costs over time. Reliable machines that adapt to rapid advancements ensure that the cost of ownership remains manageable. For instance, Messer’s commitment to minimizing costs and streamlining processes can lead to substantial savings for customers.
Understanding the Book to Bill ratios can also provide insights into production trends and demand. This ratio, calculated by dividing the value of orders received by the value of products shipped, is a critical indicator of market health. A ratio of less than one suggests a decrease in demand, which could affect pricing and availability of high-quality wafers.
The Future of Silicon Wafer Technology
Emerging Trends in Semiconductor Materials
The semiconductor industry is in a constant state of evolution, with constant research aimed at discovering innovative materials that can surpass the performance of traditional silicon. While silicon has been the cornerstone of semiconductor manufacturing, its limitations are becoming more apparent as the industry approaches the theoretical limits of silicon-based technology improvements.
One of the most notable shifts in the industry is the transition to wide-bandgap semiconductors, such as silicon carbide (SiC) and gallium nitride (GaN). These materials are gaining traction due to their ability to operate at higher voltages, frequencies, and temperatures, which is particularly beneficial for power applications. The exceptional hardness and reliability of SiC, for instance, is setting new standards in the development of high-performance electronics.
Here’s a glimpse at the emerging materials and their key advantages:
- Silicon Carbide (SiC): High voltage operation, thermal stability, and hardness.
- Gallium Nitride (GaN): High-frequency performance and efficiency.
The industry’s pivot towards these materials is not just a testament to their superior properties but also reflects a broader trend of innovation that companies like NVIDIA and Worksport are exploring to push the boundaries of semiconductor technology.
The Transition to Larger Wafer Sizes
The semiconductor industry is witnessing a significant shift towards larger silicon wafer sizes. This transition is driven by the need for greater efficiency and higher yields in chip production. As wafer sizes increase, the challenges associated with maintaining the purity and defect-free nature of the crystal lattice structure become more pronounced.
The move from traditional 150 mm wafers to 200 mm and beyond allows for more circuits per wafer, reducing the cost per chip. However, this scale-up necessitates advancements in manufacturing processes to ensure the surface finish and material removal rates remain consistent across all wafers. The table below highlights the differences in wafer sizes and their respective device yields:
Wafer Diameter (mm) | Approx. Device Yield Increase |
---|---|
150 | Baseline |
200 | 30% |
300 | 125% |
As the industry continues to push the boundaries of wafer dimensions, suppliers must adapt their lapping, polishing, and grinding techniques to accommodate the larger surface areas without compromising quality. The goal is to achieve a uniform thickness and a high-quality surface finish, which are critical for the subsequent steps in semiconductor device fabrication.
Anticipating the Next Generation of Silicon Carbide Wafers
As the semiconductor industry looks forward, the anticipation for the next generation of silicon carbide (SiC) wafers is palpable. These future wafers promise to further empower sustainable and efficient technologies, with industry experts like Brakeville hinting at product launches as early as 2024, focusing on 1,200 V modules. The evolution of SiC wafers is driven by the need for high-performance electronics that can withstand extreme conditions while maintaining efficiency and reliability.
The upcoming 200 mm SiC wafers, as mentioned by Bollina, are a testament to the industry’s commitment to innovation and cost-effectiveness. The processing of these wafers is intricate, involving steps such as multi-wire sawing (MWS), double side polishing (DSP), and chemical mechanical polishing (CMP). Each step is crucial in ensuring the wafers meet the stringent quality standards required for high-power applications.
The table below summarizes the key processing steps for SiC wafers:
Process Step | Description |
---|---|
MWS | Multi-wire sawing for slicing wafers |
DSP Coarse | Initial double side polishing |
DSP Fine | Final double side polishing to refine surface |
CMP | Chemical mechanical polishing for ultimate smoothness |
As we look to the horizon, the semiconductor industry continues to push the boundaries of what’s possible with SiC technology. The focus on materials that can only be treated with diamond, due to SiC’s exceptional hardness, underscores the relentless pursuit of excellence in surface finishing and overall wafer quality.
Conclusion
In the quest for high-quality silicon wafers, understanding the intricate processes of manufacturing and finishing is crucial. As we’ve explored, the journey from pure semiconductor material to a polished wafer involves meticulous steps such as lapping, polishing, and grinding, ensuring the removal of surface imperfections and achieving a defect-free lattice structure. With the industry moving towards larger 200 mm wafers and embracing materials like silicon carbide for their superior performance, the importance of cost-effective and efficient surface finishing solutions cannot be overstated. Companies like Pureon are at the forefront of providing these solutions, catering to the evolving needs of semiconductor manufacturing. Whether for cutting-edge electronics or extreme applications, the selection of the right silicon wafer is a pivotal decision that impacts the quality and integrity of the final product. As advancements continue, staying informed about the latest techniques and materials will be indispensable for those seeking to procure the best silicon wafers on the market.
Frequently Asked Questions
What determines the quality of a silicon wafer?
The quality of a silicon wafer is mostly determined by the purity of the crystal, the defect-free nature of the lattice structure, the uniform thickness, and the surface quality.
Why is material purity important in wafer manufacturing?
Material purity is crucial because impurities can cause defects in the lattice structure, affecting the performance and reliability of the semiconductor devices created on the wafer.
What are the techniques used to achieve a smooth wafer surface?
Techniques such as lapping, polishing, and grinding are used to achieve a very even and smooth surface on silicon wafers.
How does surface finishing improve wafer efficiency?
Surface finishing solutions, such as lapping and polishing, remove imperfections and ensure a high-quality finish, which is vital for the efficiency and performance of the wafers.
What should I look for when selecting a silicon wafer supplier?
When selecting a silicon wafer supplier, look for criteria such as material quality, processing capabilities, cost of ownership, performance, and whether they can meet your specific needs.
What are some emerging trends in silicon wafer technology?
Emerging trends include the transition to larger wafer sizes, advancements in materials like silicon carbide, and the development of the next generation of wafers for high-performance electronics.