The Essential Guide to Wafer Components: Functions and Fabrication
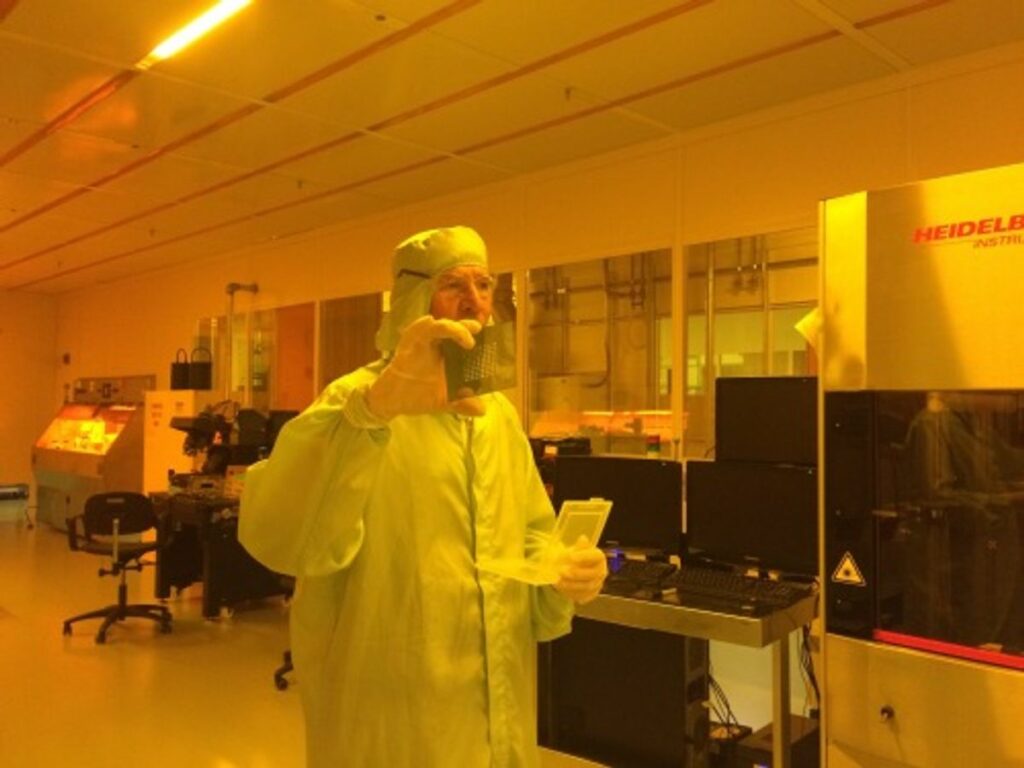
The Essential Guide to Wafer Components: Functions and Fabrication delves into the intricate world of semiconductor manufacturing, focusing on the pivotal role of wafer components. This guide offers an in-depth understanding of the various types of wafers, their specific uses, and how material selection impacts application performance. It also unravels the complexities of the wafer manufacturing process, from the initial selection of silicon to the precision of photolithography and the exhaustive steps involved in wafer testing and analysis. For professionals in the semiconductor industry, this guide is an invaluable resource for ensuring the quality and reliability of semiconductor devices.
Key Takeaways
- Selecting the appropriate wafer is critical, with material and feature considerations directly affecting application performance.
- The wafer manufacturing process is a meticulous journey from sand to ultra-pure silicon, with photolithography playing a key role in circuit pattern creation.
- Wafer testing encompasses visual inspections for physical defects, electrical testing for functionality, and advanced imaging for detailed analysis.
- Best practices in wafer testing and analysis, such as employing defect wafers and short loop wafers, are essential for high-quality semiconductor production.
- Attention to detail and precision in wafer test analysis, including Lot Genealogy and various imaging techniques, enhance the reliability of semiconductor devices.
Understanding Wafer Components and Their Roles
Types of Wafers and Their Specific Uses
Selecting the appropriate wafer is a pivotal step in semiconductor manufacturing. Different applications necessitate wafers with distinct properties, such as material composition and structural features. These characteristics directly influence the wafer’s performance in its intended environment.
Semiconductor wafers come in various types, each tailored for particular uses. For instance, Gallium Arsenide wafers are renowned for their remarkable direct bandgap properties, making them ideal for RF devices and microwave amplifiers. Silicon Carbide wafers, with their robust tetrahedral bonding, are sought after for high-power and high-temperature applications.
In the realm of semiconductor testing, specialized wafers like dummy, defect, and short-loop wafers play crucial roles. Dummy wafers are used to calibrate equipment, defect wafers help in understanding the impact of imperfections, and short-loop wafers accelerate the identification of potential issues under specific conditions.
Material Considerations for Wafer Selection
Selecting the appropriate material for wafer fabrication is a pivotal step in semiconductor manufacturing. Different materials can withstand varying degrees of thermal and chemical stress, which directly influences the wafer’s performance in specific applications. For instance, materials like PEEK and PPS are known for their high standards of precision and ability to endure extreme conditions.
The choice of wafer material also impacts the manufacturing process itself. Silicon is the most commonly used material due to its excellent semiconducting properties and abundance. However, alternative materials such as gallium arsenide or silicon carbide may be chosen for applications requiring higher frequencies or greater thermal conductivity.
Here is a comparison of common wafer materials and their key properties:
Material | Thermal Conductivity | Frequency Range | Application Examples |
---|---|---|---|
Silicon | Moderate | Up to 100 GHz | General Electronics |
GaAs | High | Up to 250 GHz | High-speed Devices |
SiC | Very High | Up to 300 GHz | Power Electronics |
Understanding the nuances of each material and its suitability for the intended application is essential for optimizing the performance and reliability of semiconductor devices.
The Impact of Wafer Features on Application Performance
The performance of semiconductor devices is intricately linked to the features of the silicon wafers they are built on. Each characteristic, from surface smoothness to electrical properties, plays a pivotal role in the final device’s functionality. For instance, even minor surface defects can precipitate device failures or suboptimal performance, underscoring the need for meticulous wafer inspection and testing.
Material purity and structural integrity are paramount in wafer selection. A wafer’s ability to perform under various environmental conditions or stress levels is determined by these attributes. This is where short-loop wafers come into play, providing valuable feedback on semiconductor behavior under specific circumstances, thereby informing enhancements in manufacturing processes.
As we look to the future, the semiconductor industry continues to evolve, with nanotechnology paving the way for more precise 3D integration testing. This progression promises smaller, more powerful chips with increased functionality, making the role of wafer features even more critical in achieving high-performance devices.
The Wafer Manufacturing Process: From Sand to Silicon
Silicon Wafer Selection: The Foundation of Semiconductor Devices
The selection of a silicon wafer marks the inception of the semiconductor device fabrication process. Choosing the right wafer is pivotal, as it lays the groundwork for the device’s performance and reliability. Engineers must consider the wafer’s resistivity, which is a key factor in determining its suitability for various applications. The right resistivity ensures that the wafer meets the specific electrical requirements of the intended device.
Silicon wafers are sourced from high-purity silica sand and undergo a rigorous purification process. This meticulous approach to purification is necessary to achieve the ultra-pure levels required for semiconductor manufacturing, with impurity levels reaching as low as a few parts per billion. The quality of the silicon wafer is paramount, as it directly influences subsequent steps in the manufacturing process, such as photolithography.
The following table outlines the typical resistivity ranges for silicon wafers used in different semiconductor devices:
Device Type | Resistivity Range (Ohm-cm) |
---|---|
High-power devices | > 0.01 – 0.05 |
Standard ICs | 1 – 100 |
High-frequency devices | > 1000 |
It is essential to select a wafer with the appropriate resistivity to ensure optimal device functionality. This selection is a crucial yet oft-overlooked step in the integrated circuit design and manufacturing process.
Purification of Silicon: Achieving Ultra-Pure Levels
The journey from sand to the ultra-pure silicon necessary for semiconductor devices is a testament to human ingenuity in materials science. Silicon, sourced from sand, undergoes meticulous purification to achieve levels of purity where impurities are measured in parts per billion. This process is critical as even the slightest impurities can significantly affect the performance of the final semiconductor devices.
The purification process typically involves a series of complex chemical reactions and physical treatments. One such method is the reaction of hydrogen with trichlorosilane, a silicon compound, at high temperatures. This reaction is part of a sequence that ensures the resulting silicon is of the highest purity required for wafer fabrication.
To illustrate the importance of this process, consider the following points:
- Ultra-pure silicon is the foundation of all semiconductor devices.
- The purity level directly impacts the electrical properties of the wafers.
- Advanced technologies demand silicon with fewer and fewer impurities.
Achieving such high purity levels is not only a matter of chemical precision but also of maintaining stringent controls throughout the manufacturing process to prevent contamination.
Photolithography: Carving Circuit Patterns with Precision
Photolithography stands as a pivotal process in the wafer manufacturing journey, where the intricate circuit patterns essential for semiconductor functionality are etched onto the silicon substrate. The precision of this step is critical, as it defines the pathways for electrical currents and the overall efficacy of the electronic device.
The process begins with the application of a light-sensitive photoresist to the wafer’s surface. A mask, designed with the desired circuit pattern, is then aligned over the wafer. Exposing the assembly to light causes the photoresist to harden in the exposed areas, while the unexposed sections remain soluble.
Subsequent steps involve:
- Developing the photoresist to remove the soluble parts, revealing the pattern.
- Etching the exposed silicon areas to create the physical circuitry.
- Stripping away the remaining photoresist, leaving the intricate circuit design imprinted on the wafer.
This meticulous process requires not only precision but also a controlled environment to prevent any contamination that could impair the wafer’s performance.
Comprehensive Steps of Wafer Testing
Visual Inspection: Identifying Physical Defects
Visual inspection serves as a critical first line of defense in wafer testing, where each wafer undergoes meticulous scrutiny for visible imperfections. Technicians meticulously search for cracks, scratches, or any surface irregularities that could compromise the wafer’s performance. This step is essential because physical defects can significantly impact yield and manufacturing costs.
The process of visual inspection has evolved with technology. Automated Optical Inspection (AOI) systems have largely supplanted manual inspections, which are less practical for the intricate and minute details of modern wafers. AOI leverages optical principles, combining image capture with software analysis to identify and categorize defects efficiently. Inspections are typically performed both before and after reflow soldering, optimizing the timing for defect correction when costs are lowest and efficiency is highest.
The following table summarizes the key aspects of visual inspection in wafer testing:
Aspect | Description |
---|---|
Focus | Detection of physical defects such as cracks and scratches |
Methods | Transition from manual to Automated Optical Inspection (AOI) |
Timing | Conducted pre- and post-reflow soldering for optimal defect management |
Impact | Physical defects directly affect yield and cost-effectiveness |
As the complexity of wafers increases, especially at nodes of 10 nm and below, the challenge of identifying and classifying defects grows. The integration of conventional optical inspection with cutting-edge techniques like nanophotonics and deep learning is opening new avenues for enhancing the defect detection process.
Electrical Testing: Assessing Device Functionality
Electrical testing is a pivotal phase in the semiconductor manufacturing cycle, ensuring that integrated circuits (ICs) perform correctly within their intended operating environments. This process involves applying electrical signals to a chip and measuring the output, comparing it against predefined criteria to assess performance. Specialized equipment, known as automated test equipment (ATE), is utilized for this purpose.
During wafer probing, a probe card is employed to test the electrical properties of the circuits on the wafer. Each die is meticulously examined to ensure it conducts electricity properly, which is crucial for identifying any electrical issues at an early stage. The following list outlines the stages where testing commonly occurs:
- Wafer Probing
- Die Test
- Packaging and Final Testing
Ensuring that semiconductor devices meet the required performance, functionality, and reliability specifications is essential before they reach the market. This testing phase is integral to maintaining high standards and preventing defective products from advancing in the manufacturing process.
Advanced Imaging Techniques: SEM and FIB Analysis
The intricacies of wafer testing are illuminated by advanced imaging techniques that provide a window into the microscopic world of semiconductors. Scanning Electron Microscopy (SEM) offers high-resolution imaging, revealing the topography and composition of wafer surfaces with remarkable clarity. This technique is complemented by Focused Ion Beam (FIB) microscopy, which allows for precise material manipulation and in-depth defect analysis at the nanoscale.
Employing these techniques, engineers can identify and characterize defects that would otherwise be invisible to the naked eye. For instance, FIB can be used to create cross-sections of semiconductor devices, enabling detailed examination of internal structures. The table below summarizes the capabilities of SEM and FIB in wafer analysis:
Technique | Resolution | Application |
---|---|---|
SEM | Sub-nanometer | Surface topography |
FIB | Nanometer-scale | Material manipulation |
The fusion of SEM and FIB technologies has become a cornerstone in the quest for perfection in semiconductor manufacturing. By leveraging these tools, manufacturers can ensure that each wafer meets the stringent quality standards required for high-performance electronics.
Wafer Testing and Analysis: Ensuring Quality and Precision
The Role of Lot Genealogy in Wafer Final Test
Lot Genealogy, often referred to as GDBN (Genealogy Database Network), is a critical aspect of the wafer final test phase. It ensures traceability and accountability throughout the semiconductor manufacturing process. By meticulously tracking each wafer lot from start to finish, manufacturers can pinpoint the origin of defects and improve overall yield.
The Wafer Lot Disposition Control tool exemplifies the integration of lot genealogy in modern testing environments. This tool streamlines the process of wafer lot releases, retests, and holds, enhancing operational efficiency. Here’s how it contributes to the process:
- Automated decision-making based on test data
- Reduction in time to market
- Improved quality control
Understanding the test results in-depth is not just about identifying defects; it’s about transforming data into actionable insights. This deep dive into the data helps to ensure that each wafer not only meets the current standards but also drives the continuous improvement of semiconductor manufacturing processes.
Employing Defect Wafers for Performance Insights
Defect wafers, intentionally embedded with known imperfections, are a critical tool for semiconductor manufacturers. By introducing pattern irregularities or material impurities, engineers can simulate potential issues and understand their impact on wafer performance. This proactive approach aids in identifying and rectifying problems early in the manufacturing process, ultimately enhancing the quality of the final product.
The analysis of defect wafers involves a meticulous examination of how these intentional flaws affect the device’s functionality. It’s a process that transforms raw data into actionable insights, ensuring that each wafer not only meets the industry’s stringent standards but also contributes to the ongoing improvement of semiconductor fabrication techniques.
To illustrate the importance of defect wafers in test analysis, consider the following roles they play in the semiconductor industry:
- Monitor Wafers: These wafers are used to assess the health of the fabrication process, undergoing the same steps as product wafers.
- Dummy Wafers: Serving as placeholders, they ensure equipment calibration and readiness for processing actual wafers.
- Defect Wafers: Specifically created to study the effects of known defects on wafer performance.
Each type of test wafer, including defect wafers, is indispensable for maintaining high standards in semiconductor testing and production.
Short Loop Wafers: Accelerating Defect Identification
Short loop wafers are a specialized tool in the semiconductor industry, designed to accelerate the identification of defects and optimize the manufacturing process. Unlike standard test wafers, these are used to quickly evaluate specific aspects of semiconductor performance, particularly under unique environmental conditions or stress levels.
The use of short loop wafers allows for rapid feedback on the production line, enabling adjustments to be made in real-time. This leads to a more efficient manufacturing process and ultimately, a higher quality product. The table below outlines the key differences between short loop wafers and standard test wafers:
Wafer Type | Testing Focus | Feedback Speed |
---|---|---|
Short Loop Wafers | Specific performance aspects | Rapid |
Standard Test Wafers | General functionality and defects | Standard |
Incorporating short loop wafers into the testing regime is part of a broader strategy that includes wafer test analysis. This analysis goes beyond mere observation of defects; it involves a deeper examination of test results to understand the underlying causes of performance issues, turning data into actionable insights.
Best Practices in Wafer Test Analysis
The Importance of Precision and Attention to Detail
In the realm of wafer testing and analysis, precision and attention to detail are paramount. The intricate nature of semiconductor devices demands that each component be scrutinized with the utmost care. This is akin to dividing a human hair into thousands of segments, each with a specific width, and then further subdividing those segments.
Ensuring quality control is not just about routine inspections; it involves regular calibration of equipment to maintain testing accuracy and consistency. Tools such as wafer probers and probe stations are pivotal in accurately assessing each wafer’s performance. The following are key practices that underscore the importance of precision:
- Routine inspections to detect any physical or performance anomalies.
- Regular calibration of testing equipment to ensure accuracy.
- Effective data analysis to identify issues and discern trends.
- Proficient troubleshooting skills to resolve any detected problems.
These practices are not just about maintaining standards; they are about guaranteeing the long-term reliability of semiconductor products. By employing methods like Statistical Process Control (SPC), Failure Mode and Effects Analysis (FMEA), and Design of Experiments (DOE), we can strive for perfection in the wafer testing process.
Key Testing Methods and Their Contributions to Quality
The semiconductor industry’s commitment to quality standards is evident in the rigorous testing methods employed. These methods are not only crucial for ensuring the functionality and reliability of wafer components but also play a significant role in reducing the manufacture of faulty wafers, ultimately lowering material waste and production costs.
Key testing methods include Statistical Process Control (SPC), Failure Mode and Effects Analysis (FMEA), and Design of Experiments (DOE). Each of these contributes uniquely to the quality assurance process:
- SPC monitors process behavior using control charts, enabling early detection of variations.
- FMEA identifies potential failure modes and their effects, facilitating proactive improvements.
- DOE helps in understanding the factors affecting process performance and their interactions.
The advancement of testing methodologies, such as the integration of AI and machine learning, continues to enhance the efficiency and effectiveness of these processes. Ensuring quality control through routine inspections and regular equipment calibration is key to reliable results. Tools such as wafer probers and probe stations are fundamental in accurately assessing each wafer’s performance. Moreover, effective data analysis is crucial for pinpointing issues and trends, while troubleshooting skills are necessary to resolve any problems that arise.
Interpreting Data for Enhanced Semiconductor Reliability
The interpretation of wafer test data is a critical step in the semiconductor manufacturing process. Reliability testing is a key aspect, where wafers are subjected to various stress conditions to predict their lifespan and performance. This ensures that semiconductors will perform reliably in real-world conditions.
Integration with the manufacturing workflow is essential, as the feedback from testing informs both designers and manufacturers. It highlights potential areas for improvement in chip design and fabrication processes, creating a feedback loop crucial for advancing semiconductor technology and increasing yields.
Statistical tools such as Statistical Process Control (SPC), Failure Mode and Effects Analysis (FMEA), and Design of Experiments (DOE) are employed to maintain quality standards. These tools help in analyzing wafer test results, ensuring the long-term reliability of semiconductor products, and safeguarding the functional integrity of the devices.
Conclusion
Throughout this essential guide, we have delved into the intricate world of wafer components, emphasizing their pivotal role in the semiconductor industry. From the meticulous selection of silicon wafers to the rigorous steps of wafer testing, each phase is instrumental in ensuring the functionality and reliability of electronic devices that permeate our daily lives. The fabrication process, marked by purification and photolithography, sets the stage for high-quality wafers, while the subsequent testing and analysis guarantee that only the best-performing wafers make it to production. As we’ve seen, the choice of wafer and the adherence to best practices in testing are not just technical decisions but are also critical to the advancement and sustainability of modern technology. The semiconductor industry’s commitment to precision and quality is a testament to the importance of these processes, and this guide serves as a comprehensive resource for professionals seeking to enhance their understanding and expertise in wafer components.
Frequently Asked Questions
What is wafer testing and why is it important?
Wafer testing is a key step in semiconductor manufacturing, where the quality and performance of wafers, the thin slices of silicon used to make electronic circuits, are checked. It is vital because minor errors can significantly impact the functionality of semiconductor devices.
What are the different types of wafers used in semiconductor testing?
In semiconductor testing, different types of test wafers are used, such as monitor, dummy, defect, and short loop wafers. Each type serves a distinct purpose in evaluating and ensuring the quality and reliability of the semiconductor products.
What is the significance of the photolithography process in wafer manufacturing?
Photolithography is a crucial step in wafer manufacturing where a circuit pattern is precisely carved onto the wafer. It’s essential for defining the intricate structures of semiconductor devices and ensuring their proper function.
How does material selection affect wafer performance?
Choosing the right material for a wafer is critical as it affects the wafer’s suitability for specific applications. Material properties such as purity, crystal structure, and thermal conductivity all impact the performance and reliability of the final semiconductor device.
What role do defect wafers play in semiconductor manufacturing?
Defect wafers are intentionally created with known defects to study their impact on wafer performance. This helps manufacturers detect and correct issues early in the manufacturing process, leading to better quality control and product reliability.
Why is precision and attention to detail crucial in wafer test analysis?
Precision and attention to detail are crucial in wafer test analysis because they ensure the reliability and performance of semiconductor devices. Accurate testing and data interpretation are necessary to meet the high standards of quality and functionality required in modern technology.