The Essential Toolbox: Must-Have Semiconductor Tools for Today’s Engineers
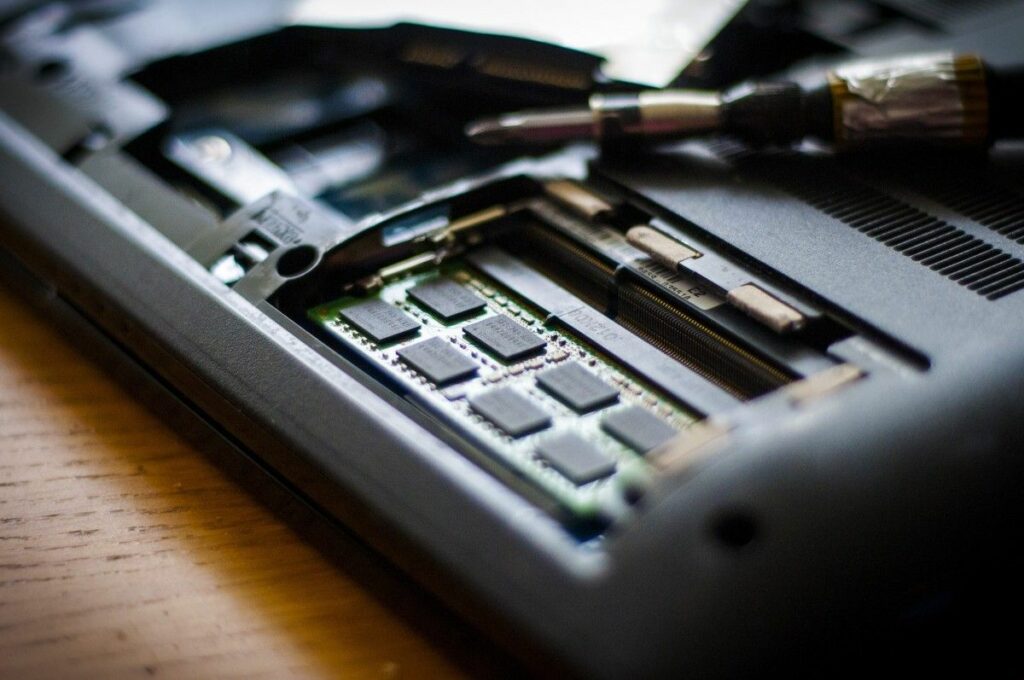
In the dynamic and intricate field of semiconductor engineering, having the right tools is critical for success. Engineers today must navigate through complex design challenges, stringent testing requirements, and relentless pursuit of quality and yield improvements. This article, ‘The Essential Toolbox: Must-Have Semiconductor Tools for Today’s Engineers,’ delves into the essential tools and resources that are indispensable for semiconductor professionals seeking to excel in their field.
Key Takeaways
- Advanced calculation tools like ASIC, IC Packages, and Die Per Wafer calculators are foundational for cost and resource estimation in semiconductor projects.
- Design and testing software, including Bonding Diagram Tools and Semiconductor Testing Software, are crucial for ensuring the integrity and functionality of semiconductor components.
- Yield enhancement and quality management software address the industry’s need for high yield and reliability, particularly in sectors like aerospace defense.
- Collaboration resources such as consultant directories and vendor lists are key for navigating the complex semiconductor ecosystem and leveraging external expertise.
- Data management and analysis tools enable optimization across the semiconductor manufacturing process, ensuring efficient operations and improved outcomes.
Advanced Calculation Tools for Semiconductor Engineering
ASIC Price Calculator
Understanding the cost implications of ASIC production is crucial for semiconductor engineers. The ASIC Price Calculator simplifies this process by providing an estimate of the unit cost for your specific ASIC design. It takes into account various factors such as die size, yield, and packaging options.
To get started, you might want to consider the following steps:
- Determine the specifications of your ASIC, including the die size and required packaging type.
- Use the calculator to estimate the die per wafer and the associated costs.
- Obtain price quotes from multiple vendors for a comprehensive cost analysis.
The tool also allows for comparisons between different packaging types, such as the commonly used Quad Flat Package (QFN). By leveraging this calculator, engineers can make informed decisions on the financial feasibility of their ASIC projects.
IC Packages Price Calculator
The IC Packages Price Calculator is an indispensable tool for engineers and procurement specialists in the semiconductor industry. It provides a streamlined way to estimate the cost of various IC packaging options, which is crucial for budgeting and strategic planning. The calculator takes into account factors such as package type, size, and quantity, offering a comprehensive pricing model.
When using the calculator, it’s important to consider the hidden costs and tradeoffs in IC quality. Balancing reliability against cost is becoming more difficult as chip complexity increases and devices become more domain-specific. This tool helps in making informed decisions by providing cost estimates that factor in these complexities.
To get started, simply select the desired package type, such as Quad Flat Package (QFN), and input the required parameters. The calculator will then generate a price estimate, which can be compared across multiple vendors. For a more detailed analysis, users can obtain three price quotes from ASIC design companies, semiconductor foundries, IC packaging specialists, IP core vendors, and IC test houses.
Die Per Wafer Calculator
The Die Per Wafer Calculator is an indispensable tool for semiconductor engineers, allowing for the precise estimation of how many dies can be obtained from a single wafer. This calculation is critical for cost analysis and production planning, ensuring that resources are utilized efficiently.
When using the Die Per Wafer Calculator, engineers must input parameters such as wafer diameter, die size, and edge exclusion. The calculator then uses these inputs to determine the maximum number of dies that can be produced, taking into account the geometric layout and the space lost to saw lanes.
For example, a typical calculation might look like this:
Wafer Diameter (mm) | Die Size (mm^2) | Edge Exclusion (mm) | Dies Per Wafer |
---|---|---|---|
200 | 50 | 2 | 100 |
This table illustrates a simplified scenario where a 200mm wafer with 50mm^2 die size and 2mm edge exclusion can yield 100 dies. The actual calculation can be more complex, involving additional factors such as kerf width and wafer map defects.
Design and Testing Software Suites
Bonding Diagram Tool
In the realm of semiconductor engineering, the ability to visualize interconnections within IC packages is crucial. The Bonding Diagram Tool serves as an indispensable resource for engineers looking to map out the intricate wiring of devices such as QFNs and BGAs. This tool not only aids in the design phase but also enhances understanding and communication across teams.
The tool’s interface is designed for ease of use, offering features that cater to a wide range of supported devices. Engineers can select from various sections such as Diagram, Features, Supported Devices, and System Requirements to tailor the tool to their specific needs. Applications of the Bonding Diagram Tool extend across different sectors, including automotive, where it is used to create general block diagrams.
Here is a brief overview of the tool’s capabilities:
- Diagram: Visualize and create wiring diagrams for IC packaging.
- Features: Access a suite of functionalities tailored to semiconductor design.
- Supported Devices: Check compatibility with a variety of IC types.
- System Requirements: Ensure your setup meets the necessary specifications for optimal performance.
- Applications: Explore the tool’s utility in various industry applications.
CPU IP Core Search Engine
In the rapidly evolving field of semiconductor engineering, the CPU IP Core Search Engine has become an indispensable tool for engineers. It streamlines the process of finding and comparing intellectual property (IP) cores that are essential for designing cutting-edge System on Chips (SoCs). With a vast array of options, from RISC-V architectures to specialized DSP cores, the search engine helps in pinpointing the perfect match for specific project requirements.
The search engine not only provides access to a comprehensive database of CPU and peripheral IPs but also offers valuable resources such as die per wafer calculators and ASIC price estimators. Engineers can leverage this tool to obtain multiple price quotes from ASIC design companies, semiconductor foundries, and IP core vendors, ensuring the best possible deal for their projects.
Here’s a quick look at some of the CPU and peripherals IP available:
- Clock Generator
- DMA Controller
- DSP
- Interrupt Controller
- IO Controller
- LCD Controller
- NoC (Network on Chip)
- Peripheral Controller
- Receiver/Transmitter
- Security
Selecting the right IP core is crucial for the success of any semiconductor project. The CPU IP Core Search Engine aids in making informed decisions by providing detailed information on each IP, including performance metrics, licensing terms, and support services.
Semiconductor Failure Analysis Software
In the fast-paced world of semiconductor engineering, failure analysis software has become an indispensable tool. These sophisticated programs assist engineers in identifying, analyzing, and resolving failures in semiconductor devices. With the pressure building on failure analysis labs to emulate the efficiency of fabrication facilities, these software solutions offer higher accuracy in pinpointing defects, thereby accelerating the time-to-market for new devices.
The software typically includes features such as automated test pattern generation, fault simulation, and diagnostic reporting. Here’s a brief overview of the core functionalities:
- Automated Test Pattern Generation (ATPG): Creates test patterns to detect and locate faults within the IC.
- Fault Simulation: Simulates various fault conditions to predict the behavior of the device under test.
- Diagnostic Reporting: Provides detailed reports on the nature and location of the detected faults, aiding in quicker resolution.
By integrating these tools into their workflow, engineers can significantly reduce the time spent on manual analysis, thus optimizing the failure analysis process and improving overall device reliability.
Semiconductor Testing Software
In the realm of semiconductor engineering, testing software is a cornerstone for ensuring the reliability and performance of integrated circuits (ICs). This software encompasses a range of tools designed to simulate, analyze, and verify semiconductor devices under various conditions before they are deployed in the field.
Key features of semiconductor testing software may include automated test pattern generation, fault simulation, and real-time analysis. These capabilities are crucial for identifying potential issues early in the development cycle, which can save significant time and resources.
Feature | Description |
---|---|
Automated Test Pattern Generation | Generates test vectors to simulate IC functionality. |
Fault Simulation | Predicts potential faults in IC designs. |
Real-Time Analysis | Provides immediate feedback during testing processes. |
Engineers rely on this software to streamline the testing phase, leading to a more efficient path from design to production. With the constant evolution of semiconductor technology, testing software must also adapt, integrating the latest methodologies to tackle new challenges in IC testing.
Yield Enhancement and Quality Management
Semiconductor Yield Analysis Software
In the realm of semiconductor manufacturing, yield analysis software plays a pivotal role in identifying and addressing the root causes of yield losses. This software is integral to the implementation of Statistical Process Control (SPC) strategies, which are essential for maintaining high-quality production standards.
Key features of yield analysis software include automated yield monitoring, detailed reporting and analysis, and data archiving. These tools enable engineers to track yield performance over time, identify trends, and make informed decisions to enhance the manufacturing process. For instance, yieldWerx offers a comprehensive suite of enterprise modules designed to optimize yield and maximize test efficiency.
Choosing the right yield analysis software involves considering various factors such as the specific data requirements of the semiconductor manufacturing process, the ability to integrate with existing systems, and the flexibility to adapt to different yield calculation methodologies. Explore features, benefits, and approaches to utilizing semiconductor Statistical Process Control software to choose the right one to maximize quality.
Semiconductor Yield Enhancement Software
In the competitive landscape of semiconductor manufacturing, yield enhancement is a critical focus area. Software solutions dedicated to this purpose are indispensable for engineers looking to improve the efficiency and output of their production processes. One such tool is yieldWerx, a platform renowned for its comprehensive approach to managing and optimizing yield rates.
The software provides a suite of features that address various aspects of yield management. For instance, it offers automated yield monitoring, detailed reporting and analysis, and data archiving capabilities. These functionalities are crucial for identifying and mitigating the root causes of yield losses, which can range from process variations to equipment malfunctions.
Moreover, yieldWerx’s flexibility in yield calculation and its ability to integrate with other semiconductor data systems make it a versatile tool for engineers. It supports the implementation of Six Sigma and SPC (Statistical Process Control) methodologies, which are essential for achieving high-quality production standards. The platform’s adaptability ensures that it can meet the specific needs of different segments within the industry, from OSATs (Outsourced Semiconductor Assembly and Test) to fabaless companies.
To illustrate the capabilities of yield enhancement software, consider the following table showcasing yieldWerx’s key modules:
Module | Function |
---|---|
Automated Yield Monitoring | Monitors yield across various production stages |
Reporting & Analysis | Provides detailed insights into yield data |
Data Archiving & Purge | Ensures historical data is stored and managed efficiently |
Lot Genealogy | Tracks the history and quality of wafer lots |
Embracing such advanced tools is essential for maintaining a competitive edge and driving innovation in semiconductor manufacturing.
Aerospace Defense Semiconductor Quality Assurance
In the high-stakes field of aerospace defense, semiconductor quality assurance is paramount. Ensuring the reliability and performance of semiconductors is critical for applications where failure is not an option. This involves rigorous testing and management practices that go beyond standard industry requirements.
Quality Engineers and Product Engineers play a vital role in this process, utilizing specialized software to track and analyze every aspect of semiconductor production. From Automated Testing Systems (ATS) to big data analytics, these tools help identify and rectify yield issues, ensuring that each component meets the stringent standards of the aerospace defense industry.
The table below outlines key metrics and tools used in aerospace defense semiconductor quality assurance:
Metric/Tool | Description |
---|---|
Outlier Detection | Identifies components that deviate from standard parameters. |
Part Average Test (PAT) | Assesses the average performance of parts to detect issues. |
Process Capability Index (CPK) | Measures process stability and capability. |
Real-time Yield Issue Tracking | Monitors yield-related problems as they occur. |
Root Cause Analysis | Determines the origins of yield losses for rectification. |
Adherence to these practices and the use of advanced management software ensure the highest quality of semiconductors for aerospace defense applications, where the cost of failure is immeasurably high.
Collaboration and Consultation Resources
Find Consultants
In the fast-paced world of semiconductor engineering, having access to expert consultants can be the difference between a project’s success or failure. Finding the right consultant is crucial, as they bring specialized knowledge that can streamline the development process, identify potential issues early on, and suggest innovative solutions.
Platforms like Semipedia and Freelancers databases offer a structured way to connect with professionals. Whether you’re looking for a freelancer or a more established consulting firm, these resources provide a variety of options:
- Semipedia: Access to tools like Bonding Diagram and CPU IP Core Search Engine, and free consulting services.
- Freelancers: A database with over 200 members where you can hire a freelancer or list yourself as one.
- Pricing: Information on how to get listed and advertise your services.
For those seeking comprehensive services, platforms like ASIC Services and IP Cores Vendors offer a range of categories from design to testing, ensuring you find the vendor that fits your project’s specific needs. Remember, the right consultancy can help you navigate the complexities of semiconductor strategies and chip architecture, much like the 3D silicon consultants at Cambridge Consultants.
Semiconductor Services Vendors
In the intricate world of semiconductor engineering, Semiconductor Services Vendors play a pivotal role in ensuring that the complex processes from design to production are executed seamlessly. These vendors offer a comprehensive range of services that cater to various stages of semiconductor manufacturing, including ASIC design, IC layout, and ASIC verification, among others.
The following is a list of services provided by these vendors:
- ASIC Design
- IC Layout
- ASIC Verification
- Semiconductor Foundries
- IC Packaging
- IC Testing
- IC Supply Chain
- IC Qualification
- IC Failure Analysis
Selecting the right vendor is crucial for the success of a semiconductor project. It involves evaluating the vendor’s expertise, capacity, and previous track record. For instance, SkyWater Technology, a U.S. semiconductor manufacturer, is recognized for streamlining the concept-to-production journey and is a DMEA-accredited Trusted supplier. Partnering with a vendor that aligns with your project’s requirements and quality standards is essential for achieving optimal results and maintaining a competitive edge in the market.
IP Vendors
In the realm of semiconductor engineering, IP vendors play a crucial role by providing a wide array of intellectual property cores that are essential for modern chip designs. These vendors offer solutions ranging from IOs and library IP, such as ESD, GPIO, and standard cell libraries, to complex memories and PHY IP including DDR, EEPROM, and various flash controllers.
Selecting the right IP vendor can be a daunting task, but resources like the ‘List of semiconductor IP core vendors‘ on Wikipedia can serve as a starting point. The list includes notable vendors in the business of licensing IP cores, covering a broad spectrum of technologies.
When considering IP vendors, engineers should evaluate several factors:
- Compatibility with the foundry’s process
- Compliance with industry standards
- Support and maintenance services
- Licensing terms and costs
Welcome new vendors like GEDEC and Advanced Sensor Integrations, who join established players in offering innovative solutions to the semiconductor industry.
Data Management and Analysis for Optimization
Metrology and Defect Data Management
In the realm of semiconductor manufacturing, metrology and defect data management are critical for maintaining high standards of quality and efficiency. These systems are designed to capture and analyze vast amounts of data, ensuring that any deviations from the norm are quickly identified and addressed.
The process begins with meticulous data collection, which is the cornerstone of wafer testing analysis. Accurate and comprehensive data must be gathered from each wafer test, encompassing electrical measurements and defect analysis. Tools like yieldWerxTM facilitate the automation of data collection, allowing for the efficient organization and analysis of information from wafer probers and chip testers.
To illustrate the importance of these tools, consider the following table which outlines key components of a robust metrology and defect data management system:
Component | Function |
---|---|
Inspect Image Management | Manages and analyzes images for defects |
Semiconductor Optical Memory Mapping | Tracks and records optical data |
Wafer Prober Control Module | Oversees wafer probing operations |
Part Average Test (PAT) | Analyzes average performance of parts |
By leveraging such systems, engineers can ensure that the semiconductor manufacturing process is not only precise but also optimized for the highest yield possible.
Semiconductor Data Integration
In the realm of semiconductor engineering, data integration is pivotal for streamlining processes and enhancing decision-making. It involves the consolidation of data from various stages of the semiconductor manufacturing process, ensuring that information is accessible and actionable across different work centers.
Key components of semiconductor data integration include:
- Wafer Lot Disposition and Control Tool
- Self Reporting & Executive Dashboard
- Part Average Test (PAT)
- Smart Wafer Merge
- Statistical Process Control (SPC/SBL/SYL)
- Wafer or Reticle Map Definition
This integration allows for real-time tracking of yield issues, facilitating the rectification of yield losses and identification of their root causes. By leveraging big data analytics and automated reporting, engineers can maintain a high process capability index (CPK) and ensure that semiconductor data requirements are met efficiently.
Cross Work Center Correlation
In the realm of semiconductor manufacturing, Cross Work Center Correlation is pivotal for ensuring product consistency and quality. This analytical tool facilitates root cause analysis by allowing engineers to compare and correlate data across various manufacturing sites and equipment. It plays a crucial role in identifying variations and potential issues that could affect the production process.
The benefits of implementing Cross Work Center Correlation include:
- Enhanced ability to spot common failure trends or recurrent issues
- Improved throughput by reducing manual intervention
- Streamlined operations through the integration of prober and tester equipment
Commonality Analysis, as part of this module, uses a structured approach to identify patterns in failure data, aiding engineers in tracing back to potential root causes. This is essential for process control and optimization, as it helps in making informed decisions for wafer lot disposition and control. The table below summarizes the key features of this tool:
Feature | Description |
---|---|
Data Comparison | Enables analysis across different sites and equipment |
Root Cause Analysis | Identifies variations and potential issues |
Commonality Analysis | Spots patterns and correlations in failure data |
Integration | Facilitates seamless operation of prober and tester equipment |
By leveraging these capabilities, semiconductor engineers can ensure a higher level of quality management and yield enhancement across the production lifecycle.
Conclusion
In the dynamic and ever-evolving field of semiconductor engineering, having the right tools is crucial for success. From the intricate tasks of ASIC design and IC layout to the complexities of semiconductor yield enhancement and quality assurance, engineers need a comprehensive toolbox to navigate the challenges of the industry. The tools we’ve discussed, ranging from yield analysis software to metrology and defect data management systems, are indispensable for today’s engineers. They not only streamline processes but also enable innovation and precision in semiconductor manufacturing. As the industry continues to advance, staying updated with the latest tools and techniques is essential for engineers to maintain a competitive edge and contribute to the technological progress that drives our world forward.
Frequently Asked Questions
What is the role of a Physical Design Engineer in the semiconductor industry?
A Physical Design Engineer is responsible for the design and physical layout of an integrated circuit (IC). This includes floor planning, placement, routing, timing optimization, and verification to ensure the IC meets its specifications.
How does a Design For Test (DfT) Engineer contribute to IC development?
A Design For Test (DfT) Engineer designs and implements testing strategies to make integrated circuits easier to test. This involves adding testability features to the IC design to ensure it functions correctly and to facilitate fault isolation.
What is BiCMOS technology, and why is it important?
BiCMOS technology is a type of semiconductor process that combines the strengths of Bipolar and CMOS transistors into a single integrated circuit. It offers the high speed of Bipolar with the low power consumption of CMOS, making it suitable for mixed-signal applications.
How can semiconductor yield analysis software enhance production outcomes?
Semiconductor yield analysis software helps identify patterns and root causes of defects in the manufacturing process. By analyzing data, it can provide actionable insights to improve yield, reduce waste, and enhance the overall efficiency of semiconductor production.
What are the advantages of using an ASIC Price Calculator?
An ASIC Price Calculator helps engineers estimate the cost of custom ASIC development by considering variables such as design complexity, production volume, and technology node. It aids in budgeting and decision-making during the IC design process.
Why is quality assurance critical in aerospace defense semiconductor applications?
Quality assurance is vital in aerospace defense applications due to the high reliability and performance standards required. Semiconductors used in these applications must withstand extreme conditions and deliver consistent performance, making stringent quality controls essential.