The Evolution of Silicon Wafer Sizes: Understanding Industry Standards
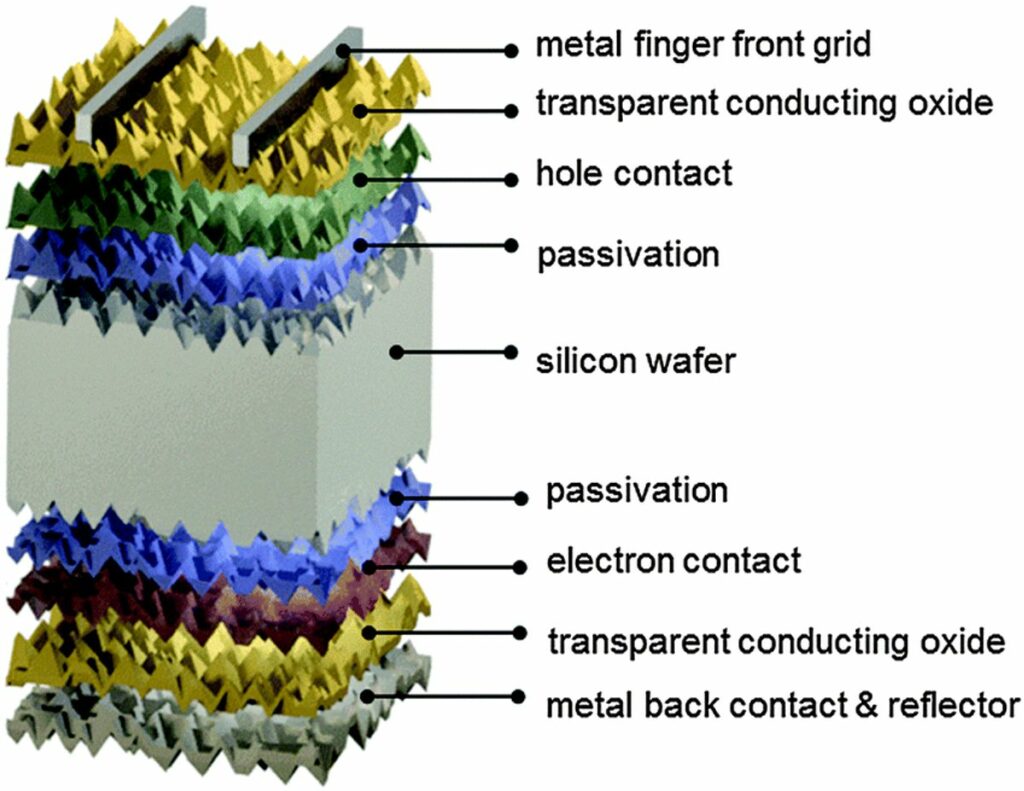
The silicon wafer is a cornerstone of modern semiconductor technology, with its evolution being a tale of innovation and scaling. This article delves into the historical progression of wafer sizes, the technological advances that have made these changes possible, and the challenges and opportunities that lie ahead. As we explore the economic and industry implications, we also look forward to the future directions in silicon wafer utilization, particularly as it intersects with the demands of high-speed data communication and complex semiconductor innovations.
Key Takeaways
- Silicon wafer sizes have historically increased to accommodate more circuits, with the industry pushing the limits of transistor shrinking as per Moore’s Law.
- Advances in wafer fabrication, such as innovations in etching and dicing, have been pivotal in maintaining the pace of semiconductor miniaturization.
- The integration of high-bandwidth memory and CoWoS (Chip on Wafer on Substrate) represents a significant step in PCB (Printed Circuit Board) miniaturization.
- Economic factors, including market trends and WFE (Wafer Fab Equipment) demand, are critical in shaping the future of the semiconductor industry.
- Future silicon wafer utilization is poised to revolutionize high-speed data communication and semiconductor innovations, leveraging optical components and other emerging applications.
Historical Progression of Silicon Wafer Sizes
From Origins to Modern Day: A Timeline
The journey of silicon wafer sizes has been marked by a relentless pursuit of miniaturization and efficiency. The progress of miniaturization has been a defining characteristic of the semiconductor industry, with each leap forward in technology enabling smaller and more powerful devices. This evolution can be traced back to the early days of microprocessors, as outlined in a comprehensive timeline on Wikipedia detailing the comparison of sizes of semiconductor manufacturing process nodes with some microscopic objects and visible light.
The manufacturing process of silicon wafers involves several intricate steps, including Photolithography, Etching, Ion Implantation, Deposition, and Chemical Mechanical Planarization, culminating in the critical stage of packaging. Over the years, these processes have seen significant advancements, with the most advanced manufacturing technologies entering the market in the last few decades, indicating a high dynamic in innovative trends.
Understanding the dynamics of innovation in the semiconductor market is crucial. A summary of the dominant technologies and their evolution over time provides insight into the technical changes that have shaped the industry. One of the main challenges in this field has been heat management, a critical aspect of semiconductor packaging that continues to drive research and development efforts.
Impacts of Moore’s Law on Wafer Size Evolution
The semiconductor industry has been profoundly shaped by Moore’s Law, which posits that the number of transistors on a microchip doubles approximately every two years, while the cost of computers is halved. This principle has not only driven the miniaturization of transistors but also influenced the evolution of silicon wafer sizes. As the demand for more powerful and efficient chips grew, the industry shifted towards larger wafers to increase the yield of chips per wafer and reduce the cost per chip.
The progression from smaller to larger wafers can be seen as a response to the relentless pursuit of Moore’s Law. In the early days, wafers were only an inch in diameter, but as technology advanced, the industry standard grew to 12 inches (300mm). This increase in size allowed for more circuits to be etched onto a single wafer, thereby improving manufacturing efficiency and reducing the defective chip rate. The table below illustrates the transition in wafer sizes over the years:
Year | Wafer Diameter (inches) |
---|---|
1960 | 1 |
1975 | 2.25 |
1980 | 3 |
1990 | 6 |
2000 | 8 |
2008 | 12 |
As we approach the physical limits of transistor shrinking, the industry must explore new avenues for maintaining the pace of innovation. The integration of high-bandwidth memory (HBM) and the development of Chip on Wafer on Substrate (CoWoS) technologies are examples of how the industry is adapting to these challenges, pushing the boundaries of what’s possible within the confines of Moore’s Law.
Key Milestones in Wafer Dimension Standards
The evolution of silicon wafer sizes has been marked by several key milestones that have shaped the semiconductor industry. Initially, wafers were small, with diameters of just 1 inch. Over time, the industry has seen a steady increase in size, with standard diameters now ranging from 200mm to 300mm. This expansion has been driven by the need for greater yield and efficiency in chip production.
The transition to larger wafers has not been without its challenges. Each leap in size requires significant investment in new equipment and processes. However, the benefits, such as reduced costs per chip and improved performance, have justified these advancements. The table below outlines the progression of standard wafer sizes over the years:
Year | Wafer Diameter (inches) |
---|---|
1960s | 1 |
1970s | 2 |
1980s | 4 |
1990s | 6 |
2000s | 8 |
2010s | 12 |
As we look to the future, the industry continues to explore the feasibility of even larger wafers. The drive for miniaturization and the relentless pursuit of Moore’s Law suggest that the evolution of wafer sizes is far from over. The next generation of wafers will likely push the boundaries of current technology, requiring novel fabrication techniques and innovative materials.
Technological Advances in Wafer Fabrication
Innovations in Etching and Dicing Techniques
The relentless pursuit of miniaturization and performance enhancement in the semiconductor industry has necessitated continuous innovations in etching and dicing techniques. Etching ICs into the wafer has evolved significantly, with companies like Applied Materials at the forefront, introducing cutting-edge patterning technologies. These include the Producer XP, Pioneer CVD patterning film, and the Sym3 Y Magnum etch system, which have revolutionized the precision and efficiency of the etching process.
Dicing the wafer is equally critical, as it separates individual circuits for packaging. The Centura Sculpta pattern-shaping technology has improved the accuracy and speed of this step, reducing the complexity of the manufacturing equipment and the time required for calibration. The advancements in etching and dicing not only enhance the manufacturing process but also pave the way for innovative packaging methods such as Wafer Level Packaging (WLP).
Despite these technological strides, the industry faces challenges such as stringent chemical regulations and the high costs of production. Yet, the development of dry etching processes and the expansion into emerging markets present significant opportunities for growth in this sector.
The Role of Hardware Description Languages in IC Design
The advent of Hardware Description Languages (HDLs) has been pivotal in the evolution of integrated circuit (IC) design. HDLs, such as VHDL and Verilog, offer a way to describe the structure and behavior of electronic circuits in a formalized manner. This abstraction allows for the simulation and verification of complex circuit designs before physical manufacturing begins.
With the miniaturization of IC tracks to tens of nanometers, HDLs have become indispensable. They enable designers to efficiently manage and iterate on designs, ensuring that the final product meets the required specifications. The role of HDLs is not limited to traditional 2D ICs but extends to the realm of 3D chip design and advanced packaging technologies like flip-chip and wafer-level packaging (WLP).
The table below illustrates the relationship between HDLs and various stages of IC development:
Stage | Role of HDL |
---|---|
Design | Describes the electronic circuit |
Simulation | Verifies circuit behavior |
Verification | Ensures design meets specifications |
Manufacturing | Guides the production process |
As the industry moves towards more complex architectures, such as 2.5D and 3D integration, the need for a common language that can describe these technologies becomes critical. HDLs serve as this common language, bridging the gap between design intent and manufacturing capabilities.
Advancements in Semiconductor Packaging: WLP and Flip-Chip
Wafer Level Packaging (WLP) has revolutionized semiconductor packaging by processing entire wafers before dicing, in contrast to traditional methods that package each die post-dicing. This approach not only minimizes the footprint by 30-50% but also enhances efficiency, making it particularly suitable for compact devices such as smartphones, wearables, and IoT gadgets. The market share for WLP is projected to be substantial, ranging from 12-17%, thanks to its scalability and cost-effectiveness.
Flip-chip technology, while not the latest, remains a cornerstone in semiconductor packaging. It connects the die to the package using solder bumps, bypassing the need for wire bonding. This results in lower latency, reduced power consumption, and a smaller package size, which are critical advantages for high-performance applications.
Both WLP and flip-chip technologies have faced challenges, such as thermal management and the complexity of further miniaturization. However, innovations like fan-out WLP are addressing these issues by allowing more I/O connections through redistribution layers (RDL) that extend beyond the die boundaries.
Technology | Footprint Reduction | Market Share | Key Advantages |
---|---|---|---|
WLP | 30-50% | 12-17% | Scalability, Efficiency |
Flip-Chip | Significant | Established | Low Latency, Power Efficiency |
Challenges and Opportunities in Scaling
The Limits of Transistor Shrinking and Future Prospects
The relentless pursuit of Moore’s Law has been a guiding force in the semiconductor industry, with the number of transistors on a chip doubling approximately every two years. However, as we approach the physical limits of silicon with a crystal lattice parameter of 0.543 nm, the future of transistor shrinking is a subject of intense debate. The industry now stands at a pivotal point where the traditional path of simply shrinking transistors is no longer viable.
Beyond the constraints of current lithographic tools, which are bound by the reticle limit of about 800 square millimeters, lies the potential for innovation in system integration and architecture. The integration of high-bandwidth memory (HBM) and the use of advanced packaging techniques like Wafer-Level Packaging (WLP) are indicative of the industry’s shift towards optimizing performance through other means.
As we look to the future, the semiconductor packaging industry faces both significant challenges and opportunities. The adoption of novel manufacturing techniques such as 3D stacking is already making a substantial impact, with a market share of 30%. The next phase of evolution may well focus on shrinking the printed circuit board (PCB) itself, as suggested by the development of Chip on Wafer on Substrate (CoWoS) technology.
Integrating High-Bandwidth Memory (HBM) in Wafer Design
The integration of High-Bandwidth Memory (HBM) into wafer design represents a significant leap in semiconductor technology, particularly for applications demanding high-speed data processing, such as artificial intelligence (AI). HBM is a stack of vertically interconnected DRAM chips atop a control logic IC, utilizing through-silicon-vias (TSVs) for communication, which allows for a compact and efficient design.
Recent advancements in 3D SoIC technology have paved the way for denser vertical interconnections. Hybrid bonding techniques, featuring copper-to-copper connections, offer a ‘bumpless’ alternative to traditional solder bumps, enabling the creation of HBM structures with unprecedented layer counts and reduced thickness.
The table below highlights the evolution of HBM technology:
Generation | Layer Count | Connection Type | Thickness |
---|---|---|---|
Traditional HBM | Up to 8 | Solder Bumps | >600 µm |
Advanced HBM | 12 | Hybrid Bonding | 600 µm |
Incorporating HBM into system designs, such as TSMC’s CoWoS technology, allows for the integration of a vast array of devices, far exceeding the capabilities of a single chip. This approach is instrumental in creating high-performance GPUs and other complex systems, where the synergy between compute dies and HBM is critical for managing cache, I/O traffic, and overall system performance.
CoWoS: Revolutionizing Printed Circuit Board Miniaturization
Chip-on-Wafer-on-Silicon (CoWoS) technology represents a pivotal shift in the miniaturization of printed circuit boards (PCBs). By integrating multiple chips onto a single wafer, CoWoS significantly reduces the overall footprint of PCBs, paving the way for more compact and efficient electronic devices. TSMC’s CoWoS advanced packaging technology has been instrumental in the development of high-performance products, such as the Nvidia Ampere and Hopper GPUs, showcasing its potential to transform the industry.
The implementation of CoWoS has led to a remarkable increase in the number of input/output (I/O) connections, which is essential for accommodating the complex circuitry required by today’s sophisticated devices. This advancement is not just about size reduction; it’s about enhancing the functionality and performance of PCBs while maintaining a compact form factor. The table below illustrates the impact of CoWoS on PCB density and cost reduction:
Feature | Impact on PCB Density | Cost Reduction |
---|---|---|
SMD Packaging | Increased density by allowing chips to be mounted from one side only | Reduced PCB costs by 15% |
Fan-out Techniques | Extends I/O connections beyond die boundaries | – |
Despite the challenges associated with thermal management and the complexity of further reducing form factors, CoWoS continues to evolve. Innovations such as fan-out techniques have emerged, allowing for an even greater number of I/O connections by extending beyond the die boundaries. These advancements are crucial for the integration of high-bandwidth memory (HBM) and large-scale compute requirements, which are becoming increasingly important as we move towards devices with trillions of transistors.
Economic and Industry Implications
Market Trends and the Trillion-Dollar Revenue Forecast
The silicon wafer market is on a trajectory of significant growth, with projections indicating a leap from $15.3 billion in 2022 to $25.9 billion by 2032. This represents a compound annual growth rate (CAGR) that underscores the market’s robust expansion and the increasing demand for silicon wafers across various industries.
Economic forecasts suggest that the semiconductor industry’s revenues may hit the trillion-dollar mark by the end of the decade. This anticipated growth is expected to double the spending on Wafer Fab Equipment (WFE), with etch and deposition markets poised to grow even faster. Strategic initiatives are already in place to capitalize on these trends, ensuring that companies are well-positioned to benefit from the burgeoning market.
Valuation metrics reveal a dynamic market, with the industry’s P/E ratio oscillating between highs and lows, reflecting investor sentiment and market conditions. The forward-looking estimates for 2024 and 2025 suggest a modest uptick in earnings, despite a short-term decline due to current market challenges. As the industry navigates through these fluctuations, the potential for substantial shareholder returns remains a key narrative.
Factors Influencing Wafer Fab Equipment (WFE) Demand
The demand for Wafer Fab Equipment (WFE) is intricately linked to the semiconductor industry’s pulse. The strength of semiconductor demand and the existing capacity level are the primary drivers of WFE demand. Other influential factors include geopolitical constraints, such as restrictions on semiconductor sales to specific countries, and macroeconomic conditions like interest rates and consumer spending patterns. These elements can significantly impact both the demand for semiconductors and the capacity to produce them.
Technology transitions also play a crucial role as they necessitate new equipment to support advanced manufacturing processes. The anticipation of new fabs coming online is a positive indicator for long-term WFE demand, despite the cyclical nature of memory market spending, which dominates WFE expenditures.
Projected sales growth for WFE and related sectors is outlined below:
Year | WFE Sales Growth | Test Equipment Growth | Assembly & Packaging Growth |
---|---|---|---|
2024 | 3% | 13.9% | 24.3% |
2025 | 18% | 17% | 20% |
While certain regions like China, Taiwan, and Korea are expected to remain leading destinations for WFE, the overall market is poised for a rebound. After a predicted decline in the short term, growth is anticipated to resume, with a 10% increase in WFE sales by 2025, continuing through 2027. This resurgence is expected to align with rising utilization rates and subsequent increases in semiconductor capital expenditures.
Strategic Initiatives and Growth in Etch and Deposition Markets
The etch and deposition segments within the semiconductor equipment industry are poised for significant growth. Management’s strategic initiatives are aimed at capitalizing on this trend, with a focus on outpacing the overall growth in Wafer Fab Equipment (WFE) spending. This is particularly relevant as the semiconductor industry’s revenues are projected to reach a trillion dollars by the end of the decade, doubling today’s WFE spending levels.
Challenges such as stringent regulations on chemical usage and disposal, high production costs, and environmental concerns are being addressed through innovation and market expansion. Companies are investing in research and development to create new products and forming strategic partnerships to enhance their market presence. The table below outlines key players in the Semiconductor grade Wet Chemicals market and their strategic growth initiatives:
Company | Strategic Growth Initiatives |
---|---|
KMG Chemicals Inc | Expanding product portfolio and distribution channels |
Solvay S.A. | Focusing on innovative product development and partnerships |
BASF SE | Investing in R&D and forming industry alliances |
By navigating these challenges and leveraging opportunities, companies are set to drive innovation and growth in the etch and deposition markets.
Future Directions in Silicon Wafer Utilization
Emerging Applications in High-Speed Data Communication
The relentless pursuit of higher bandwidth and faster data transmission has led to significant advancements in network technology. The evolution of 800G optical transceivers marks a pivotal moment in this journey, addressing the growing demand for seamless communication and data exchange. These high-speed modules are critical in facilitating the rapid transfer of information, ensuring that latency remains on par with traditional board-level copper-electrical connections.
In the realm of data centers, 800G optical modules have emerged as a cornerstone technology. They are instrumental in managing the immense data throughput required by modern facilities. The integration of these modules is not just about speed; it’s also about maintaining low bit error rates (BERs) to minimize the need for forward-error correction and the associated latency it introduces.
The future of high-speed data communication is also looking towards the integration of silicon photonics for direct, optical GPU-to-GPU communication. This innovation is set to revolutionize the way high-performance computing systems operate, by significantly enhancing the bandwidth efficiency and reducing the energy footprint of data transfers between processing units.
- Data Center Applications: 800G Optical Transceivers
- High bandwidth and low latency for fast data transmission
- Enhanced capacity for switch and router systems
- Introduction of 3.2Tbps ports to support large AI models and computations
As the industry converges on coding, equalization, and error correction standards, the economic viability of 800G technology is set to expand across various applications, making it a key player in the next generation of high-speed data communication.
The Intersection of Optical Components and Silicon Fabrication
The integration of optical components into silicon wafers represents a transformative leap in semiconductor technology. Silicon photonics has emerged as a key enabler for high-speed data communication, merging the efficiency of photonic systems with the scalability of semiconductor manufacturing. This synergy has led to the development of advanced photonic integrated circuits (PICs) that are revolutionizing data centers, artificial intelligence, and high-performance computing.
Silicon photonics leverages standard wafer fabrication processes to produce optical modules such as 100G and 400G transceivers. The technology’s compatibility with existing semiconductor infrastructure has streamlined the mass production of these optical subsystems, significantly reducing costs and facilitating the creation of compact modules. The table below highlights the impact of silicon photonics on optical module production:
Aspect | Benefit of Silicon Photonics |
---|---|
Production Scalability | Utilizes existing semiconductor facilities |
Cost Efficiency | Reduces assembly costs |
Module Compactness | Enables smaller form factors |
Data Transmission Speed | Supports 100G and 400G modules |
Recent advancements in this field are reshaping the optical market, particularly within data centers. The challenge lies in connecting compute chips over extended distances without compromising bandwidth, energy efficiency, or density. Silicon photonics addresses these issues, offering a path forward for the design and architecture of next-generation AI, cloud, and high-performance computing systems.
Anticipating the Next Wave of Semiconductor Innovations
As we stand on the brink of new horizons in the semiconductor industry, the anticipation for the next wave of innovations is palpable. The industry is expected to maintain its growth trajectory in the foreseeable future, fueled by relentless advancements in materials research, device complexities, and the integration of manufacturing processes. These factors, along with the emergence of new applications, are pivotal in driving the industry forward.
The AI boom is a testament to the semiconductor industry’s capacity for innovation, with AI applications demanding ever-increasing computing power and memory access. The integration of chiplets represents a significant shift from traditional integrated devices, offering a glimpse into the future of semiconductor design and functionality.
Looking ahead, the industry faces both opportunities and challenges. The packaging industry, for example, is at a crossroads, balancing the pursuit of miniaturization and performance optimization. Advanced manufacturing techniques such as 3D stacking and Wafer-Level Packaging (WLP) are already making substantial inroads, capturing a significant market share. As we anticipate the next wave of semiconductor innovations, it is clear that the industry’s evolution will be marked by strategic initiatives and a continued focus on overcoming the technical hurdles that lie ahead.
Conclusion
The journey through the evolution of silicon wafer sizes and industry standards reveals a landscape of relentless innovation and technological prowess. As we grapple with the limits imposed by the silicon crystal lattice and the principles of Moore’s Law, the industry continues to push boundaries, exploring new horizons like Chip-on-Wafer-on-Substrate (CoWoS) and Wafer Level Packaging (WLP) to meet the growing demands for higher performance and integration. The semiconductor industry’s march towards a trillion-dollar revenue milestone underscores the critical role of wafer fabrication and the sophisticated equipment that drives it. With each technological transition, from etching intricate circuits to the advent of optical components on silicon, we witness a testament to human ingenuity. The future of this dynamic field is as exciting as it is uncertain, with the potential to redefine our relationship with technology and propel us into an era of unprecedented computational capabilities.
Frequently Asked Questions
What is the significance of the silicon crystal lattice parameter in transistor shrinking?
The silicon crystal lattice parameter, which measures 0.543 nm, is a fundamental physical limit that influences the extent to which transistors can be miniaturized. As transistor sizes approach this scale, it becomes increasingly challenging to shrink them further, raising questions about the future progression of Moore’s Law.
How does hardware description language (HDL) impact integrated circuit design?
HDLs, such as VHDL and Verilog, are used to describe the structure and behavior of electronic circuits, allowing for the automation of the IC design process. This has facilitated the creation of more complex designs and the reduction of minimum circuit track sizes to tens of nanometers.
What is the difference between Wafer Level Packaging (WLP) and traditional semiconductor packaging?
WLP involves packaging processes applied to entire silicon wafers before they are diced into individual chips, which contrasts with traditional methods that package each die after dicing. WLP enhances the packaging density and reduces the overall footprint of semiconductor devices.
What are the primary drivers of Wafer Fab Equipment (WFE) demand?
The main drivers include the overall demand for semiconductors, the current capacity levels, technology transitions requiring new equipment, and external factors such as economic conditions and policy constraints on semiconductor sales.
How is CoWoS changing the landscape of printed circuit board (PCB) miniaturization?
Chip on Wafer on Substrate (CoWoS) technology is enabling the integration of different types of chips, such as memory and logic, into a single package. This approach is reducing the size of PCBs by eliminating the need for separate memory and processor boards.
What emerging applications are being enabled by the integration of optical components on silicon wafers?
The integration of optical components onto silicon wafers is paving the way for faster and more efficient data communication solutions. These advancements are particularly beneficial for applications in data centers, artificial intelligence, and high-performance computing.