The Evolution of Wafer Probes: Enhancing Contact Quality and Reliability
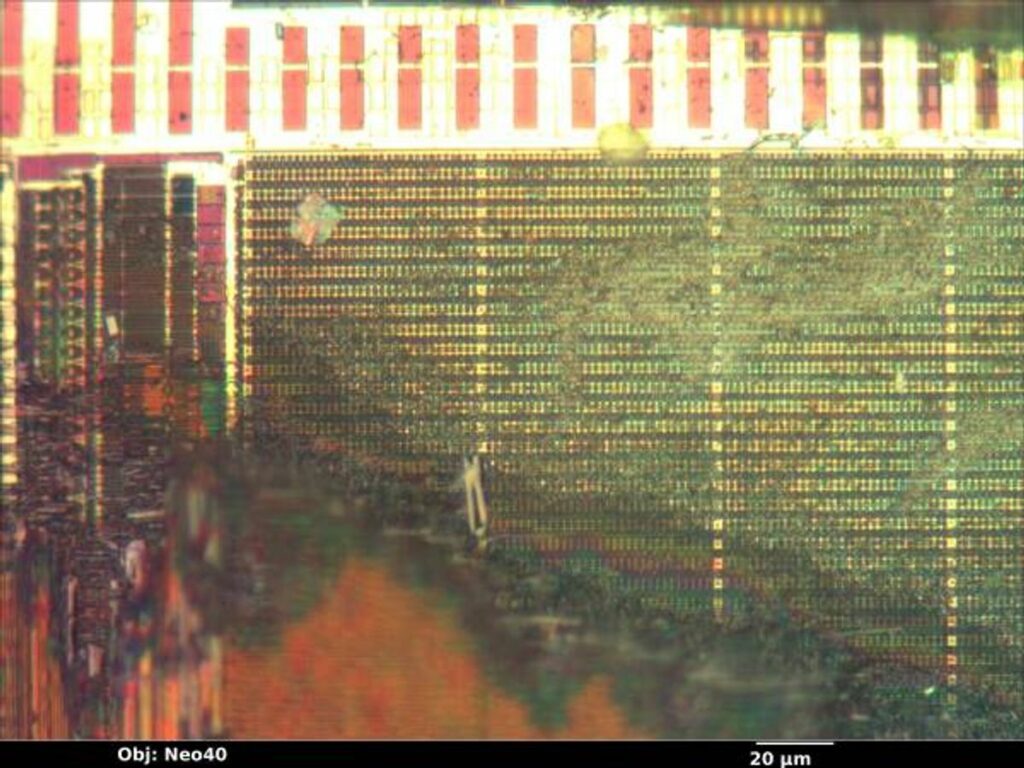
Probe cards play a pivotal role in the semiconductor manufacturing industry, serving as critical tools for testing the electrical performance of wafers. With the relentless push for miniaturization and enhanced performance in consumer electronics, automotive applications, and emerging technologies like IoT, the demands on probe card technology have intensified. This article explores the evolution of wafer probes, focusing on advancements in technology that improve contact quality and reliability, the challenges faced in probe card development, innovative inspection techniques, market influences, and future directions for innovation.
Key Takeaways
- Innovations in probe card technology, such as high-density interconnects and microfabrication techniques, are crucial for meeting the testing needs of advanced semiconductor devices.
- Probe card development faces challenges in balancing efficiency with sensitivity, managing increased cost and complexity, and adapting to the shortened lifecycles of semiconductor technologies.
- Inspection techniques like SEM, AFM, and confocal microscopy are evolving to provide higher accuracy and better signal-to-noise ratio for quality assurance in wafer inspection.
- The demand for probe cards is being driven by the growth of consumer electronics and automotive sectors, as well as the impact of IoT and government initiatives supporting semiconductor manufacturing.
- Future innovation in probe card technology will likely focus on material research, cost-effective manufacturing, and sustainable production methods to keep pace with evolving semiconductor technologies.
Advancements in Probe Card Technology
Innovations in High-Density Interconnects
The relentless pursuit of miniaturization in semiconductor devices has necessitated the evolution of high-density interconnects. These interconnects serve as the backbone for modern probe cards, enabling faster and more efficient electrical signal transmission between the probe and the wafer. With the advent of technologies such as through-silicon vias (TSVs) and interposers, the industry has seen a significant leap in the performance of these critical components.
In the realm of probe card technology, the integration of advanced materials and novel fabrication methods has led to the development of interconnects that can handle the increased throughput demanded by high-density microelectrode arrays (μECoG devices). The table below outlines some of the key technologies contributing to this advancement:
Technology | Description |
---|---|
TSVs | Enable vertical electrical connections through a silicon wafer |
Interposers | Act as a bridge for electrical signals between different die layers |
ILT | Optimizes photomask shapes for improved signal fidelity |
These innovations not only improve the data transfer rates but also reduce the power consumption and heat generation, which are critical factors for the longevity and reliability of semiconductor devices. As the industry moves towards more complex packaging solutions like heterogeneous integration and chiplets, high-density interconnects will continue to play a pivotal role in enabling these technologies.
Microfabrication Techniques
The relentless pursuit of miniaturization in semiconductor devices has necessitated the evolution of microfabrication techniques. Inert-atmosphere microfabrication technology has emerged as a pivotal advancement, enabling the creation of intricate patterns without the reliance on traditional photolithography. This approach is particularly beneficial for 2D materials, where conventional methods may introduce impurities or prove inefficient.
Alternative additive manufacturing methods have been developed to directly synthesize 2D materials, such as inkjet-printed graphene and MoS2-based FETs fabricated using laser-assisted techniques. These methods demonstrate the potential to advance fabrication processes while circumventing the need for lithography within inert atmospheres. For instance, laser-assisted techniques can generate thousands of micro-patterns rapidly, enhancing manufacturing efficiency and scalability.
The table below summarizes key microfabrication techniques and their attributes:
Technique | Material | Precision | Speed | Scalability |
---|---|---|---|---|
Inkjet Printing | Graphene, MoS2 | Moderate | High | Moderate |
Laser-Assisted | MoS2 | High | Very High | High |
Plasma Treatment | Various | High | Moderate | Moderate |
These techniques are instrumental in achieving the high resolution and precision required for advanced electronic devices. They offer a path towards photolithography-free manufacturing, which is crucial for batch production and the high-volume demands of the industry.
Adapting to Advanced Semiconductor Devices
As semiconductor devices continue to evolve, probe card manufacturers are challenged to keep pace with the increasing complexity and performance demands. The TESLA300 Advanced On-Wafer Power Semiconductor Probe System represents a significant leap in addressing these needs, offering precise high-power testing capabilities. This system is part of a broader trend where advanced probe cards are designed to accommodate the intricate architectures of modern semiconductors.
The shift towards materials like 2D substances, which can achieve single-atomic-layer thickness, is pushing the boundaries of traditional silicon-based technologies. These materials not only promise to extend Moore’s Law but also require novel probing solutions that can handle their ultra-high carrier mobility and delicate structures. As a result, probe card developers are exploring new materials and methods to ensure compatibility with these advanced semiconductors.
To illustrate the progress in this field, consider the following advancements:
- Introduction of vacuum adsorption technology for delicate component handling
- Development of probe cards for 400V/600V ESD Withstand-Capable Rectifiers
- Collaborative research efforts, such as those between Samsung and Nova, to enhance device packaging and testing
These developments underscore the industry’s commitment to innovation, as manufacturers strive to meet the stringent requirements of next-generation semiconductor devices.
Challenges in Probe Card Development
Balancing Efficiency and Sensitivity
In the realm of semiconductor testing, the probe card plays a pivotal role, acting as the intermediary between the testing equipment and the semiconductor wafers. Efficiency and sensitivity are paramount in ensuring that the testing process is both rapid and accurate. To strike this balance, advancements in technology such as TDI (Time Delay Integration) image sensors have been introduced. These sensors enhance sensitivity through noise suppression and a larger field of view (FOV), while maintaining a high frame rate for efficient imaging.
The significant role of probe card PCBs cannot be overstated; they are a critical competitive advantage for manufacturers. However, defective cards can severely interfere with the testing process, leading to false results and production delays. The table below outlines the key features of TDI image sensors that contribute to balancing efficiency and sensitivity in wafer inspection:
Feature | Advantage |
---|---|
Noise Suppression | Enhances image clarity |
Larger FOV | Increases inspection coverage |
High Frame Rate | Reduces exposure time |
By optimizing light sources and leveraging the capabilities of TDI sensors, manufacturers can improve detection sensitivity and reduce exposure times, thus enhancing overall efficiency. This delicate balance is crucial for the rapid and accurate inspection of non-patterned wafers, where defects must be identified with precision to ensure the quality of semiconductor devices.
Cost and Complexity Considerations
The probe card industry is currently facing a significant challenge in balancing the escalating costs and complexity of production with market demands. The integration of sophisticated technologies into probe cards has led to increased manufacturing expenses, which in turn affects the pricing strategies and ultimately the adoption rate in the semiconductor industry.
To illustrate the financial implications, consider the following table showing the projected growth of the probe card market:
Year | Market Value (USD billion) | CAGR (%) |
---|---|---|
2023 | 3.26 | N/A |
2030 | 6.04 | 9.18 |
This growth is fueled by the essential role of probe cards in semiconductor testing, yet manufacturers must navigate the fine line between innovation and cost-efficiency. The ease of use and versatility of probe cards are becoming increasingly important as they are now utilized across a diverse range of products. However, the impact of lithography on wafer costs and the need for efficient architectures in probe card design are also driving up expenses.
Companies are responding by investing in R&D to develop more cost-effective manufacturing processes and automated tools to streamline production. The goal is to reduce the time to market and make advanced packaging more predictable and less expensive, which is crucial given the rising cost of scaling transistors beyond 28nm.
Shortening Lifecycles and Continuous R&D
The semiconductor industry is characterized by rapid innovation and evolving technologies. Probe cards are no exception, with their lifecycles shortening as a result of continuous advancements in semiconductor devices. This dynamic environment necessitates ongoing research and development (R&D) to maintain relevance and competitiveness.
Key industry players are responding to these challenges by investing significantly in R&D. This investment is not only about keeping up with technological changes but also about creating new growth opportunities. The table below illustrates the relationship between test intensity and probe card demand, highlighting the importance of R&D investment:
Test Intensity | Probe Card Demand | R&D Investment |
---|---|---|
High | Increased | Essential |
Moderate | Stable | Important |
Low | Decreased | Reduced |
Government initiatives and incentives aimed at promoting semiconductor manufacturing have become crucial in offsetting the costs associated with the high demand for probe cards. Moreover, research into new materials and manufacturing processes is paving the way for more cost-effective solutions, which could revolutionize the industry.
Inspection Techniques for Wafer Quality Assurance
SEM, AFM, and Confocal Microscopy
The quest for precision in wafer inspection has led to the adoption of sophisticated techniques such as scanning electron microscopy (SEM), atomic force microscopy (AFM), and confocal microscopy. These methods are pivotal in identifying defects at the micro and nano-scale, ensuring the reliability of semiconductor devices.
SEM offers a high-resolution view of the wafer surface, capable of detecting minute irregularities. AFM, on the other hand, provides topographical data with atomic-scale resolution, which is crucial for understanding surface roughness and patterns. Confocal microscopy complements these by offering three-dimensional imaging capabilities, allowing for a more comprehensive analysis of wafer defects.
Despite their effectiveness, these inspection methods face challenges in balancing high sensitivity with the need for efficient throughput. The following table summarizes the key attributes of each technique:
Technique | Resolution | Throughput | Sensitivity |
---|---|---|---|
SEM | High | Low | High |
AFM | Atomic | Moderate | Very High |
Confocal | High | Moderate | High |
In-line Inspection Systems
In-line inspection systems are crucial for maintaining high standards in wafer production. Optical wafer inspection instruments facilitate rapid defect detection through advanced techniques like bright-field and dark-field microscopy. These instruments work in tandem with SEM-based review tools to provide a comprehensive defect analysis.
The process begins with the optical instruments performing a quick scan to identify potential defects. Identified defects are then precisely located and categorized, which allows for targeted SEM review. This two-stage approach optimizes both speed and accuracy in defect identification:
- Stage 1: Rapid defect scanning with optical instruments
- Stage 2: Detailed defect analysis using SEM
Despite their effectiveness, in-line inspection systems face the challenge of balancing high efficiency with high sensitivity. The integration of multi-channel acquisition and automated control has been pivotal in addressing this issue, enabling faster throughput without compromising on the sensitivity required for accurate defect detection.
Improving Signal-to-Noise Ratio in Non-Patterned Wafer Inspection
The inspection of non-patterned wafers presents unique challenges, particularly in achieving high detection sensitivity without compromising efficiency. Experiments illustrate that the increase in the number of TDI stages and reduction in the column fixed pattern noise effectively improve the signal-to-noise ratio, offering a promising avenue for enhancing defect inspection capabilities.
Dark-field microscopy, a primary technique used in non-patterned wafer inspection, relies heavily on the signal-to-noise ratio (SNR) and image contrast to detect defects. To address the limitations of high reflection and contamination, researchers have proposed methods to improve SNR without sacrificing efficiency. This balance is crucial for maintaining the throughput of semiconductor manufacturing processes.
Future work in this area is set to focus on several key improvements:
- Utilizing polarization information to reduce noise
- Optimizing scanning strategies for better defect coverage
- Applying deblurring algorithms to enhance image clarity
These advancements are expected to further refine the detection sensitivity and efficiency, making them integral to the continuous development of wafer inspection technologies.
Market Dynamics Influencing Probe Card Demand
Growth in Consumer Electronics and Automotive Sectors
The probe card market is experiencing significant growth, driven by the surge in demand for sophisticated electronic devices. The market size, valued at USD 2.7 billion in 2023, is forecasted to expand at a robust pace, fueled by advancements in technologies such as 5G, IoT, and AI. These technologies are not only revolutionizing the consumer electronics sector but are also pivotal in the automotive industry, where the integration of electronic components is becoming increasingly complex.
The adoption of probe cards is critical across various verticals, with IT & Telecommunication sectors holding a substantial market share. However, the automotive sector is rapidly catching up, as vehicles become more reliant on electronic systems for safety, navigation, and entertainment. This trend is reflected in the growing investments in automotive electronics, which in turn propels the demand for reliable and efficient probe cards.
Government initiatives aimed at strengthening digital economies have also played a role in shaping the probe card market. Regulations and standards for electronic device fabrication and component performance have established a conducive environment for the adoption of advanced probe cards. While regions like the Middle East and Africa are still emerging markets, the APAC region stands out with significant investments in electronics manufacturing, positioning it as a key player in the global probe card landscape.
Impact of IoT and Other Emerging Technologies
The Internet of Things (IoT) has become a transformative force in the evolution of wafer probes, driving the demand for more sophisticated and reliable contact solutions. IoT devices, often equipped with sensors or actuators, require seamless integration and communication capabilities, necessitating advanced probe card technologies to ensure high-quality data transmission.
Emerging technologies, such as intelligent self-organizing networks and interposers, are shaping the future of probe card development. These technologies facilitate real-time analysis and reconfiguration, as well as fast, low-power inter-die signal transmission, which are critical for the efficient operation of interconnected devices.
The table below summarizes the impact of IoT and related technologies on probe card demand:
Technology | Impact on Probe Cards |
---|---|
IoT Devices | Increased demand for high-density interconnects |
Intelligent Networks | Need for probes that support real-time reconfiguration |
Interposers | Requirement for low-power, high-speed signal transmission |
Government Initiatives and Incentives
The probe card market is significantly influenced by government initiatives and incentives aimed at fostering the growth of the semiconductor industry. In the APAC region, countries like China, India, Japan, Indonesia, and South Korea have implemented various programs to reduce reliance on foreign technology and encourage domestic innovation. These initiatives often include tax incentives, grants, and resources to support local semiconductor production, which in turn drives the demand for advanced probe cards.
The presence of stringent regulations and standards for electronic device fabrication and component performance has also contributed to a standardized environment conducive to the adoption of sophisticated probe cards. This is particularly true in regions with a strong digital economy, where the need for high-quality electronic components is paramount. As a result, probe card providers find significant opportunities in these markets.
Emerging markets such as the Middle East and Africa are gradually increasing their investments in electronics manufacturing and assembly, presenting new frontiers for the probe card industry. The global landscape of government support for the semiconductor sector is diverse, with each region presenting unique challenges and opportunities for probe card manufacturers.
Future Directions in Probe Card Innovation
Material Research and Cost-Effective Manufacturing
The relentless pursuit of efficiency in probe card manufacturing has led to the exploration of additive manufacturing methods. These methods promise to streamline the production process and enhance yield rates. For example, stamp printing techniques allow for the simultaneous transfer of multiple 2D material pieces, which can be particularly beneficial for high-volume production.
Advancements in material research have also focused on the precision and scalability of techniques such as printing, laser processing, and direct chemical vapor deposition (CVD) synthesis. The table below summarizes the potential impact of these methods on manufacturing efficiency:
Technique | Potential Impact on Efficiency |
---|---|
Stamp Printing | Simplifies transfer of 2D materials, aiding batch production |
Printing & Laser Techniques | Facilitates direct generation on flexible substrates |
Direct CVD Synthesis | Could significantly enhance overall manufacturing efficiency |
As the industry moves forward, the advantages and disadvantages of each technique are being meticulously evaluated to drive future advancements. The goal is to refine selective synthesis methods for increased precision and to scale down to meet the stringent requirements of modern semiconductor technologies.
Meeting the Needs of Evolving Semiconductor Technologies
As semiconductor technologies rapidly evolve, probe card manufacturers are tasked with developing solutions that can keep pace with the increasing complexity of next-generation chips. The Yole Group highlights that chips now undergo as many as six stages of testing, reflecting the intricate nature of modern semiconductor testing readiness.
To meet these demands, probe card innovation is focusing on several key areas:
- Enhanced material properties to withstand the rigors of multiple testing stages.
- Precision engineering for accurate contact with ever-smaller chip features.
- Advanced design methodologies to accommodate a variety of chip architectures.
These efforts are critical in ensuring that the probe cards can interface effectively with fragile device packaging and advanced semiconductor structures, such as chiplets and high-density advanced packaging (HDAP). The industry’s move towards heterogeneous integration and the use of through-silicon vias (TSVs) further underscores the need for probe cards that can adapt to diverse and complex packaging technologies.
Strategies for Sustainable Development in Probe Card Production
The sustainable development of probe card production hinges on the industry’s ability to innovate while minimizing environmental impact. Research into new materials and manufacturing processes is pivotal, aiming to create probe cards that are not only cost-effective but also exhibit higher performance.
To address the rapid advancements in semiconductor technology and the associated shortening lifecycles of probe cards, a strategic approach is necessary. This includes:
- Continuous R&D investment to keep pace with technological changes.
- Leveraging government initiatives and incentives to support R&D and offset high production costs.
- Standardizing manufacturing practices to comply with global regulations and performance standards.
The APAC region, with its initiative to bolster the digital economy, presents significant opportunities for sustainable growth in probe card markets. Meanwhile, emerging markets such as the Middle East and Africa are gradually increasing investments in electronics manufacturing, which could benefit from sustainable probe card production practices.
Conclusion
The evolution of wafer probes is a testament to the relentless pursuit of enhancing contact quality and reliability in the semiconductor industry. As we have explored, the development of probe cards is driven by the need to meet the ever-increasing demands of advanced semiconductor devices. Innovations in materials, manufacturing processes, and inspection techniques are crucial to achieving the delicate balance between efficiency and sensitivity required for high-quality IC testing. The growth of the consumer electronics, automotive electronics, and IoT sectors further fuels the demand for more sophisticated probe cards, pushing the boundaries of what is possible in wafer testing. Despite the challenges of technical complexity and cost, the industry’s commitment to R&D, supported by government initiatives, promises a future of continued advancement and cost-effective solutions in probe card technology.
Frequently Asked Questions
What are probe cards and why are they important in semiconductor manufacturing?
Probe cards are essential tools used in the semiconductor manufacturing process to test the electrical performance of wafers. They consist of probes that make physical contact with the semiconductor wafer to assess the functionality and reliability of integrated circuits (ICs) before they are packaged.
What challenges are associated with developing probe cards?
Developing probe cards involves balancing efficiency and sensitivity, managing cost and complexity, and dealing with the shortening lifecycles of technology which necessitates continuous R&D. Rapid advancements in semiconductor technology also contribute to these challenges.
How do inspection techniques like SEM and AFM contribute to wafer quality assurance?
Techniques such as Scanning Electron Microscopy (SEM) and Atomic Force Microscopy (AFM) offer high sensitivity in detecting defects on wafers, which is crucial for ensuring the quality of integrated circuits. However, they generally have lower throughput compared to other methods.
What impact does the growth in consumer electronics have on the demand for probe cards?
The increasing global demand for consumer electronics, automotive electronics, and IoT devices supports the growth of the semiconductor industry, which in turn influences the demand for probe cards, as they are a vital part of the semiconductor manufacturing process.
What future innovations are expected in probe card technology?
Future innovations in probe card technology may include new materials and cost-effective manufacturing processes, as well as adaptations to meet the demands of evolving semiconductor technologies and strategies for sustainable development.
What are the limitations of current wafer inspection methods and how can they be improved?
Current wafer inspection methods like SEM and confocal microscopy can be limited by high reflection and contamination, particularly in non-patterned wafer inspection. Improvements aim to enhance the signal-to-noise ratio (SNR) of defects without sacrificing efficiency, thus achieving a balance between detection efficiency and sensitivity.