The Evolution of Wafer Production: Trends and Technologies Shaping the Industry
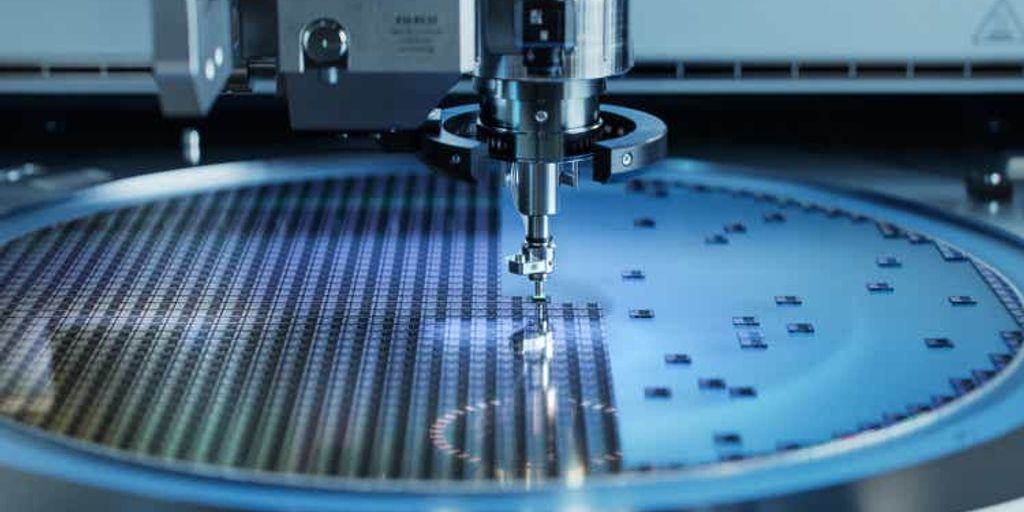
The world of wafer production is always changing, driven by new technologies and ideas. As we look closer, we see big trends and breakthroughs that are shaping how wafers are made. From making wafers bigger to using new materials, these changes are helping the industry grow and improve. This article will explore these trends and what they mean for the future of wafer production.
Key Takeaways
- Larger wafer sizes are boosting production efficiency and lowering costs.
- New crystal growth methods are improving wafer quality and scalability.
- Non-silicon materials are being explored for their potential benefits and challenges.
- Sustainability and ethical sourcing are becoming more important in wafer production.
- Technological advances in wafer cleaning are crucial for maintaining production quality.
Increasing Wafer Diameter: Enhancing Production Efficiency
The semiconductor industry is always looking for ways to improve. One of the biggest trends is making wafers bigger. Larger wafers mean more chips can be made at once, which saves money and time. The industry is working on moving from 300mm wafers to even bigger 450mm ones. This change will help make technology cheaper and more available to everyone.
Technological Advances Driving Larger Wafers
New technology is making it possible to create larger silicon crystals. This means we can make bigger wafers without losing quality. As we get better at this, we can make even larger wafers, which will help the industry keep growing.
Cost Reduction and Accessibility
Bigger wafers help lower the cost of making chips. When you can make more chips from a single wafer, it spreads out the cost, making each chip cheaper. This helps make technology more affordable for everyone.
Impact on Chip Production
Using larger wafers means we can produce more chips at once. This not only saves time but also makes the whole process more efficient. As a result, the industry can meet the growing demand for more and better technology.
Innovations in Crystal Growth Methods
New Techniques in Crystal Growth
The development of new methods of crystal growth is at the forefront of research in the field. Scientists and engineers are constantly exploring innovative techniques to grow silicon crystals more efficiently and with even greater purity. These advancements aim to produce crystals with optimal electrical properties for semiconductor applications, ensuring the continued miniaturization and enhancement of electronic devices.
Quality Improvements
The industry standard for production of monocrystalline silicon for semiconductors is the Czochralski (CZ) method. Use of melt-based growth for semiconductor crystal growth was pioneered by Teal and Little by demonstrating the growth of single crystal Ge. Later, Teal and Buehler grew CZ–Si using the same technique, but they could only grow dislocated single crystals of specified orientation.
Scalability and Production
The concentration is below the critical supersaturation level. Various stages of Czochralski crystal growth: (a) meltdown; (b) seed dip; (c) top; (d) shoulder; and (e) body. Examples of progress in Czochralski crystal pullers from 1970 through current diameter capability. Showing approximate period, crystal diameters, typical polysilicon charge weight and approximate height of the equipment above the working floor. Later models.
Alternative Materials in Wafer Production
Exploring Non-Silicon Materials
While silicon has long been the cornerstone of wafer production, the industry is now exploring other materials that could offer unique benefits. Materials like silicon carbide (SiC) and gallium nitride (GaN) are gaining attention for their potential to improve power management and radio frequency (RF) components. These materials can handle higher voltages and temperatures, making them ideal for advanced applications.
Advantages and Challenges
Using alternative materials comes with both advantages and challenges. One major advantage is the superior electrical, thermal, or optical properties these materials can offer. For example, SiC and GaN can operate at higher efficiencies compared to traditional silicon. However, the transition to these materials is not without hurdles. The cost of production can be higher, and existing manufacturing processes may need significant adjustments to accommodate these new materials.
Future Prospects
The future looks promising for the integration of alternative materials in wafer production. As technology advances, the industry is likely to overcome current challenges, making these materials more accessible and cost-effective. This could lead to the development of new technologies and applications that were previously unattainable, pushing the boundaries of what is possible in semiconductor manufacturing.
Sustainability and Ethical Considerations in Wafer Production
The environmental and ethical aspects of wafer production are becoming increasingly important. Manufacturers are actively pursuing sustainable practices to address growing environmental concerns. Efforts to reduce the industry’s ecological footprint are gaining momentum.
The Role of Wafer Cleaning in Semiconductor Manufacturing
Wafer cleaning is a vital step in semiconductor manufacturing. It ensures that wafers are free from contaminants and defects, which is crucial for the quality and performance of semiconductor devices. As semiconductor devices become more complex, the demand for high-precision manufacturing processes, including wafer cleaning, continues to grow.
Technological Advancements in Cleaning Equipment
The adoption of advanced cleaning techniques has revolutionized the wafer cleaning process. These techniques include the use of deionized (DI) water for a preliminary rinse to wash away loose particles and initial surface contaminants. Technological advancements in cleaning equipment have made it possible to achieve higher levels of cleanliness, which is essential for the production of high-quality semiconductor devices.
Importance of Cleanliness in Production
Cleanliness in wafer production is paramount. Contaminants and defects can impair the functionality of the final semiconductor products. After cutting, wafer surface treatment involves grinding, polishing, and etching to achieve a mirror-like surface. This ensures that the wafers are perfectly smooth and free of any defects that could affect the subsequent phases of semiconductor fabrication, such as doping, oxidation, lithography, and deposition.
Market Growth and Trends
The wafer cleaning equipment market is poised for significant growth and transformation in the next decade. Factors driving this growth include technological advancements, the growing demand for semiconductor devices, and an emphasis on sustainability. As wafer cleaning becomes more critical to the semiconductor manufacturing process, stakeholders must stay updated on these trends and invest in innovative solutions to ensure continued success.
Historical Evolution of Wafer Production
Early Developments in Wafer Technology
The history of wafer production is a fascinating journey of scientific curiosity and technological breakthroughs. In the 1950s and 60s, the semiconductor industry began to take shape, with circular wafers becoming the standard. These early trends set the foundation for modern wafer production.
Milestones in Production Techniques
Over the decades, wafer production has seen numerous milestones. From the introduction of 100mm wafers to today’s 300mm giants, each step has brought improvements in efficiency and capability. Key advancements include:
- The transition from manual to automated production lines.
- The development of precision metrology tools.
- The adoption of new materials and processes.
Adapting to Modern Demands
As technology continues to evolve, so does wafer production. Modern demands require wafers that are not only larger but also thinner and more precise. This ongoing adaptation ensures that the industry can meet the needs of next-generation technologies, from advanced computing to innovative consumer electronics.
Future Trends in Wafer Production
The semiconductor industry is always changing, and new trends are shaping the future of wafer production. Emerging technologies are at the forefront, promising to revolutionize how wafers are made and used. These technologies include advanced lithography techniques and quantum computing applications, which could significantly enhance production capabilities.
Integration of Novel Materials
The industry is also exploring the use of new materials beyond traditional silicon. Materials like silicon carbide (SiC) and gallium nitride (GaN) are gaining traction due to their superior performance in specific applications, such as power electronics and RF devices. This shift could lead to more efficient and powerful semiconductor devices.
Predictions for the Next Decade
Looking ahead, experts predict substantial growth in wafer production. For instance, a new report on emerging resilience in the semiconductor supply chain expects the U.S. to increase its fab capacity by 203% between 2022 and 2032. This growth will likely be driven by technological advancements and increased demand for semiconductor devices.
Conclusion
In summary, the world of wafer production is constantly changing, driven by new trends and technologies. From larger wafer sizes to better surface quality and new materials, these advancements are making the industry more efficient and cost-effective. As we look to the future, it’s clear that these innovations will keep pushing the boundaries of what’s possible in semiconductor technology. The journey of wafer production is far from over, and the next big breakthrough could be just around the corner.
Frequently Asked Questions
What is a silicon wafer?
A silicon wafer is a thin slice of silicon that serves as a base for making microchips and integrated circuits used in electronic devices.
Why is increasing wafer diameter important?
Larger wafer diameters allow more chips to be produced from a single wafer, which boosts production efficiency and helps lower costs.
What are some new methods in crystal growth for wafers?
Innovative techniques in crystal growth are being developed to improve the quality and scalability of silicon wafers, making them more efficient for production.
Why are alternative materials being explored in wafer production?
Non-silicon materials are being explored to overcome limitations of silicon, offering potential benefits like better performance and new applications, though they also present challenges.
How does wafer cleaning impact semiconductor manufacturing?
Advanced cleaning equipment is crucial for removing impurities from wafers, ensuring high-quality production and preventing defects in microchips.
What are the ethical and environmental considerations in wafer production?
The industry is focusing on sustainable practices and ethical sourcing of materials to minimize environmental impact and promote responsible manufacturing.