The Evolution of Wafer Size in Semiconductor Manufacturing
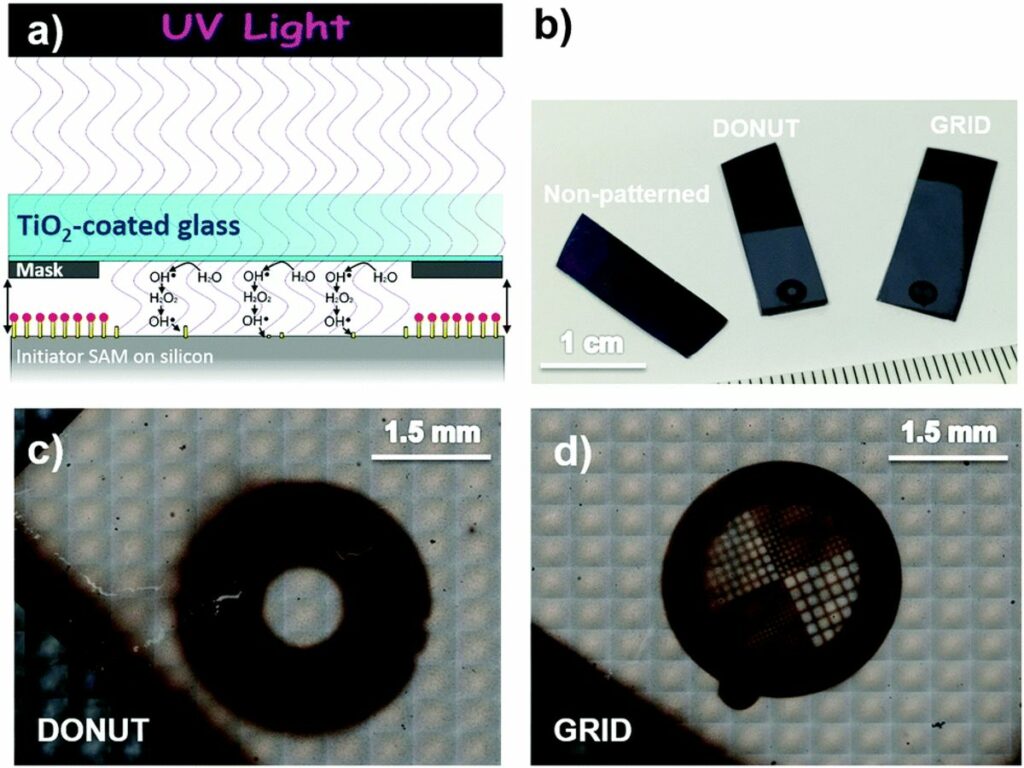
The semiconductor industry has experienced remarkable transformations in wafer size throughout its history, which have been pivotal for the advancements in technology and manufacturing efficiency. This article delves into the evolution of wafer size in semiconductor manufacturing, exploring the historical progression, technological drivers, economic and geographic influences, and the challenges and innovations that have shaped the current state of the industry. As we look towards the future, we’ll also examine emerging trends and consider what lies beyond the current standards.
Key Takeaways
- The evolution of wafer size has been driven by the pursuit of increased integration levels, performance improvements, and advancements in lithographic technologies.
- Research into new materials, alternative device architectures, and optimized system functionality has been crucial for the transition to smaller and more efficient transistors.
- Geographic shifts in semiconductor production to East Asia have been influenced by market dynamics, with a significant focus on customer intimacy and demand responsiveness.
- The industry’s move to a “top-down” approach with Foundries and Fabless companies has redefined the semiconductor landscape, emphasizing strategic planning and investment trends.
- Future wafer size advancements may challenge current manufacturing processes, but innovations such as the 15-nanometer technology and 300mm wafer production hint at continuous growth and efficiency gains.
Historical Progression of Wafer Size
Early Beginnings and Incremental Advances
The semiconductor industry has witnessed a remarkable transformation in wafer size over the decades. The size of wafers has increased over time, from the early days of 25mm wafers to the now standard 300mm diameter wafers. This growth has been a response to the industry’s relentless pursuit of cost efficiency and higher production yields.
The journey began with modest-sized wafers that were easier to handle and process. However, as technology advanced, the industry recognized the benefits of larger wafers. Each step up in size offered the potential for more chips per wafer and better economies of scale. The transition wasn’t immediate; it involved incremental advances, with each new standard carefully evaluated for its technical and economic viability.
Here is a brief timeline of wafer size evolution:
- 1960s: 25mm (1 inch) wafers
- 1970s: 50mm (2 inches)
- 1980s: 100mm (4 inches)
- 1990s: 200mm (8 inches)
- Early 2000s: 300mm (12 inches)
The shift to larger wafers has been a complex process, involving not just the wafers themselves but also the equipment and processes needed to handle them. As the industry moves forward, the lessons learned from these early beginnings continue to inform the development of even larger wafer sizes.
The Shift to Larger Wafers in the Late 20th Century
The late 20th century marked a pivotal era in semiconductor manufacturing with the industry’s transition to larger wafer sizes. This shift was primarily driven by the need to increase production efficiency and meet the burgeoning demand for semiconductor devices. Larger wafers provide more surface area per wafer, allowing for more chips to be produced from a single wafer, thus optimizing the use of materials and resources.
The adoption of larger wafers was also a response to the technological advancements of the time. As devices became more complex, with increased integration levels and smaller transistors, the industry required a larger canvas to accommodate the intricate patterns of circuitry. This evolution was supported by extensive research into new materials and alternative device architectures, which were crucial in maintaining the pace of innovation.
The table below outlines the progression of wafer sizes over the years, highlighting the significant jump in diameter that occurred during this period:
Year | Wafer Diameter (inches) |
---|---|
1970s | 2 – 3 |
1980s | 4 – 5 |
1990s | 6 – 8 |
2000s | 12 |
As the industry continues to evolve, the implications of these larger wafers are still being felt today, with economic and geographic factors playing a significant role in the ongoing development of semiconductor manufacturing.
Current Standards and the 300mm Revolution
The semiconductor industry has witnessed a significant transformation with the adoption of the 300mm wafer standard. This shift has been pivotal in meeting the growing demands for higher performance and lower cost per chip. The 300mm wafers offer substantial benefits over their predecessors, primarily due to the increased number of dies that can be produced from a single wafer, thus enhancing the overall manufacturing efficiency.
The transition to 300mm wafers was not just a change in size; it represented a leap in technological capability and infrastructure requirements. The larger wafers necessitated advancements in equipment design, handling, and processing techniques. As a result, the industry saw a surge in investment to upgrade facilities and develop new methods to maintain yield and productivity.
Wafer Diameter (inches) | Die per Wafer Increase (%) | Notable Improvements |
---|---|---|
8 (200mm) | – | – |
12 (300mm) | 125 | Enhanced throughput, improved cost efficiency, and reduced material usage per chip. |
The scalability of silicon wafer diameters has been a cornerstone of the industry’s evolution. From the early days of 1-inch wafers to the current 300mm standard, each increment has been a strategic move to optimize resource utilization and maximize output. The industry continues to explore further advancements, with discussions around the feasibility and benefits of transitioning to even larger wafer sizes in the future.
Technological Drivers of Wafer Size Evolution
Advancements in Lithographic Technologies
The semiconductor industry has witnessed a significant transformation with the introduction of advanced lithographic technologies. High-NA-EUV lithography represents a pivotal development, setting new benchmarks for microchip production. This technology enables the creation of smaller and more complex patterns, essential for the miniaturization of transistors and the consequent increase in chip performance and functionality.
Advancements in lithography have been instrumental in achieving increased integration levels and improved performance. These strides have been made possible through the development of new materials, alternative device architectures, and the optimization of system functionality. The industry’s shift to a top-down approach, characterized by the rise of Foundries and Fabless companies, has been largely influenced by these technological advancements.
Current research in the field of lithography continues to push the boundaries of what is possible. For instance, novel processes are being developed for robust layering on flexible materials, which could open up new applications and further drive the evolution of wafer sizes. As the industry moves forward, the role of lithography in shaping the future of semiconductor manufacturing remains central.
The Role of New Materials and Device Architectures
The semiconductor industry has witnessed a significant transformation with the introduction of new materials and alternative device architectures. These innovations have been pivotal in driving the evolution of semiconductor production since the 1990s. Research in these areas has not only enhanced system functionality but also expanded the range of applications across various fields such as healthcare, automotive, and communication.
Materials like Silicon Carbide (SiC) and Gallium Nitride (GaN) have emerged as game-changers, especially for high-power applications in sectors like 5G and alternative energy. The unique properties of these wide bandgap semiconductors have introduced new complexities in testing and manufacturing, necessitating innovative approaches to maintain efficiency and performance.
The industry’s shift towards these advanced materials and architectures is also reflected in the economic landscape, with a marked transition to a "top-down" industry approach. Foundries and Fabless companies have become instrumental in shaping the semiconductor production ecosystem, leveraging these technological advancements to achieve increased integration levels and improved performance.
Integration Levels and Performance Improvements
The relentless pursuit of higher integration levels and performance improvements has been a cornerstone of semiconductor evolution. The miniaturization of transistors and the refinement of lithographic technologies have enabled the industry to pack more functionality into smaller areas, leading to significant gains in performance and energy efficiency. This trend is exemplified by the progression from micro-scale to nano-scale device features.
Advancements in semiconductor technology have not only been about scaling down. They also encompass the integration of diverse systems to enhance overall device capabilities. For instance, modern automotive applications demand semiconductors that combine performance with reliability, integrating systems such as Advanced Driver-Assistance Systems (ADAS), vehicle electrification, and power management.
The table below highlights the relationship between integration levels, device performance, and wafer size over time:
Year | Integration Level | Device Performance | Wafer Size (mm) |
---|---|---|---|
1990 | Low | Moderate | 150 |
2000 | Medium | High | 200 |
2010 | High | Very High | 300 |
2020 | Ultra-High | Extreme | 300 |
As the industry continues to innovate, the synergy between integration and performance remains a driving force behind the push for larger wafer sizes, enabling economies of scale and meeting the growing demand for sophisticated electronic devices.
Economic and Geographic Influences
Market Dynamics and the Move to East Asia
The semiconductor industry has witnessed a significant geographical shift towards East Asia, a change that has been shaped by market dynamics and strategic business decisions. In the 2010s, the focus on customer intimacy and demand responsiveness became pivotal, driving the growth of chip-making capacity in the region. This transition was influenced by the need for rapid response to new product transitions and the demands of lead firms.
The US-China trade war and subsequent export restrictions have further influenced the semiconductor supply chain, emphasizing the geopolitical importance of the industry. The pandemic and rising nationalism have also played roles in shaping the political economy of semiconductors, leading to strategic decisions that impact key players like TSMC and others in the region.
The following table illustrates the market share distribution in 2022, highlighting the significant presence of East Asian countries in the semiconductor market:
Region | Market Share (%) |
---|---|
US | 48 |
East Asia (including China) | 43 |
These figures underscore a paradigm shift in the semiconductor ecosystem, with East Asia emerging as a formidable force in the global market.
Foundries and Fabless Companies: A Top-Down Industry Approach
The semiconductor industry has witnessed a significant transformation with the rise of Foundries and Fabless companies, representing a top-down approach to manufacturing. Fabless companies focus on design and innovation without the overhead of owning production facilities, often headquartered in regions where production costs would be higher. Conversely, foundries operate the manufacturing plants, strategically located in areas with lower labor costs to optimize expenses.
This bifurcation has led to a symbiotic relationship where fabless companies can leverage the manufacturing prowess of foundries to bring products to market more efficiently. The table below illustrates the geographical distribution of fabless companies and foundries, highlighting the economic rationale behind their locations.
Region | Fabless Company Headquarters | Foundry Locations |
---|---|---|
North America | High concentration | Fewer facilities |
Asia | Growing presence | Majority of plants |
Europe | Moderate presence | Selected locations |
The evolution of this industry structure has been driven by factors such as increased integration levels, performance improvements through advanced technologies, and the need for cost-effective production. As semiconductor production continues to evolve, the relationship between fabless companies and foundries remains a cornerstone of the industry’s economic and geographic landscape.
Investment Trends and Capacity Expansion
The semiconductor industry is witnessing a significant surge in investment, driven by the escalating demand for advanced electronics. Global semiconductor capacity is expected to increase 6.4% in 2024, reaching a new zenith of over 30 million wafers per month. This expansion is fueled by substantial financial commitments from industry leaders aiming to meet the burgeoning market needs.
Investments are not only directed towards increasing the sheer volume of production but also towards enhancing the sophistication of manufacturing facilities. The table below encapsulates recent investment announcements and their projected impacts on capacity:
Company | Investment (USD) | Additional Capacity (wpm) |
---|---|---|
Company A | $5 Billion | 500,000 |
Company B | $3 Billion | 300,000 |
Company C | $7 Billion | 700,000 |
These investments are indicative of the industry’s commitment to scaling up production capabilities while also addressing the need for more advanced and efficient manufacturing processes. The trend towards capacity expansion is not only a response to current demands but also a strategic move to position companies for future growth in a highly competitive market.
Challenges and Innovations in Wafer Manufacturing
Complexities in Scaling Up Wafer Size
As the semiconductor industry pushes the boundaries of technology, scaling up wafer size presents a myriad of challenges. The transition to larger wafers is not merely a question of size, but a complex interplay of technological and material constraints. For instance, the demand for larger wafer sizes necessitates the growth of proportionally larger boules, the cylindrical crystals from which wafers are sliced. This escalation in size can introduce difficulties in maintaining crystal purity and structural integrity during growth and processing.
The complexities are further compounded by the need to ensure compatibility with existing manufacturing processes. As wafers increase in size, equipment and tools must also be scaled up or redesigned, leading to significant capital investments. Moreover, larger wafers are more susceptible to defects, which can reduce yield and increase production costs. The table below summarizes some of the key challenges associated with scaling up wafer size:
Challenge | Impact on Manufacturing |
---|---|
Crystal Growth | Difficulty in maintaining purity and integrity |
Equipment Scaling | Capital investments for new or modified tools |
Defect Susceptibility | Reduced yield and increased costs |
Addressing these challenges requires innovative solutions that balance the benefits of larger wafers with the practicalities of manufacturing. As the industry continues to evolve, manufacturers must navigate these complexities to meet the escalating demand for advanced semiconductor devices.
Innovative Solutions for Enhanced Yield and Efficiency
The semiconductor industry is witnessing a transformative era where innovative solutions are pivotal for enhanced yield and efficiency. One such breakthrough is the integration of Artificial Intelligence (AI) and Machine Learning (ML) into the manufacturing process. These technologies offer actionable insights across various silos within a fabrication plant, including wafer production, equipment optimization, and design adjustments.
To illustrate the impact of AI and ML, consider the following benefits:
- Predictive maintenance to preempt equipment failures
- Real-time process optimization for consistent quality
- Enhanced defect detection through advanced imaging and data analysis
- Yield forecasting to better manage production schedules
These advancements not only streamline operations but also contribute to significant cost savings and improved time-to-market for semiconductor products. As the industry continues to scale, the role of AI and ML in driving efficiency will become increasingly central, marking a new chapter in the evolution of wafer manufacturing.
Environmental and Sustainability Considerations
The semiconductor industry is increasingly focusing on environmental and sustainability issues, recognizing the importance of these factors in long-term viability. One of the most widely adopted approaches to increased sustainability among semiconductor manufacturers has been a shift to the use of renewable energy. This transition not only aligns with global sustainability goals but also helps companies mitigate the risk of fluctuating energy costs.
In addition to energy sourcing, manufacturers are implementing various strategies to minimize their environmental footprint. These include:
- Reducing water usage and improving recycling processes
- Lowering chemical waste through advanced waste management systems
- Adopting materials and processes with lower environmental impact
- Enhancing energy efficiency across production facilities
These efforts are not only environmentally responsible but also contribute to cost savings and improved public perception of the industry. As the sector continues to grow, the integration of sustainability practices will likely become a standard, driven by both regulatory pressures and consumer demand.
Future Outlook and Emerging Trends
Beyond 300mm: The Next Frontier in Wafer Size
As the semiconductor industry continues to scale new heights, the transition beyond 300mm wafers is becoming a focal point for strategic planning. The rise in the production capacity of larger wafers is a testament to the industry’s relentless pursuit of efficiency and cost-effectiveness. Historically, yield has been a critical concern, with larger wafer sizes often leading to decreased yield. However, advancements in manufacturing technologies are poised to overturn this trend.
The industry’s push towards larger wafers is driven by the need to keep up with the increasing demand for high-performance semiconductors. The adoption of 15-nanometer process technology and the integration of wide-bandgap semiconductors are indicative of the relentless innovation in the field. These advancements not only enhance the capabilities of semiconductor devices but also necessitate the development of new packaging solutions to accommodate the changes in wafer size.
The economic rationale for this shift is clear: larger wafers mean more chips per wafer and potentially lower costs per chip. This is particularly important as the industry faces intense competition and pressure to deliver more cost-effective solutions. The entry of new players in the power semiconductor market, offering a variety of package configurations and industry-best figures of merit, underscores the dynamic nature of this sector.
Potential Disruptions from Alternative Technologies
The semiconductor industry is on the cusp of potential disruptions as alternative technologies challenge the status quo. Advanced semiconductor packaging trends, such as 2.5D and 3D hybrid bonding, are at the forefront of this transformation. These packaging methods offer significant advantages in terms of performance and form factor, making them particularly relevant for applications in Artificial Intelligence (AI) and High-Performance Computing (HPC).
In addition to packaging innovations, the industry is also exploring alternative communication methods within chips. Optical communication, for instance, promises to overcome the limitations of electrical interconnects by offering higher bandwidth and lower power consumption. This could lead to a paradigm shift in how data is transferred within and between semiconductor devices.
The table below summarizes some of the key alternative technologies and their potential impact on the semiconductor industry:
Technology | Impact | Relevance |
---|---|---|
2.5D/3D Hybrid Bonding | Enhanced performance, smaller form factor | AI, HPC |
Optical Communication | Higher bandwidth, lower power | Data transfer |
As these technologies mature, they may redefine the landscape of semiconductor manufacturing, leading to new design paradigms and possibly altering the trajectory of wafer size evolution.
Strategic Planning for the Semiconductor Roadmap
Strategic planning for the semiconductor roadmap is a critical component in guiding the industry towards future milestones. The semiconductor industry’s evolution has been marked by a series of strategic decisions that have shaped its current state and will continue to influence its trajectory. The roadmap serves as a blueprint, outlining the necessary steps to achieve desired outcomes in technology, production capacity, and market positioning.
Recent updates, such as the March 2024 news from Sourcengine, highlight the ongoing expansion efforts within the industry. Tower Semiconductor’s plan to produce 80,000 wafers per month is a testament to the aggressive scaling strategies employed by key players. This planned facility is a step in Tower Semiconductor’s overall strategic goal of expanding its global operations.
To ensure the roadmap remains relevant and actionable, it must consider several factors:
Conclusion
The journey of semiconductor manufacturing has been marked by relentless innovation and geographical shifts, primarily towards East Asia, driven by market demands and the pursuit of technological advancements. The evolution of wafer size is a testament to the industry’s commitment to progress, as seen in the transition to larger wafers and finer process technologies, such as the 15-nanometer nodes for NAND flash memories. Investments like Infineon’s €1.6 billion in a new 300-millimeter chip factory underscore the industry’s focus on long-term growth and efficiency. As semiconductor production continues to adapt to a ‘top-down’ approach, with Foundries and Fabless companies at the forefront, the roadmap for future developments remains guided by the need for increased integration, performance enhancement, and the exploration of new materials and device architectures. The semiconductor industry’s trajectory promises further innovation, ensuring its pivotal role in various sectors from healthcare to communication, and beyond.
Frequently Asked Questions
How has the semiconductor wafer size evolved over time?
The semiconductor wafer size has evolved from smaller diameters in the early days of the industry to larger sizes to increase yield and efficiency. The industry standard has moved from wafers as small as 1 inch in diameter to the current 300mm wafers, with research into even larger sizes ongoing.
What technological advances have driven the evolution of wafer sizes?
Advancements in lithographic technologies, the development of new materials and device architectures, as well as the need for greater integration levels and performance improvements, have all driven the increase in wafer size in semiconductor manufacturing.
Why did semiconductor production shift towards East Asia in the 2010s?
The shift towards East Asia was influenced by market dynamics such as customer intimacy and demand responsiveness, along with the region’s growing chip-making capacity and the demands of lead firms for new product transitions.
What challenges are associated with scaling up wafer size?
Scaling up wafer size presents several challenges, including the need for more sophisticated equipment, the potential for increased defects, and the complexities of handling larger wafers without compromising yield and efficiency.
How do economic and geographic factors influence the semiconductor industry?
Economic factors such as investment trends, capacity expansion, and market dynamics, along with geographic shifts in production to areas like East Asia, have a significant impact on the semiconductor industry’s evolution and strategic planning.
What is the future outlook for wafer sizes in semiconductor manufacturing?
The future outlook suggests a potential move beyond the current 300mm wafers to even larger sizes, as the industry seeks to improve efficiency and yield. However, this evolution will also depend on overcoming technical challenges and adapting to new market demands and alternative technologies.