The Future of Production: Innovations in Automated Manufacturing Systems
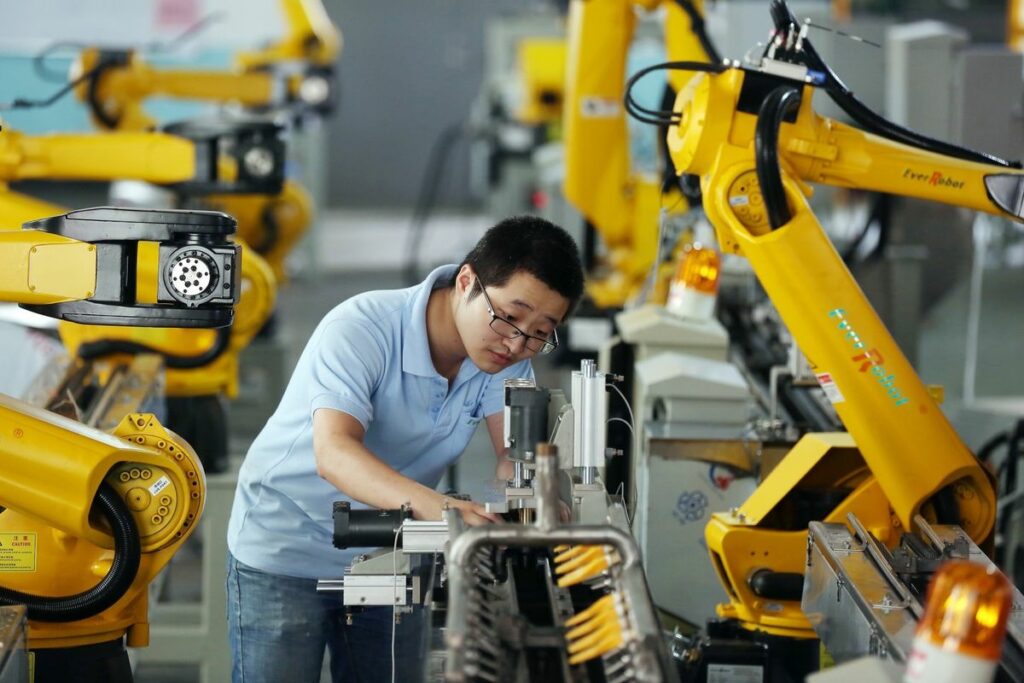
In a rapidly digitizing world, manufacturing is set to experience profound transformations. The integration of digital technologies and automation will revolutionize every aspect of the manufacturing process, from product design to production, distribution, and service delivery. Smart factories, powered by AI, machine learning, and connected devices, will optimize efficiency, quality, and customer satisfaction. This article explores the future of production through the lens of automated manufacturing systems, highlighting key innovations that are shaping this dynamic field.
Key Takeaways
- Automated manufacturing systems are leveraging AI and machine learning to create smart factories with enhanced efficiency and reduced downtime.
- The rise of 3D printing is enabling customization and complex design, disrupting traditional supply chains and promoting on-demand production.
- Collaboration between human workers and machines is essential, with a focus on workforce transformation and the development of new skills.
- Automation presents both challenges and opportunities, necessitating a balance between job creation and technological advancement while ensuring safety and quality.
- Trends such as IoT, sustainable automation practices, and evolving supply chain dynamics are critical in shaping the future of automated manufacturing.
Revolutionizing Production: The Rise of Smart Factories
The Integration of AI and Machine Learning
The integration of Artificial Intelligence (AI) and Machine Learning (ML) into automated manufacturing systems marks a significant leap forward in industrial automation. These technologies enable machines to learn from data, adapt to new scenarios, and improve their performance over time without human intervention. The benefits of this integration are manifold, leading to smarter, more adaptive automation systems that can handle complex tasks with greater efficiency.
AI-driven frameworks are now at the forefront of test automation tools, offering capabilities such as automatic generation and optimization of test cases, and the prediction of potential defects. This not only enhances the efficiency and accuracy of testing but also significantly reduces the time to market for new software products.
To fully harness the power of AI and ML in automated manufacturing, certain steps can be taken:
- Invest in Training: Upskilling the workforce to understand AI and ML concepts is crucial.
- Collaborate with Data Scientists: Working with experts to develop tailored AI models can optimize testing processes.
- Embrace Complexity: Building in-house expertise in AI and ML is essential for tackling advanced automation challenges.
- Prioritize Data Quality: High-quality test data is vital for the accuracy of AI-powered tools.
- Promote Collaboration: Encouraging teamwork between testers and data scientists fosters innovation in test automation.
Real-time Data and Interconnected Systems
The advent of the Internet of Things (IoT) has transformed manufacturing into a realm where machines, equipment, and devices are intricately connected. This network of interconnected systems harnesses real-time data to streamline operations and enhance decision-making processes. By leveraging this data, manufacturers can optimize resource allocation and supply chain management, leading to improved operational efficiency.
The integration of digital technologies with physical manufacturing processes is blurring the boundaries between the physical and digital worlds. As a result, the concept of ‘smart factories’ is becoming more prevalent, where seamless production processes are enabled by this symbiotic relationship. The benefits are clear: increased efficiency, reduced downtime, and a notable improvement in product quality.
Future directions point towards an infrastructure that unites data from all sources with business and technology tools. This will facilitate innovation, R&D, operating models, and business growth. The table below highlights the impact of real-time data on key manufacturing metrics:
Metric | Before IoT Integration | After IoT Integration |
---|---|---|
Efficiency | Moderate | High |
Downtime | Frequent | Reduced |
Product Quality | Standard | Improved |
Decision-making | Slower | Rapid |
These advancements are driven by the continuous development of artificial intelligence, which promises to further revolutionize the landscape of automated manufacturing systems.
Enhancing Efficiency and Reducing Downtime
In the realm of automated manufacturing, efficiency and downtime reduction are paramount. Manufacturers are leveraging the power of ongoing process optimization to identify and eliminate inefficiencies. This continuous refinement is not only about maintaining the status quo but actively enhancing production capabilities.
Lean manufacturing principles are instrumental in this pursuit. By streamlining operations and reducing unnecessary steps, companies can significantly cut costs while maintaining or even improving product quality. Just-in-time inventory management and continuous improvement methodologies, such as Six Sigma or Kaizen, further contribute to a culture of efficiency.
The integration of AI and machine learning has been a game-changer, particularly in testing processes. With the help of AI algorithms, testing is not only more efficient but also more accurate, reducing the risk of human error. This technological synergy is crucial for catching bugs early in the development cycle, minimizing both the time and resources required for fixes.
Here’s a snapshot of the benefits:
- Improved efficiency in testing processes
- Enhanced accuracy through AI algorithms
- Reduced risk of human error
- Cost-effective testing solutions
- Reduce long-term costs by catching bugs early
- Minimize time and resources for bug fixes with automated testing
The Impact of 3D Printing on Manufacturing Paradigms
Customization and Complex Design
The advent of 3D printing technology has ushered in a new era of manufacturing, where the constraints of traditional methods are being dismantled. This innovation allows for the creation of designs that were once considered too intricate or financially unfeasible. For example, 3D printing enables the creation of complex and custom structures that might take months to create with traditional manufacturing methods.
The flexibility of 3D printing is not just in design but also in its ability to accommodate changes swiftly. This is a stark contrast to conventional production, where even minor modifications can lead to significant delays and increased costs. The table below illustrates the differences in adaptability and risk management between traditional and 3D printing methods:
Aspect | 3D Printing | Traditional Manufacturing |
---|---|---|
Adaptability | High; accommodates changes quickly. | Low; changes may require major revisions. |
Efficiency & Risk | Builds quality in from the start. | Risk of delays and cost overruns. |
By integrating 3D printing into production lines, manufacturers can not only enhance the aesthetic and functional aspects of their products but also significantly reduce the time-to-market. This shift towards on-demand production models is transforming the industry, making it more responsive to consumer needs and market trends.
Disruption of Traditional Supply Chains
The advent of 3D printing technology has been a game-changer for manufacturing, breaking barriers that once seemed insurmountable. By enabling on-demand production, 3D printing reduces the need for extensive inventories and mitigates risks associated with over-reliance on specific suppliers or geographies.
Supply chain resilience is now a focal point for manufacturers, especially after recent global events that have highlighted the vulnerability of traditional supply networks. The ability to produce parts locally and on-demand means that manufacturers can respond more swiftly to market changes and customer needs, bypassing lengthy and often complex supply chains.
Here are some key advantages of 3D printing in supply chain management:
- Reduced costs through elimination of excess inventory
- Enhanced ability to produce complex and customized designs
- Greater flexibility in responding to supply chain disruptions
- Shorter lead times from design to production
In conclusion, 3D printing is democratizing manufacturing, offering numerous advantages such as reduced costs and increased flexibility, which are essential for staying competitive in today’s fast-paced market.
On-demand Production and Waste Reduction
The advent of 3D printing in manufacturing has ushered in a new era of on-demand production, where items are created as they are needed, rather than in large batches. This shift not only streamlines the manufacturing process but also significantly cuts down on waste, as products are made to order, reducing the need for excess inventory that may never be used.
By leveraging just-in-time inventory management and lean manufacturing principles, companies are able to minimize waste and optimize resource utilization. These practices ensure that materials are used more efficiently, with a focus on producing what is needed, when it’s needed, and in the exact quantity required.
Innovative solutions for sustainable manufacturing are becoming increasingly prevalent. Manufacturers are investing in the development of biodegradable, bio-based materials and integrating renewable energy sources into their operations. The table below highlights the impact of these practices on waste reduction:
Practice | Waste Reduction Impact |
---|---|
Just-in-Time Inventory | Minimizes excess stock |
Lean Manufacturing | Reduces unnecessary steps |
Bio-based Materials | Lowers environmental impact |
Renewable Energy | Decreases carbon footprint |
As the industry continues to evolve, these sustainable practices are expected to become the standard, driving the manufacturing sector towards a more eco-friendly and efficient future.
The Synergy of Human and Machine in Automated Manufacturing
Workforce Transformation and Skill Development
As the landscape of manufacturing shifts towards automation and AI, the upskilling of the workforce becomes imperative. The transformation underscores the necessity for skill development and training to deploy transformative technology in everyday tasks. According to the World Economic Forum, significant reskilling could lead to the creation of 133 million jobs by 2022, highlighting the positive potential of technological change when paired with the right educational strategies.
Investments in workforce training programs are essential to bridge the skills gap in the manufacturing industry. These programs not only prepare workers for the challenges of automation and AI but also foster collaboration between humans and machines, leading to heightened productivity and innovation. Manufacturers are increasingly focusing on upskilling current employees and expanding their workforce to include new talent, particularly in science, technology, engineering, and mathematics (STEM) fields.
- Upskilling current employees to manage new technologies
- Recruiting and training new talent, especially in STEM
- Collaborating with educational institutions for outside training
- Fostering human-machine collaboration for enhanced productivity
Collaborative Robotics and Enhanced Productivity
The Rise of Collaborative Robots is transforming industrial automation, marking a significant shift in how production lines are conceived and operated. These advanced machines work alongside humans, not just to enhance productivity but also to foster a more dynamic and adaptable manufacturing environment.
Collaborative robots, or ‘cobots’, are designed to operate in conjunction with human workers, bringing together the best of both worlds: the precision and consistency of robotic systems with the cognitive and problem-solving abilities of humans. This synergy has led to a new era of industrial efficiency where the boundaries between human and machine capabilities are increasingly blurred.
To fully harness the potential of collaborative robotics, manufacturers are investing in training programs that upskill their workforce. The focus is on areas such as robotics, data analysis, and programming, which are critical for managing a more automated environment. Here’s a snapshot of the key areas of development:
- Robotics engineering and maintenance
- Advanced programming for automation
- Data analysis and interpretation
- Safety and operational training
By equipping employees with these skills, companies are not only enhancing productivity but also ensuring a future-proof workforce capable of driving innovation and maintaining a competitive edge in the market.
The Human Touch in a Digitalized Industry
In the midst of rapid automation, the value of human insight and expertise remains irreplaceable. Workers are not being replaced, but rather redeployed to roles that leverage their unique human skills—creativity, problem-solving, and emotional intelligence. As machines handle repetitive tasks, employees are free to focus on areas that require a human touch, such as quality control, design, and customer service.
The collaboration between humans and machines is creating new job categories and transforming existing ones. Below is a list of key areas where human skills are crucial in a digitalized manufacturing landscape:
- Quality Assurance: Ensuring the final product meets standards
- Design and Innovation: Developing new products and improving existing ones
- Customer Interaction: Providing personalized service and support
- Maintenance and Troubleshooting: Addressing complex issues that machines cannot
- Training and Development: Educating the workforce on new technologies
This synergy is not just about maintaining human roles; it’s about enhancing them. By working alongside advanced technologies, employees can achieve a higher level of productivity and job satisfaction. The challenge for industry leaders is to foster an environment where this partnership thrives, ensuring that the human element remains a cornerstone of manufacturing excellence.
Navigating the Challenges and Opportunities of Automation
Balancing Job Creation with Technological Advancement
The advent of automation in manufacturing has sparked a critical debate on the balance between job creation and technological advancement. The World Economic Forum suggests that with significant reskilling, the rise of automation could lead to the creation of 133 million jobs by 2022. This optimistic outlook hinges on the industry’s commitment to developing the workforce’s capabilities in tandem with technological progress.
To harness the potential of automation, manufacturers must prioritize investment in training programs. These programs should focus on skills such as robotics, data analysis, and programming, which are essential for operating and maintaining advanced machinery. A culture of continuous learning and career advancement opportunities will not only boost productivity and innovation but also help in attracting and retaining skilled workers.
The reshaping of the workforce is evident as new roles emerge in robotics engineering, maintenance, and programming. The collaboration between humans and robots exemplifies the modern manufacturing landscape, where human ingenuity is amplified by machine precision and efficiency. Below is a list of key areas where manufacturers are focusing their training efforts:
- Robotics and automation
- Data analysis and interpretation
- Advanced programming techniques
- Maintenance and engineering of automated systems
- Creative problem-solving and innovation
Training for a New Era of Manufacturing
As the manufacturing landscape is reshaped by automation and AI, the demand for a skilled workforce adept in these technologies is surging. Upskilling and retraining initiatives are becoming indispensable to prepare employees for the digital transformation of the industry. These programs focus on imparting knowledge in robotics, data analysis, and programming, which are pivotal in enhancing productivity and fostering innovation.
Investing in workforce development not only equips employees with the skills necessary for modern manufacturing but also contributes to job satisfaction and retention. A culture of continuous learning is essential, as it encourages workers to adapt to new challenges and seize opportunities for career growth. The table below outlines key areas of focus for training programs in the era of automated manufacturing:
Skill Area | Description |
---|---|
Robotics | Understanding and operating automated systems and machinery. |
Data Analysis | Interpreting and leveraging data to improve processes. |
Programming | Developing software for machine control and process automation. |
The transition to a more digital and automated industry necessitates a collaborative effort between employers, educational institutions, and policymakers. By aligning training programs with the evolving needs of the manufacturing sector, we can ensure a workforce that is not only competent but also innovative and ready to tackle the challenges of tomorrow.
Maintaining Safety and Quality in High-Automation Environments
In the realm of high-automation environments, maintaining safety and quality is paramount. Automated systems mitigate risks by reducing the need for direct human intervention in potentially dangerous tasks, thus providing a safer working environment. The implementation of UL 508 control panels is a testament to the industry’s commitment to safety and efficiency. These panels are crucial in robot cell automation, ensuring electrical safety measures are met and integrated seamlessly for a robust industrial setup.
To uphold the highest standards of quality, updating industrial machine controls is imperative. This not only aligns with evolving safety regulations but also addresses the dynamic needs of businesses. As technology advances, the necessity for upgrades becomes more pronounced, ensuring that safety and quality are not compromised.
Security measures are equally important in safeguarding against cyber threats. Protecting sensitive data and infrastructure is a critical aspect of maintaining the integrity of automated manufacturing systems. By focusing on security, companies can prevent unauthorized access and potential disruptions to their operations.
Predicting the Future: Trends Shaping Automated Manufacturing
The Role of IoT in Advanced Manufacturing Systems
The Internet of Things (IoT) has become a cornerstone of modern manufacturing, enabling a level of connectivity and intelligence within factories that was once unimaginable. By integrating advanced sensors and devices, manufacturers can now monitor and control operations with incredible precision, leading to a significant boost in efficiency and productivity.
IoT’s impact extends beyond mere monitoring; it facilitates predictive maintenance, ensuring that equipment is serviced before breakdowns occur, thus minimizing downtime. This proactive approach to maintenance is revolutionizing how factories operate, shifting from reactive to predictive strategies.
The benefits of IoT in manufacturing are numerous, including:
- Enhanced operational efficiency through real-time monitoring and control
- Improved product quality with continuous performance data
- Optimized resource allocation by analyzing vast amounts of data
- Streamlined supply chain management, leading to reduced costs and increased transparency
As the industry continues to evolve, the role of IoT will only grow more significant, shaping the future of automated manufacturing and establishing new benchmarks for what smart factories can achieve.
Sustainable Practices and Eco-friendly Automation
As the world confronts the challenges of climate change, sustainable manufacturing practices are becoming a cornerstone of the industry. Innovative solutions for sustainable manufacturing are being adopted by forward-thinking companies, aiming to reduce waste, conserve resources, and minimize environmental impact.
The integration of sustainable practices into automated manufacturing systems is not just about meeting societal expectations; it also opens doors to significant cost savings, enhanced brand reputation, and long-term business resilience. Manufacturers are now optimizing motor control to reduce CO2 emissions, with some systems achieving up to a 60% reduction.
Sustainable Initiative | Expected Outcome |
---|---|
Renewable Energy Adoption | Reduced carbon footprint |
Eco-friendly Materials | Lower environmental impact |
Waste Reduction Strategies | Enhanced resource efficiency |
Embracing these eco-friendly automation technologies is essential for the socio-economic impact of manufacturing, ensuring the sector evolves in harmony with our planet’s ecological balance.
The Evolution of Supply Chain Dynamics
As the global manufacturing landscape evolves, supply chain dynamics are undergoing significant transformations. Technological advancements and sustainability integration are leading the charge towards more decentralized production models. The adoption of 3D printing and additive manufacturing continues to challenge traditional processes, fostering greater customization and waste reduction.
Supply chain resilience has become a focal point, especially in the wake of disruptions from natural disasters and pandemics. To enhance resilience, strategies such as diversifying supply sources, promoting local production, and developing robust logistics networks are being prioritized. These measures aim to mitigate risks and maintain operational continuity under adverse conditions.
Strategy | Objective | Expected Outcome |
---|---|---|
Diversifying Supply Sources | Minimize Dependency | Reduced Risk of Disruption |
Encouraging Local Production | Strengthen Local Economies | Enhanced Responsiveness |
Developing Logistics Networks | Improve Distribution Efficiency | Greater Supply Chain Agility |
In navigating these complexities, manufacturers must remain agile, adapting to geopolitical shifts, trade agreements, and the unpredictable nature of global events. The future of manufacturing sectors will likely see a harmonious blend of innovation, eco-friendly practices, and strategic supply chain management.
Embracing the Future: The Synergy of Humans and Automation in Manufacturing
As we stand on the brink of a new era in manufacturing, it is clear that the fusion of automation, robotics, and digital technologies is not just reshaping the industry—it is redefining the very nature of production. The future promises smart factories where efficiency and innovation are paramount, and where the synergy between human creativity and machine precision creates products of unparalleled quality. The challenge ahead lies in ensuring a workforce that is adept at navigating this high-tech landscape, fostering a culture of continuous learning and adaptation. By embracing these changes, the manufacturing sector can look forward to a future that is not only more productive but also more sustainable, flexible, and responsive to the ever-evolving demands of a dynamic global market.
Frequently Asked Questions
How are smart factories changing the manufacturing landscape?
Smart factories are revolutionizing manufacturing by integrating AI, machine learning, and connected devices to optimize efficiency, quality, and customer satisfaction. They enable seamless production processes with real-time data and interconnected systems.
What role do automation and robotics play in modern manufacturing?
Automation and robotics enhance efficiency, precision, and speed in manufacturing. They help meet increasing customer demands with high-quality products and play a critical role in reducing errors and workplace accidents by optimizing production processes.
What opportunities does automation create for the manufacturing workforce?
Automation reinforces the need for human abilities in manufacturing, creating jobs for managing automated systems and engineering robotics. It emphasizes the value of distinctly human skills like creativity, critical thinking, and innovation.
How is 3D printing transforming the manufacturing industry?
3D printing, or additive manufacturing, enables the creation of complex, customized designs without traditional constraints. It disrupts supply chains, reduces waste, and supports on-demand production, leading to significant industry transformation.
What is the significance of human-machine collaboration in manufacturing?
Collaboration between human workers and intelligent machines unlocks new levels of productivity, creativity, and innovation. It requires workforce transformation and training to adapt to an increasingly automated industry.
What are the predicted trends shaping the future of automated manufacturing?
Key trends shaping automated manufacturing include the integration of IoT, sustainable and eco-friendly practices, and evolving supply chain dynamics. These trends will continue to drive growth and innovation in the industry.