The Future of Semiconductor Packaging: Innovations and Trends
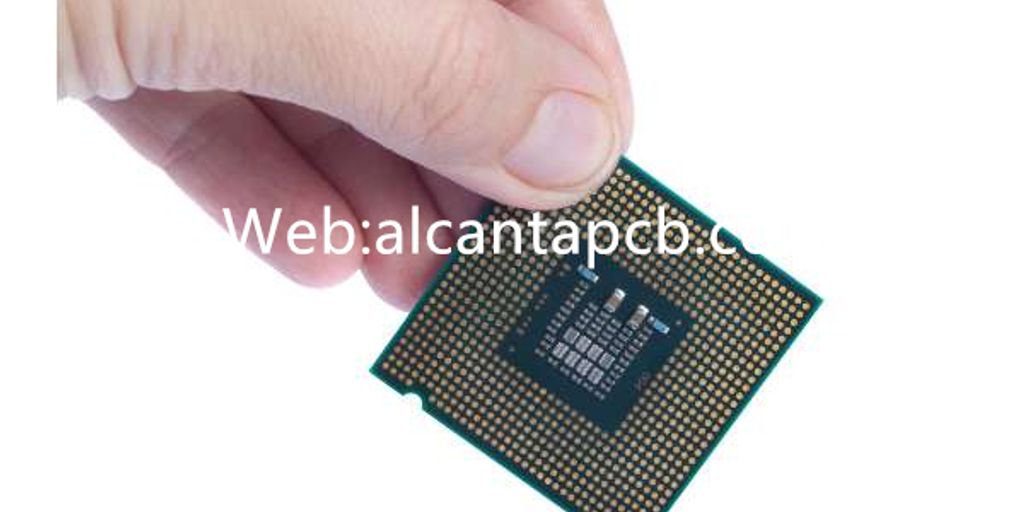
The world of semiconductor packaging is changing fast. New technologies are making chips smaller, faster, and more powerful. This article will explore some of the latest trends and innovations shaping the future of semiconductor packaging. From System-in-Package (SiP) to Through-Silicon Via (TSV) and the role of dielectric materials, we’ll cover it all.
Key Takeaways
- Heterogeneous integration combines different technologies in one package, boosting performance and saving space.
- System-in-Package (SiP) technology is advancing, offering better performance compared to traditional packaging methods.
- Through-Silicon Via (TSV) helps make faster and more efficient connections in modern semiconductor packages.
- New dielectric materials are improving the performance and efficiency of semiconductor packages.
- Regulations and market demands are driving innovation in semiconductor packaging.
Heterogeneous Integration in Semiconductor Packaging
The future of semiconductor packaging is being shaped by the growing need for heterogeneous integration. This approach combines chips with different technologies and functions into a single package, leading to more complex systems with better performance and smaller sizes.
Advancements in System-in-Package (SiP) Technology
System-in-Package (SiP) technology is revolutionizing the world of electronics by allowing multiple chips, passive components, and interconnects to be integrated into a single package. This integration results in higher functionality, better performance, and smaller device sizes.
SiP vs Traditional Packaging
SiP technology stands out from traditional packaging methods by enabling the combination of different types of chips, such as logic, memory, and sensors, into one package. This flexibility allows for the creation of highly customized and application-specific devices.
Applications of SiP
SiP is used in a variety of applications, from consumer electronics to medical devices. It supports the development of complex systems with improved performance and reduced power consumption. This makes it ideal for modern gadgets that require high efficiency and compact design.
Future Developments in SiP
The future of SiP technology looks promising, with ongoing innovations aimed at further enhancing its capabilities. Researchers are working on new methods to improve integration and performance, ensuring that SiP remains at the forefront of semiconductor packaging advancements.
The Role of Through-Silicon Via (TSV) in Modern Packaging
Advantages of TSV
Through-silicon via (TSV) technology is changing semiconductor packaging by allowing high-density interconnects and better performance. TSV enables vertical chip integration through the silicon substrate, making interconnects shorter and reducing signal delays. This leads to higher data transfer rates and improved power efficiency.
TSV Manufacturing Processes
Creating TSVs involves several steps. First, tiny holes are drilled into the silicon wafer. Next, these holes are filled with a conductive material, usually copper. Finally, the wafer is thinned to expose the TSVs, allowing for vertical connections between stacked chips. This process requires precision and advanced equipment.
Market Adoption of TSV
TSV technology is gaining traction in the market, especially in 3D packaging where multiple chips are stacked vertically. This method is popular for making compact electronic devices with better performance and smaller sizes. As the demand for high-performance and miniaturized devices grows, TSV adoption is expected to increase.
Emerging Trends in Dielectric Materials for Packaging
Importance of Dielectric Materials
Dielectric materials are crucial in semiconductor packaging. They insulate different parts of the chip, preventing electrical shorts and ensuring efficient performance. As chips get smaller and more powerful, the need for advanced dielectric materials grows. New interconnect metals need new dielectrics to keep up with the demands of modern technology.
Innovations in Dielectric Technology
The industry is seeing exciting innovations in dielectric technology. One major trend is the development of low-k and ultra-low-k dielectric materials. These materials help reduce signal delay and power consumption. Another innovation is the improvement of dielectric formulations to boost mechanical strength and thermal stability. Additionally, novel materials are being integrated to enable finer interconnect pitches and higher density packaging.
Impact on Performance and Efficiency
Emerging dielectric materials are set to redefine chip performance and efficiency. With the rise of 2.5D and 3D packaging technologies, the demand for materials that support high bandwidth and energy efficiency is increasing. Organic dielectric materials are becoming popular because they offer lower dielectric constants and cost advantages. These materials not only provide the necessary electrical properties but also bring benefits like reduced RC delay and better resistance to copper. As bandwidth requirements exceed 1000 GB/s, innovative dielectric solutions are essential to maintain progress.
2.5D and 3D Packaging Technologies
2.5D packaging is a method where multiple chips are placed side-by-side on an interposer. This interposer can be made from different materials like silicon, organic, or glass. One key advantage of 2.5D packaging is that it allows for better performance and lower power consumption compared to traditional methods.
3D packaging stacks chips vertically, connecting them with Through-Silicon Vias (TSVs). This method saves space and can significantly boost performance. However, it also comes with challenges like heat dissipation and manufacturing complexity.
When comparing 2.5D and 3D packaging, each has its own set of benefits and drawbacks. 2.5D is generally easier to manufacture and offers good performance improvements. On the other hand, 3D packaging provides even greater performance gains but is more complex and costly to produce. Here’s a quick comparison:
Feature | 2.5D Packaging | 3D Packaging |
---|---|---|
Space Efficiency | Moderate | High |
Performance | Good | Excellent |
Manufacturing Complexity | Low to Moderate | High |
Cost | Lower | Higher |
In summary, both 2.5D and 3D packaging technologies are crucial for the future of semiconductor advancements. They each offer unique benefits that can be leveraged depending on the specific needs of the application.
Regulatory Influences on Semiconductor Packaging
Regulations play a crucial role in shaping the semiconductor packaging industry. They ensure safety and compliance while also driving innovation by setting standards that push the boundaries of current technologies. Regulations can accelerate the adoption of advanced packaging solutions by creating a demand for higher performance and environmentally sustainable practices.
Market Drivers and Challenges in Semiconductor Packaging
Key Market Drivers
The semiconductor packaging industry is experiencing strong growth, driven by several key factors. Advanced semiconductor packaging is reshaping the industry by enabling higher performance and miniaturization. Additionally, the demand for consumer electronics, automotive electronics, and IoT devices is pushing the market forward. Regulatory mandates, such as those for driver monitoring systems, also play a significant role in the development and adoption of innovative packaging technologies.
Challenges Facing the Industry
While the industry is growing, it faces several challenges. The rapid pace of technological change often outpaces the development of new packaging materials. Manufacturers must invest heavily in specialized equipment, which can quickly become outdated. Cost pressures and intense competition further complicate the landscape. The need for solutions that align with future trends adds another layer of complexity.
Strategies for Overcoming Challenges
To mitigate these challenges, companies are adopting several strategies:
- Investing in specialized equipment and materials to stay ahead in the market.
- Focusing on modular designs to facilitate integration and future upgrades.
- Exploring biodegradable and eco-friendly materials for sustainable packaging solutions.
- Optimizing costs by leveraging the long-term benefits of advanced packaging technologies.
By implementing these strategies, companies can better navigate the complexities of the semiconductor packaging industry.
Conclusion
In conclusion, the future of semiconductor packaging is bright and full of promise. With new technologies like 2.5D and 3D packaging, and innovations in materials such as dielectric technology, the industry is set to achieve greater heights. These advancements will lead to more powerful, efficient, and compact electronic devices. As we continue to push the boundaries of what is possible, the role of semiconductor packaging will be more important than ever. The journey ahead is exciting, and the potential for growth and innovation is limitless.
Frequently Asked Questions
What is heterogeneous integration in semiconductor packaging?
Heterogeneous integration is when different types of chips are combined into one package. This helps make more complex systems that work better and take up less space.
How does System-in-Package (SiP) differ from traditional packaging?
System-in-Package (SiP) puts multiple chips into one package, unlike traditional packaging that usually holds just one chip. This allows for better performance and smaller devices.
What are the benefits of using Through-Silicon Via (TSV) in modern packaging?
TSV helps connect different layers of chips vertically, making them faster and more efficient. This technology is great for high-performance devices.
Why are dielectric materials important in semiconductor packaging?
Dielectric materials help insulate and protect the electrical parts of a chip. They are crucial for making sure the chip works well and lasts a long time.
What is the difference between 2.5D and 3D packaging?
2.5D packaging uses a special base to connect chips side-by-side, while 3D packaging stacks chips on top of each other. Both methods aim to improve performance and save space.
How do regulations impact semiconductor packaging innovation?
Regulations ensure that semiconductor packaging meets safety and performance standards. They can also drive innovation by setting new requirements that push the industry to develop better technologies.