The Future of Wafer Fabrication: Innovations and Trends
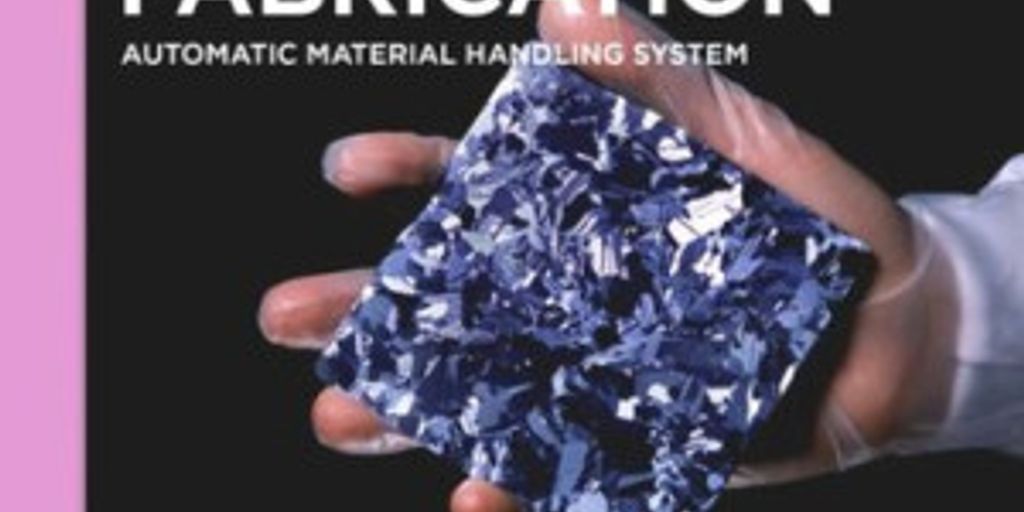
Wafer fabrication is at the heart of the electronics industry, driving the creation of everything from smartphones to advanced computing systems. As we look to the future, new materials, cutting-edge techniques, and innovative trends are set to revolutionize this field. This article explores the latest advancements and what they mean for the future of technology.
Key Takeaways
- New materials like silicon carbide and gallium nitride are making waves in wafer fabrication.
- Advanced processing techniques such as epitaxial growth and atomic layer deposition are enhancing wafer quality.
- 3D integration and stacked wafers promise to boost performance and reduce power consumption.
- Automation and smart manufacturing are streamlining production and improving quality control.
- Sustainability efforts, including energy-efficient processes and recycling, are becoming more important in wafer fabrication.
Emerging Materials in Wafer Fabrication
Silicon Carbide and Gallium Nitride
While silicon is still the main material used in wafer fabrication, there’s a growing interest in alternatives like silicon carbide (SiC) and gallium nitride (GaN). These materials have special properties that make them perfect for certain uses, such as power electronics and high-frequency devices. Combining these materials with silicon wafers can lead to new and better device designs.
Graphene and Other 2D Materials
Graphene and other two-dimensional (2D) materials are also making waves in wafer fabrication. These materials are incredibly thin and have unique electrical properties. They can be used to create faster and more efficient electronic devices. Researchers are exploring how to integrate these 2D materials into existing wafer technologies to push the boundaries of what’s possible.
Compound Semiconductors
Compound semiconductors, which are made from two or more elements, offer another exciting avenue for innovation. These materials can be tailored to have specific electrical properties, making them ideal for specialized applications like optoelectronics and high-speed transistors. The use of compound semiconductors is expected to grow as the demand for advanced electronic devices continues to rise.
Advancements in Wafer Processing Techniques
Epitaxial Growth
Epitaxial growth is a method where crystalline layers are deposited on the wafer surface. This technique allows for the creation of complex structures and heterostructures with improved properties. Epitaxy is crucial for developing advanced silicon wafer technology.
Atomic Layer Deposition
Atomic Layer Deposition (ALD) is a process that deposits thin films of material onto the wafer. This technique is known for its precision and ability to create uniform layers, which is essential for modern semiconductor devices.
Chemical Mechanical Planarization
Chemical Mechanical Planarization (CMP) is a process used to smooth and flatten the wafer surface. This step is vital for ensuring that subsequent layers are evenly applied, which is critical for the performance of the final semiconductor device.
3D Integration and Stacked Wafers
3D integration is a groundbreaking trend in wafer fabrication. Instead of just using traditional 2D scaling, manufacturers are now stacking multiple layers of silicon wafers to create three-dimensional structures. This method boosts transistor density, improves performance, and cuts down on power use. By 2024, 3D integration is expected to become a common practice in silicon wafer manufacturing, especially in the APAC region.
Benefits of 3D Integration
3D integration offers several advantages:
- Increased transistor density
- Enhanced performance
- Reduced power consumption
- Smaller device footprints
Challenges in Stacked Wafer Fabrication
Despite its benefits, 3D integration comes with challenges:
- Thermal management issues
- Complex manufacturing processes
- Higher production costs
Future Prospects
The future of 3D integration looks promising. As technology advances, we can expect:
- Improved manufacturing techniques
- Lower costs
- Broader adoption across various industries
Precision Engineering and Nanofabrication
Miniaturization Techniques
The continuous shrinking of chip sizes demands highly precise and detailed fabrication methods. This miniaturization brings challenges like forming tiny patterns and placing them accurately on the die. Advanced techniques are pushing the boundaries of how small and efficient chips can get. Startups are now using additive manufacturing to innovate in this space.
Advanced Lithography
Lithography is a key process in creating intricate patterns on wafers. New methods, such as extreme ultraviolet (EUV) lithography, are enabling the production of smaller and more complex designs. These advancements are crucial for making next-generation semiconductors that are both powerful and energy-efficient.
Nanofabrication Challenges
Working at the nanoscale introduces unique challenges. Metals used to reduce wiring delays add complexity to the fabrication process. Universities are leading research in nanotechnology, exploring nanoscale transistors and sensors. These innovations hold the potential to unlock new possibilities in electronics.
Automation and Smart Manufacturing in Wafer Fabrication
Role of AI and Machine Learning
Automation and artificial intelligence (AI) are becoming more important in wafer fabrication. By 2024, these technologies will make production faster and better. AI helps predict problems and keeps machines running smoothly. It also finds defects in wafers, making sure they are high quality.
Automated Quality Control
Robots and automated systems are used to handle wafers with great precision. This reduces mistakes and speeds up the process. Automated quality control systems check each wafer for defects, ensuring only the best ones move forward in production.
Smart Factories
Smart factories use advanced technology to make wafer fabrication more efficient. These factories use sensors and data analytics to monitor and control the production process. This helps in making quick decisions and improving overall efficiency. Smart factories are the future of wafer fabrication, combining technology and automation to create better products faster.
Sustainability in Wafer Fabrication
Energy-Efficient Processes
Silicon wafer manufacturers are working hard to use less energy. In the APAC region, they are making big changes to save water, use fewer chemicals, and cut down on energy use. By 2024, these efforts will not only help the environment but also save money.
Recycling and Waste Management
Companies are finding new ways to recycle materials and manage waste better. They are using recycled chemicals and capturing harmful gases to make the process cleaner. These steps are helping to make chip manufacturing more eco-friendly.
Green Materials
Manufacturers are also looking for green materials to use in wafer fabrication. This includes using recycled silicon carbide and other eco-friendly options. These materials help reduce the environmental impact and make the process more sustainable.
Market Trends and Economic Impacts
Growth of 300mm Wafers
The semiconductor industry is seeing a significant shift towards 300mm wafers. These larger wafers allow for more chips to be produced per wafer, which can reduce costs and increase efficiency. This trend is driven by the growing demand for advanced electronics and the need for higher performance in smaller devices.
Economic Benefits of Advanced Materials
Using advanced materials like silicon carbide and gallium nitride in wafer fabrication can lead to better performance and energy efficiency. These materials are becoming more popular in various applications, from electric vehicles to renewable energy systems. The economic benefits include lower energy costs and longer-lasting products, which can save money in the long run.
Global Market Dynamics
The global semiconductor market is highly dynamic, with rapid changes in demand and supply. For instance, between 2020 and year-end 2023, 80 new semiconductor manufacturing projects were announced across the United States alone, projected to create thousands of jobs. This growth is influenced by factors such as technological advancements, geopolitical tensions, and shifts in consumer behavior. The market is expected to continue evolving, with new opportunities and challenges emerging regularly.
Conclusion
In summary, the future of wafer fabrication is bright and full of exciting changes. New materials like gallium nitride and silicon carbide are being explored, offering better performance for certain uses. The shift to larger 300mm wafers is making production more efficient. Plus, 3D integration is allowing for more powerful and energy-saving devices. As these trends continue, we can expect even more amazing advancements in technology, making our electronic devices faster, smaller, and more reliable.
Frequently Asked Questions
What are the new materials being used in wafer fabrication?
New materials like silicon carbide (SiC) and gallium nitride (GaN) are being used. These materials are great for power electronics and high-frequency devices.
How do 3D integrated wafers work?
3D integrated wafers stack multiple layers of silicon wafers. This makes devices faster and use less power.
Why are 300mm wafers important?
300mm wafers are bigger, so they can make more chips at once. This makes production more efficient and cheaper.
What is epitaxial growth?
Epitaxial growth is a method where a crystal layer is grown on a wafer. This helps create complex structures with better properties.
How is AI used in wafer fabrication?
AI helps in automating quality checks and improving manufacturing processes. It makes factories smarter and more efficient.
What are the challenges in nanofabrication?
Nanofabrication involves making very tiny structures, which is hard and requires precision. Challenges include forming fine patterns and placing them accurately.