The Impact of Industrial Automation Systems on Manufacturing Efficiency
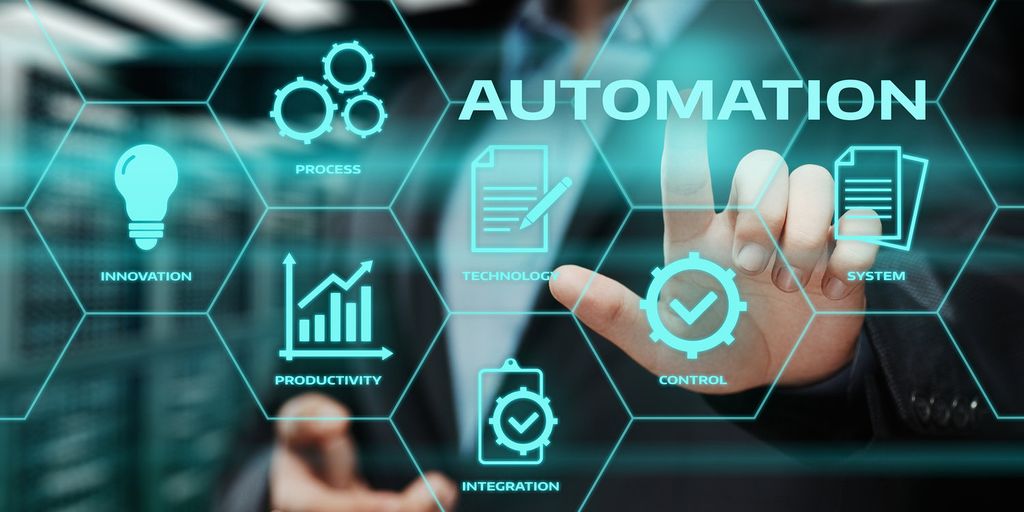
Industrial automation has revolutionized the manufacturing industry by integrating advanced technologies such as robotics, control systems, and information technologies into existing workflows. This transformation has significantly enhanced speed, precision, and efficiency in manufacturing processes. By enabling 24/7 operations, minimizing human error, and accelerating production timelines, industrial automation systems have become indispensable in modern manufacturing.
Key Takeaways
- Industrial automation systems enable round-the-clock operations, significantly boosting productivity.
- Automation minimizes human error, resulting in higher precision and consistent quality in manufacturing.
- Advanced technologies such as robotics and machine learning drive industrial automation systems, enhancing efficiency.
- While the initial investment in automation can be high, the long-term ROI through reduced labor costs and increased output is substantial.
- Industrial automation contributes to safer work environments by reducing workplace hazards and ensuring compliance with safety standards.
Enhancing Productivity Through Industrial Automation Systems
Industrial automation has been a game-changer in the manufacturing industry, transforming the way companies operate and produce goods. It involves using machines and robotics to perform tasks that were once done by humans, making processes faster, more efficient, and cost-effective. Automation can transform your business; improving productivity, optimizing time, enhancing quality and increasing safety in your operations.
Technologies Driving Industrial Automation Systems
As technology advances, industrial automation will undoubtedly play a pivotal role in driving industries toward a future where efficiency knows no bounds. At the core of industrial automation is the desire to improve efficiency and reliability in manufacturing. It leverages technologies such as robotics, control systems, and information technologies to handle tasks that were once manual, repetitive, or dangerous. This transition enables many industries to achieve mass production with minimal human intervention. Industries embracing this transformation will thrive and lead toward a smarter, more efficient, and sustainable world.
Cost Implications of Implementing Industrial Automation
Implementing industrial automation systems involves a significant initial investment. This includes the cost of purchasing and installing the necessary technology and resources. However, the return on investment (ROI) can be substantial as these systems often lead to increased efficiency and productivity over time.
Another significant advantage of industrial automation is the reduced labor costs it brings to the manufacturing industry. The cost of labor is a major expense for businesses, and automating tasks can significantly reduce these costs. Automated systems do not require a salary, benefits, or time off, and they do not get sick or injured. Therefore, businesses can save a considerable amount of money by using automated systems instead of human labor.
Maintenance and upkeep of automated systems are also important considerations. While these systems can reduce operational costs, they do require regular maintenance to ensure they function correctly. This includes routine checks, software updates, and occasional repairs. Despite these costs, the overall savings and efficiency gains often outweigh the expenses associated with maintenance.
Quality Control and Precision in Automated Manufacturing
Consistent Quality Assurance
Automated systems significantly enhance quality control in manufacturing by providing consistent production parameters and minimizing human error. These systems can continuously monitor and adjust processes to ensure that the product meets strict quality standards. Automated quality control (AQC) is the use of automated tools and systems to inspect and test products during the manufacturing process to make sure that they meet predefined criteria.
Advanced Monitoring Systems
Automation systems employ sensors and feedback loops to monitor and adjust processes continuously. These real-time feedback mechanisms ensure that any deviations from the set parameters are immediately corrected, maintaining high levels of precision. For instance, automated machine tools such as CNC machines can ensure a high degree of repeatability and accuracy.
Error Detection and Correction
Automated inspection systems can detect errors throughout various stages of production, allowing them to be corrected before they become an issue. This reduces the likelihood of defective products reaching the market, improving customer satisfaction and reducing the cost of recalls or returns. Automated systems can detect defects and errors in products much faster and more accurately than humans, reducing the likelihood of defective products reaching the market.
Safety and Risk Management in Automated Manufacturing
Reducing Workplace Hazards
Businesses can create a more secure work area for employees by adopting automation. Various manufacturing and industrial plants are hazardous environments, with workers completing challenging tasks alongside heavy machinery. When automated systems complete procedures, it allows employees to handle additional, safer tasks that minimize risks. By removing the necessity for humans to directly interact with dangerous equipment and materials, automation is reducing the risk of workplace accidents.
Emergency Response Systems
Automated systems can perform tasks that are dangerous or hazardous to human workers, reducing the risk of workplace injuries or accidents. This can save businesses money on workers’ compensation claims and reduce the likelihood of lawsuits. Moreover, automated systems can typically be customized to fit different needs and preferences. This is especially useful for manufacturers who may require specific features not available in traditional systems.
Compliance with Safety Standards
By utilizing automation tools with standard docking equipment, companies can protect their workforce while ensuring efficient material handling operations. Automation can be used to improve safety initiatives for industrial workers in a variety of ways, including:
- Enhanced monitoring and control
- Immediate cessation of production if a foreign object is detected
- Customizable safety features to meet specific needs
Scalability and Flexibility of Industrial Automation Systems
Industrial automation systems offer significant advantages in terms of scalability and flexibility, allowing businesses to adapt to changing market demands efficiently. Flexibility also means scalability as the system can scale up or down to meet varying production volumes as needed without significant redesign or downtime.
Adapting to Market Demands
Automated systems can be programmed to perform a wide range of tasks, making it easier for businesses to adapt to changing market demands. This means that businesses can easily increase or decrease production output as needed without having to hire or lay off workers.
Modular System Designs
A key advantage of automation in manufacturing is scalability, which is increasingly possible with the latest generation of technologies. New systems are designed to flexibly produce a range of products and accept a variety of materials, meaning that business leaders can quickly respond to market changes. At the same time, the rapid deployment of automated systems means that businesses no longer need to cease production as their assembly lines and processes are upgraded.
Future-Proofing Manufacturing Operations
One of the defining features of automation in the future will be its adaptability. Systems will become increasingly agile, able to reconfigure themselves rapidly to accommodate changing demands. For instance, a manufacturing plant may seamlessly switch from producing one product to another within hours without extensive retooling.
Environmental Impact of Industrial Automation Systems
Energy Efficiency
Industrial automation systems have significantly improved energy efficiency in manufacturing processes. Automated systems can optimize energy use by precisely controlling machinery and reducing idle times. This leads to substantial energy savings and a lower carbon footprint for manufacturing facilities.
Waste Reduction
Automation plays a crucial role in minimizing waste during production. By ensuring precise measurements and consistent quality, automated systems reduce the amount of defective products and material waste. This not only conserves resources but also decreases the environmental burden of manufacturing operations.
Sustainable Practices
The integration of automation in manufacturing supports sustainable practices. Automated systems can monitor and manage resource use more effectively, promoting the efficient use of raw materials and reducing environmental impact. Additionally, automation enables the implementation of advanced recycling processes and the use of eco-friendly materials, further contributing to sustainability.
Conclusion
Industrial automation has undeniably revolutionized the manufacturing industry, driving unprecedented levels of efficiency, productivity, and cost-effectiveness. By integrating advanced technologies such as robotics and control systems, manufacturers can achieve continuous production, minimize human error, and maintain consistent quality. This transformation not only enhances operational capabilities but also positions businesses to better adapt to evolving market demands. As the industry continues to evolve, companies that embrace automation will be well-equipped to thrive in an increasingly competitive global marketplace.
Frequently Asked Questions
What is industrial automation?
Industrial automation involves using machines, robotics, and control systems to perform tasks that were traditionally done by humans. This transformation increases speed, precision, and efficiency in manufacturing processes.
How does industrial automation enhance productivity?
Industrial automation systems can operate 24/7 without rest, significantly increasing production times and output. They also reduce human errors and accelerate production timelines.
What are the key technologies driving industrial automation systems?
Key technologies include robotics, machine learning, control systems, Programmable Logic Controllers (PLCs), and information technologies.
What are the cost implications of implementing industrial automation?
While the initial investment in industrial automation can be high, it offers a substantial return on investment (ROI) through reduced labor costs, increased efficiency, and lower maintenance and upkeep expenses over time.
How does industrial automation impact quality control in manufacturing?
Automated systems ensure consistent quality assurance through advanced monitoring systems and error detection and correction mechanisms, leading to higher precision and fewer defects.
What are the environmental benefits of industrial automation?
Industrial automation contributes to energy efficiency, waste reduction, and sustainable practices, making manufacturing processes more environmentally friendly.