The Importance of Semiconductor Testing in Modern Manufacturing
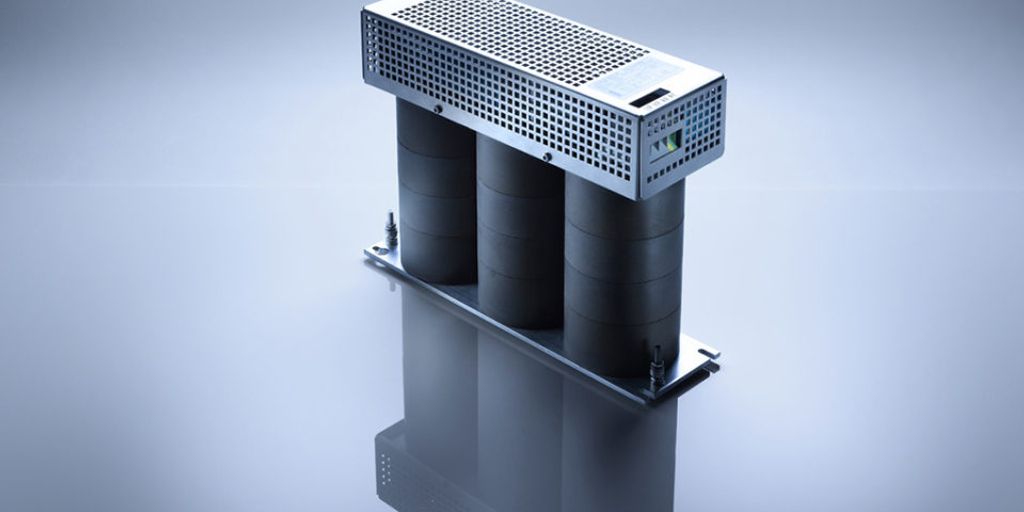
Semiconductors, the tiny powerhouses at the core of our modern electronics, undergo a rigorous journey before they make their way into our devices. The testing process in semiconductor design is vital, ensuring that these minuscule components meet the highest quality standards. In this article, we’ll take you step-by-step through the semiconductor testing process and discuss why it’s absolutely crucial.
Key Takeaways
- Semiconductor testing is essential for ensuring the high quality, reliability, and performance of electronic devices.
- Various methods and techniques, including inspection, measurement, and evaluation, are employed to identify and correct defects in semiconductor manufacturing.
- Challenges such as fabrication defects, functional bugs, and managing lower technology nodes must be addressed during the testing process.
- Advancements in testing technology, such as automation and innovative test equipment, are driving the future of semiconductor testing.
- Effective semiconductor testing significantly reduces recalls and returns, improves market competitiveness, and boosts manufacturer reputation.
The Role of Semiconductor Testing in Quality Assurance
Semiconductor testing plays a crucial role in quality assurance by ensuring that only high-quality semiconductor devices enter the market. This process helps in preventing subpar components from compromising electronic systems’ reliability. Testing identifies defects early, reducing the likelihood of device failures and increasing their overall reliability.
Identifying Defects Early
Early identification of defects is vital in the semiconductor fabrication process. By employing a combination of inspection, measurement, and evaluation techniques, manufacturers can detect and correct defects at an early stage. This not only improves process control but also helps in maintaining high manufacturing yields.
Ensuring Reliability and Performance
Testing verifies that semiconductor devices meet their intended specifications, ensuring they perform as expected in real-world applications. This performance validation is essential for maintaining the reliability and efficiency of electronic systems. The key tests in semiconductor quality control are functional, parametric, and reliability testing.
Maintaining High Manufacturing Yields
Maintaining high manufacturing yields is another critical aspect of semiconductor testing. By identifying and correcting defects early in the production cycle, manufacturers can minimize the risk of producing faulty products. This not only improves the overall quality of the final devices but also helps in maintaining a competitive edge in the global market.
Methods and Techniques in Semiconductor Testing
Inspection Techniques
Inspection techniques in semiconductor testing are crucial for identifying defects early in the manufacturing process. These techniques range from visual inspection to advanced spectroscopy, ensuring device reliability and adherence to Moore’s Law. Visual inspection involves examining the wafer for any visible defects, while advanced spectroscopy can detect minute imperfections that might affect performance.
Measurement Methods
Measurement methods are employed to evaluate the electrical and physical properties of semiconductor devices. Electrical testing, such as parametric testing, measures key parameters like voltage, current, and resistance to ensure devices meet performance specifications. Physical measurements might include dimensions and material properties, ensuring that the devices conform to design requirements.
Evaluation Procedures
Evaluation procedures encompass a series of tests and assessments to verify the functionality and reliability of semiconductor devices. These procedures often include stress testing, where devices are subjected to extreme conditions to evaluate their performance limits. Reliability assessment is an ongoing process throughout the semiconductor fabrication process, aimed at improving the long-term performance and stability of the devices.
Challenges in Semiconductor Testing
Dealing with Fabrication Defects
Fabrication and manufacturing defects are inevitable, particularly for lower technology nodes. These defects can significantly impact the performance and reliability of semiconductor devices, making it difficult to meet the substantial demand for semiconductor devices and compromising the ability to maintain high-quality control standards.
Addressing Functional Bugs
The presence of functional bugs cannot be ruled out in a fabricated chip. Tackling the unknown in semiconductor test and metrology is as crucial as perfecting the known. It is not enough to build complex models; the solution must be comprehensive and adaptable to various scenarios.
Managing Lower Technology Nodes
As semiconductor devices continue to scale down in size, manufacturers face several challenges, including the need for more advanced patterning techniques, thinner layers, and higher-density interconnects. Additionally, smaller devices often generate more heat, necessitating improved thermal management solutions within the package design.
Impact of Semiconductor Testing on Consumer Electronics
Semiconductor testing plays a pivotal role in the consumer electronics industry, ensuring that devices are reliable, efficient, and safe for everyday use. Without these tests, our electronic systems would be far less reliable, efficient, and safe.
Advancements in Semiconductor Testing Technology
Automation in Testing Processes
Automation has revolutionized semiconductor testing by significantly reducing the time and effort required for manual testing. Automated systems can handle complex testing procedures with high precision, ensuring that each device meets stringent quality standards. This not only improves efficiency but also enhances the accuracy of test results, making it easier to identify defects early in the production cycle.
Innovations in Test Equipment
Recent innovations in test equipment have led to the development of more sophisticated and reliable testing tools. For instance, advancements in vertical probe technology offer improved contact reliability and signal integrity for high-frequency and high-speed devices. These innovations enable manufacturers to conduct more thorough and accurate tests, ensuring that only high-quality semiconductor devices enter the market.
Future Trends in Semiconductor Testing
The future of semiconductor testing is poised for exciting developments. One of the top 7 trends in semiconductor testing boards is the integration of artificial intelligence and machine learning algorithms to predict potential defects and optimize testing processes. Additionally, the adoption of 5G technology and the Internet of Things (IoT) will drive the need for more advanced testing solutions to handle the increased complexity and performance requirements of modern devices.
The Economic Importance of Semiconductor Testing
Reducing Recalls and Returns
Semiconductor testing plays a crucial role in minimizing product recalls and returns. By identifying defects early in the production process, manufacturers can ensure that only high-quality semiconductor devices enter the market. This not only saves costs associated with recalls but also enhances customer satisfaction and trust.
Improving Market Competitiveness
Thorough semiconductor testing ensures that products meet high standards of quality and performance, giving manufacturers a competitive edge in the market. High-quality, reliable products are more likely to attract and retain customers, thereby increasing market share and profitability.
Boosting Manufacturer Reputation
A strong reputation for quality and reliability is invaluable in the semiconductor industry. Rigorous testing processes help manufacturers build and maintain a positive reputation, which can lead to increased customer loyalty and brand strength. This, in turn, can result in long-term economic benefits and sustained business growth.
Semiconductor Testing in the Production Cycle
Testing During Fabrication
During the fabrication phase, semiconductor testing is crucial for identifying defects and ensuring that the manufacturing process is on track. Early detection of issues can save significant costs and time by preventing defective wafers from progressing through the production line. This phase often involves:
- In-line testing to monitor the fabrication process.
- Electrical testing to verify the functionality of the circuits.
- Visual inspections to detect physical defects.
Post-Fabrication Testing
Once the fabrication is complete, post-fabrication testing ensures that the final product meets all specifications. This stage includes:
- Functional testing to verify that the chip performs its intended functions.
- Parametric testing to measure electrical characteristics like voltage and current.
- Burn-in testing to identify early-life failures by operating the chip under stress conditions.
Continuous Quality Monitoring
Continuous quality monitoring is essential throughout the semiconductor production cycle to maintain high manufacturing yields and product reliability. This involves:
- Statistical process control (SPC) to monitor and control the production process.
- Yield analysis to identify trends and improve the manufacturing process.
- Regular audits and reviews to ensure compliance with quality standards.
By integrating these testing phases into the production cycle, manufacturers can ensure that only high-quality semiconductor devices reach the market, thereby enhancing their reputation and competitiveness.
Conclusion
In conclusion, semiconductor testing is an indispensable component of modern manufacturing, ensuring the high quality, reliability, and performance of the devices that power our digital world. This meticulous process identifies and rectifies defects early, thereby preventing potential failures and enhancing the overall reliability of electronic systems. By employing a combination of inspection, measurement, and evaluation techniques, manufacturers can maintain high manufacturing yields and continue to innovate in semiconductor technology. As the backbone of modern technology, the rigorous testing of semiconductors not only safeguards the functionality of our devices but also propels the industry forward, shaping the future of innovation and progress.
Frequently Asked Questions
Why is testing essential for semiconductor manufacturing?
Testing ensures that semiconductor devices meet the highest quality standards, operate with precision, and are reliable and safe for use in electronic systems.
What are the main goals of semiconductor testing?
The main goals of semiconductor testing are to identify defects early, ensure reliability and performance, maintain high manufacturing yields, and prevent device failures.
What methods are used in semiconductor testing?
Semiconductor testing employs various inspection, measurement, and evaluation techniques to identify and correct defects, improve process control, and maintain high manufacturing yields.
How does semiconductor testing impact consumer electronics?
Semiconductor testing prevents device failures, enhances user experience, and ensures safety in critical applications, making electronic devices more reliable and efficient.
What challenges are faced in semiconductor testing?
Challenges in semiconductor testing include dealing with fabrication defects, addressing functional bugs, and managing lower technology nodes, which require advanced testing techniques.
How has semiconductor testing technology advanced?
Advancements in semiconductor testing technology include automation in testing processes, innovations in test equipment, and emerging trends that improve the accuracy and efficiency of testing.