The Importance of Wafer Probe Testing in Semiconductor Manufacturing
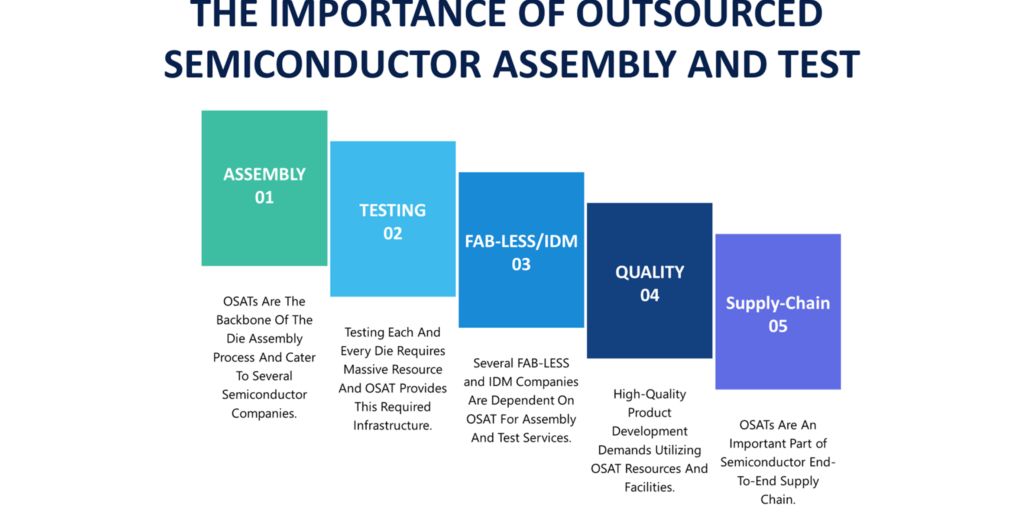
Wafer probe testing is a critical step in semiconductor manufacturing, ensuring the functionality and quality of integrated circuits (ICs) before they proceed to the packaging stage. This process involves the use of precise equipment to electrically test each die on a wafer, identifying defects early and enhancing overall production yield. As technology advances, wafer probe testing continues to evolve, playing a pivotal role in the semiconductor industry.
Key Takeaways
- Wafer probe testing is essential for identifying and removing defective dies early in the semiconductor manufacturing process.
- Both manual and automatic wafer probing techniques are used, with automation being crucial for mass production and high-speed testing.
- Temperature control during wafer probing allows for accurate assessment of wafer reliability under different conditions.
- Wafer probe testing significantly enhances production yield and ensures the delivery of high-quality semiconductor components.
- Technological advancements in wafer probing, such as automation and integration with other testing methods, continue to improve accuracy and efficiency.
Understanding Wafer Probe Testing
Definition of Wafer Probe Testing
Wafer probing is a process in semiconductor development and manufacturing where each die on a wafer is electrically tested. This is performed with an automated wafer probing system. The system holds a wafer on a stable mount and places a set of very thin pins on designated probe pads on the die. These probe pads are also called contact or connection pads.
Significance in Semiconductor Manufacturing
Wafer probing bears considerable significance in semiconductor and microelectronics manufacturing. Manual wafer probing is primarily used to assess the characteristics of prototype integrated circuits and evaluate defect signs. Additionally, it offers extremely accurate measurement and evaluation of a test element group (TEG) for an integrated circuit made up of transistors, connectors, and other components.
Key Components Involved
The wafer probe testing system includes several key components:
- Wafer Chuck: A round plate that loads and accurately positions the wafer.
- Probe Card: A collection of tiny needles that make electrical contact with the wafer.
- Tester: A measuring instrument that transmits test signals to the devices on the wafer and receives signals back.
These components work together to ensure the electrical performance of the wafers is tested using a testing device (prober).
The Wafer Probing Process
Steps in Wafer Probe Testing
The wafer probing process involves several critical steps to ensure the functionality of each die on a wafer. First, the wafer is placed on a stable mount. Then, a set of very thin pins, known as probe pins, are positioned on designated probe pads on the die. These probe pads, also called contact or connection pads, facilitate the electrical testing of the wafer. The automated wafer probing system then performs a series of electrical tests to verify the integrity and performance of each die.
Manual vs. Automatic Wafer Probing
Manual wafer probing involves human operators positioning the probe pins on the wafer, which can be time-consuming and prone to errors. In contrast, automatic wafer probing uses advanced machinery to place the probe pins with high precision and speed. Automatic wafer probing is necessary for semiconductor mass production testing to ensure precise placement and high-speed controls during the testing procedure. This automation significantly reduces the risk of human error and increases the throughput of the testing process.
Temperature Control in Wafer Probing
Temperature control is a crucial aspect of the wafer probing process. During testing, wafers can heat up, potentially affecting the accuracy of the test results. To mitigate this, the automated wafer probing system often includes temperature control mechanisms to maintain a stable testing environment. This ensures that the electrical tests are conducted under consistent conditions, leading to more reliable and accurate results.
Benefits of Wafer Probe Testing
Enhancing Production Yield
Wafer probe testing plays a crucial role in enhancing production yield by identifying defective dies early in the manufacturing process. This allows manufacturers to address issues before they escalate, ensuring that only high-quality components proceed to the next stages of production. By catching defects early, wafer probing significantly reduces waste and improves overall efficiency.
Early Detection of Defects
One of the primary benefits of wafer probe testing is the early detection of defects. This process checks the quality and functionality of each die on a wafer, allowing for the identification of issues that could affect the performance of the final product. Early detection helps in making timely adjustments, thereby maintaining the high standards expected in today’s technology.
Ensuring High-Quality Components
Wafer probe testing ensures that only high-quality components are used in semiconductor manufacturing. By verifying the electrical properties of each die, this process guarantees that the final products meet stringent quality requirements. This is particularly important in applications where reliability and performance are critical, such as in medical devices and aerospace technology.
Technological Advancements in Wafer Probe Testing
Automation in Wafer Probing
Automation has revolutionized wafer probe testing by significantly enhancing efficiency and accuracy. Automated wafer probing systems can handle a large volume of wafers with minimal human intervention, reducing the risk of human error and increasing throughput. These systems are equipped with advanced robotics and software algorithms that ensure precise alignment and contact with the probe pads.
High-Speed Testing Capabilities
The demand for faster testing processes has led to the development of high-speed wafer probing systems. These systems are capable of performing rapid electrical tests on each die, significantly reducing the overall testing time. High-speed testing is crucial for meeting the production demands of modern semiconductor manufacturing, where time-to-market is a critical factor.
Integration with Other Testing Methods
Modern wafer probing systems are designed to integrate seamlessly with other testing methods, such as burn-in testing and final test. This integration allows for a more comprehensive evaluation of the wafers, ensuring that only high-quality components proceed to the next stage of production. The ability to combine multiple testing methods in a single platform enhances the overall reliability and efficiency of the semiconductor manufacturing process.
Challenges in Wafer Probe Testing
Common Issues Encountered
Wafer probe testing is critical in semiconductor manufacturing, but it is not without its challenges. One of the most common issues is the accurate placement of probes on the wafer. Misalignment can lead to incorrect readings and potential damage to the wafer. Additionally, the delicate nature of the probes means they are prone to wear and tear, which can affect their performance over time.
Mitigating Testing Errors
To mitigate testing errors, manufacturers often employ advanced alignment systems and regular calibration of equipment. Automated systems are increasingly used to reduce human error and improve precision. Another strategy is to implement rigorous testing protocols that include multiple verification steps to ensure the accuracy of the results.
Improving Accuracy and Reliability
Improving the accuracy and reliability of wafer probe testing involves continuous advancements in technology. AI/ML provides the capabilities to weed out marginal or latent defects in production testing, enhancing the overall reliability of the process. Additionally, integrating high-resolution imaging systems can help in better identifying and addressing potential issues during the testing phase.
Applications of Wafer Probe Testing
Prototype IC Evaluation
Wafer probing is primarily used to assess the characteristics of prototype integrated circuits (ICs) and evaluate defect signs. This process offers extremely accurate measurement and evaluation of a test element group (TEG) for an integrated circuit made up of transistors, connectors, and other components.
Failure Analysis
Wafer probing plays a crucial role in failure analysis by allowing engineers to pinpoint the exact location and nature of defects within a wafer. This early detection is vital for improving the reliability and performance of semiconductor devices.
Design Verification
In the design verification phase, wafer probing ensures that the fabricated ICs meet the design specifications. This step is essential for confirming that the design will function correctly in real-world applications, thereby reducing the risk of costly redesigns and production delays.
Future Trends in Wafer Probe Testing
Emerging Technologies
The semiconductor industry is witnessing rapid advancements in wafer probe testing technologies. Emerging technologies such as MEMS (Micro-Electro-Mechanical Systems) probes and advanced materials are revolutionizing the testing process. These innovations are enabling more precise and reliable measurements, which are crucial for the development of next-generation integrated circuits (ICs).
Impact on Semiconductor Industry
The integration of cutting-edge wafer probe testing technologies is significantly impacting the semiconductor industry. These advancements are not only enhancing the accuracy and efficiency of testing processes but also reducing costs and time-to-market for new products. As a result, manufacturers can achieve higher production yields and better quality control.
Predicted Developments
Looking ahead, several key developments are expected to shape the future of wafer probe testing:
- Increased Automation: The trend towards fully automated wafer probing systems will continue, minimizing human intervention and errors.
- High-Speed Testing: Advances in high-speed testing capabilities will allow for faster and more efficient testing of wafers, meeting the demands of high-volume production.
- Integration with AI and Machine Learning: The use of AI and machine learning algorithms will enhance the predictive maintenance and optimization of wafer probing systems.
- Enhanced Temperature Control: Improved temperature control mechanisms will enable more accurate testing across a wider range of environmental conditions.
These predicted developments highlight the ongoing evolution of wafer probe testing and its critical role in the semiconductor manufacturing landscape.
Conclusion
In the realm of semiconductor manufacturing, wafer probe testing stands as a pivotal process to ensure the functionality and quality of integrated circuits (ICs). By systematically testing individual dies on wafers, engineers can detect and rectify various manufacturing errors, thereby enhancing production efficiency and ensuring the delivery of high-performance devices that meet the demands of modern technology. As technological advancements continue to evolve, the significance of wafer probing in the semiconductor industry remains indispensable, underscoring its role in fostering innovation and maintaining high standards of quality.
Frequently Asked Questions
What is wafer probe testing?
Wafer probe testing is a process in semiconductor manufacturing where each die on a wafer is electrically tested using an automated wafer probing system. This system uses thin pins to make contact with designated probe pads on the die to assess electrical properties.
Why is wafer probe testing important in semiconductor manufacturing?
Wafer probe testing is crucial because it helps identify and remove defective dies before they are packaged. This ensures that only functional integrated circuits proceed to the next stages of production, thereby improving yield and quality.
What are the key components involved in wafer probe testing?
The key components include the wafer probing machine, thin pins for making contact with probe pads, and temperature control features to assess wafer reliability under different conditions.
How does automatic wafer probing differ from manual wafer probing?
Automatic wafer probing is used for mass production and ensures precise placement and high-speed controls, whereas manual wafer probing is primarily used for prototype ICs and offers highly accurate measurement and evaluation of test element groups.
What are the benefits of wafer probe testing?
Wafer probe testing enhances production yield, allows for early detection of defects, and ensures the production of high-quality components by systematically testing each die on the wafer.
What challenges are associated with wafer probe testing?
Common challenges include aligning the probe correctly, mitigating testing errors, and improving accuracy and reliability of the tests. Advanced technologies and continuous improvements are necessary to address these issues.