The Importance of Wafer Reliability Tests in Semiconductor Manufacturing
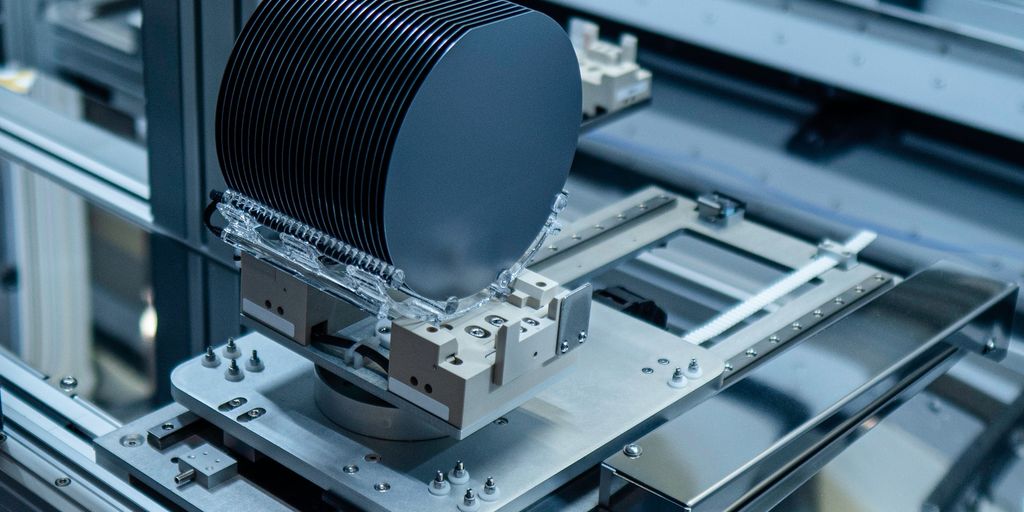
In the world of semiconductor manufacturing, making sure wafers are reliable is super important. Wafer reliability tests help predict how long and how well semiconductor devices will work, even under tough conditions. These tests are key to making sure the whole manufacturing process runs smoothly, from quality checks to building trust with customers. This article explores why wafer reliability tests matter, how they fit into the manufacturing process, and best practices for ensuring top performance.
Key Takeaways
- Wafer reliability tests help predict how long semiconductor devices will last and how well they will perform.
- Adding reliability tests to the manufacturing process helps find defects early and keeps wafers working well.
- Good wafer tests build customer trust and make products more reliable, boosting the company’s reputation.
- Common tests include thermal cycling, electrical stress, and mechanical stress tests.
- Following best practices, like early defect detection and consistent monitoring, ensures top-quality wafers.
The Role of Wafer Reliability Tests in Semiconductor Manufacturing
Wafer reliability tests are a key part of making semiconductors. These tests help make sure that the devices will work well over their expected life, even when they face different stress conditions. By predicting how wafers will act in real-world situations, manufacturers can promise the long-term performance of their products.
Integration of Wafer Reliability Tests in the Manufacturing Workflow
Integrating wafer reliability tests into the manufacturing workflow is essential for maintaining a seamless production process. This ensures that the insights gained from the analysis can be promptly and effectively implemented, leading to immediate improvements in the manufacturing process.
Impact of Wafer Reliability Tests on Customer Confidence and Market Reputation
Building Customer Trust
Wafer reliability tests are key to earning customer trust. By making sure semiconductor devices work well and last long, manufacturers show they care about quality. This means the final products are less likely to break, giving users peace of mind.
Maintaining Compliance with Standards
Following strict testing standards helps companies meet industry rules. This not only avoids legal issues but also shows customers that the products are safe and reliable. Sticking to these standards is crucial for maintaining a good reputation.
Enhancing Market Competitiveness
Reliable products make a company stand out in the market. When customers know they can trust a brand, they are more likely to buy from it again. This boosts the company’s position against competitors and can lead to higher sales.
Common Techniques Used in Wafer Reliability Testing
Thermal Cycling Tests
Thermal cycling tests involve repeatedly heating and cooling the wafer to simulate the stress it will experience in real-world conditions. This helps identify potential failures due to thermal expansion and contraction.
Electrical Stress Tests
Electrical stress tests apply high voltage and current to the wafer to check its electrical stability and performance. These tests are crucial for ensuring that the wafer can handle the electrical demands of its intended application.
Mechanical Stress Tests
Mechanical stress tests subject the wafer to physical forces, such as bending and pressure, to evaluate its structural integrity. This type of testing helps ensure that the wafer can withstand mechanical stresses during manufacturing and use.
Best Practices in Wafer Reliability Testing
Early Defect Detection
One of the most important practices in wafer reliability testing is early defect detection. By identifying issues at the earliest stages, manufacturers can address problems before they escalate. This proactive approach not only saves time but also reduces costs associated with late-stage defect rectification.
Consistent Performance Monitoring
Regular monitoring of wafer performance ensures that any deviations from expected behavior are promptly identified and corrected. Consistent performance monitoring helps maintain the quality and reliability of semiconductor devices, ensuring they meet the required standards throughout the manufacturing process.
Adopting Industry Standards
Following established industry standards is crucial for maintaining high levels of reliability in wafer testing. These standards provide a framework for testing protocols, data interpretation, and continuous improvement strategies. Adhering to these guidelines ensures that the testing processes are both effective and efficient.
Ensuring Long-Term Device Performance
Reliability testing involves subjecting wafers to different stress conditions to predict their lifespan and performance. This practice helps in guaranteeing that the semiconductors will perform reliably in real-world conditions.
Guaranteeing Real-World Reliability
Stress Condition Simulations
Wafer reliability tests are crucial for ensuring that semiconductor devices can handle real-world conditions. By simulating stress conditions, manufacturers can predict how wafers will perform under various scenarios. This helps in identifying potential failure points early.
Reliability Over Time
Testing wafers for long-term reliability ensures that they will perform consistently over their expected lifespan. This involves subjecting the wafers to prolonged stress tests to see how they hold up over time. The goal is to minimize failure rates and ensure sustained performance.
Customer Satisfaction
Reliable wafers lead to reliable end products, which in turn boosts customer satisfaction. When customers know that the products they are using are dependable, it builds trust and enhances the manufacturer’s reputation. This is why wafer reliability tests are so important in the semiconductor industry.
Conclusion
In summary, wafer reliability tests are a key part of making semiconductors. These tests make sure each wafer is good quality and works well, which is super important for the devices’ long life. By doing these tests, companies can find and fix problems early, making the final products better. This not only makes customers happy but also helps the company’s reputation. Overall, wafer reliability tests help make sure that the technology we use every day is safe and reliable.
Frequently Asked Questions
Why are wafer reliability tests important in semiconductor manufacturing?
Wafer reliability tests are crucial because they help predict how long and how well semiconductor devices will perform. These tests ensure that each wafer meets high standards of quality and performance.
How do wafer reliability tests impact the manufacturing process?
These tests are integrated into the manufacturing workflow to catch defects early. This helps maintain consistent quality and reduces the chances of product failure.
What techniques are used in wafer reliability testing?
Common techniques include thermal cycling tests, electrical stress tests, and mechanical stress tests. Each of these tests checks how wafers respond to different stress conditions.
How do wafer reliability tests build customer trust?
By ensuring that semiconductor devices are reliable and perform well, manufacturers can show their commitment to quality. This helps build customer trust and confidence in the products.
What are the benefits of integrating wafer reliability tests into the manufacturing workflow?
Integrating these tests helps in early defect detection, maintaining consistent quality, and reducing production costs. It also ensures a continuous flow of information for proactive quality control.
How do wafer reliability tests affect market competitiveness?
High-quality wafer testing ensures that the final products are reliable. This boosts customer confidence, meets industry standards, and enhances the company’s reputation in the market.