The Latest Innovations in Wafer Testing Equipment
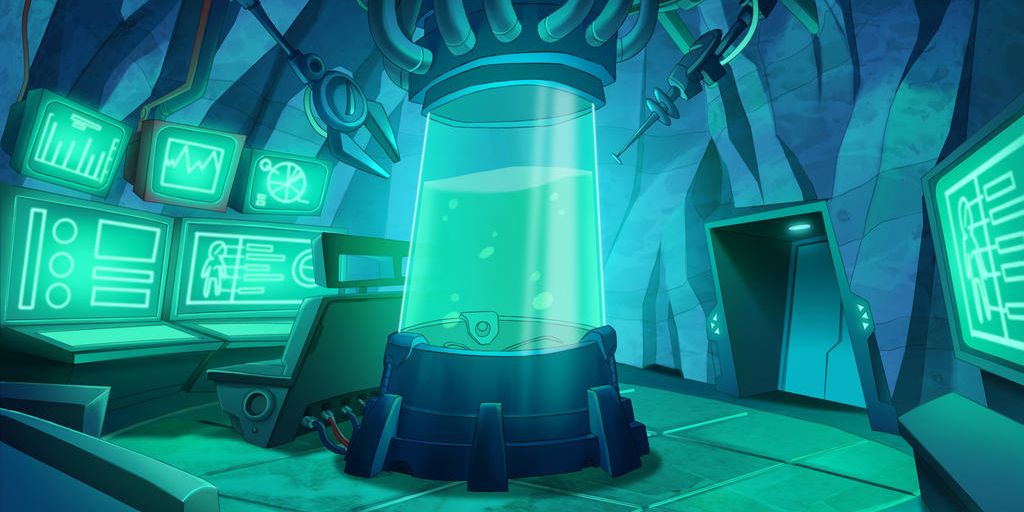
The semiconductor industry is on the cusp of a transformative era with the advent of cutting-edge wafer testing equipment. These innovations are not only enhancing chip quality but also redefining the standards of efficiency and reliability in chip manufacturing. From in-die monitoring to advanced metrology, and from tackling wafer-level packaging challenges to leveraging data-driven strategies, the sector is witnessing a paradigm shift. This article explores the latest technologies and approaches revolutionizing wafer testing equipment.
Key Takeaways
- Advancements in wafer testing equipment are pivotal for the semiconductor industry’s pursuit of impeccable chip quality.
- AI and machine learning are revolutionizing chip quality, predictive maintenance, and data-driven decision-making in wafer testing.
- Centralized analytics platforms play a crucial role in real-time data analysis, improving yield rates, and streamlining operations.
- Challenges in wafer-level packaging are being addressed through the integration of multiple dies and cost-effective performance solutions.
- The future of wafer testing includes innovations in nanotechnology, 3D integration testing, and enhanced chip functionality.
Advancements in In-Die Monitoring for Wafer Testing Equipment
Enhancing Defect Detection
The advancements in wafer testing equipment are pivotal for the semiconductor industry’s pursuit of impeccable chip quality. Innovations such as in-die monitoring IP are revolutionizing the way chips are tested and monitored. These technologies enhance the detection of defects, ensuring higher reliability and performance of semiconductor devices.
Optimizing Manufacturing Processes
The semiconductor industry is on the cusp of a transformative era with the advent of cutting-edge wafer testing equipment. These innovations are not only enhancing chip quality but also redefining the standards of efficiency and reliability in chip manufacturing. From in-die monitoring to advanced metrology, the sector is witnessing a paradigm shift.
Adapting to Customer-Specific Needs
Customization and adaptability in semiconductor test and metrology are key to addressing customer-specific needs and novel issues. Supported by robust data management systems, these advancements ensure that the unique requirements of each customer are met, enhancing overall satisfaction and performance.
AI and Machine Learning in Wafer Testing
Revolutionizing Chip Quality
Artificial intelligence (AI) is becoming increasingly important in wafer testing. AI can analyze data from tests much faster and more accurately than humans. It can quickly identify patterns and anomalies that might indicate a problem with the wafer. As AI technology advances, its applications in wafer testing will become more sophisticated, leading to faster and more reliable testing processes.
Predictive Maintenance
The integration of AI/ML in wafer testing equipment is revolutionizing the way real-time decisions are made during the chip quality assurance process. AI/ML models must navigate decision-making thresholds with precision, ensuring that only genuine concerns are flagged without being overwhelmed by data variances. This precision is crucial to maintain system stability and avoid unnecessary disruptions.
Data-Driven Decision Making
The challenge for AI/ML research is to develop models capable of identifying unexpected issues, even those not previously encountered. This requires models that are not only predictive but also possess the ability to recall, compare, and reason. The table below summarizes the key considerations for AI/ML model training in wafer testing:
Key Consideration | Description |
---|---|
Precision | Ensuring only genuine concerns are flagged |
Adaptability | Customization to address novel issues |
Speed | Faster data analysis and decision making |
Accuracy | High accuracy in identifying patterns and anomalies |
Centralized Analytics Platforms for Wafer Testing
Centralized analytics platforms collect and integrate data from various sources, enabling better data preparation and engineering. This facilitates the training of AI/ML models, which can then be used to make real-time decisions during chip testing, thereby enhancing the test process.
Challenges and Solutions in Wafer-Level Packaging
Integration of Multiple Dies
With the emergence of innovative technologies, such as integrating multiple dies into monolithic systems, meeting the increasing demand for cost-effective performance in top-end applications has become more challenging. Advanced packaging technologies like High Bandwidth Memory (HBM), Fan Out Wafer Level Packaging (FOWLP), and Heterogeneous Integration (HI) require highly optimized and accurate fabrication processes to be cost-effective and achieve high-quality results.
Cost-Effective Performance
Innovative inspection techniques for 3D structures and wire bonds, as well as thermal management strategies for 2.5D integration, are critical in overcoming wafer-level packaging challenges. Data provenance and predictive analytics are instrumental in improving final test yields, with knowledge transfer across the supply chain driving continuous improvement.
Wafer-Level Burn-In
One of the significant challenges in wafer-level packaging is determining the best testing solutions for the next generation of semiconductors. Even when die has been packaged, there is a complex trade-off between how much to spend on the final test of the package versus the cost to the user or supplier if the device fails while in use. Standardization efforts, particularly in chiplet IP, along with industry collaboration and talent development, are essential.
Precision and Scalability in Wafer Electrical Testing
Wafer electrical testing attains a superior level of accuracy and expandability by employing numerous precise, calibrated electrical sources and measuring tools for each wafer. In wafer test analysis, a blend of precision and attention to detail is vital. From selecting the right materials to designing wafers that accurately replicate production models, every step is crucial. Employing various testing methods like electrical testing for device functionality, Scanning Electron Microscopy (SEM) provides detailed imaging of wafer surfaces, and Focused Ion Beam (FIB) techniques are used for precise material manipulation and analysis.
Future Trends in Wafer Testing Equipment
Nanotechnology Applications
The future of wafer testing in the semiconductor sector is poised for innovative developments, notably through nanotechnology. Nanotechnology enables more accurate 3D integration testing, which is crucial for improving chip functionality while reducing size. This advancement is expected to revolutionize the way chips are tested and manufactured, leading to higher efficiency and reliability.
3D Integration Testing
3D integration testing is becoming increasingly important as the demand for smaller, more powerful chips grows. This type of testing allows for the stacking of multiple layers of circuits, which can significantly enhance chip performance. The ability to test these complex structures accurately is essential for ensuring the quality and functionality of the final product.
Enhanced Chip Functionality
Innovations in wafer testing equipment are not only enhancing chip quality but also redefining the standards of efficiency and reliability in chip manufacturing. From in-die monitoring to advanced metrology, these technologies are revolutionizing the way chips are tested and monitored. The ability to adapt to customer-specific needs while identifying new opportunities for improvement is a key trend in the industry.
Types of Test Wafers in Semiconductor Testing
In the field of semiconductor testing, various types of test wafers are employed to meet specific manufacturing and quality assurance needs, utilizing chip probes and other techniques. Each type of test wafer, be it a monitor, dummy, defect, or short loop, plays a distinct role in maintaining high standards in semiconductor testing. These wafers, along with the use of wafer probers and comprehensive chip and die tests, contribute significantly to the production of reliable and high-quality semiconductor products.
Best Practices in Wafer Manufacturing and Testing
Ensuring Reliability and Performance
The importance of best practices in wafer testing cannot be overstated for the semiconductor industry. High-quality wafer testing ensures the reliability and performance of semiconductor devices, which are integral to almost every modern technology. Wafer testing is a key step in semiconductor manufacturing, verifying the high standards expected in today’s technology. This process checks the quality and performance of wafers, the thin slices of silicon used to make electronic circuits. It’s a complex task that demands careful attention, as even minor errors can have big impacts.
Evaluation and Data Interpretation
Wafer test analysis, a critical component of this process, involves evaluation and data interpretation to ensure each semiconductor meets the highest standards of quality and functionality. In wafer test analysis, a blend of precision and attention to detail is vital. From selecting the right materials to designing wafers that accurately replicate production models, every step is crucial. Employing various testing methods like electrical testing for device functionality, Lot Genealogy in Wafer Final Test, Scanning Electron Microscopy (SEM) for detailed imaging of wafer surfaces, and Focused Ion Beam (FIB) techniques for precise material manipulation and analysis.
Commitment to Quality
Each type of test wafer, be it a monitor, dummy, defect, or short loop, plays a distinct role in maintaining high standards in semiconductor testing. These wafers, along with the use of wafer probers and comprehensive chip and die tests, contribute significantly to the production of reliable and high-quality semiconductor products. The industry’s commitment to quality is further solidified by continuous advancements in testing methodologies and technologies.
Conclusion
The advancements in wafer testing equipment are pivotal for the semiconductor industry’s pursuit of impeccable chip quality. Innovations such as in-die monitoring IP, centralized analytics platforms, and AI/ML-driven analytics capabilities are revolutionizing the way chips are tested and monitored. These technologies not only enhance the detection of defects but also contribute to the optimization of manufacturing processes. The semiconductor industry is on the cusp of a transformative era with the advent of cutting-edge wafer testing equipment. These innovations are not only enhancing chip quality but also redefining the standards of efficiency and reliability in chip manufacturing. From in-die monitoring to advanced metrology, and from tackling wafer-level packaging challenges to leveraging data-driven strategies, the sector is witnessing a paradigm shift. As we look to the future, the integration of nanotechnology and more accurate 3D integration testing will further propel the industry towards achieving improved chip functionality with reduced size. The importance of best practices in wafer testing cannot be overstated, as high-quality testing ensures the reliability and performance of semiconductor devices, which are integral to almost every modern technology.
Frequently Asked Questions
What are the latest advancements in wafer testing equipment?
The latest advancements in wafer testing equipment include in-die monitoring IP, centralized analytics platforms, and AI/ML-driven analytics capabilities. These innovations enhance defect detection, optimize manufacturing processes, and adapt to customer-specific needs.
How is AI and machine learning revolutionizing wafer testing?
AI and machine learning are revolutionizing wafer testing by improving chip quality, enabling predictive maintenance, and facilitating data-driven decision making.
What role do centralized analytics platforms play in wafer testing?
Centralized analytics platforms provide real-time data analysis, improve yield rates, and streamline operations in wafer testing.
What are the challenges in wafer-level packaging?
Challenges in wafer-level packaging include the integration of multiple dies, achieving cost-effective performance, and conducting wafer-level burn-in.
Why is precision important in wafer electrical testing?
Precision in wafer electrical testing is crucial for ensuring accurate measurements and scalability. This is achieved through calibrated electrical sources, detailed imaging techniques, and precise material manipulation and analysis.
What future trends are expected in wafer testing equipment?
Future trends in wafer testing equipment include the application of nanotechnology, 3D integration testing, and enhanced chip functionality.