The Process Behind Silicon Wafer Manufacturing
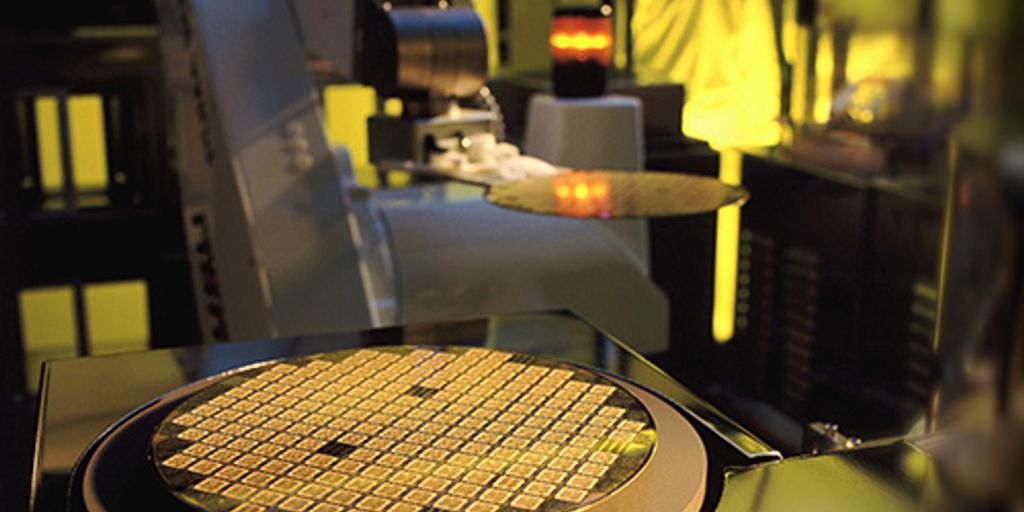
The journey from a single crystal to a polished, tested silicon wafer encapsulates the essence of silicon wafer manufacturing. It’s a process that combines advanced technology, precision engineering, and stringent quality control to produce the fundamental building block of the semiconductor industry, enabling the vast array of electronic devices that power our modern world. In this article, we will explore the silicon wafer processing and manufacturing, from raw material acquisition to final wafer characterization and inspection.
Key Takeaways
- Silicon wafer manufacturing involves multiple stages, starting from raw material acquisition and purification to final wafer characterization and inspection.
- The Czochralski method is a critical process in crystal growth, ensuring the production of high-quality single silicon crystals.
- Precision in wafer slicing, shaping, and thickness control is essential to meet the stringent requirements of the semiconductor industry.
- Doping and diffusion processes are crucial for altering the electrical properties of silicon wafers, impacting their performance in electronic devices.
- Quality control measures, including electrical testing and defect analysis, are vital to ensure the reliability and performance of the final silicon wafers.
Raw Material Acquisition and Purification
Sources of Silicon
Silicon wafer manufacturing starts with silicon extraction. The primary source of silicon is quartzite, a form of high-purity quartz. This raw material is mined and then transported to processing facilities. High-quality silicon wafers are essential for the performance and reliability of semiconductor devices.
Purification Techniques
The extracted silicon is ground down to a fine powder, mixed with hydrogen chloride, and heated until it turns into a liquid. This process, known as the Siemens process, helps in further purification. You would think that 99% purity would be enough, but for a semiconductor to function optimally, you want that to get as close to 100% purity as possible. This step involves the production of high-quality, purified silicon wafers, in which the silicon is melted and crystallized to form a round, flat wafer.
Quality Control Measures
Quality control is critical in ensuring the purity and performance of silicon wafers. Manufacturers employ various techniques such as spectrometry and chemical analysis to detect and eliminate impurities. Regular inspections and stringent quality control measures are in place to maintain the high standards required for semiconductor manufacturing.
Crystal Growth Using the Czochralski Method
Process Overview
The Czochralski process is the most common method for growing silicon crystals for use in silicon wafer manufacturing. The process involves heating a germanium or silicon seed crystal and dipping it into molten silicon, gradually solidifying around it to form a cylindrical crystal. The crystal is rotated as it grows to ensure a uniform crystal structure and minimize impurities. This method is essential for producing high-quality semiconductor chips.
Equipment Used
The primary equipment used in the Czochralski method includes a quartz crucible, a seed crystal, and a rotating mechanism. The quartz crucible holds the molten silicon, while the seed crystal is dipped into the melt. The rotating mechanism ensures the cylindrical geometry of the growing crystal. Additionally, a controlled environment is maintained to facilitate the growth of flawless single crystals.
Challenges and Solutions
One of the main challenges in the Czochralski method is oxygen contamination, as the boule is grown in a quartz crucible. This can affect the quality of the silicon wafers. To mitigate this, researchers are exploring alternative methods like the floating zone and edge-defined film-fed growth (EFG) methods. These techniques aim to grow crystals more quickly and with fewer defects, offering potential improvements over the traditional Czochralski process.
Wafer Slicing and Shaping
Wafer shaping involves a series of precise mechanical and chemical process steps that are necessary to turn the ingot segment into a functional wafer. It is during these steps that the wafer surfaces and dimensions are perfected to exacting detail. Each step is designed to bring the wafer into compliance with each customer specification.
Doping and Diffusion Processes
Doping and diffusion are critical steps in silicon wafer manufacturing, where specific impurities are introduced to alter the electrical properties of silicon. This intricate dance of adding just the right atoms into the silicon lattice is what makes the technology behind our gadgets possible.
Introduction to Doping
Small quantities of dopants are added, which are basically elements from Group 3 and 4 of the periodic table, such as Boron, Phosphorus, Arsenic, or Antimony. These dopants are responsible for determining the properties of the resultant wafer material—it may be P type (Boron) or N type (Phosphorous, Arsenic, Antimony). The material is then heated above a temperature of 1412 degrees (usually above 1500 degrees) until everything has liquefied.
Diffusion Techniques
Dopant diffusion is one of the primary applications of diffusion in semiconductor fabrication. The material is heated to a high temperature, allowing the dopants to diffuse into the silicon lattice. This process is carefully controlled to achieve the desired electrical characteristics.
Impact on Wafer Properties
The introduction of dopants into the silicon crystal finely tunes its electrical properties, enhancing the semiconductor’s performance in electronic devices. This step is crucial for the suitability for the subsequent phases of semiconductor fabrication, such as oxidation, lithography, deposition, and metallization.
Wafer Polishing and Cleaning
Polishing Methods
Polishing is a critical step in silicon wafer manufacturing, ensuring the wafer surface is flat and smooth. This process is typically performed in a clean room environment, where the particle count per cubic foot is controlled to be between Class 1 to Class 10,000. Workers wear clean suits and work under fans that blow away excess particles. High-quality silicon wafers usually undergo two to three stages of polishing, which can be either single-side or double-side polishing.
Cleaning Procedures
After polishing, wafers must be chemically etched and cleaned to remove any remaining surface defects, even at a microscopic level. This is usually done using a bath consisting of sodium hydroxide, acetic acid, or nitric acid. Chemical and mechanical cleaning processes are essential to remove residual impurities and prepare the surface for further processing.
Ensuring Surface Quality
To ensure the surface quality of the wafers, they are subjected to both chemical and mechanical cleaning processes. These steps help in removing residual impurities and preparing the surface for further processing. The wafers are polished and ground to ensure they are flat and have a uniform thickness, which is crucial for the performance of semiconductor devices.
Final Wafer Characterization and Inspection
Electrical testing is a critical step in wafer characterization. Manufacturers use computer-controlled probes to test every section of the wafer. These tests measure properties such as resistivity and carrier concentration to ensure the wafers meet the required specifications for semiconductor devices. Wafers that pass these tests are marked as ready for distribution.
Visual inspection involves checking the wafers for physical defects such as scratches, cracks, and contamination. This step is crucial because any physical imperfections can significantly impact the performance and reliability of semiconductor devices. Wafers that meet the visual inspection criteria are then prepared for final packaging.
Defect analysis is performed to identify and categorize any defects found during the inspection process. This analysis helps in understanding the root causes of defects and in improving the manufacturing process. The wafers are inspected for flatness and thickness to ensure they meet the required specifications. Those that do not meet the criteria are sorted out of the batch.
Summary of Inspection Steps
- Electrical Testing
- Visual Inspection
- Defect Analysis
Key Parameters Measured
Parameter | Description |
---|---|
Resistivity | Measures the wafer’s resistance to electrical flow |
Carrier Concentration | Indicates the number of charge carriers in the wafer |
Flatness | Ensures the wafer surface is even |
Thickness | Confirms the wafer’s uniform thickness |
Applications of Silicon Wafers in Electronics
Silicon wafers are fundamental to the electronics industry, serving as the base material for manufacturing semiconductors. These semiconductors are then fabricated into integrated circuits (ICs) or chips, which are essential components in a wide array of electronic devices. The versatility of silicon wafers allows for the creation of everything from simple diodes and transistors to complex microprocessors and memory chips. This versatility makes silicon wafers invaluable in the semiconductor industry.
Microprocessors
Microprocessors are the brains of computers and many other electronic devices. Silicon wafers are used to create these microprocessors, which can contain millions of transistors. These transistors work together to perform complex calculations and tasks, enabling the functionality of modern computing devices.
Memory Chips
Memory chips, including RAM and flash memory, are another critical application of silicon wafers. These chips store data and are essential for the operation of computers, smartphones, and other digital devices. Advances in silicon wafer technology have led to the development of memory chips with higher storage capacities and faster data retrieval speeds.
Sensors
Silicon wafers are also used in the production of various sensors, including those found in smartphones, automotive systems, and industrial machinery. These sensors can detect and measure physical properties such as temperature, pressure, and acceleration, providing critical data for a wide range of applications.
Conclusion
This journey from a single crystal to a polished, tested silicon wafer encapsulates the essence of silicon wafer manufacturing. It’s a process that combines advanced technology, precision engineering, and stringent quality control to produce the fundamental building block of the semiconductor industry, enabling the vast array of electronic devices that power our modern world. The production of silicon wafers is a symphony of precision and innovation, showcasing incredible advancements in crystal growth, doping techniques, and the myriad of processes that define the semiconductor industry. Each phase of production, from the initial purification of silicon to the final packaging and testing, contributes to the extraordinary capabilities of today’s electronic devices.
Frequently Asked Questions
What is silicon wafer manufacturing?
Silicon wafer manufacturing refers to the series of processes involved in producing high-quality silicon wafers from raw materials like silica sand. These wafers are essential components in semiconductor devices such as microprocessors, memory chips, and sensors.
How is silicon purified for wafer production?
Silicon is purified through a series of chemical processes that remove impurities, resulting in high-purity polycrystalline silicon. This purified silicon is essential for producing high-quality wafers.
What is the Czochralski method?
The Czochralski method is a process used to grow single silicon crystals. It involves melting silicon in a quartz crucible and carefully drawing out a single crystal by rotating and lifting a tiny seed crystal from the melt.
Why is quality control important in silicon wafer manufacturing?
Quality control is crucial because the performance and reliability of semiconductor devices depend on the quality of the silicon wafers. Stringent quality control measures ensure that the wafers meet the required standards.
What are the applications of silicon wafers?
Silicon wafers are used in various electronic devices, including microprocessors, memory chips, and sensors. They are fundamental components in the semiconductor industry, enabling the functionality of modern electronic devices.
How are silicon wafers inspected for defects?
Silicon wafers undergo electrical testing, visual inspection, and defect analysis to ensure they meet quality standards. These inspections help identify any imperfections that could affect the performance of the semiconductor devices.