The Titans of Silicon Wafers: Profiling US Chip Manufacturers
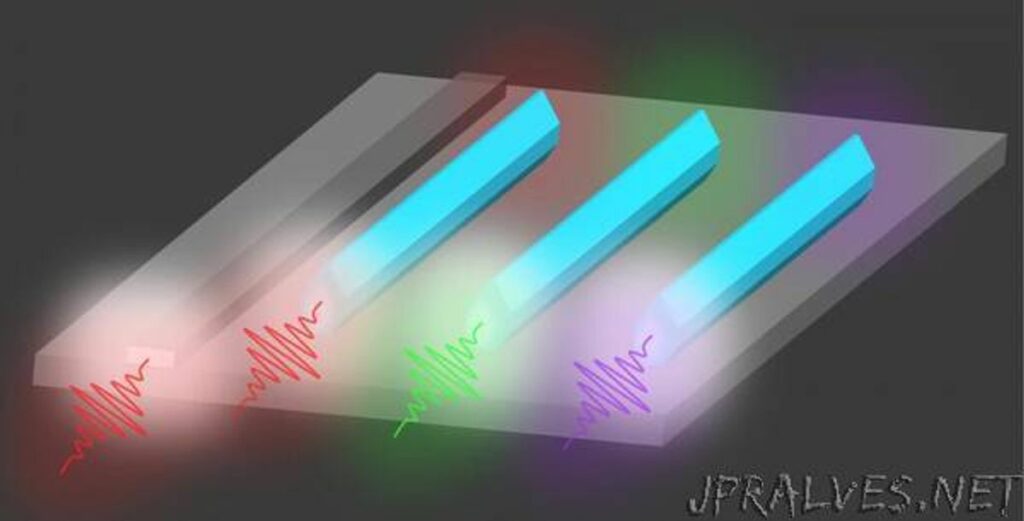
The United States has long been a bastion of technological innovation, particularly in the semiconductor industry. This article profiles the giants of US chip manufacturing, delving into their technological prowess, market influence, and the intricate processes that underpin the production of silicon wafers. From Wolfspeed’s leadership in Silicon Carbide and GaN technologies to the diverse ecosystem of chip manufacturing, we explore the key players and their roles in shaping the future of electronics.
Key Takeaways
- Wolfspeed is a leading semiconductor company specializing in silicon carbide and GaN technologies with a significant global market presence.
- The US chip manufacturing landscape features a diverse ecosystem with companies like Wolfspeed and Intersurface Dynamics, each focusing on specialized sectors and processes.
- Intersurface Dynamics has been a pioneer in surface chemistry since 1985, providing tailored chemical solutions and holding an ISO-9001:2015 certification.
- Lapping and polishing are critical consumables in wafer processing, with advancements in these technologies impacting chip performance and reliability.
- US chip manufacturers maintain a diversified product portfolio and address key process steps in chip fabrication, contributing to the robustness of the semiconductor industry.
Wolfspeed: A Semiconductor Powerhouse
Innovation in Silicon Carbide and GaN Technologies
Wolfspeed, Inc. has established itself as a leader in the semiconductor industry, particularly in the realm of silicon carbide and gallium nitride (GaN) technologies. These materials are at the forefront of the next generation of power electronics, offering superior performance in terms of efficiency, thermal conductivity, and power density.
The company’s advancements in these areas are not only technical but also strategic, as they align with the growing demand for energy-efficient solutions in sectors like industrial e-mobility. Wolfspeed’s silicon carbide technology is pivotal for energy conversion and delivery systems that are both reliable and cost-effective, a critical aspect for the burgeoning electric vehicle market.
Wolfspeed’s global operations span across multiple continents, with a significant presence in key markets. This international footprint allows the company to effectively serve a diverse customer base and respond to the dynamic needs of the industry.
Global Presence and Market Reach
Wolfspeed’s expansion into the global market is underscored by its significant supply agreements, which are indicative of the robust demand for silicon carbide technology. With a recent deal now valued at approximately $275M, the company’s reach extends across several critical industries, emphasizing its role as a key player in the semiconductor space.
The company’s international footprint is not limited to sales; it also encompasses a strategic network of operations. Wolfspeed maintains a presence in multiple countries, ensuring that its cutting-edge products are accessible to a diverse range of customers. This global distribution of resources and services is a testament to the company’s commitment to meeting the needs of a dynamic and ever-expanding market.
To illustrate the scale of Wolfspeed’s operations, consider the following data:
- 8 locations across five countries
- Partnerships with major industry players
- A diverse portfolio that caters to consumer, digital media, entertainment, logistics, and cloud computing services.
Strategic Focus on Power Semiconductor Sectors
Wolfspeed’s strategic emphasis on the power semiconductor sectors is a testament to their foresight in the industry. With a history rooted in innovation, the company has pivoted from its early work on silicon carbide to become a leader in high-power semiconductor devices. This focus is not just about technology, but also about addressing the fundamental process steps in chip manufacturing that are critical for the future of electronics.
The company’s commitment to silicon carbide and gallium nitride (GaN) technologies has positioned it well within the global semiconductor market. As a global supplier with a presence in five countries, Wolfspeed has the reach and resources to influence the market significantly. Their product portfolio, which includes silicon carbide bare wafers, epitaxial wafers, and GaN epitaxial layers, caters to a diverse range of applications, from RF to power and beyond.
Wolfspeed’s growth and strategic direction are reflected in their business performance and market presence. The company’s trajectory is marked by a clear plan to dominate the power semiconductor sectors, leveraging their expertise in materials and manufacturing to meet the demands of an ever-evolving industry.
The Diverse Ecosystem of US Chip Manufacturing
Business Segments and Subsidiaries
The US chip manufacturing landscape is characterized by a diverse array of business segments and subsidiaries, each playing a crucial role in the supply chain. Our business segments encompass four wholly-owned subsidiaries, which operate under premier brand names and are strategically positioned across various niches in the semiconductor market. These subsidiaries include BTU International, Entrepix Inc., PR Hoffman, and Intersurface Dynamics, each contributing unique expertise and products to our portfolio.
With a global footprint, our subsidiaries are spread across eight locations in five countries, ensuring a robust presence in key markets. This international reach allows for a seamless integration of resources and expertise, which is vital for maintaining a competitive edge. The subsidiaries cater to a wide range of needs within the semiconductor industry, from advanced surface chemistry solutions to essential consumables for wafer processing.
The following table outlines the key subsidiaries and their respective specializations:
Subsidiary | Specialization |
---|---|
BTU International | Thermal processing equipment |
Entrepix Inc. | Chemical mechanical planarization (CMP) |
PR Hoffman | Lapping and polishing solutions |
Intersurface Dynamics | Surface chemistry for semiconductor and optics |
Diversified Product Portfolio
The US chip manufacturing landscape is marked by a diversified product portfolio that caters to a broad spectrum of technological needs. From AI to 5G, and the Internet of Things (IoT), these products are the backbone of tech innovation and are pivotal for long-term growth. The subsidiaries under the US chip manufacturers, such as BTU International, Entrepix Inc., PR Hoffman, and Intersurface Dynamics, each contribute to this rich mosaic of offerings.
With operations spanning across eight locations in five countries, these companies collectively address the critical process steps in chip fabrication. Their products and services are not only essential for the semiconductor market but also for consumer electronics, digital media, entertainment, and cloud computing services. This global presence underscores their market reach and the role they play in fueling tech innovation and potentially offering significant investment returns.
The following table outlines the key business segments and their respective contributions to the semiconductor industry:
Business Segment | Products/Services | Market Application |
---|---|---|
BTU International | Thermal processing equipment | Semiconductor, electronics |
Entrepix Inc. | CMP and cleaning services | Semiconductor manufacturing |
PR Hoffman | Lapping and polishing solutions | Semiconductor, optics |
Intersurface Dynamics | Chemical solutions for surface engineering | Semiconductor, optics |
As the industry evolves, these manufacturers continue to adapt, ensuring that their product portfolios remain relevant and competitive in a rapidly changing technological landscape.
Addressing Key Process Steps in Chip Fabrication
The intricate journey of chip manufacturing involves several key process steps that are critical to the production of high-quality semiconductors. Each step is meticulously designed to ensure precision and control, from the initial wafer creation to the final packaging of the chip. US chip manufacturers have honed their expertise in addressing these steps, ensuring that every phase of the process contributes to the overall performance and reliability of the end product.
To illustrate the complexity of chip fabrication, consider the following stages:
- Design and Development: Crafting the architecture and functionality of the chip.
- Material Preparation: Preparing silicon wafers or other substrates for layering.
- Photolithography: Transferring circuit patterns onto the wafer.
- Etching: Removing unwanted material to create the circuit design.
- Doping: Introducing impurities to modify electrical properties.
- Deposition: Adding layers of materials to form the electronic structure.
- Planarization: Flattening the wafer surface for subsequent layers.
- Assembly and Packaging: Encasing the chip for protection and connectivity.
These steps are supported by a diverse ecosystem of specialized equipment, materials, and services, such as the patented CXT polishing carriers that improve machine and wafer cleanliness while reducing downtime. The commitment to innovation and quality is evident in the strategic focus on advanced materials like silicon carbide and the adoption of ISO-9001:2015 quality management systems. As the industry evolves, US manufacturers continue to refine these processes, ensuring their position at the forefront of semiconductor technology.
Intersurface Dynamics: Pioneering Surface Chemistry
Tailored Chemical Solutions for Surface Engineering
Intersurface Dynamics stands at the forefront of surface engineering, offering a suite of application-specific process chemicals since 1985. These specialized chemicals are pivotal in achieving desired surface morphologies on a variety of materials, including semiconductor devices and precision optics.
The company’s expertise is reflected in its ability to provide tailored solutions that cater to the unique needs of each material. For instance, their patented CXT Polishing Carriers enhance wafer processing by improving machine cleanliness and reducing downtime, which in turn saves time and money for their clients.
Intersurface Dynamics’ commitment to quality is underscored by their ISO-9001:2015 certification, ensuring that their products meet the highest standards. This dedication to excellence has earned them the trust of some of the world’s largest manufacturers in the semiconductor and optics industries.
Serving Major Semiconductor and Optics Manufacturers
Intersurface Dynamics has established itself as a critical partner to some of the world’s leading manufacturers in the semiconductor and optics fields. With a history dating back to 1985, the company has honed its expertise in providing application-specific chemicals that are essential for achieving the desired surface morphologies on a variety of materials.
Their clientele includes major players in the production of semiconductor devices, silicon wafers, sapphire wafers, silicon carbide wafers, precision optics, ophthalmic lenses, advanced displays, and flat glass. This wide-ranging impact underscores the company’s versatility and the trust placed in its products and services.
The following table highlights Intersurface Dynamics’ global reach and experience:
Metric | Detail |
---|---|
Years in Business | 42 |
Locations | 8 across five countries |
Strategic Focus | Silicon Carbide and Power Semiconductor Sectors |
Fundamental Process Steps Addressed | Several in Chip Manufacturing |
Their commitment to quality is further exemplified by their ISO-9001:2015 certification, ensuring that their products meet the highest standards required by their prestigious clientele.
Commitment to Quality with ISO-9001:2015 Certification
Intersurface Dynamics stands out in the semiconductor industry for its unwavering commitment to quality, as evidenced by its ISO-9001:2015 certification. This prestigious certification is not just a badge of honor; it represents the company’s dedication to maintaining the highest standards in every aspect of its operations. The certification underscores a record of excellence, ensuring that clients receive reliable and timely service for their critical process technology demands.
The company’s advanced manufacturing techniques are complemented by a rigorous quality management system that permeates every level of production. This system is designed to consistently meet customer requirements and enhance customer satisfaction through the effective application of the system, including processes for continual improvement and the assurance of conformity to customer and applicable statutory and regulatory requirements.
- Advanced manufacturing techniques
- Rigorous quality management system
- Consistent customer satisfaction
- Continual improvement processes
- Assurance of conformity to requirements
The Role of Lapping and Polishing in Semiconductor Production
Essential Consumables for Wafer Processing
In the realm of semiconductor production, lapping and polishing consumables are indispensable. Their quality and performance directly influence the final characteristics of the wafers. For instance, CXT Polishing Carriers are renowned for their extended lifespan and contribution to machine cleanliness, which in turn reduces operational downtime and enhances the cost of ownership (CoO).
The market offers a variety of consumables tailored to different stages of wafer processing. The OnTrak cleaner, for example, is acclaimed for its cleaning performance, especially for SiC substrates, ensuring that post-processing steps do not introduce contamination that could lead to defects or yield loss.
Here is a brief overview of some key consumables and their attributes:
- CXT Polishing Carriers: Seamless construction, slurry incursion prevention.
- OnTrak Cleaner: Market-leading cleaning for SiC substrates.
- BTU International Equipment: Advanced thermal processing for various applications.
These products, among others, form the backbone of the wafer processing industry, with each playing a critical role in the production of high-quality semiconductor devices.
Advancements in Surface Finishing Technologies
The semiconductor industry has witnessed a surge in technological advancements in surface finishing technologies. Innovations in chemical and mechanical processes have significantly enhanced the efficiency and effectiveness of wafer polishing and lapping. These improvements are crucial for achieving the high precision and surface quality required for advanced semiconductor devices.
Recent developments include the introduction of new chemical agents and engineered systems designed to optimize surface treatment. For instance, the OnTrak cleaner offers market-leading cleaning performance for SiC substrates, which is vital for preventing yield loss due to contamination. Similarly, the CXT Polishing Carriers feature a patented design that extends their lifetime and reduces machine downtime, contributing to a lower cost of ownership.
The table below summarizes some of the key advancements in surface finishing technologies:
Technology | Description | Impact |
---|---|---|
OnTrak Cleaner | Enhances cleaning for SiC substrates | Reduces contamination-related defects |
CXT Polishing Carriers | Patented carrier design for improved longevity | Lowers cost of ownership and downtime |
These enhancements not only improve the surface quality of wafers but also contribute to the overall reliability and performance of semiconductor chips. As the demand for advanced semiconductor devices grows, the role of sophisticated surface finishing technologies becomes increasingly important.
Impact on Chip Performance and Reliability
The meticulous process of lapping and polishing is a critical step in semiconductor production, directly influencing the performance and reliability of the final chip. These surface-finishing solutions, such as those improving SiC wafer efficiency, play a pivotal role in enhancing the overall quality of the semiconductor devices.
By removing surface faults and reducing built-up stress from the ingot-slicing process, lapping ensures a smoother and more uniform wafer surface. This not only facilitates better layer deposition in subsequent manufacturing steps but also contributes to the longevity and stability of the semiconductor components.
The following table summarizes the impact of lapping and polishing on chip performance:
Aspect | Impact of Lapping & Polishing |
---|---|
Surface Uniformity | Increased precision and consistency |
Defect Reduction | Lower failure rates and improved yield |
Stress Management | Enhanced structural integrity |
Efficiency & Cost | Optimized production and reduced expenses |
Continued advancements in these technologies are essential to meet the ever-increasing demands for more powerful and reliable chips in various industries.
Conclusion
As we conclude our exploration of the titans of silicon wafers and US chip manufacturers, it’s evident that the industry is not just about the technology but also the strategic business maneuvers and partnerships that drive innovation forward. Companies like Wolfspeed, with their focus on silicon carbide and GaN technologies, and the diversified portfolios of subsidiaries such as BTU International, Entrepix Inc., PR Hoffman™, and Intersurface Dynamics, highlight the multifaceted approach to addressing the complex demands of chip manufacturing. The advancements in semiconductor technology, such as the 2.5GHz, 12nm, out-of-order execution chips, and AI chips capable of processing nearly 80K images per second, underscore the rapid pace of innovation. As the sector continues to evolve, with a strategic focus on materials like silicon carbide and the expansion of global suppliers across multiple countries, the US remains a pivotal player in shaping the future of semiconductor technology and its myriad applications across industries.
Frequently Asked Questions
What technologies does Wolfspeed specialize in?
Wolfspeed specializes in silicon carbide and gallium nitride (GaN) technologies, which are essential for manufacturing products for RF, power, and other applications.
How extensive is Wolfspeed’s global presence?
Wolfspeed has a significant global presence, operating in Europe, Hong Kong, China, the rest of Asia-Pacific, and the United States.
What are the key process steps in chip manufacturing that US chip manufacturers address?
US chip manufacturers address several fundamental process steps in chip manufacturing, including lapping and polishing, which are crucial for wafer processing.
Can you name some subsidiaries within the US chip manufacturing ecosystem?
The US chip manufacturing ecosystem includes subsidiaries such as BTU International, Entrepix Inc., PR Hoffman™, and Intersurface Dynamics, all of which contribute to a diversified product portfolio.
What is the significance of Intersurface Dynamics’ ISO-9001:2015 certification?
Intersurface Dynamics’ ISO-9001:2015 certification signifies the company’s commitment to quality management systems and continuous improvement in providing chemical solutions for surface engineering.
Why are lapping and polishing consumables important in semiconductor production?
Lapping and polishing consumables are essential for wafer processing as they help achieve the required surface finish on wafers, which impacts chip performance and reliability.