Thin Slices of Innovation: Understanding Wafers Technology in Electronics
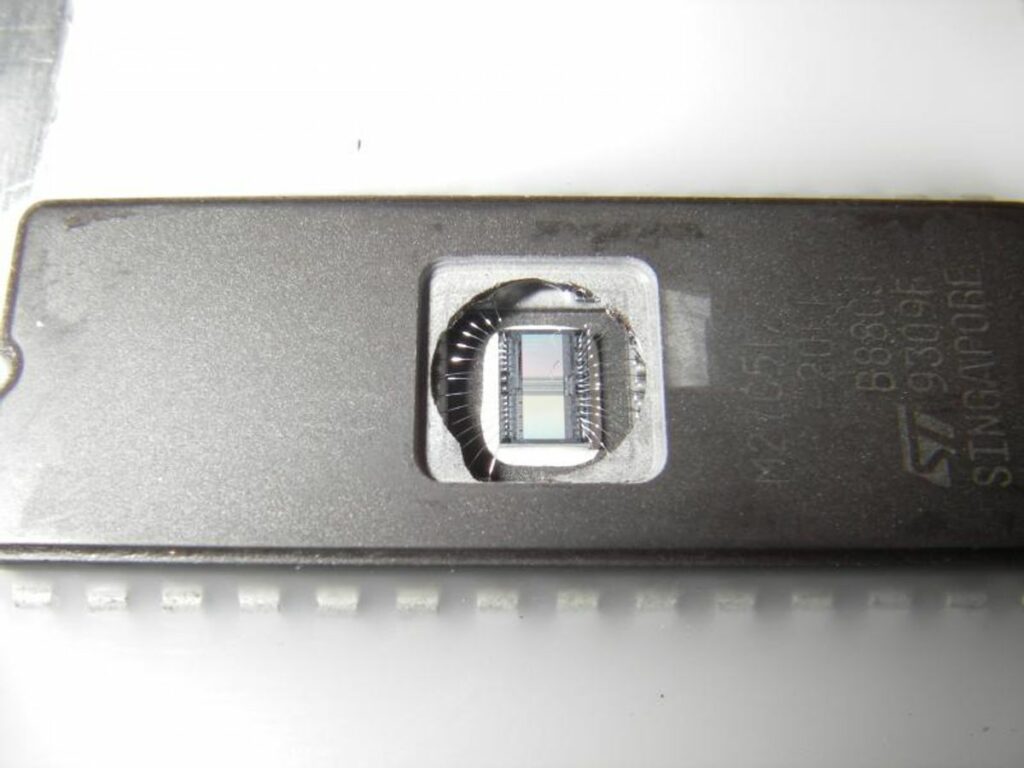
In the realm of electronics, silicon wafers are the unsung heroes that form the foundation of modern technology. These thin slices of semiconductor material are not just crucial for the production of integrated circuits found in everyday devices but also play a significant role in cutting-edge innovations and the burgeoning solar energy sector. As technology advances, wafer technology evolves to meet the demands of increasingly complex electronic systems. This article delves into the intricacies of wafer technology, exploring its evolution, the impact of wafer-level packaging, innovations in wafer processing, the significance of wafer thickness, and the global semiconductor landscape shaped by wafer demand.
Key Takeaways
- Wafer technology has significantly evolved from simple silicon ingots to ultra-thin, highly sophisticated slices essential for 3D integration in modern electronics.
- Fan-Out Wafer-Level Packaging (FOWLP) represents a leap forward in system-in-package solutions, addressing the challenges of space and performance in compact devices.
- Advancements in wafer processing, such as new etch variation analysis techniques and the emergence of 3D transistors, have drastically improved device performance.
- The production and refinement of silicon wafers, including dicing and thickness control, are critical for the efficiency and reliability of electronic devices.
- Global semiconductor demand, influenced by market expansion in integrated circuits and solar cell manufacturing, is driving innovation and growth in wafer technology.
The Evolution of Wafer Technology
From Silicon Ingots to Ultra-Thin Slices
The journey from raw silicon to the ultra-thin slices that form the backbone of modern electronics is a marvel of engineering precision. Silicon wafers are the fundamental building blocks for semiconductor devices, and their production is a multi-step process that begins with the purification of raw silicon. This purified silicon is then melted and formed into a cylindrical single crystal, known as an ingot.
The ingot undergoes a slicing operation, where it is cut into wafers using advanced cutting techniques such as a diamond-tipped saw or a wire saw with an abrasive slurry. The resulting wafers must have mirror-smooth surfaces to ensure the effective deposition of semiconductor layers. The thickness of these wafers is a critical parameter, influencing not only the efficiency of light absorption in solar panels but also the performance of integrated circuits.
The current method of wafer production can create ingots large enough to produce wafers with diameters up to 450 mm. However, this method has certain limitations, including the precision required in cutting and the potential for material waste. As the demand for smaller and more powerful electronic devices grows, the technology for slicing silicon ingots continues to evolve, striving for thinner wafers without compromising quality.
Advancements in Wafer Cutting Techniques
The relentless pursuit of efficiency in semiconductor manufacturing has led to significant advancements in wafer cutting techniques. These innovations are not just about precision, but also about the speed and cost-effectiveness of the slicing process. Mechanical sawing, once the industry standard, has evolved with the introduction of dicing blades capable of producing die sizes as small as 0.1mm. This miniaturization is critical as it allows for more chips to be produced from a single wafer, optimizing material usage and reducing waste.
In parallel, laser cutting has emerged as a sophisticated alternative, offering a contactless method that reduces mechanical stress on the wafers. The precision of laser cutting is particularly beneficial for the intricate designs of modern chips. Moreover, the integration of Single Wafer Transfer Systems has become essential. These systems provide a high degree of control and cleanliness, crucial for maintaining the integrity of wafers during the transfer stages of fabrication.
The market for Single Wafer Transfer Systems is booming, reflecting the growing complexity of chip designs and the need for precise handling. With a projected CAGR of 23.4% from 2024 to 2031, this technology is a testament to the industry’s commitment to innovation and efficiency. As we continue to push the boundaries of what’s possible, the role of cutting-edge wafer cutting and handling techniques will only become more pivotal.
The Role of Wafers in 3D Integration
The advent of 3D integration has revolutionized the semiconductor industry, enabling higher performance and functionality within a smaller footprint. This integration technique relies heavily on the use of ultra-thin wafers, which are essential for stacking and interconnecting multiple layers of circuits.
Wafer thinning has become a critical process in 3D integration, with thicknesses now approaching 10µ. This reduction in thickness introduces new challenges, such as increased mechanical stress and potential for wafer warpage, interconnect/Si cracking, and delamination. Ensuring the reliability of these thin wafers is paramount, as any failure can significantly impact device performance.
Alignment is another crucial aspect of 3D integration. Precise wafer-to-wafer alignment is necessary to achieve the interlayer connections required for 3D ICs. The complexity of aligning multiple layers with high accuracy has led to the development of advanced alignment technologies, which are continually being refined to meet the stringent demands of modern electronics.
Wafer-Level Packaging and Its Impact on Electronics
Understanding Fan-Out Wafer-Level Packaging (FOWLP)
Fan-Out Wafer-Level Packaging (FOWLP) represents a significant leap in integrated circuit packaging technology. Unlike traditional WLP solutions, FOWLP eliminates the need for a silicon interposer, bonding the package directly onto a circuit board. This approach not only simplifies the assembly process but also allows for the integration of multiple chips into a single IC structure, enhancing the overall functionality and performance of the device.
The benefits of FOWLP are numerous, including reduced package size and thickness, improved thermal performance, and the ability to achieve finer pitch interconnections. Samsung, a leader in the industry, has been at the forefront of this technology, offering both panel and wafer level fan-out package solutions. With FOWLP set to enter mass production in Q4-23, the industry is poised for a shift towards more efficient and compact electronic devices.
However, the transition to FOWLP is not without its challenges. The increased substrate size, up to 600 mm, presents new performance and reliability concerns, particularly in high-density packaging. The table below summarizes some of the key reliability tests conducted on advanced wafer-level packages:
Topic | Device Tested | Test Type | References |
---|---|---|---|
Thermomechanical reliability | aWLP (advanced wafer-level package) | FEA modeling | [111] |
2.5D packaging development | CoWoS MCM | FESA to check warpage and thermal cycling | [101, 112] |
CoWoS architecture in 2.5D system | CoWoS-S compared to CoWoS-L | μ-bump, TSV, TIV, and C4 daisy chains | [113] |
3D die-to-wafer hybrid Cu bonding | HCB with 4 μm pitch and 2 μm pad | Daisy chains that consist of 2 μm pad in 4 μm | [Google Scholar] |
As the semiconductor industry continues to evolve, the importance of reliable and efficient packaging solutions like FOWLP cannot be overstated. It is a technology that not only addresses current demands but also sets the stage for future innovations in electronics.
Challenges and Reliability in Thin Wafer Implementation
The implementation of thin wafers in advanced packaging systems introduces a unique set of challenges that impact their reliability. As wafer thicknesses approach 10 micrometers, the mechanical stress and strain on the wafers increase significantly. This can lead to a variety of failure risks, such as wafer warpage, interconnect and silicon cracking, delamination, and deterioration of device characteristics.
In the realm of 3D integration, the alignment of wafers is critical. However, issues such as wafer-to-wafer alignment challenges and thermal misalignment over time complicate the process. These alignment issues can result in bonding failures and must be carefully evaluated to ensure the long-term reliability of the packages.
The table below summarizes some of the key reliability concerns and the associated technologies:
Concern | Technology | Impact |
---|---|---|
Wafer Warpage | 3D IC Integration | Mechanical Stress |
Interconnect Cracking | CoWoS | Electrical Failure |
Thermal Misalignment | Wafer-to-Wafer Alignment | Bonding Failures |
Reliability testing for modern microelectronics packaging has evolved to identify and mitigate these risks. It is essential to understand that the reliability of thin wafer-based systems is not just a matter of material integrity but also involves complex interactions between various packaging processes and materials.
The Future of System-in-Package Solutions
The System in Package (SiP) technology is rapidly evolving, marking a significant shift from traditional single-chip packaging to a more integrated approach. SiP allows for the combination of multiple integrated circuits (ICs) within a single package, enhancing functionality while maintaining a compact footprint. This integration is particularly beneficial in applications where space is at a premium and high performance is required.
Recent advancements have blurred the lines between a monolithic chip and a packaged assembly of heterogeneous chips. The trend towards heterogeneous integration (HI) signifies a move to more complex systems that are not only more efficient in terms of power and latency but also offer higher bandwidths. The adoption of silicon processing techniques in packaging has been a key factor in this evolution.
The table below outlines some of the key drivers for the adoption of SiP technology:
Driver | Impact on SiP Adoption |
---|---|
Space Constraints | Enables compact, multi-functional devices |
Performance Requirements | Facilitates high-speed, low-latency operation |
Integration Complexity | Simplifies system design and assembly |
Thermal Management | Improves heat dissipation for better reliability |
As we look to the future, the continued refinement of SiP solutions is expected to play a pivotal role in the semiconductor industry. The focus on system-level integration will likely lead to further innovations, ensuring that SiP remains at the forefront of packaging technologies.
Innovations in Wafer Processing
New Techniques to Analyze and Reduce Etch Variation
In the pursuit of ever-smaller and more efficient electronic devices, the semiconductor industry continues to innovate in the realm of wafer etching. Etch variation is a critical factor that can significantly impact device performance and yield. As device geometries shrink, the need for precision in etching becomes paramount. Traditional methods such as wet etching, which involves chemical baths, are mainly used for cleaning wafers, while dry etching is predominantly used for creating semiconductors.
Recent advancements in etching technology include the development of new materials for 3D integration and the refinement of processes like electron beam lithography (EBL) and extreme ultraviolet lithography (EUVL). These techniques aim to enhance the precision and control of the etching process. Additionally, the integration of process automation and the application of artificial intelligence (AI) and machine learning (ML) are playing a significant role in reducing variability.
The table below summarizes some of the key innovations in etch technology and their contributions to reducing etch variation:
Innovation | Description | Impact on Etch Variation |
---|---|---|
EBL | Utilizes focused electron beams for patterning | Increases precision and reduces variability |
EUVL | Employs extreme ultraviolet light for finer patterning | Enhances resolution and control |
AI/ML Integration | Applies smart algorithms for process optimization | Minimizes variability and improves consistency |
As the industry moves towards more complex 3D structures, such as 3D NAND and 3D transistors, the importance of these new techniques cannot be overstated. They are essential for maintaining the integrity of the intricate patterns required for next-generation devices.
The Emergence of 3D Transistors and NAND Memory
The advent of 3D transistors marked a significant leap in semiconductor technology. Unlike traditional planar transistors, 3D transistors have source and drain regions that are structured as fins on the gate, allowing for more control over the current and reducing leakage. This architectural change has paved the way for increased transistor density and improved energy efficiency, which are critical for the advancement of modern electronics.
In parallel, the development of 3D NAND memory has revolutionized data storage. By stacking memory cells vertically, 3D NAND provides a substantial increase in storage capacity while occupying the same footprint as 2D NAND. This vertical arrangement not only boosts capacity but also enhances performance and reliability.
The integration of these technologies has been instrumental in meeting the demands of next-generation applications, such as 5G, which require high data transfer rates and low latency. The table below summarizes the key differences between traditional and 3D technologies:
Feature | Traditional Planar | 3D Technology |
---|---|---|
Structure | Horizontal layers | Vertical stacking |
Density | Limited | High |
Energy Efficiency | Lower | Higher |
Performance | Standard | Enhanced |
As the electronics industry continues to evolve, the exploration of alternative materials like graphene and transition metal dichalcogenides offers the potential for even more efficient transistor designs, challenging the dominance of silicon and opening new avenues for innovation.
Etching Precision and Its Effect on Device Performance
The precision of etching processes in semiconductor manufacturing is a critical factor that directly impacts the performance and reliability of electronic devices. Advanced etching techniques such as extreme ultraviolet lithography (EUVL) and electron beam lithography (EBL) have enabled the creation of finer patterns, essential for the miniaturization of components. The market for semiconductor wafer dry etching equipment is experiencing significant growth, driven by the demand for sophisticated electronics.
Etching precision is not only about the fidelity of patterns but also about the uniformity across the wafer. Variations in etch depth can lead to inconsistent circuit behavior and reduced device yield. Innovations like smart cleaning technologies and chemical mechanical polishing (CMP) process enhancements are instrumental in achieving the desired uniformity. The table below summarizes some of the key technologies influencing etching precision:
Technology | Application | Impact on Etching Precision |
---|---|---|
EUVL | Pattern miniaturization | High precision in fine patterns |
EBL | Direct write lithography | Accurate pattern creation |
CMP Enhancements | Surface planarization | Improved uniformity and yield |
Smart Cleaning | Selective cleaning | Consistent etch depths |
As the industry moves towards more complex 3D structures, such as quantum dots and nanotechnology applications, the role of etching precision becomes even more pivotal. These advancements not only enhance device performance but also extend the life of components, as seen in the improved reliability of solder joints with controlled intermetallic compound (IMC) thickness.
Silicon Wafers: The Foundation of Modern Electronics
The Purification and Formation of Silicon Wafers
The journey of a silicon wafer begins with the transformation of raw silicon into a highly pure form. This process is critical as it determines the quality and performance of the final semiconductor products. Silicon, often derived from silicon dioxide found in sand or quartz, undergoes a rigorous purification process to remove impurities. The result is a material integral to the production of semiconductors, which are the heart of all types of electronic devices.
Once purified, the silicon is melted in a quartz crucible within a graphite chamber, surrounded by graphite heaters. In an environment of Argon gas and under vacuum, the molten silicon is pulled using a seed crystal, a method known as the Czochralski (CZ) process. This forms a single crystal ingot, which is then meticulously sliced into ultra-thin wafers. The cutting is performed using advanced techniques such as a diamond-tipped saw or a wire saw with abrasive slurry, ensuring mirror-smooth surfaces that are ready for subsequent semiconductor layering.
The following table summarizes the key stages in silicon wafer production:
Stage | Description |
---|---|
1. Purification | Removal of impurities from raw silicon to achieve high purity. |
2. Melting | Silicon is melted in a quartz crucible under vacuum and Argon atmosphere. |
3. Crystal Pulling (CZ Method) | A seed crystal is used to pull a single crystal ingot from molten silicon. |
4. Slicing | The ingot is sliced into wafers using precision cutting techniques. |
The precision in these steps is not just about achieving the necessary purity and structure, but also about ensuring the wafers are of the correct thickness, which is vital for the efficiency of the devices they will become a part of.
Wafer Dicing: Slicing the Future of Technology
Wafer dicing is the critical back-end process that transforms a completed wafer into individual semiconductor chips, or dies. This process is not only about precision cutting; it’s about ensuring the integrity and performance of the chips that will eventually power countless electronic devices. The yield of wafer dicing is a measure of its efficiency and effectiveness, with the goal of maximizing the number of usable chips while minimizing waste.
The process typically involves automated methods such as mechanical sawing or laser cutting. Mechanical sawing uses a dicing saw with a circular blade, capable of cutting dies as small as 0.1mm. Post-dicing, the delicate task of transferring these chips to the die-bonding stage is handled by specialized die-handling equipment, underscoring the need for precision at every step.
As the semiconductor industry pushes towards greater miniaturization and complexity, the role of Single Wafer Transfer Systems becomes increasingly important. These systems provide the necessary control and cleanliness, crucial for maintaining the high standards required in semiconductor fabrication. With the relentless drive towards higher chip densities, the demand for such precise and reliable wafer processing solutions is expected to grow.
The Critical Role of Wafer Thickness in Device Efficiency
The drive towards miniaturization in electronics has placed a spotlight on the critical role of wafer thickness in device efficiency. Thinner wafers not only allow for a more compact form factor but also bring about significant performance enhancements. For instance, reducing the thickness of wafers can bring the ground plane closer to the chip’s backside, which is particularly beneficial for high-frequency applications, leading to improved electrical efficiency and signal integrity.
However, the pursuit of thinness is not without its challenges. As wafers become thinner, they are subjected to increased mechanical stress, which can lead to warpage, cracking, and delamination. These issues can compromise the reliability of the device and deteriorate its characteristics. The table below illustrates some of the potential failure risks associated with thin wafer implementation:
Failure Risk | Consequence |
---|---|
Wafer Warpage | Misalignment during layer stacking |
Interconnect/Si Cracking | Electrical failure |
Delamination | Reduced structural integrity |
Addressing these challenges requires a careful balance between the benefits of thinner wafers and the need to maintain structural integrity and reliability. Innovations in wafer processing and packaging technologies continue to push the boundaries, enabling the use of ultra-thin wafers while mitigating the associated risks.
The Global Semiconductor Landscape and Wafer Demand
Market Sentiments and the Expansion of Integrated Circuits
The semiconductor industry has witnessed a remarkable expansion, with integrated circuits (ICs) becoming the cornerstone of modern electronics. Companies are increasingly embedding ICs into their products to enhance efficiency and intelligence, catering to the demand for lightweight, fast, and miniaturized devices. The global sales of semiconductors have soared, as evidenced by a report from the Semiconductor Industry Association, which noted a climb from USD 139.0 billion in 2008 to an impressive USD 557.4 billion by 2022.
The IC substrate market, a critical component of semiconductor manufacturing, has also seen significant growth. Valued at $15.14 billion in 2022, it is projected to reach $28.96 billion by 2028, with an anticipated compound annual growth rate (CAGR) of 11 percent. This growth is fueled by substantial investments in the advanced IC substrate sector, totaling $15.5 billion between 2021 and 2022. These investments are strategically aimed at meeting the burgeoning market demand and are often a collaborative effort between customers and industry leaders.
However, the focus on expanding production capabilities has led to a scenario where the increased capacity is frequently reserved for the investing entities, which could restrict access for smaller players in the market. This dynamic underscores the importance of strategic partnerships and investments in shaping the future landscape of the semiconductor industry.
India’s Role in the Semiconductor Industry
India’s foray into semiconductor manufacturing marks a pivotal shift in the global electronics landscape. The country is making strides with significant investments, such as Applied Materials’ commitment to processing 300 mm wafers, a first for India’s private sector. This move signals India’s dedication to technological prowess and its potential to influence the semiconductor market.
Key developments like Micron’s ATMP unit construction and LAM Research’s Semiverse Solutions initiative are poised to strengthen India’s semiconductor ecosystem. These efforts are not just about meeting local demand but also about integrating India into the global supply chain of high-tech components.
The future outlook for India in the semiconductor industry is optimistic. Strategic partnerships with industry leaders and a focus on innovation suggest that India is on a path to becoming a significant player. The country’s success in this field could drive both technological advancement and economic growth, contributing to a more diverse and resilient global semiconductor market.
Solar Cell Manufacturing and Silicon Wafer Utilization
The solar industry’s reliance on silicon wafers is a testament to their versatility beyond traditional electronics. Silicon wafers serve as the substrate for solar cells, playing a crucial role in the conversion of sunlight into electricity. The process of manufacturing solar panels begins with the purification of silicon, which is then crafted into wafers ready for the production line.
The manufacturing steps for solar panels include the transformation of sand into highly pure silicon, followed by the slicing of silicon into wafers. These wafers are then doped to create an electrical junction, a critical step in enabling the flow of electricity. The precision in wafer thickness is vital, impacting the solar cell’s efficiency and light absorption capabilities.
As the demand for renewable energy sources escalates, the utilization of silicon wafers in solar cell manufacturing is expected to grow. This growth is driven by the anticipated expansion in the integrated circuits and solar markets, highlighting the importance of continued innovation in wafer technology for sustainable energy solutions.
Conclusion
In the intricate dance of innovation that characterizes the electronics industry, silicon wafers are the unsung heroes, underpinning the marvels of modern technology. From the meticulous crafting of these ultra-thin slices to their role in advanced packaging technologies like FAN-OUT WAFER LEVEL EWLB and 3D ICs, wafers are integral to the semiconductor production process. Challenges such as wafer thinning and the associated reliability issues underscore the need for ongoing research and development. As we stand on the cusp of the 5G era, the importance of wafers is only set to increase, with new techniques like 3D NAND and 3D transistors heralding a future of even more compact and efficient electronic devices. The wafer technology, a blend of precision engineering and material science, continues to evolve, driving the relentless march of electronics towards greater heights.
Frequently Asked Questions
What is wafer technology and why is it important in electronics?
Wafer technology involves the creation of thin slices of semiconductor material, typically silicon, which are used as the substrate for integrated circuits. These wafers are essential in the production of electronic components found in devices like computers, smartphones, and solar cells.
How have wafer cutting techniques evolved over time?
Wafer cutting techniques have evolved from using simple mechanical saws to advanced methods like diamond-tipped saws and wire saws with abrasive slurry, enabling the production of ultra-thin wafers with precise thickness essential for device efficiency.
What is Fan-Out Wafer-Level Packaging (FOWLP) and its significance?
FOWLP is an advanced packaging technique that allows for more I/O connections by spreading out the die beyond its original footprint. It’s significant because it enables higher performance and functionality in a smaller package, essential for modern electronics.
What are the challenges associated with implementing thin wafers in electronics?
Implementing thin wafers can lead to reliability issues due to increased mechanical stress and strain. Challenges include wafer warpage, interconnect/Si cracking, delamination, and deterioration of device characteristics as wafer thicknesses approach 10µm.
How is the emergence of 3D transistors and NAND memory changing wafer processing?
The emergence of 3D transistors and NAND memory, where components are stacked vertically, requires new wafer processing techniques. This innovation leads to higher density and improved performance, but also demands greater precision in etching and manufacturing.
What role does India play in the global semiconductor industry?
India is becoming an increasingly important player in the semiconductor industry, contributing to market expansion and integrated circuit development. The country’s growing tech sector and supportive government policies are fostering a conducive environment for semiconductor manufacturing.