Top Industrial Automation Equipment for Modern Factories
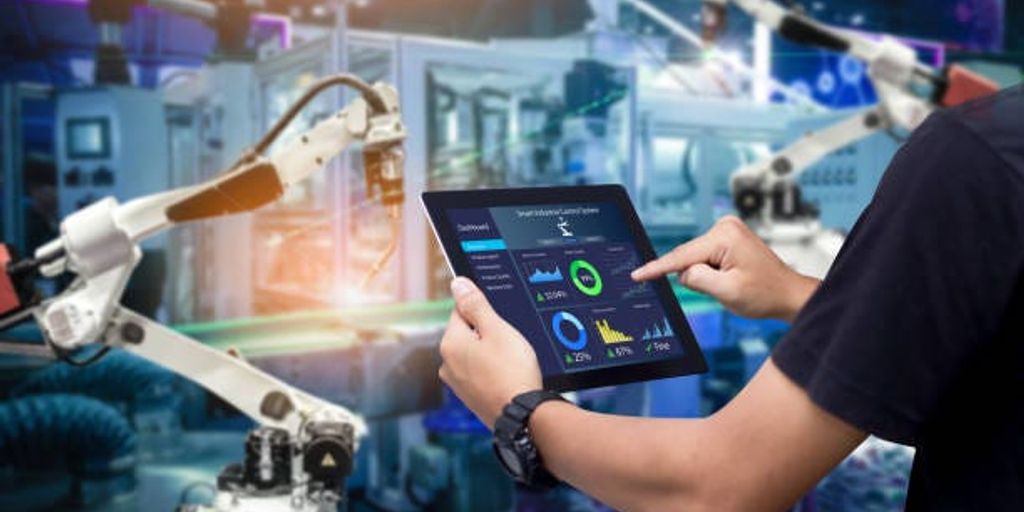
Automation in factories means using machines and technology to do tasks with little or no human help. This trend is growing in many industries like aerospace, defense, and automotive. Automation helps make more products faster, reduces costs, and keeps quality high.
Key Takeaways
- Industrial robots can perform tasks like welding, painting, and assembly without human intervention.
- Automated Guided Vehicles (AGVs) move materials around a factory floor without the need for human drivers.
- Programmable Logic Controllers (PLCs) are used to control machinery and processes in real-time.
- Human-Machine Interfaces (HMIs) allow operators to interact with machines using touchscreens and other input devices.
- Supervisory Control and Data Acquisition (SCADA) Systems monitor and control industrial processes from a central location.
1. Industrial Robots
Industrial robots are a cornerstone of modern manufacturing. These machines are designed to perform tasks that are hazardous to humans or require precision and endurance beyond human capabilities. They can work multiple shifts without tiring and maintain a high level of quality and efficiency.
Robots in manufacturing can handle a variety of tasks, including:
- Welding, such as arc welding
- Spray painting
- Assembly work, like pick-and-place for printed circuit boards
- Packaging and palletizing
- Inspecting products to ensure they meet quality standards
One of the key advantages of industrial robots is their ability to be reprogrammed for different tasks. This flexibility allows them to adapt to various manufacturing needs, whether it’s handling, transferring, or processing materials and parts. Additionally, robots equipped with inspection and vision capabilities can detect required customizations for batches of similar, mixed parts.
In today’s factories, robots are often used in manufacturing operations to improve efficiency and safety. They can work autonomously, adjusting their actions based on the task at hand or the product’s level of completeness. This autonomy not only allows robots to collaborate safely with humans but also enables them to work together, such as in portable assembly lines where autonomous vehicles ferry work in progress between stations.
2. Automated Guided Vehicles (AGVs)
Automated Guided Vehicles (AGVs) are portable robots that follow marked lines or wires on the floor, or use radio waves, vision cameras, or magnets to navigate. These vehicles have transformed material handling in modern factories. They were first used in the 1950s, following tracks or wires on factory floors, but today’s AGVs are much more advanced.
AGVs are used to move materials around factories, warehouses, and distribution centers. They help streamline operations by reducing time, effort, and costs, while also minimizing manual errors. This leads to better production efficiency and outcomes.
Some common types of automated material handling equipment include:
- Stockers
- Automated storage and retrieval systems (ASRS)
- Rail-guided vehicles (RGVs)
- Automated guided vehicles (AGVs)
- Autonomous intelligent vehicles (AIVs)
AGVs offer several benefits:
- High levels of production
- Low cost per unit produced
- Consistent quality in production
- Easy to trace production procedures
- Limited maintenance required
However, there are also some drawbacks:
- High initial cost of installation
- Hard to accommodate changes
Overall, AGVs play a crucial role in modern industrial automation, making processes more efficient and reliable.
3. Programmable Logic Controllers (PLCs)
Programmable Logic Controllers (PLCs) are essential for modern industrial automation. They act as the brain of the factory floor, controlling machinery and processes with high reliability. PLCs are designed to handle many tasks at once, making them perfect for complex industrial environments.
PLCs are modular, meaning you can add or remove parts like input and output modules, power supplies, and CPUs to fit different needs. This flexibility makes them highly adaptable to various applications. Modern PLCs also support modular programming, allowing for easier updates and maintenance.
One of the key benefits of PLCs is their durability. They are built to withstand harsh industrial conditions, including electrical and mechanical stress. Many PLC components are even hot-pluggable, meaning they can be replaced without shutting down the system.
In summary, PLCs are a cornerstone of industrial automation, offering flexibility, reliability, and ease of use.
4. Human-Machine Interfaces (HMIs)
Human-Machine Interfaces (HMIs) are essential in modern factories. They act as the bridge between operators and machines, allowing for seamless interaction and control. Effective human-machine interfaces earn higher efficiencies by enhancing manufacturing processes and improving operator interaction.
HMIs serve as the front end for Programmable Logic Controllers (PLCs), providing a user-friendly way to program and monitor tasks. This makes it easier for operators to manage complex systems without needing deep technical knowledge.
In addition to improving efficiency, HMIs also contribute to better quality control. By providing real-time data and feedback, they help operators make informed decisions quickly. This reduces errors and ensures that production stays on track.
Overall, HMIs play a critical role in modern industrial automation, making factories more efficient and easier to manage.
5. Supervisory Control and Data Acquisition (SCADA) Systems
Supervisory Control and Data Acquisition (SCADA) systems are essential for modern factories. They help in monitoring and controlling industrial processes. SCADA systems are widely used in continuous flow production control within the steel industry production environment. These systems gather data from sensors and other devices, allowing operators to make informed decisions.
SCADA systems have several key features:
- Real-time data acquisition
- Remote monitoring and control
- Alarm processing and notification
- Historical data analysis
These features make SCADA systems invaluable for maintaining efficiency and safety in industrial settings. They also support automated systems’ control functions and strategies, reducing the need for constant human supervision. SCADA systems are a cornerstone of smart manufacturing, enabling scalable and intelligent machine operations.
6. Distributed Control Systems (DCS)
Distributed Control Systems (DCS) are essential for managing complex industrial processes. They provide centralized control with decentralized elements, allowing for efficient and reliable operations. DCS are commonly used in industries like oil and gas, chemical manufacturing, and power generation.
Key Features of DCS
- Centralized Monitoring: Operators can monitor the entire system from a central location.
- Decentralized Control: Control functions are distributed across various subsystems.
- Scalability: Easily scalable to accommodate growing industrial needs.
- Reliability: High reliability due to redundancy and fault-tolerant design.
Benefits of Using DCS
- Improved Efficiency: Streamlines operations and reduces manual intervention.
- Enhanced Safety: Advanced safety features to protect both equipment and personnel.
- Cost-Effective: Reduces operational costs through automation and efficient resource management.
Applications of DCS
- Oil and Gas: Used for controlling drilling operations and refining processes.
- Chemical Manufacturing: Manages complex chemical reactions and production lines.
- Power Generation: Controls various aspects of power plants, from generation to distribution.
7. Machine Vision Systems
Machine vision is an essential component of how digital systems interact with the real world. It lets automated systems see components, products, patterns, and more. Machine vision systems are crucial in modern factories for quality control and inspection. They use cameras and smart sensors to monitor processes and ensure everything runs smoothly.
Key Components
- Cameras and image-capture equipment: These are the eyes of the system, capturing images of products and components.
- Image sensors and storage devices: These store the captured images for processing and analysis.
- Lenses: They focus the images so the system can see clearly.
- Lighting and illumination systems: Proper lighting is essential for capturing clear images.
- Optical subsystems: These help in the precise capture and processing of images.
- Software: This analyzes the images and makes decisions based on what it sees.
- System boards: These are the brains of the system, processing the data from the cameras and sensors.
- Test and measurement equipment: These ensure the system is working correctly.
Benefits
Machine vision systems offer several benefits:
- Improved Quality Control: They can detect defects that are too small for the human eye.
- Increased Efficiency: Automated inspection speeds up the production process.
- Cost Savings: Reducing the number of defective products saves money.
- Consistency: Machines don’t get tired, so they provide consistent results.
Applications
Machine vision systems are used in various applications, including:
- Assembly line inspection: Checking products for defects as they are made.
- Sorting: Separating products based on size, shape, or color.
- Guidance: Helping robots and other machines navigate and perform tasks accurately.
- Measurement: Ensuring products meet specific size and shape requirements.
8. Industrial IoT Sensors
Industrial IoT (IIoT) sensors are transforming modern factories by providing real-time data and insights. These sensors are embedded in various devices along the production line, in the field, and in control centers. IoT devices gather data from machines, AGVs (Automated Guided Vehicles), workers, and goods to enhance the efficiency of production processes. This data can be used to monitor sales orders, parts received, or identify issues along the production line.
One of the key benefits of IIoT sensors is their ability to enable predictive maintenance. By continuously monitoring equipment, these sensors can predict when a machine is likely to fail and schedule maintenance before a breakdown occurs. This not only reduces downtime but also extends the lifespan of the equipment.
IIoT sensors also facilitate customized movement for robots. For example, they can adjust the speed of a robot based on its location. Companies like ABB are now producing robots that can store data and communicate it to other devices, making automation more efficient.
In summary, IIoT sensors are a crucial component of modern industrial automation. They provide granular data, enable predictive maintenance, and allow for more flexible and efficient operations.
9. Automated Storage and Retrieval Systems (ASRS)
Automated Storage and Retrieval Systems (commonly referred to as ASRS systems) are most commonly used in manufacturing and distribution facilities. These systems are designed to streamline operations by reducing the time, effort, and cost associated with manual storage and retrieval tasks. ASRS systems can significantly improve production efficiency and outcomes.
Some common types of automated material handling equipment include:
- Stockers
- Rail-guided vehicles (RGVs)
- Automated guided vehicles (AGVs)
- Autonomous intelligent vehicles (AIVs)
The main purpose of ASRS is to enhance workflow by minimizing manual errors and increasing the speed of operations. These systems are a key component in modern industrial automation, helping businesses achieve higher production rates and better efficiency.
10. Conveyor Systems
Conveyor systems are essential in modern factories for moving materials efficiently. They help increase production rates by automating the transport of goods. These systems come in various types, each suited for different tasks and environments.
Types of Conveyor Systems
- Belt Conveyors: These are the most common type, ideal for moving items of various sizes and shapes.
- Roller Conveyors: Suitable for heavy loads, these use rollers to move items along.
- Chain Conveyors: Perfect for moving heavy items in a straight line.
- Overhead Conveyors: These save floor space by moving items above the ground.
- Pneumatic Conveyors: Use air pressure to move bulk materials through tubes.
Benefits of Conveyor Systems
- Efficiency: They reduce the need for manual labor, speeding up production.
- Safety: By automating material transport, they lower the risk of workplace injuries.
- Versatility: Different types can handle a wide range of materials and products.
Applications of Conveyor Systems
Conveyor systems are used in various industries, including:
- Manufacturing: For moving parts and products through assembly lines.
- Warehousing: To transport goods within storage facilities.
- Food and Beverage: For moving products through different stages of production.
- Mining: To transport raw materials from one place to another.
In summary, conveyor systems are a vital part of modern industrial automation, offering numerous benefits and applications across different sectors.
Conclusion
In conclusion, industrial automation equipment is transforming modern factories by making them more efficient, productive, and safe. From robots and conveyors to advanced control systems, these technologies are helping industries like automotive, aerospace, and food processing achieve higher output and better quality. As automation continues to evolve, it will play an even bigger role in shaping the future of manufacturing. Embracing these advancements not only reduces costs but also ensures consistent and reliable production. Modern factories that invest in automation are setting themselves up for long-term success in an increasingly competitive market.
Frequently Asked Questions
What is industrial automation?
Industrial automation uses machines, control systems, and technology to do tasks with little or no human help. It makes work faster and more consistent.
How do industrial robots help factories?
Industrial robots can do repetitive tasks quickly and accurately. They help increase production and reduce mistakes.
What are Automated Guided Vehicles (AGVs)?
AGVs are robots that move materials around a factory. They follow markers or wires on the floor and help transport goods without human help.
Why are Programmable Logic Controllers (PLCs) important?
PLCs are computers used to control machines. They can be programmed to do different tasks, making them very useful in automation.
What is the role of Human-Machine Interfaces (HMIs)?
HMIs allow humans to interact with machines. They use screens and buttons to control and monitor equipment.
How does automation improve safety?
Automation reduces the need for humans to do dangerous tasks. Machines can handle risky jobs, making the workplace safer.