Top Semiconductor Equipment Manufacturers Shaping the Microchip Industry
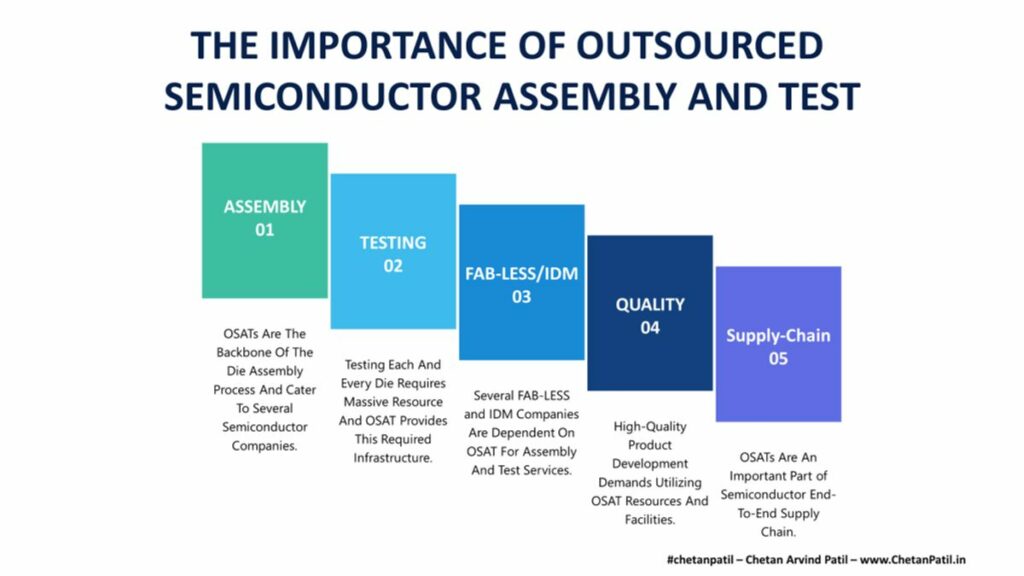
The semiconductor equipment manufacturing sector is a pivotal component in the microchip industry, driving innovation and enabling the production of increasingly sophisticated and miniaturized chips. This article delves into the top manufacturers that are shaping the industry, the technological advancements they are pioneering, the dynamic global industry landscape, market trends, and the challenges and opportunities that lie ahead. As we explore the intricate world of semiconductor equipment manufacturing, we uncover the key players and innovations that are essential to the electronic devices we rely on daily.
Key Takeaways
- Applied Materials, Lam Research, ASML, and Tokyo Electron are leading the semiconductor equipment manufacturing industry with cutting-edge technologies.
- Innovations such as nanoimprint lithography and hybrid bonding are revolutionizing chip fabrication, enabling further miniaturization and 3D integration.
- Global industry dynamics, including US-China trade tensions and regional semiconductor ecosystems like Arizona, are significantly influencing the supply chain and industry growth.
- Market trends indicate a surge in demand for semiconductor chips, with a particular increase in the automotive sector and the emergence of specialized processors and memory technologies.
- The industry faces challenges such as the ABF substrate shortage and thermal integrity management, but opportunities like silicon carbide advancements present new frontiers for development.
Leading Players in Semiconductor Equipment Manufacturing
Applied Materials: Innovation at the Forefront
Applied Materials stands as a titan in the semiconductor equipment manufacturing industry, consistently pushing the boundaries of innovation. The company’s commitment to research and development has positioned it as a key player in the Integrated Circuit Advanced Packaging Systems (ICAPS) sector. The steady growth in demand for ICAPS chips is a testament to the powerful megatrends shaping the industry, which in turn has absorbed the used equipment market and bolstered new equipment sales.
The company’s success can be attributed to its strategic focus on several core areas. Here’s a glimpse into what makes Applied Materials a leader:
- Pioneering new materials to enhance chip performance
- Developing advanced process technologies for scaling
- Investing in AI and machine learning to optimize manufacturing
- Expanding capabilities in metrology and inspection
As the semiconductor landscape evolves, Applied Materials continues to adapt, ensuring that their equipment meets the ever-increasing complexity of chip production. Their forward-thinking approach not only drives the industry forward but also sets a high bar for competitors.
Lam Research: Pioneering Etch and Deposition Technologies
Lam Research stands at the forefront of etch and deposition technologies, essential processes in semiconductor manufacturing. Their commitment to innovation is evident in their latest offerings, which cater to the evolving needs of the industry. Lam Research introduces breakthrough deposition technique to enhance the performance of various semiconductor components.
One of the key technologies developed by Lam Research is the Pulsus deposition process. This advanced technique is designed to deposit high-quality films that are critical for optimizing RF filters and MEMS microphones. The effectiveness of Pulsus is particularly notable in the context of scandium levels in the film, which play a significant role in the overall quality and performance of the end product.
Lam Research’s dedication to advancing semiconductor technology not only drives industry standards but also opens up new possibilities for customer-specific solutions. Their focus on targeted, simple, and reproducible measurement of electrical properties is a testament to their role as a leader in the semiconductor equipment manufacturing sector.
ASML: Mastering Lithography for Chip Miniaturization
ASML stands at the forefront of the semiconductor industry, primarily known for its advanced photolithography machines. These machines are crucial for the production of computer chips, employing a process that etches circuit patterns onto silicon wafers. ASML’s technology is pivotal in the race to shrink chip sizes, pushing the boundaries down to 7nm, 5nm, and even approaching the 2nm frontier.
The company’s expertise in high-NA (numerical aperture) lithography is setting the stage for the next generation of chip manufacturing. This technique allows for finer patterning on chips, which is essential for enhancing processing capabilities and accommodating the increasing demand for powerful and efficient electronics.
ASML’s contributions to the semiconductor industry are not just limited to lithography. Their holistic approach includes a suite of services and technologies that support the entire chip fabrication process. The following list highlights some of the key areas where ASML is making an impact:
- Development of cutting-edge photolithography equipment
- Pioneering high-NA lithography for ultra-fine patterning
- Providing comprehensive customer support and maintenance services
- Engaging in partnerships and collaborations to drive innovation forward
Tokyo Electron: Diverse Portfolio in Semiconductor Production
Tokyo Electron Ltd. stands out in the semiconductor equipment manufacturing landscape with its broad range of products that cater to various stages of the chip production process. The company’s commitment to innovation and technology synergy is evident as it continuously invests in new technologies that complement its existing portfolio. This strategic approach not only strengthens Tokyo Electron’s market position but also ensures that it remains at the cutting edge of semiconductor production.
The company’s diverse offerings include systems for photolithography, etching, deposition, and more, each playing a crucial role in the intricate process of chip fabrication. Tokyo Electron’s ability to provide comprehensive solutions has made it a preferred partner for many semiconductor producers around the globe. Here’s a glimpse into their product categories:
- Photolithography Systems
- Etching Equipment
- Deposition Systems
- Thermal Processing Systems
- Surface Preparation Systems
With a keen eye on the evolving needs of the industry, Tokyo Electron is well-positioned to address the challenges of modern semiconductor manufacturing. The company’s proactive engagement with portfolio companies through development support highlights its dedication to fostering technological advancements and maintaining a competitive edge.
Technological Advancements in Chip Fabrication
The Evolution of Silicon Wafer Manufacturing
The production of silicon wafers is foundational to the semiconductor industry, involving intricate and energy-intensive processes. These wafers are the substrates upon which semiconductor devices are built, making their quality and purity critical for the performance of the final chips. Over the years, the manufacturing process has seen significant advancements, from the initial creation of ultra-pure silicon to the precise deposition of various materials.
Silicon wafer fabrication begins in a clean room environment, where wafers are processed with thermal silicon dioxide (SiO2) and often an Indium Tin Oxide (ITO) layer. This layer is crucial as it serves as a gold adhesion layer, enhancing the reliability and precision of the wafers. Such advancements have allowed for the production of wafers that meet the stringent quality requirements of both small and large chemical companies.
The industry’s relentless pursuit of miniaturization has driven the evolution of wafer manufacturing. As chip sizes shrink towards 2nm and 3nm scales, the demand for wafers with even higher purity and defect-free surfaces has intensified. This has led to the development of new materials and processes, ensuring that silicon wafers continue to be the powerhouses of semiconductor chip production.
Breakthroughs in Power Management Integrated Circuits
The global power management Integrated Circuit (IC) market is witnessing a significant transformation. With the increasing demand for energy-efficient electronics, PMICs have become critical in optimizing power consumption and enhancing battery life across various devices. In 2022, the market size was valued at USD 33.20 Billion and is projected to reach USD 147.87 Billion by 2032, indicating a robust growth trajectory.
Power management ICs are often likened to the ‘heart’ of electronic systems, supplying the necessary voltage and managing power distribution to ensure optimal performance. Engineers face numerous trade-offs in SoC design, balancing Power, Performance, and Area (PPA) to meet stringent design specifications. These challenges are compounded by the need for advanced packaging to maintain power and signal integrity, as well as effective cooling solutions.
Adaptive clocking schemes have emerged as a solution to manage dynamic voltage variation and maximize system performance while keeping temperatures within safe margins. This approach is part of a broader trend towards more sophisticated power management strategies that are essential for the next generation of semiconductor devices.
Nanoimprint Lithography: Finding its Place in Chip Making
Nanoimprint lithography (NIL) is emerging as a pivotal technology in the realm of semiconductor manufacturing, offering a cost-effective and high-throughput method for patterning nanoscale features. This technique is particularly advantageous for applications requiring large-area patterning, such as advanced photonic devices and high-density data storage.
The process of NIL involves the mechanical deformation of a resist, typically through a stamping action, to create intricate patterns. The key benefits of NIL include its ability to produce high-resolution patterns and its scalability for mass production. However, the technology also faces challenges such as defect management and alignment precision.
- High-resolution patterning capability
- Scalability for mass production
- Cost-effectiveness compared to traditional lithography
- Challenges in defect management
- Alignment precision requirements
Recent advancements in NIL have addressed some of these challenges, leading to increased adoption in the industry. As noted by Nikolay, NIL is finally finding its footing in the semiconductor space, indicating its growing significance and potential for future applications.
Hybrid Bonding: The Future of 3D Chip Integration
Hybrid bonding is rapidly becoming a cornerstone technology for 3D chip integration, offering a pathway to higher performance and functionality in a smaller footprint. This technique enables the stacking of semiconductor wafers or die with fine interconnect pitches, allowing for greater density and shorter interconnect lengths. The main applications for hybrid bonding include CMOS image sensors, memory, and 3D system-on-chip (SoC) designs.
The process of hybrid bonding involves several critical steps:
- Surface preparation to ensure cleanliness and compatibility
- Alignment of the wafers or die to achieve precise positioning
- Bonding at room temperature to initiate the connection
- Annealing to strengthen the bond and enhance electrical conductivity
As the industry moves towards more complex architectures, the role of hybrid bonding will only grow in significance. Manufacturers and researchers are continuously refining the process to overcome challenges such as thermal management and alignment accuracy.
Global Semiconductor Industry Dynamics
The Impact of US-China Trade Tensions on Equipment Supply
The geopolitical landscape has significantly influenced the semiconductor equipment supply chain. The US and its allies’ tightening of semiconductor export restrictions to China has led to a strategic pivot by the latter, markedly increasing its imports of chip manufacturing equipment, particularly from the Netherlands. Within a span of five years, China’s import of lithography machines from the Netherlands has more than doubled, with over 400 units reported.
This surge in equipment import is a direct response to the embargo, reflecting China’s urgency to bolster its domestic semiconductor capabilities. The table below summarizes the recent trends in lithography equipment imports to China:
Year | Lithography Machines Imported |
---|---|
Year 1 | 50 |
Year 2 | 70 |
Year 3 | 90 |
Year 4 | 120 |
Year 5 | 200 |
The implications of these trade tensions are far-reaching, affecting not only the supply and demand dynamics but also the strategic positioning of global semiconductor manufacturing. As countries navigate these challenges, the industry is witnessing a reshaping of alliances and a reevaluation of supply chain resilience.
Europe’s Strategic Position in the Semiconductor Race
Europe’s role in the semiconductor industry is pivotal, yet it faces challenges in scaling its market share. The EU’s share of the global microchips market stands at 10%, trailing behind other major players. This has spurred a series of strategic initiatives aimed at bolstering Europe’s position in the semiconductor race.
Key to these initiatives is the investment in research and development, as well as the establishment of partnerships and alliances. Europe has been actively fostering collaborations between its research institutions and industry giants to accelerate innovation and production capabilities.
The following table outlines some of the recent strategic moves in Europe’s semiconductor sector:
Year | Initiative | Expected Impact |
---|---|---|
2023 | Increased R&D funding | Enhance innovation |
2024 | Expansion of fabrication facilities | Boost production capacity |
2025 | New industry alliances | Strengthen global competitiveness |
These steps are part of a broader effort to secure a more significant foothold in the semiconductor market and to ensure that Europe remains a key player in the technological advancements shaping the future.
How Arizona’s Ecosystem is Shaping the Future of Semiconductors
Arizona is emerging as a significant player in the semiconductor industry, with its ecosystem rapidly evolving to meet the demands of modern chip fabrication. The state’s commitment to fostering a conducive environment for semiconductor growth is evident through its active competition for the CHIPS Act funding, which aims to bolster domestic chip production. These efforts have led to important new initiatives to enhance the state’s semiconductor ecosystem, including new industry-led apprenticeships and workforce development programs.
The choice of Arizona for semiconductor plant construction, despite its arid climate, is a testament to the state’s strategic advantages. Key industry players are drawn to Arizona’s stable regulatory environment, availability of skilled labor, and the presence of leading research institutions. The state’s infrastructure is being tailored to support the high water usage of chip manufacturing, ensuring that the arid landscape does not hinder the industry’s growth.
Arizona’s semiconductor ecosystem is not just about the physical infrastructure; it’s also about the intellectual capital. The state is investing in early STEM education and university-industry partnerships to sustain industry growth and innovation. By nurturing a skilled workforce and fostering cutting-edge research, Arizona is positioning itself as a hub for the future of semiconductor technology.
The Role of Early STEM Education in Sustaining Industry Growth
The semiconductor industry’s future hinges on a skilled workforce capable of driving innovation and meeting the complex demands of chip design and manufacturing. Early STEM education is pivotal in cultivating the next generation of engineers and scientists who will sustain the industry’s growth. Initiatives to integrate technology and engineering concepts into primary and secondary education are essential in sparking interest and developing the necessary skill sets from a young age.
Experts like Liz Allan and Rob Pearson emphasize the importance of early STEM exposure to grow the future chip workforce. Art Scott and Santosh Kurinec advocate for rethinking engineering education in the U.S., suggesting that a revamp of the current curriculum could better prepare students for the challenges of the semiconductor sector. The table below highlights key voices in the industry and their stance on STEM education:
Expert | Focus Area |
---|---|
Liz Allan | Early STEM Education |
Rob Pearson | Future Chip Workforce Development |
Art Scott | Engineering Education Reform |
Santosh Kurinec | Curriculum Revitalization |
By investing in early education and aligning curricula with industry needs, we can ensure a steady pipeline of talent. This is not just a national imperative but a global one, as countries like Vietnam recognize the importance of developing their semiconductor ecosystems through educational partnerships and initiatives.
Market Trends and Demand Forecast
Predicting the Surge in Semiconductor Chip Demand
The semiconductor industry is on the cusp of a significant upswing in chip demand, anticipated to commence in the second quarter of 2024. This resurgence is largely attributed to the burgeoning sectors of AI-driven data centers and the rapidly expanding electric vehicle (EV) market. The anticipated demand surge is expected to catalyze a pivotal transition in the silicon cycle, impacting manufacturers and supply chains globally.
Key drivers of this demand include:
- Advancements in AI technology necessitating more powerful data centers
- The global shift towards electric vehicles requiring advanced semiconductor components
- Increased adoption of smart technologies and IoT devices
Industry analysts have outlined the following forecast for the upcoming quarter:
Sector | Projected Growth |
---|---|
AI Data Centers | 15% increase |
Electric Vehicles | 20% increase |
IoT Devices | 10% increase |
These projections underscore the importance of strategic planning and investment by semiconductor equipment manufacturers to meet the escalating needs of these dynamic sectors.
The Growing Importance of Chiplets in the Automotive Sector
The automotive industry is rapidly embracing the concept of chiplets to meet the increasing demands for performance and functionality in vehicles. Chiplets offer a modular approach to design, allowing manufacturers to combine different semiconductor technologies into a single package. This not only enhances the capabilities of automotive systems but also reduces development time and costs.
Key factors such as standardization, interconnect technologies, and communication protocols are essential for the interoperability of automotive chiplets. Moreover, addressing power and thermal management challenges is crucial for the reliable operation of these complex systems. The table below outlines the core aspects that are driving the adoption of chiplets in the automotive sector:
Aspect | Importance in Automotive Chiplets |
---|---|
Standardization | Ensures compatibility and simplifies integration |
Interconnect Tech | Enables high-speed data transfer between chiplets |
Communication Protocols | Facilitates seamless data exchange |
Power Management | Critical for energy efficiency and safety |
Thermal Management | Maintains system stability and longevity |
As the industry moves towards more advanced driver-assistance systems (ADAS) and autonomous vehicles, the role of chiplets is set to become even more significant. The collaboration between chip manufacturers and automotive companies will be key to developing the next generation of vehicles that are safer, smarter, and more connected.
Memory Technology Innovations: MRAM’s Rising Popularity
The landscape of memory technology is witnessing a significant shift with the rising popularity of Magnetic Random-Access Memory (MRAM). Experts like Jim Handy and Nicolas Dujarrier have noted MRAM’s increasing attention at the smallest nodes, signaling a trend towards more robust and efficient memory solutions. MRAM stands out for its non-volatility, endurance, and speed, making it a strong candidate for applications where these attributes are critical.
Spin-orbit transfer MRAM (SOT-MRAM) is particularly noteworthy for its potential in next-generation memory offerings. Its faster write speeds and durability position SOT-MRAM as a promising technology for future devices. The table below highlights the comparative advantages of SOT-MRAM over traditional memory types:
Memory Type | Write Speed | Endurance | Non-Volatility |
---|---|---|---|
SOT-MRAM | Fast | High | Yes |
DRAM | Moderate | Moderate | No |
NAND Flash | Slow | Low | Yes |
As the industry evolves, the integration of MRAM into mainstream markets is anticipated to grow, driven by its compatibility with existing semiconductor processes and the ongoing miniaturization of chips. This trend is not only reshaping the memory landscape but also opening new avenues for innovation in the semiconductor sector.
The Shift Towards Specialized Processors and Interface IP
The semiconductor industry is witnessing a significant shift towards specialized processors and interface IP, driven by the need for more efficient and tailored computing solutions. Specialized processors are increasingly favored for their ability to optimize performance for specific applications, from AI and machine learning to automotive systems. This trend is complemented by the growth of interface IP, which facilitates communication between various chip components, enhancing overall system integration and performance.
The market for semiconductor intellectual property (IP) is expanding rapidly. According to recent projections, the semiconductor IP market value is expected to reach USD 11.2 billion by 2029, growing from USD 7.5 billion in 2024. This growth is indicative of the rising demand for customizable and scalable chip designs that can cater to a wide range of emerging technologies.
As the industry evolves, companies are investing in the development of advanced interface IPs, such as those for high-speed data transfer and power management. These innovations are crucial for supporting the complex requirements of next-generation electronics. The table below highlights some of the key areas of focus within the specialized processor and interface IP landscape:
Area of Focus | Description |
---|---|
AI and Machine Learning | Processors optimized for high-speed data analysis and pattern recognition. |
Automotive Systems | Robust processors and IPs designed for vehicle safety and automation. |
High-Speed Data Transfer | Interface IPs enabling faster communication between chip components. |
Power Management | IPs that improve energy efficiency and battery life in portable devices. |
The shift towards specialized processors and interface IP is not only transforming the semiconductor industry but also shaping the future of technology as a whole. As companies continue to innovate, we can expect to see even more sophisticated and purpose-built solutions emerge.
Challenges and Opportunities in Semiconductor Manufacturing
Addressing the ABF Substrate Shortage
The semiconductor industry is currently grappling with a shortage of Ajinomoto Build-up Film (ABF) substrates, which are critical for the packaging of high-performance chips. The scarcity is primarily due to the surge in demand for advanced chips and the limited number of suppliers capable of producing ABF substrates at scale.
Efforts to mitigate the shortage have included diversifying the supply chain and investing in alternative technologies. Companies are exploring the following strategies:
- Expanding production capacity of existing ABF substrate manufacturers.
- Qualifying additional suppliers to reduce dependency on a single source.
- Accelerating the development of next-generation substrate materials that could potentially replace ABF.
The industry is also seeing collaborations between chipmakers and substrate providers to ensure a stable supply. Project Manager Thomas Stoppe highlights the importance of customer-specific solutions and the continuous development of technology to meet industrial partner needs. This proactive approach is essential for maintaining the momentum of semiconductor innovation and meeting the growing market demands.
Security Considerations in Chip Design
In the ever-evolving landscape of semiconductor manufacturing, security has become a cornerstone of chip design. The integration of security measures is no longer an afterthought but a fundamental aspect of the design process. This shift is driven by the increasing sophistication of cyber threats and the critical role that semiconductors play in modern technology.
Effective collaboration among security, design, and verification teams is crucial to ensuring a ‘secure by design‘ approach. This multidisciplinary effort aims to embed security features early in the design phase, reducing vulnerabilities and mitigating risks associated with chip exploitation. The table below outlines key areas of focus for security in chip design:
Area of Focus | Description |
---|---|
Secure Boot | Ensures that only trusted software is executed during the startup process. |
Hardware Root of Trust | Provides a foundation for secure operations and key storage. |
Cryptographic Functions | Enables secure data encryption and authentication. |
Side-channel Attack Protection | Guards against attacks that exploit information leakage from physical implementations. |
As the industry moves forward, the importance of a ‘secure by design’ philosophy is underscored by the growing complexity of semiconductor devices and the diverse applications they serve. The challenge lies in balancing security with performance, cost, and time-to-market pressures. However, the stakes are high, and the industry must rise to meet them to protect the integrity of the digital infrastructure.
The Increasing Complexity of Thermal Integrity Management
As semiconductor devices continue to scale down in size, managing heat dissipation has become a critical challenge. Material choices are critical to thermal management in advanced packaging, where heterogeneous integration brings together components with varying coefficients of thermal expansion (CTE). When these components heat up, the differences in CTE can lead to mechanical stress and potential failure of the device.
To address these challenges, engineers are exploring a variety of solutions:
- Selection of materials with compatible CTE values
- Innovative cooling techniques, such as liquid cooling and heat pipes
- Enhanced thermal interface materials (TIMs) to improve heat conduction
- Advanced packaging designs that incorporate thermal considerations from the outset
These strategies are essential for maintaining device reliability and performance as the industry moves towards more complex chip architectures, such as those involving 3D stacking and chiplets.
Silicon Carbide’s Role in Power Semiconductor Advancements
Silicon carbide (SiC) is emerging as a pivotal material in the power semiconductor industry, particularly for applications requiring high efficiency and thermal stability. SiC’s wide bandgap properties enable devices to operate at higher voltages, frequencies, and temperatures than traditional silicon-based components. This translates into significant energy savings and reduced cooling requirements, which is crucial for tackling the climate crisis by enhancing energy efficiency.
The adoption of SiC technology is accelerating, driven by its superior performance in electric vehicles (EVs), renewable energy systems, and power supplies. Below is a comparison of key attributes between silicon carbide and gallium nitride (GaN), another wide-bandgap semiconductor:
Property | Silicon Carbide (SiC) | Gallium Nitride (GaN) |
---|---|---|
Bandgap | ~3.3 eV | ~3.4 eV |
Thermal Conductivity | ~5 W/(cm·K) | ~1.3 W/(cm·K) |
Electric Field Strength | ~3 MV/cm | ~3.3 MV/cm |
Maximum Operating Temperature | >600°C | ~300°C |
As the industry continues to innovate, the role of SiC in power semiconductors is expected to expand, offering opportunities for manufacturers to develop more efficient and compact devices. The challenge lies in reducing manufacturing costs and improving the quality of SiC wafers to fully leverage these advantages.
Conclusion
As we have explored the intricate landscape of semiconductor equipment manufacturers, it’s clear that their role is pivotal in the ever-evolving microchip industry. From the precision required in silicon wafer manufacturing to the complexities of power management and chip design, these companies are at the forefront of innovation. The recent surge in chip demand and the strategic moves by industry giants like Asahi Kasei, Infineon, and Texas Instruments highlight the competitive nature of this sector. Moreover, the push towards smaller chip sizes and the establishment of robust semiconductor ecosystems, such as Arizona’s, underscore the dynamic progress and the collaborative efforts needed to meet the technological challenges ahead. The insights from industry experts and the focus on topics like hybrid bonding, chiplets, and advanced packaging technologies reveal a future where semiconductor equipment manufacturers will continue to shape the capabilities and efficiencies of electronic devices worldwide.
Frequently Asked Questions
Who are the top players in semiconductor equipment manufacturing?
The top players in the semiconductor equipment manufacturing industry include Applied Materials, Lam Research, ASML, and Tokyo Electron, each known for their innovation and specialized technologies.
What recent technological advancements have been made in chip fabrication?
Recent advancements include the evolution of silicon wafer manufacturing, breakthroughs in power management integrated circuits, the emergence of nanoimprint lithography, and the development of hybrid bonding for 3D chip integration.
How are global semiconductor industry dynamics being affected by geopolitical factors?
Geopolitical factors like US-China trade tensions are impacting the supply of equipment, while regions like Europe and Arizona are strategically positioning themselves in the semiconductor race, influenced by early STEM education and local ecosystems.
What are the market trends and demand forecasts for semiconductor chips?
Market trends indicate a surge in semiconductor chip demand, particularly in the automotive sector with chiplets and memory technology innovations like MRAM, as well as a shift towards specialized processors and interface IP.
What challenges and opportunities exist in semiconductor manufacturing?
The semiconductor industry faces challenges such as the ABF substrate shortage and thermal integrity management, but also opportunities with the rising role of silicon carbide in power semiconductors and security considerations in chip design.
How is the Arizona semiconductor ecosystem shaping the industry’s future?
Arizona’s semiconductor ecosystem is becoming a hub for innovation, with a focus on shrinking chip sizes and enhancing processing capabilities, and driving the development of robust semiconductor ecosystems.