Understanding Silicon Wafer Sizes: A Detailed Overview
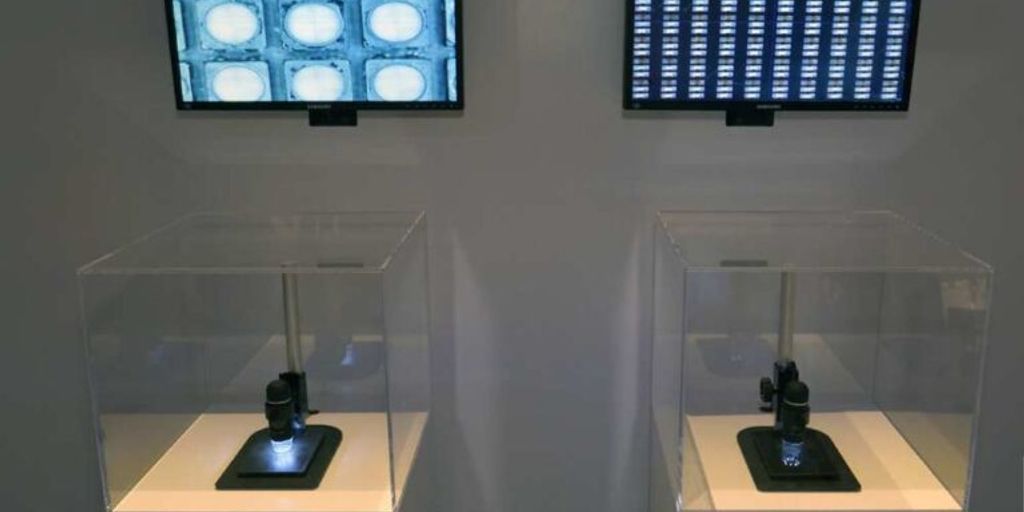
Silicon wafers are the foundational material for the semiconductor industry, serving as the substrate for integrated circuits and various microdevices. Over the years, the size of silicon wafers has evolved significantly, driven by technological advancements and the need for higher productivity and efficiency. This article delves into the history, standard sizes, manufacturing processes, performance impacts, challenges, and future prospects of silicon wafer sizes.
Key Takeaways
- Silicon wafers have expanded in size over the decades, from 1 inch to the current state-of-the-art 300 mm, with future projections aiming for 450 mm.
- Larger wafer sizes offer higher productivity and efficiency, making them more economically viable for semiconductor manufacturing.
- Different wafer sizes are used for various applications, ranging from small-scale devices to large, high-performance integrated circuits.
- The manufacturing process of silicon wafers involves crystal growth, slicing, polishing, and stringent quality control measures to ensure optimal performance.
- Future trends in silicon wafer sizes are influenced by ongoing research, potential new materials, and market demand, with a strong focus on larger diameters.
The Evolution of Silicon Wafer Sizes
Historical Milestones in Wafer Size
The history of semiconductors is closely tied to the historical trend of the size of the silicon wafer. In the early 1960s, monocrystalline silicon wafers of 0.75 inch (about 20 mm) in diameter became available. Around 1965, 1.25-inch (30 mm) wafers were replaced by 1.5-inch (40 mm) wafers due to increased demand. The trend continued with the introduction of 2-inch (50 mm) and 3-inch (75 mm) wafers, followed by 4-inch (100 mm) wafers around 1975. Successive introductions of 5-inch (125 mm), 6-inch (150 mm), and 8-inch (200 mm) wafers marked the industry’s progress. The 21st century has brought us to the 300 mm age, and that’s where we are right now.
Technological Advancements Driving Size Increase
Technological advancements have been a key driver in the increase of wafer sizes. Larger wafers allow for higher productivity and efficiency, which is why the standard silicon wafer size is now 300 mm. Semiconductor fabrication plants, or fabs, are defined by the diameter of wafers they produce. The diameter has gradually increased to improve throughput and reduce cost. Currently, there is a proposal to adopt 450 mm wafers, with companies like Intel, TSMC, and Samsung conducting research on 450 mm prototypes.
Future Trends in Wafer Dimensions
The future of silicon wafer sizes looks promising with ongoing research and development. The industry is exploring the potential of adopting 450 mm wafers to further enhance productivity and reduce costs. As technology continues to advance, we can expect to see even larger wafer sizes becoming the norm in semiconductor fabrication plants.
Standard Silicon Wafer Sizes and Their Applications
Common Wafer Sizes in the Industry
Silicon wafers come in various sizes, each serving different purposes in the semiconductor industry. The standard silicon wafer size is 300mm, although the trend is growing in favor of larger sizes. This is mostly due to the higher productivity and efficiency that a larger wafer size can provide. Here are some common wafer sizes:
- 2 Inch Silicon Wafer
- 3 Inch Silicon Wafer
- 4 Inch Silicon Wafer
- 5 Inch Silicon Wafer
- 6 Inch Silicon Wafers
- 12 Inch Silicon Wafers
Applications of Different Wafer Sizes
Different wafer sizes are used for various applications, depending on the requirements of the semiconductor devices being manufactured. For instance, smaller wafers like the 2-inch and 3-inch sizes are often used in research and development, while larger wafers such as the 300mm and 450mm are used in mass production due to their higher yield and efficiency.
Advantages of Larger Wafer Sizes
Larger wafer sizes offer several advantages, including higher productivity and lower cost per unit area. This is because more chips can be produced from a single wafer, reducing the overall manufacturing cost. Additionally, larger wafers can improve the performance and reliability of semiconductor devices.
Wafer Size | Common Applications |
---|---|
2 Inch | Research & Development |
3 Inch | Research & Development |
4 Inch | Small-scale Production |
5 Inch | Small-scale Production |
6 Inch | Medium-scale Production |
12 Inch | Mass Production |
300mm | Mass Production |
450mm | Mass Production |
Manufacturing Processes for Various Wafer Sizes
Crystal Growth and Wafer Slicing
The manufacturing process begins with the growth of a silicon crystal, known as a boule. The boule is then sliced with a wafer saw, which is a type of wire saw. This slicing process is crucial as it determines the initial thickness and flatness of the wafers. Chemical etching is used to remove any crystal damage from the machining steps. The wafers are then polished to achieve the desired smoothness and flatness.
Polishing and Cleaning Techniques
Polishing is a multi-step process that involves both mechanical and chemical methods to achieve a mirror-like surface. This is essential for the subsequent photolithography steps in semiconductor manufacturing. Cleaning techniques often involve the use of ultra-pure water and various chemical solutions to remove any contaminants. The goal is to ensure that the wafer surface is as clean as possible to avoid defects in the final semiconductor devices.
Quality Control Measures
Quality control is an integral part of the manufacturing process. It involves various inspection and testing methods to ensure that the wafers meet the required specifications. Common quality control measures include:
- Visual Inspection: To check for any surface defects or irregularities.
- Dimensional Measurement: To ensure the wafers are of the correct size and thickness.
- Electrical Testing: To verify the electrical properties of the wafers.
These steps are crucial for maintaining the high standards required in semiconductor manufacturing.
Impact of Wafer Size on Semiconductor Performance
Die Yield and Wafer Size
The size of a silicon wafer is one of the most important parameters in semiconductor manufacturing. It determines how many dies can be fabricated on the wafer, the cost of the dies, and the overall cost of the finished ICs. Higher chip density per wafer means more IC production in a single manufacturing run. However, larger wafer sizes are prone to defects such as contamination and warpage, making careful process optimization crucial for improved yield and production efficiency.
Cost Implications of Larger Wafers
A unit of wafer fabrication step, such as an etch step, can produce more chips proportional to the increase in wafer area, while the cost of the unit fabrication step goes up more slowly than the wafer area. This was the cost basis for increasing wafer size. Conversion to 300 mm wafers from 200 mm wafers began in early 2000, reducing the price per die by about 30–40%. Larger diameter wafers allow for more die per wafer, thus lowering the cost per chip.
Performance Benefits of Different Sizes
Larger surface area on wafers allows for more IC production, improving manufacturing throughput. Despite the advantages, larger wafer sizes are prone to defects such as contamination and warpage. Careful process optimization is important for leveraging the utmost benefits of the wafer size in use for improved yield and production efficiency.
Challenges in Scaling Up Wafer Sizes
Scaling up silicon wafer sizes presents several significant challenges that manufacturers must overcome to meet the escalating demand for larger wafers. These challenges span technical, economic, and environmental domains, each posing unique obstacles.
Future Prospects of Silicon Wafer Sizes
Research and Development in Wafer Technology
Research and development in silicon wafer technology are pivotal for the future of the semiconductor industry. Continuous innovation is essential to meet the growing demand for smaller, faster, and more efficient chips. Key areas of focus include improving wafer quality, reducing defects, and enhancing manufacturing processes.
Potential for New Materials
While silicon remains the dominant material for wafers, there is ongoing research into alternative materials that could offer superior performance. Materials such as silicon carbide (SiC) and gallium nitride (GaN) are being explored for their potential to handle higher voltages and temperatures, which could be beneficial for specific applications like electric vehicles and high-frequency devices.
Market Demand and Industry Adoption
The market demand for larger silicon wafers is expected to grow significantly. Projections indicate that the total silicon wafer market could reach nearly $17 billion by 2027. This growth is driven by the transition from 200mm to 300mm wafers and the potential future adoption of 450mm wafers. The industry is investing heavily in larger wafers and new fabrication plants to meet this demand.
Wafer Size | Current Status | Future Prospects |
---|---|---|
200mm | Phasing out | Limited use |
300mm | Mainstream | Continued growth |
450mm | In development | Potential future adoption |
Conclusion
In summary, the evolution of silicon wafer sizes has been a critical factor in the advancement of semiconductor technology. From the early days of small wafers to the current standard of 300mm, and the anticipated shift to 450mm, each increase in wafer size has brought about significant improvements in productivity, efficiency, and cost-effectiveness. Understanding the various sizes and their implications helps in appreciating the complexities and innovations within the semiconductor industry. As technology continues to advance, the trend towards larger wafer sizes is expected to persist, driving further progress and enabling the development of more sophisticated and powerful electronic devices.
Frequently Asked Questions
What are the standard sizes of silicon wafers?
Silicon wafers come in various standard sizes, including 25.4mm (1 inch), 50.8mm (2 inches), 76.2mm (3 inches), 100mm (4 inches), 125mm (5 inches), 150mm (6 inches), 200mm (8 inches), 300mm (12 inches), and 450mm (18 inches).
Why are larger silicon wafers preferred in the industry?
Larger silicon wafers are preferred because they can accommodate more dies per wafer, improving throughput and reducing the cost per die. This leads to higher productivity and efficiency in semiconductor manufacturing.
What are the historical milestones in the evolution of silicon wafer sizes?
The evolution of silicon wafer sizes has seen several milestones, including the introduction of 2-inch wafers in the 1960s, 4-inch wafers in the 1970s, 6-inch wafers in the 1980s, 8-inch wafers in the 1990s, and the current standard of 12-inch wafers. The industry is now exploring the feasibility of 18-inch wafers.
What are the main applications of different silicon wafer sizes?
Different silicon wafer sizes are used for various applications. Smaller wafers (1-4 inches) are typically used for research and development, MEMS, and niche applications. Larger wafers (6-12 inches) are used in mass production of integrated circuits and semiconductor devices. The largest wafers (18 inches) are being researched for future high-volume manufacturing.
What are the challenges in manufacturing larger silicon wafers?
Manufacturing larger silicon wafers presents several challenges, including increased complexity in crystal growth, difficulties in handling and processing larger wafers, higher costs for equipment and materials, and maintaining quality control to ensure defect-free wafers.
How does wafer size impact semiconductor performance?
Wafer size impacts semiconductor performance in several ways. Larger wafers can improve die yield and reduce production costs, but they also require advanced manufacturing techniques to ensure high quality. Additionally, larger wafers can enable the production of more powerful and efficient semiconductor devices.