Understanding Silicon Wafers: From Production to Application
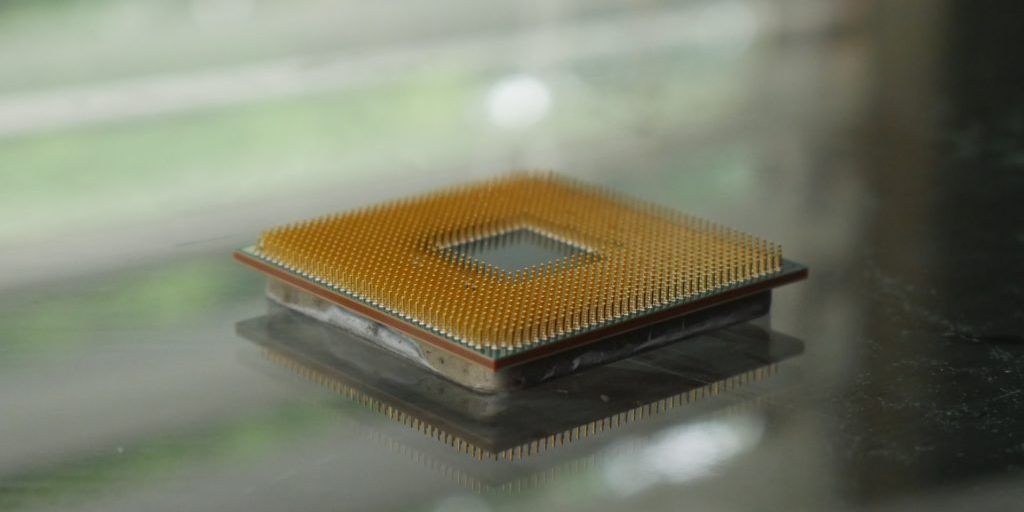
Silicon wafers are pivotal in the realm of technology, serving as the bedrock for myriad applications from integrated circuits to solar cells. Their unique electrical and thermal properties, coupled with high purity, make them indispensable in the semiconductor industry. Understanding the production, properties, and applications of silicon wafers provides insight into their critical role and the challenges faced in their manufacture.
Key Takeaways
- Silicon wafers are essential for the production of integrated circuits and semiconductor devices due to their unique electrical and thermal properties.
- The production of silicon wafers involves complex processes such as the Czochralski pulling method and precise slicing and polishing techniques.
- High purity and specific electrical properties are crucial in silicon wafers to prevent operational failures in electronic components.
- Silicon wafers are used in a variety of applications, including semiconductor devices, solar cells, and other electronic components.
- Innovations and advancements in silicon wafer manufacturing continue to enhance their efficiency and sustainability in the semiconductor industry.
The Basics of Silicon Wafer Production
Key Processes and Equipment
Silicon wafer production is a crucial part of the semiconductor industry, serving as the foundation for integrated circuits. The process involves slicing the silicon crystal into precise, thin discs, ensuring each wafer has the correct orientation for optimal electronic functionality. Key equipment includes diamond saws for cutting and polishing machines to create a smooth surface.
Types of Silicon Wafers
Silicon wafers are categorized based on their diameter, type of crystal structure, and doping materials used. Common diameters range from 100mm to 450mm. The two main types of crystal structures are monocrystalline and polycrystalline, each suited for different applications.
Challenges in Production
Despite the high demand, silicon wafer production faces several challenges such as maintaining high purity and managing production costs. Minor impurities or variations in electrical properties can lead to operational failures, emphasizing the need for stringent quality control.
Silicon Wafer Properties and Specifications
Electrical and Thermal Characteristics
Silicon wafers are renowned for their electrical conductivity, which is crucial for semiconductor applications. The ability to control this property through doping makes silicon wafers versatile in various electronic applications. Additionally, their thermal conductivity is essential for managing heat in electronic devices, ensuring performance and longevity.
Purity and Quality Control
High purity and stringent quality control are paramount in silicon wafer production. Factors such as defect densities and uniformity are critical, with prime grade SiC wafers standing out for their exceptional performance. Regular testing and monitoring are integral to maintaining these standards.
Influence on Semiconductor Performance
The properties of silicon wafers directly influence the performance and reliability of semiconductor devices. Variations in properties like resistivity can determine the suitability of wafers for different types of devices, such as power devices or memory devices. Understanding these influences is crucial for optimizing device design and functionality.
Applications of Silicon Wafers in Technology
Semiconductor Devices
Silicon wafers form the backbone of semiconductor devices, which are pivotal in numerous modern technologies. These devices include transistors, diodes, and integrated circuits, all of which are essential for the operation of electronic devices ranging from smartphones to advanced medical equipment.
Solar Cells
The role of silicon wafers in solar energy is significant, as they are primarily used in the production of photovoltaic cells. These cells convert sunlight into electricity, playing a crucial role in renewable energy solutions. The efficiency and cost-effectiveness of solar cells are directly influenced by the quality of the silicon wafers used.
Other Electronic Components
Silicon wafers are also utilized in a variety of other electronic components. Their high thermal conductivity and low coefficient of thermal expansion make them ideal for applications requiring robust, reliable materials. Examples include high-performance radio frequency (RF) applications and sensors in automotive and aerospace industries.
Advanced Fabrication Techniques
Photolithography and Etching
Photolithography and etching are critical steps in the microfabrication of silicon wafers. Photolithography transfers circuit patterns onto wafers, while etching removes layers to create the circuitry. This process involves multiple steps:
- Surface preparation
- Photoresist application
- Exposure to light
- Development and etching
Doping Methods
Doping is essential for modifying the electrical properties of silicon wafers. It involves introducing impurities into the silicon to change its conductivity. The most common dopants are boron and phosphorus, which are introduced through processes such as ion implantation or diffusion.
Wafer Thinning
Wafer thinning is necessary for many modern applications, especially in devices requiring thin, lightweight, and high-performance wafers. Techniques include mechanical grinding and chemical-mechanical planarization (CMP), which ensure the wafers are thinned uniformly to meet precise specifications.
Silicon Wafers in the Semiconductor Industry
Role in Integrated Circuits
Silicon wafers are indispensable in the production of integrated circuits (ICs), serving as the primary substrate where various electronic components are embedded. The role of silicon wafers in ICs is pivotal due to their excellent semiconductor properties, which allow for the miniaturization and integration of complex circuits. Silicon is commonly used in wafer and chip production due to its ability to withstand high temperatures and its abundance in the earth’s crust.
MEMS Integration
Micro-Electro-Mechanical Systems (MEMS) utilize silicon wafers for their structural base. These systems combine mechanical and electrical components that are microfabricated on the silicon substrate. MEMS are integral in various applications, including sensors, actuators, and microfluidic devices, highlighting the versatility of silicon wafers in modern technology.
Impact on Device Efficiency
The efficiency of electronic devices heavily relies on the quality of silicon wafers used. High-purity and defect-free wafers lead to better performance and longer device lifespans. Innovations in wafer manufacturing, such as improved doping techniques and precision cutting, have significantly enhanced the efficiency of electronic devices, making silicon wafers a critical factor in the advancement of the semiconductor industry.
Innovations in Silicon Wafer Manufacturing
Emerging Technologies
Technological advancements are pivotal in enhancing the efficiency and capabilities of silicon wafers. The shift towards using 450mm wafers, for instance, significantly increases production capacity, allowing manufacturers to meet the escalating demand for electronic devices.
Sustainability Practices
The manufacturing of silicon wafers is not only complex but also resource-intensive. Innovations in sustainability practices focus on reducing the environmental impact through process optimization, silicon recycling, and the exploration of alternative materials.
Cost-Effective Solutions
Addressing the high costs associated with silicon wafer production is crucial. Innovations here include the development of new manufacturing techniques and materials that aim to lower energy consumption and reduce overall production costs, thereby making the process more economically viable.
Future Trends in Silicon Wafer Usage
Demand Projections
The demand for silicon wafers is projected to grow significantly, driven by the expansion of sectors like IoT, AI, and renewable energy. Worldwide silicon wafer shipments decreased 5.4% in the first quarter of 2024, indicating a temporary dip but an expected rebound due to technological advancements and increased demand in various electronic sectors.
Technological Advancements
Advancements in silicon wafer technology are crucial for meeting the increasing demands of the semiconductor industry. The transition to larger wafer sizes, such as the 450mm, could increase production capacity by up to 2.5 times, making it a pivotal development in the industry.
Potential New Applications
New applications for silicon wafers are emerging as technology evolves. These include uses in advanced medical devices, flexible electronics, and more efficient solar cells. The versatility and ongoing development of silicon wafer technology suggest a broadening of applications beyond traditional electronics.
Conclusion
In summary, silicon wafers are indispensable to the technology industry, serving as the backbone for a myriad of applications ranging from integrated circuits to solar cells. Their unique electrical and thermal properties, coupled with high purity, make them essential for the production of semiconductor devices. Despite the complexities and challenges involved in their production, continuous advancements ensure their availability and efficiency. Understanding the intricacies of silicon wafer production and application not only highlights their importance but also underscores the ongoing innovation within the semiconductor industry. This knowledge is crucial for anyone involved in or interested in the fields of electronics and technology.
Frequently Asked Questions
What are silicon wafers?
Silicon wafers are thin slices of silicon that serve as the substrate for the fabrication of electronic devices. They are produced from ultra-pure silicon through a series of complex processes, including the Czochralski process, wafer slicing, and polishing.
Why are silicon wafers used in the technology industry?
Silicon wafers are used in the technology industry due to their unique combination of electrical and thermal properties, making them ideal for the fabrication of semiconductor devices, solar cells, and other electronic components.
What are the key processes involved in silicon wafer production?
The key processes in silicon wafer production include the Czochralski pulling method for crystal growth, slicing the crystal into wafers using a diamond saw, and polishing the wafers to create a smooth surface.
How do impurities affect silicon wafer performance?
Even minor impurities or variations in silicon wafers can lead to operational failures in electronic devices, as they can significantly alter the electrical properties of the wafers, which are crucial for their functionality.
What advancements are being made in silicon wafer manufacturing?
Advancements in silicon wafer manufacturing include the development of new fabrication techniques like wafer thinning and MEMS integration, as well as improvements in sustainability practices and cost-effective solutions.
What future trends are expected in silicon wafer usage?
Future trends in silicon wafer usage include increased demand due to the growth of high-tech electronics, technological advancements in fabrication methods, and the exploration of new applications in various industries.