Understanding the Complexities of Wafer Production in Modern Technology
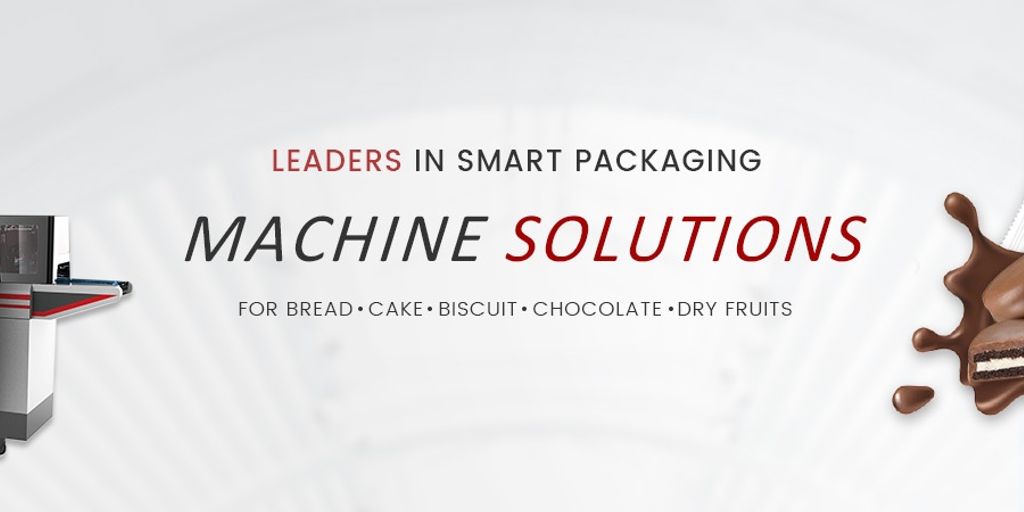
Silicon wafer production is a vital part of making the tiny chips that power our devices. From smartphones to computers, these chips are everywhere. The process of making these wafers is complex and requires a lot of care and precision. Each step, from extracting silicon to making sure the wafers are clean, is crucial. Understanding this process helps us appreciate the technology that runs our world.
Key Takeaways
- Silicon wafers are the foundation for most electronic devices, making their production essential.
- The process requires hyperpure silicon, which undergoes several steps to become usable wafers.
- Techniques like photolithography and etching are used to create the intricate patterns on wafers.
- Maintaining wafer quality involves addressing issues like contamination and uniformity.
- Sustainability in wafer production focuses on reducing energy and water use and recycling materials.
The Role of Silicon in Wafer Production
Silicon wafer production is a crucial part of the semiconductor industry since it is the foundation upon which integrated circuits (ICs) are built. As the demand for high-tech electronics continues to grow, the production of silicon wafers, which are used to manufacture ICs, increases. This section delves into the nitty-gritty of silicon wafer production by discussing the processes involved, the equipment used, and the different types of wafers available in the market. Through a thorough understanding of silicon wafer production, one can appreciate the complexities of the semiconductor industry and the factors that influence its growth and development.
Key Processes in Wafer Manufacturing
Material Deposition Techniques
Material deposition is the first step in wafer manufacturing. Various materials are layered onto the wafer’s surface. This step is crucial for defining the wafer’s properties. Techniques like chemical vapor deposition (CVD) and physical vapor deposition (PVD) are commonly used. Each method has its own advantages and is chosen based on the specific requirements of the wafer.
Photolithography and Patterning
Photolithography is used to create intricate patterns on the wafer. This process involves coating the wafer with a light-sensitive material called photoresist. A mask with the desired pattern is then placed over the wafer, and ultraviolet light is shined through it. The exposed areas of the photoresist are then developed, revealing the pattern. This step is essential for defining the circuitry of the semiconductor devices.
Etching and Cleaning Procedures
After patterning, the wafer undergoes etching to remove unwanted material. There are two main types of etching: wet etching and dry etching. Wet etching uses liquid chemicals, while dry etching uses gases. Both methods have their own benefits and are selected based on the material and desired outcome. Cleaning procedures are also critical to remove any contaminants and ensure the wafer’s quality. Maintaining cleanliness is vital to prevent defects and ensure high performance.
Types of Wafers and Their Applications
Monocrystalline vs. Polycrystalline Wafers
Monocrystalline wafers are made from a single, continuous crystal structure, making them ideal for high-performance applications. These wafers are essential for producing highly integrated components. On the other hand, polycrystalline wafers consist of multiple small crystals and are generally used in less demanding applications. The choice between these two types depends on the specific needs of the technology being developed.
Specialty Wafers for Advanced Technologies
Specialty wafers, such as epitaxial wafers, offer a superior basis for highly integrated components. These wafers undergo a rigorous process to achieve an extremely flat and smooth surface, which is crucial for the subsequent layers of materials that will be added during the chip fabrication process. Other types of wafer materials include gallium arsenide, silicon carbide, and gallium nitride. The choice of wafer material depends on the specific requirements of the application.
Market Trends and Demand
The market for wafers is continually evolving, driven by advancements in technology and increasing demand for more powerful and efficient semiconductor devices. Polished wafers, known for their perfect surfaces, are widely used in various applications. Epitaxial wafers are also in high demand due to their superior characteristics. As technology advances, the need for specialized wafers will continue to grow, influencing market trends and demand.
Challenges in Maintaining Wafer Quality
Uniformity and Consistency Issues
Process engineers face many difficulties when processing silicon wafers, including maintaining uniformity across wafers. Ensuring uniform deposition or etching across a wafer is paramount. Non-uniformities could lead to device malfunction or decreased efficiency. Any misstep can result in yield losses that render wafers useless for device manufacturing. These complexities require precise controls, stringent safety protocols, and consistent maintenance.
Contamination Control
The semiconductor industry uses various chemicals with specific properties and reactions. Engineers must manage these reactions effectively to reach desired outcomes without introducing contaminants. Adhering to industry standards and rigorous quality testing is more than a habit; it is a commitment to perfection. As silicon wafers continue to constitute the foundation of modern electronics, quality standards become increasingly important.
Yield Loss and Its Implications
Identifying and correcting faults early in the production process is important for both quality and efficiency. Quality testing reduces the manufacture of faulty wafers, lowering material waste and production costs. The consequences of these excursions can be severe, creating defective chips that fail to meet the required specifications. Thus, they impact customer satisfaction and trust. Meeting or exceeding quality standards demonstrates a manufacturer’s dedication to excellence.
Sustainability in Wafer Production
Energy and Water Efficiency
The increasing demands on wafers necessitate that they not only meet physical and chemical requirements but also contribute to more efficient chip production. By enabling the production of more chips per wafer, they help reduce the energy and water requirements of the manufacturing process, reflecting the industry’s push towards sustainability.
Recycling and Waste Management
Environmental concerns: The production of silicon wafers is an energy-intensive process that requires significant amounts of water and electricity. This has raised environmental concerns, and semiconductor manufacturers are looking for ways to reduce their carbon footprint. For instance, some companies are investing in renewable energy sources such as solar and wind power.
Sustainable Materials and Practices
The semiconductor industry is not just about meeting the increasing physical and chemical requirements of wafers; it’s also about leveraging these advancements to produce more chips per wafer, thereby reducing energy and water consumption for customers. This focus on sustainability is part of the broader ‘three S’s‘ strategy that includes sustainability, supply, and scalability, which are crucial for attracting investment and reaching a broader market.
Advanced Equipment for Wafer Processing
Precision Tools and Machinery
In wafer production, precision tools and machinery are essential. These tools ensure that each wafer meets strict quality standards. High-precision equipment like etchers and deposition systems are used to create intricate patterns on the wafers. This equipment must be regularly maintained to ensure optimal performance.
Automation in Wafer Production
Automation has revolutionized wafer production. Automated systems can handle wafers with minimal human intervention, reducing the risk of contamination and increasing efficiency. Modutek provides an extensive range of wafer fabrication equipment, which includes manual, semi-automated, and fully automated wet bench stations. This automation helps in maintaining consistency and quality across batches.
Innovations in Equipment Design
Innovations in equipment design continue to push the boundaries of what is possible in wafer production. New designs focus on improving efficiency and reducing waste. For example, advanced wet bench systems are designed to use less water and chemicals, making the process more sustainable. These innovations are crucial for meeting the growing demands of the semiconductor industry.
Future Trends in Wafer Production
Miniaturization and Its Demands
The trend towards smaller and more powerful devices continues to drive the need for miniaturization in wafer production. As components shrink, the precision required in manufacturing increases, making advanced equipment and techniques essential. This push for smaller sizes also means that wafers must meet stricter physical and chemical standards to ensure they perform reliably in high-demand applications.
Emerging Materials and Technologies
New materials and technologies are constantly being explored to improve wafer performance and production efficiency. For instance, the use of 450mm wafers is expected to boost production capacity significantly, allowing manufacturers to meet the growing demand for electronic devices. These advancements not only enhance the capabilities of semiconductors but also contribute to more sustainable manufacturing processes by reducing energy and water usage.
Impact of Industry 4.0 on Wafer Manufacturing
Industry 4.0 technologies, such as automation and data analytics, are revolutionizing wafer production. By integrating smart machinery and real-time monitoring systems, manufacturers can achieve higher precision and efficiency. This shift towards more resilient wafer fabrication is expected to increase fab capacity significantly over the next decade, helping to meet the ever-growing demand for advanced electronic devices.
Conclusion
In conclusion, the production of silicon wafers is a complex and essential part of the semiconductor industry. Each step, from the creation of hyperpure silicon to the precise processes of photolithography and material deposition, requires meticulous control and innovation. As technology advances, the demand for more efficient and powerful chips continues to grow, pushing the boundaries of what is possible in wafer production. Understanding these complexities helps us appreciate the intricate dance of technology that powers our modern world. By meeting stringent requirements and embracing sustainability, the industry continues to evolve, ensuring that the devices we rely on become even more efficient and powerful.
Frequently Asked Questions
What is a silicon wafer?
A silicon wafer is a thin slice of silicon that serves as the base for building electronic circuits. It’s essential in making chips for computers and other devices.
Why is hyperpure silicon important in wafer production?
Hyperpure silicon is crucial because any impurities can affect the performance of the semiconductor. Purity ensures that the electronic devices work efficiently.
How are silicon wafers made?
Silicon wafers are made by extracting silicon from sand, purifying it, and then slicing it into thin wafers. These wafers are then polished to be smooth and clean.
What are the main steps in wafer manufacturing?
The main steps include material deposition, photolithography, etching, and cleaning. Each step must be carefully controlled to ensure high-quality wafers.
What are the different types of silicon wafers?
There are monocrystalline and polycrystalline wafers. Monocrystalline wafers are made from a single crystal and are used for high-performance devices, while polycrystalline wafers are made from multiple crystals and are generally less expensive.
Why is wafer quality important?
Wafer quality is vital because any defects can lead to malfunctioning electronic devices. High-quality wafers ensure that the final products are reliable and efficient.