Understanding the Impact of Wafer Size on Semiconductor Performance
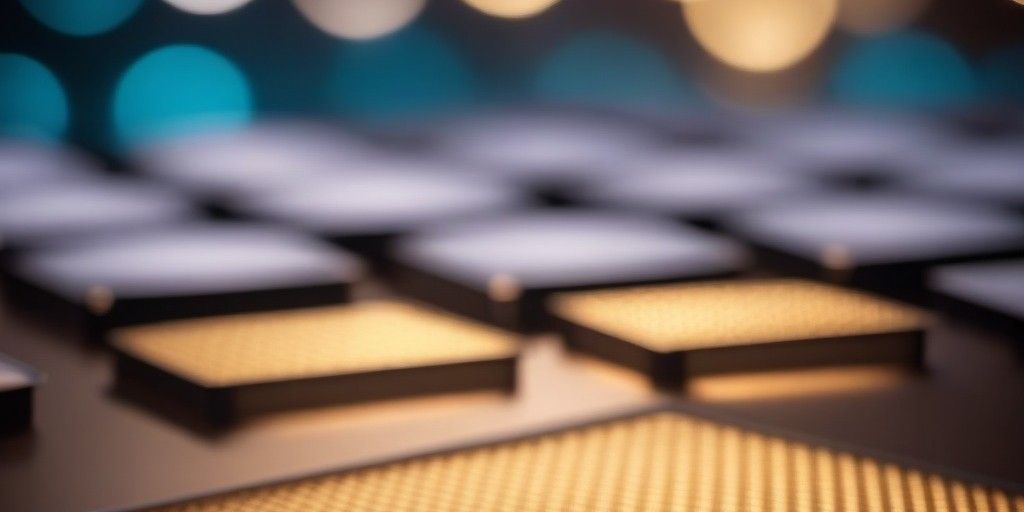
In the world of semiconductors, wafer size plays a huge role in how well and how efficiently devices work. From the early days of tiny wafers to today’s larger sizes, the industry has seen big changes. This article dives into how wafer size affects the performance of semiconductors and what it means for the future.
Key Takeaways
- Larger wafer sizes help make more devices from a single wafer, improving efficiency and productivity.
- The shift from small to larger wafers has required major technological advancements and investments.
- Bigger wafers can lower costs but need high initial investments for upgrades.
- Wafer size impacts many factors, including electrical characteristics, thermal management, and reliability.
- Future trends suggest even larger wafers, but they come with their own set of challenges and opportunities.
The Evolution of Wafer Sizes in the Semiconductor Industry
Historical Progression of Wafer Sizes
The historical trend of the size of the silicon wafer has seen a remarkable journey. Initially, silicon wafers were available in sizes as small as 25.4 mm (1 inch). Over the years, the industry has gradually increased the size to improve efficiency and meet growing demands. Today, the common wafer size is 300 mm, which is 11.8 times larger than the original 1-inch wafers. This progression has been driven by the need to produce more chips per wafer, thereby reducing costs and increasing production capacity.
Technological Advancements Enabling Larger Wafers
Technological advancements have played a crucial role in enabling the production of larger wafers. Innovations in manufacturing processes and equipment have allowed for the transition from 200 mm wafers to the current standard of 300 mm. These advancements have not only improved the efficiency of semiconductor production but have also paved the way for future increases in wafer size.
Future Trends in Wafer Size
Looking ahead, the semiconductor industry is planning to move towards even larger wafer sizes. There is a clear plan to transition to 450 mm wafers, which are 1.5 times larger than the current 300 mm wafers. This shift is expected to further enhance production efficiency and meet the increasing demand for advanced semiconductor products.
Economic Implications of Wafer Size
Cost Efficiency of Larger Wafers
Larger wafers can significantly reduce the cost per chip. By shipping more parts in the same amount of time, manufacturers can improve efficiency. This cost efficiency is a strong argument for adopting larger wafer sizes in the semiconductor industry.
Investment in Wafer Size Upgrades
Increasing wafer size is not a simple process. It requires re-engineering silicon wafer manufacturing technologies, which involves substantial capital investment. The amount of money invested in this innovation is estimated to be in the triple-digit billion USD range.
Market Demand and Wafer Size
The number of die per wafer is directly related to wafer size. This relationship allows semiconductor design houses to estimate cost reductions. However, companies must carefully weigh the benefits and drawbacks of using different wafer sizes from a commercial standpoint. The semiconductor silicon wafer market is expected to reach USD 13.93 billion in 2024 and grow at a CAGR of 3.82% to reach USD 16.81 billion by 2029.
Wafer Size and Manufacturing Efficiency
Yield Improvement with Larger Wafers
Larger wafers can produce more chips, which means higher efficiency for manufacturers. This is because the edge of the wafer has less wasted material, reducing extra costs. More chips per wafer also means fewer wafers are needed, saving time and resources.
Production Speed and Wafer Size
With bigger wafers, manufacturers can ship more parts in the same amount of time. This boosts productivity and can make the whole process more economical. The key is to balance the cost of upgrading to larger wafers with the benefits they bring.
Challenges in Scaling Up Wafer Size
Scaling up wafer size isn’t easy. Manufacturers need to plan years in advance to support new wafer sizes. The main challenge is the expense of setting up new processes for each upgrade. Despite these challenges, the industry continues to push for larger wafers to meet growing demand.
Impact of Wafer Size on Device Performance
Electrical Characteristics and Wafer Size
The size of a wafer can significantly influence the electrical properties of the devices made from it. Larger wafers often lead to better performance due to the ability to produce more devices from a single wafer, which enhances productivity and efficiency. This is crucial for supporting the high volume of modern electronics like smartphones and tablets.
Thermal Management in Different Wafer Sizes
Thermal management becomes more challenging as wafer size increases. Larger wafers tend to generate more heat, which can affect the overall performance and reliability of the semiconductor devices. Effective cooling solutions are essential to maintain optimal device function.
Reliability and Wafer Size
Reliability is another critical factor impacted by wafer size. Larger wafers can sometimes lead to more defects, which can compromise the quality and longevity of the devices. Therefore, precise measurement and analysis, known as wafer metrology, are vital to ensure the quality and performance of semiconductor wafers.
Technological Challenges in Increasing Wafer Size
Material Quality and Wafer Size
Increasing wafer size is not a simple task. Silicon wafer manufacturing technologies had to be re-engineered to achieve the necessary advancements. Ensuring high material quality becomes more challenging as the wafer size grows. Even minor defects can lead to significant issues in larger wafers, affecting overall yield and performance.
Equipment and Infrastructure Requirements
Larger wafers require specialized equipment and infrastructure. Existing semiconductor manufacturing facilities must invest heavily in new machinery and tools to handle bigger wafers. This includes everything from wafer handling systems to inspection tools. The cost of upgrading these facilities can be enormous, often reaching billions of dollars.
Process Optimization for Larger Wafers
Optimizing manufacturing processes for larger wafers is crucial. This involves fine-tuning every step, from wafer slicing to final inspection. The complexity of these processes increases with wafer size, requiring advanced techniques and technologies. Manufacturers must continuously innovate to maintain efficiency and yield rates while scaling up wafer sizes.
Environmental and Sustainability Considerations
Resource Utilization in Wafer Production
Semiconductor production requires a significant amount of energy and resources, with a non-negligible environmental impact. The industry must focus on using materials more efficiently to reduce waste and conserve resources. Innovations in recycling and reusing materials can help lessen the environmental footprint of wafer production.
Waste Management and Larger Wafers
As wafer sizes increase, so does the potential for waste. Effective waste management strategies are essential to handle the by-products of semiconductor manufacturing. Companies are investing in technologies to recycle and repurpose waste materials, aiming to minimize their environmental impact.
Energy Consumption and Wafer Size
Larger wafers can lead to higher energy consumption during production. However, advancements in manufacturing processes can help offset this increase. By optimizing energy use and incorporating renewable energy sources, the industry can work towards more sustainable production methods.
Market Dynamics and Wafer Size
Consumer Electronics and Wafer Size
The consumer electronics market is a major driver for changes in wafer size. As devices become more advanced, the demand for larger wafers increases to support higher performance and efficiency. This trend is evident in the rapid growth of the semiconductor back-end equipment market, which is expected to grow at a CAGR of 8.11%, reaching a market size of US$148.756 billion in 2029 from US$86.193 billion.
Automotive Industry Needs
The automotive industry also plays a significant role in the dynamics of wafer size. Modern vehicles require more sophisticated electronics, which in turn demands larger wafers for better performance and reliability. This shift is crucial as the industry moves towards electric and autonomous vehicles, which rely heavily on advanced semiconductor technologies.
Emerging Technologies and Wafer Size
Emerging technologies such as 5G, IoT, and AI are pushing the boundaries of what is possible with current wafer sizes. These technologies require more powerful and efficient semiconductors, which can be achieved through the use of larger wafers. As a result, the industry is continuously investing in research and development to support the transition to larger wafer sizes.
Conclusion
In summary, wafer size plays a crucial role in the semiconductor industry. Larger wafers allow for the production of more semiconductor devices from a single wafer, boosting both productivity and efficiency. This is essential for meeting the high demand for modern electronics like smartphones, tablets, and PCs. However, increasing wafer size is not a simple task; it requires significant investment and technological advancements. As the industry continues to evolve, understanding the impact of wafer size will remain vital for future innovations and manufacturing processes.
Frequently Asked Questions
Why is wafer size important in semiconductor manufacturing?
Larger wafers mean more chips can be made from a single wafer, which boosts productivity and efficiency. If we still used small wafers, we couldn’t keep up with the demand for gadgets like smartphones and tablets.
What are the common wafer sizes used today?
Today, the most common wafer size is 300mm. In the past, wafers were much smaller, but there’s a plan to move towards even larger sizes, like 450mm.
How does wafer size impact the cost of semiconductor production?
Bigger wafers help reduce costs because more chips can be produced at once. However, upgrading to larger wafers requires a big investment in new equipment and technology.
What are the challenges of increasing wafer size?
Making larger wafers isn’t easy. It needs better materials, advanced equipment, and optimized processes. Plus, it costs a lot of money to make these changes.
Does wafer size affect the performance of semiconductor devices?
Yes, wafer size can impact the electrical characteristics, thermal management, and reliability of the devices made from them. Larger wafers generally lead to better performance.
How does wafer size relate to environmental sustainability?
Larger wafers can be more efficient, using fewer resources per chip. However, the production process for larger wafers can also consume more energy and create more waste.