Understanding the Semiconductor Process: A Comprehensive Guide
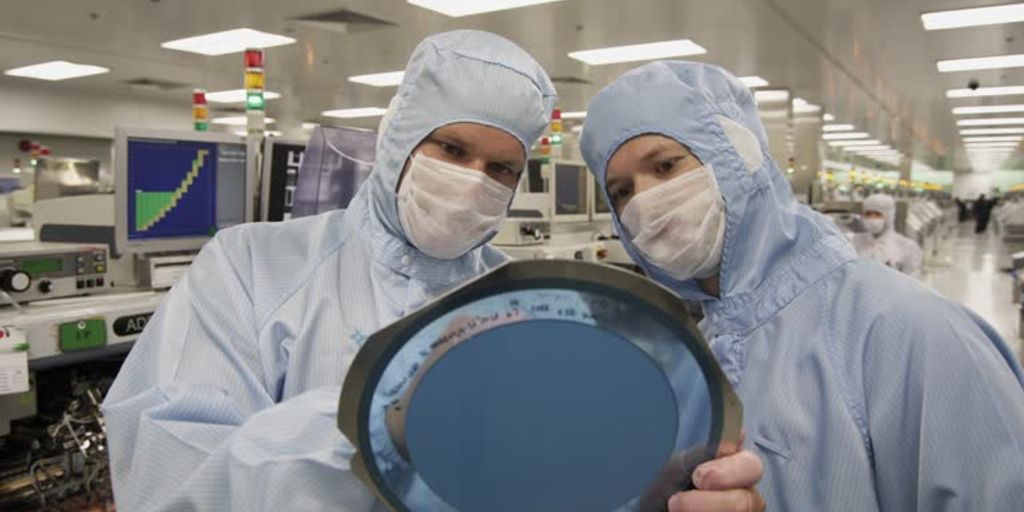
Semiconductors are at the heart of almost every electronic device we use today, from smartphones to computers. They are tiny but incredibly powerful. Understanding how they are made can help us appreciate the technology that shapes our world. This guide will take you through the whole process of making semiconductors, from the basic materials to the final testing and packaging.
Key Takeaways
- Semiconductors are essential for modern electronics, found in devices like phones and computers.
- The process of making semiconductors involves many steps, starting from raw materials.
- Special techniques like doping and lithography are used to create the tiny structures inside semiconductors.
- Quality control and testing are crucial to ensure semiconductors work correctly.
- Understanding semiconductor manufacturing helps us appreciate the technology in our everyday devices.
Fundamentals of Semiconductor Materials
Before diving into the complex world of semiconductor fabrication, it is essential to have a solid understanding of the basic properties of semiconductors. Semiconductors are materials that exhibit properties between conductors and insulators. Silicon is the most commonly used semiconductor material due to its abundance and favorable electrical characteristics. In a semiconductor, the ability to conduct electricity can be controlled, making them essential for electronic applications.
Crystal Growth and Wafer Preparation
Crystal growth is the process of making a large, high-quality semiconductor crystal, which is the starting material for wafer production. For silicon-based devices, the most common method of crystal growth is the Czochralski process. This involves melting high-purity silicon in a crucible and cooling it to a temperature near the freezing point. The process starts with the development of a crystal silicon ingot.
Methods of Crystal Growth
Other methods for crystal growth include the Bridgman-Stockbarger method, which involves slowly cooling a molten semiconductor material in a controlled environment. The Float Zone method is another method particularly useful for producing very high-purity silicon crystals.
Wafer Slicing and Polishing
Wafer preparation is a critical initial step in the semiconductor fabrication process, as it lays the foundation for creating high-quality electronic devices. The process involves transforming a semiconductor crystal, such as silicon or gallium arsenide, into a thin-flat wafer with an extremely smooth surface. This section will delve into the various stages of wafer preparation, including crystal growth, wafer slicing, polishing, and cleaning.
Contamination Control
In conclusion, wafer preparation is a critical step in the semiconductor fabrication process, as it lays the groundwork for creating high-quality electronic devices. By carefully controlling the crystal growth, wafer slicing, polishing, and cleaning processes, manufacturers can ensure that their wafers meet the stringent requirements necessary for the production of reliable, high-performance semiconductor devices.
Layer Deposition Techniques
Layer deposition is the process of adding thin layers of material onto the wafer’s surface. This step is crucial in forming the various layers needed for semiconductor devices. There are several methods used to achieve this, each with its own advantages and applications.
Lithography and Patterning
Photolithography Process
In the semiconductor materials industry, photolithography is a crucial technology for creating intricate electronic circuits. The process starts with applying a light-sensitive material called a photoresist onto the silicon dioxide layer. The photoresist is then exposed to ultraviolet light through a mask with the circuit pattern. This exposure causes the photoresist to harden in the pattern of the mask. Afterward, the unexposed photoresist is washed away, leaving behind the desired circuit pattern on the wafer.
Next-Generation Lithography Techniques
As technology advances, new lithography techniques are being developed to create even smaller and more complex patterns. These next-generation methods include extreme ultraviolet (EUV) lithography and electron beam lithography. EUV lithography uses light with a very short wavelength to achieve higher resolution, while electron beam lithography employs a focused beam of electrons to draw patterns directly onto the wafer. These advanced techniques are essential for producing the next generation of semiconductor devices.
Etching Methods
Once the pattern is created on the wafer, etching is used to remove the unwanted material. There are two main types of etching: wet etching and dry etching. Wet etching involves using liquid chemicals to dissolve the unwanted material, while dry etching uses gases or plasmas. Both methods have their advantages and are chosen based on the specific requirements of the semiconductor manufacturing process.
Doping and Ion Implantation
Doping and ion implantation are essential steps in making semiconductors. They help create n-type and p-type regions in the device. Doping means adding impurities, or dopants, to the semiconductor material, which changes its electrical properties. These impurities can be trivalent or pentavalent.
Diffusion Process
Before the ion implanter, doping was achieved by diffusion. This method involves heating the semiconductor material and allowing the dopant atoms to spread out and embed themselves in the crystal lattice. However, this process can lead to variations in the turn-on voltage of the transistors produced, requiring sorting.
Ion Implantation Techniques
Ion implantation is a popular doping method that involves bombarding the wafer with a beam of ions. The ions are accelerated and directed toward the wafer surface, where they penetrate and embed themselves in the crystal lattice. This technique offers several advantages:
- Precise control over dopant concentration and depth
- Uniform dopant distribution across the wafer surface
- Low-temperature processing, reducing the risk of wafer damage
However, ion implantation can also damage the crystal lattice, which must be repaired through a subsequent annealing process.
Annealing and Activation
After ion implantation, the wafer undergoes annealing to repair any damage to the crystal lattice and activate the dopants. This process involves heating the wafer to a high temperature, allowing the crystal lattice to heal and the dopant atoms to move into their proper positions. Annealing ensures that the electrical properties of the semiconductor material are restored and optimized.
Metallization and Interconnects
Metallization and interconnects are vital parts of semiconductor devices. They create the electrical paths that link different parts of an integrated circuit. These paths allow electrical signals and power to move between transistors, resistors, capacitors, and other components on the wafer. Choosing the right materials and deposition methods is key to making these connections work well. Let’s explore the main aspects of metallization and interconnects, including the methods used to deposit metals, the use of copper, and the materials that act as barriers and liners.
Metal Deposition Methods
Metallization involves placing metal layers on the wafer’s surface to form electrical connections. This can be done using different techniques like sputtering or Chemical Vapor Deposition (CVD). After the metal layers are added, they are patterned and etched to create the needed interconnect structures.
Copper Interconnects
Copper is often used for interconnects because it has low electrical resistance and high reliability. This makes it a good choice for creating efficient and long-lasting connections in semiconductor devices.
Barrier and Liner Materials
Barrier and liner materials are used to prevent copper from diffusing into other parts of the semiconductor device. These materials help maintain the integrity and performance of the interconnects. Common barrier materials include tantalum and titanium nitride.
Final Testing and Packaging
The final stage in semiconductor manufacturing is packaging. This step involves cutting the completed wafer into individual chips. Each chip is then mounted, interconnected, and enclosed in a protective housing. This packaging not only shields the chip from physical harm but also provides electrical connections to external circuits.
Electrical Testing
After packaging, chips undergo final testing to ensure they are still functional and have survived the packaging process. They are tested under various conditions, such as temperature and humidity, to ensure reliability. If the chip is part of a larger system on a chip (SoC), it might go through functional testing where all subsystems are checked for correct operation.
Packaging Techniques
Packaging semiconductors involves several steps:
- Die singulation: Cutting the individual dies from the wafer.
- Die bonding: Attaching the die to a substrate or lead frame.
- Wire bonding or flip-chip bonding: Connecting the die’s electrical contacts to the package leads.
Reliability and Quality Control
The electrical die sorting (EDS) process performs quality checks and tests the manufactured semiconductor for reliability. This final check eliminates faults inside the wafer. The foundry then sends the packaged device to the selling unit, eventually reaching consumers. By carefully selecting the right materials and techniques, manufacturers can ensure the chips are reliable and high-performing.
Conclusion
In wrapping up, we’ve taken a detailed journey through the world of semiconductor processing. From the basics of what semiconductors are to the intricate steps involved in their fabrication, it’s clear that these tiny components are the backbone of modern technology. Understanding this process not only highlights the incredible engineering feats achieved but also underscores the importance of precision and innovation in the electronics industry. Whether you’re a student, a professional, or just curious, we hope this guide has provided valuable insights into the fascinating realm of semiconductor manufacturing.
Frequently Asked Questions
What is a semiconductor?
A semiconductor is a material that can conduct electricity under certain conditions, making it a good medium for controlling electrical current. Silicon is the most commonly used material.
Why is silicon used in semiconductors?
Silicon is used because it is abundant, cost-effective, and has ideal electrical properties for making semiconductors. It can also be easily doped to change its electrical properties.
What is doping in semiconductors?
Doping involves adding small amounts of other elements to a semiconductor to change its electrical properties. This process helps control the flow of electricity in devices.
How are semiconductor wafers made?
Semiconductor wafers are made through a process that includes crystal growth, slicing the crystal into thin wafers, and polishing them to create a smooth, flat surface.
What is photolithography?
Photolithography is a process used to transfer patterns onto a semiconductor wafer. It involves using light to etch specific designs onto the surface, which are then used to create electronic circuits.
Why is contamination control important in semiconductor manufacturing?
Contamination control is crucial because even tiny particles can ruin a semiconductor. Keeping the manufacturing environment clean ensures the quality and reliability of the final product.