Understanding Wafer Burn-In Processes: Ensuring Chip Reliability
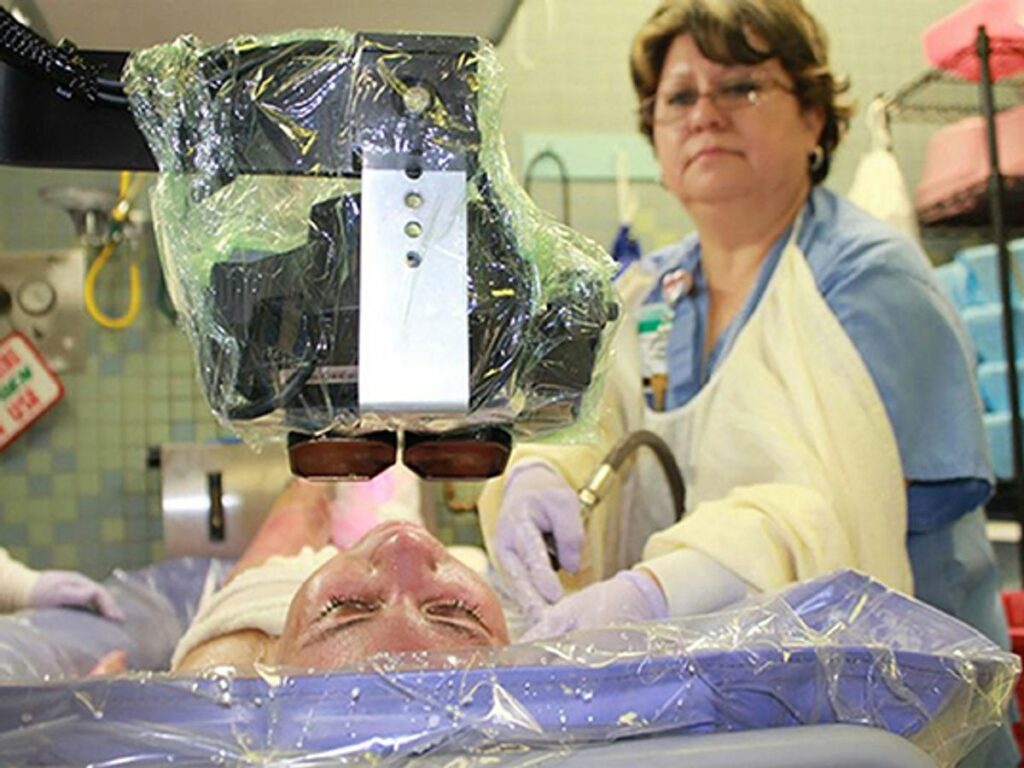
The relentless pursuit of chip reliability and efficiency has led to significant advancements in semiconductor manufacturing and packaging techniques. Among these, the wafer burn-in process stands out as a critical step in ensuring the longevity and performance of chips. This article delves into the intricacies of the burn-in process, explores the innovative realm of Photonic Wire Bonding (PWB), and addresses the challenges in photonic packaging. We’ll also examine the pivotal role of Photonic Integrated Circuits (PICs) in system assembly, highlighting current developments and future prospects in the field.
Key Takeaways
- Wafer burn-in processes are essential for verifying the reliability of chips, simulating early-life failures to enhance long-term performance.
- Photonic Wire Bonding (PWB) emerges as a groundbreaking technique in optical packaging, offering low-loss, high-bandwidth, and robust connections at low temperatures.
- Advanced 3D nano-printing technology enables fully automated PWB, fostering design flexibility and scalability in photonic packaging.
- Photonic Integrated Circuits (PICs) are becoming increasingly important in optics and photonics, with scalable packaging being a key factor for commercial adoption.
- Innovations in burn-in techniques and photonic packaging, such as the use of the POET Optical Interposer, are driving down costs and improving integration in high-growth areas like Artificial Intelligence.
The Role of Burn-In Processes in Chip Reliability
Understanding the Importance of Burn-In Testing
Burn-in testing is a critical step in the semiconductor manufacturing process, aimed at ensuring the reliability and longevity of chips before they are deployed in the field. Burn-In Testing exposes chips to stress conditions, such as high temperatures and voltage, to weed out early failures. This preemptive measure is crucial for identifying potential defects that could lead to premature failure in real-world applications.
The process involves several stages, each designed to simulate different stress scenarios that a chip might encounter during its lifecycle. Here’s a brief overview of the typical burn-in testing procedure:
- Initial inspection and preparation of the wafer or chip.
- Application of electrical and thermal stress to accelerate potential failure mechanisms.
- Continuous monitoring of electrical parameters to detect any signs of degradation or failure.
- Final evaluation of the chip’s performance post-stress testing.
The results from semiconductor testing are invaluable, providing insights into the robustness of the chip design and the effectiveness of the manufacturing process. By identifying and eliminating early-life failures, manufacturers can significantly improve the overall quality and reliability of their products.
Evaluating the Impact on Long-Term Performance
The long-term performance of semiconductor chips is a critical factor in determining their reliability and lifespan. Burn-in processes are essential in identifying early-life failures, ensuring that only robust and enduring chips make it to market. These processes subject chips to extreme conditions to accelerate potential failures, providing valuable data on their longevity.
Repeated experiments have shown that burn-in testing can significantly improve the metrics of precision, recall, F1-score, and accuracy. The table below summarizes the results of ten repeated experiments for a proposed framework, demonstrating the reproducibility and effectiveness of the burn-in process:
Experiment Index | Precision (%) | Recall (%) | F1-Score (%) | Accuracy (%) |
---|---|---|---|---|
1 | 95.94 | 95.98 | 95.99 | 96.55 |
2 | 94.15 | 95.88 | 94.99 | 96.41 |
3 | 94.95 | 95.78 | 95.38 | 96.58 |
4 | 95.35 | 94.97 | 95.18 | 96.66 |
5 | 93.79 | 94.83 | 94.43 | 95.97 |
6 | 95.41 | 95.79 | 95.58 | 95.31 |
7 | 96.12 | 96.26 | 96.16 | 97.92 |
8 | 94.99 | 95.52 | 95.39 | 96.96 |
9 | 91.96 | 91.44 | 91.98 | 94.96 |
10 | 95.74 | 95.85 | 95.81 | 97.89 |
The average performance across these experiments approaches 94.84% for precision, 95.23% for recall, 94.93% for F1-score, and 96.52% for accuracy. This consistency underscores the importance of burn-in testing in predicting and enhancing the long-term performance of semiconductor devices.
Advancements in Burn-In Techniques for Enhanced Reliability
The semiconductor industry is witnessing significant advancements in burn-in techniques, aiming to enhance the reliability of chips before they are deployed in the field. Wafer-level test and burn-in is one such advancement that has gained traction, particularly for its ability to screen for early-life failures and ensure the excellence of semiconductor devices. This method is not only crucial for quality assurance but also for maintaining the high standards expected in today’s technology-driven world.
Recent innovations in burn-in processes have focused on improving efficiency and reducing costs while maximizing the detection of potential defects. For instance, the integration of advanced algorithms and machine learning techniques has led to smarter and faster testing procedures. These improvements are pivotal for the industry, especially as chips become more complex and the demand for reliability intensifies.
To illustrate the progress in burn-in techniques, consider the following table showcasing the comparison between traditional and advanced methods:
Technique | Detection Speed | Cost Efficiency | Reliability Improvement |
---|---|---|---|
Traditional | Moderate | Low | Significant |
Advanced | High | High | Very Significant |
The table highlights the strides made in enhancing the speed of defect detection, the cost efficiency of the process, and the overall improvement in chip reliability. As the industry continues to evolve, these advancements in burn-in techniques will play a crucial role in maintaining the trust and confidence of consumers and businesses alike.
Innovations in Photonic Wire Bonding (PWB)
The Emergence of PWB in Optical Packaging
Photonic Wire Bonding (PWB) represents a significant leap forward in the field of optical packaging. Built on advanced 3D nano-printing technology, PWB offers a fully automated process that enhances design flexibility and addresses the complex packaging requirements of various photonic devices. The technology has been instrumental in creating low-loss, 3D free-form connections between optical components, akin to the role of electronic wire bonding in electrical integrated circuits.
The rapid growth of photonic integrated circuits has necessitated innovations like PWB, which enable low insertion loss for critical connections such as laser-to-chip and fiber-to-chip integration. PWB’s ability to operate at low temperatures with high bandwidth and mechanical robustness further underscores its potential. This method significantly reduces the alignment challenges typically encountered during assembly and thermal cycling, making it a versatile solution for a wide range of applications.
Key features of PWB include:
- Low-loss, flexible interconnections
- High bandwidth and mechanical robustness
- Compatibility with ultra-high vacuum and vacuum bakeout
- Resilience to thermal cycling
These attributes make PWB a promising technique for the future of photonic integration, where reliability and efficiency are paramount.
Advantages of PWB for Chip-to-Chip Connections
Photonic Wire Bonding (PWB) is revolutionizing the way we approach optical interconnects in chip-to-chip connections. Built on advanced 3D nano-printing technology, PWB offers a fully automated process that enhances design flexibility and integration capabilities. This technology has been pivotal in addressing the complex packaging requirements of various architectures, including neuromorphic photonic accelerators.
The inherent advantages of PWB are numerous. Here are some key benefits:
- Low insertion loss: PWBs create efficient connections with minimal signal degradation.
- High bandwidth: These interconnections support high data transfer rates, essential for modern applications.
- Mechanical robustness: PWBs are durable and can withstand thermal cycling and other environmental stresses.
- Design flexibility: The 3D nano-printing base allows for intricate and custom designs.
Moreover, PWB has shown promising results in extreme conditions such as cryogenic temperatures, where it maintains low loss and high performance. This capability is critical for applications that require operation in harsh environments, making PWB a versatile solution for a wide range of applications.
PWB’s Role in the Future of Photonic Integration
Photonic Wire Bonding (PWB) is poised to play a pivotal role in the evolution of photonic integration, offering a bridge between the diverse components that make up complex photonic systems. Built on advanced 3D nano-printing technology, PWB enables low-loss, 3D free-form connections that are essential for the next generation of silicon photonics. This technology not only facilitates laser-to-chip and fiber-to-chip integration but also meets the intricate packaging demands of cutting-edge applications like neuromorphic photonic accelerators.
The inherent automation and design flexibility of PWB are crucial for scaling up photonic integration. As the technology matures, we can expect to see a broader adoption in various domains, including WDM communications, where PWBs merge the unique benefits of different photonic platforms. For instance, combining DFB lasers on InP substrates with SiP chips for electro-optic modulators and TriPleX material systems for AWGs, PWBs enable dense packing of optical channels, which is vital for high-bandwidth communication systems.
The future of PWB in photonic integration is not just about enhancing current capabilities but also about unlocking new possibilities. As passive alignment packaging techniques evolve, PWB stands out as a promising alternative that leverages computer vision and automation to streamline the assembly process. The table below summarizes the key advantages of PWB in photonic integration:
Feature | Advantage |
---|---|
Low Insertion Loss | Ensures efficient signal transmission |
Design Flexibility | Accommodates complex geometries |
Automation | Reduces human error and increases throughput |
Hybrid Integration | Facilitates the combination of different photonic materials |
Embracing PWB will be instrumental in roadmapping the future of photonic technologies, where reliability, efficiency, and scalability are paramount.
Challenges and Solutions in Photonic Packaging
Overcoming Alignment Issues in Chip Assembly
The assembly of photonic integrated circuits (PICs) is a critical step in the manufacturing process, with alignment being a particularly challenging aspect. Automated alignment systems have emerged as a solution to these challenges, significantly reducing the time required for alignment. These systems utilize advanced algorithms and mechanics to streamline the process, making it more efficient and cost-effective.
Active alignment techniques, which are essential for optimizing coupling efficiency during assembly, have traditionally led to complex and costly processes. However, recent innovations, such as 3D-printed facet-attached microlenses (FaML), are paving the way for simpler and more scalable solutions. These advancements allow for relaxed alignment tolerances and the use of passive assembly techniques, which are more conducive to high-volume production.
The table below summarizes the benefits of using automated and passive alignment methods compared to traditional active alignment techniques:
Technique | Alignment Time | Cost | Scalability |
---|---|---|---|
Active Alignment | High | High | Low |
Automated Alignment | Low | Medium | High |
Passive Alignment (e.g., FaML) | Low | Low | High |
By adopting these innovative approaches, manufacturers can overcome the alignment hurdles in chip assembly, leading to more efficient production and ultimately, more reliable photonic devices.
Cryogenic Optical Packaging and Its Advantages
Cryogenic optical packaging, particularly when integrated with Photonic Wire Bonding (PWB), presents a transformative approach to optical connections. The use of PWB at cryogenic temperatures has been shown to maintain low loss, high bandwidth, and mechanical robustness, which are critical for reliable performance in extreme conditions. This method significantly reduces the alignment challenges typically encountered during assembly and cooldown in traditional packaging techniques.
The advantages of cryogenic optical packaging extend to its compatibility with ultra-high vacuum (UHV) and its resilience to thermal cycling, making it a versatile solution for a variety of applications. Notably, the integration of PWB in cryogenic environments addresses the unresolved challenge of efficiently coupling single photons into a defined optical mode at low temperatures, a key factor in advancing optical computing.
Feature | Benefit |
---|---|
Low Temperature Operation | Enables efficient photon coupling |
Mechanical Robustness | Withstands thermal cycling and extreme conditions |
High Bandwidth | Supports fast computation and data transfer |
UHV Compatibility | Suitable for a wide range of applications |
The POET Optical Interposer, leveraging advanced wafer-level semiconductor manufacturing, offers a cost-efficient alternative to conventional high-precision alignment techniques. This innovation is poised to bring significant value to high-growth computing areas, such as Artificial Intelligence, by harnessing the speed advantages of optical computing.
Automated Processes for Scalable Photonic Packaging
The advent of automated processes in photonic packaging is revolutionizing the industry, enabling scalable production that keeps pace with the growing demand for photonic integrated circuits (PICs). Automation not only streamlines the assembly process but also enhances precision and repeatability, which are critical for high-performance optical systems.
One of the key technologies in this domain is Photonic Wire Bonding (PWB), a technique that leverages advanced nano-printing technology for creating low-loss connections between optical components. PWB is a fully automated process, offering high packaging density and design flexibility, which are essential for multi-chip integration. Vanguard Automation is at the forefront of this technology, developing process technology and software-defined manufacturing equipment that is compatible with industry simulation software.
The table below summarizes the benefits of automated photonic packaging processes:
Benefit | Description |
---|---|
Scalability | Facilitates wafer-level mass production of PICs. |
Precision | Ensures accurate alignment and connection of optical components. |
Repeatability | Delivers consistent quality across high-volume production. |
Flexibility | Allows for complex designs and customizations. |
Throughput | Increases production speed and efficiency. |
As the industry continues to evolve, the integration of automated processes like PWB will be pivotal in overcoming the challenges of photonic packaging and ensuring the successful commercial adoption of PIC-based solutions.
Photonic Integrated Circuits (PICs) and System Assembly
The Importance of PICs in Modern Optics and Photonics
Photonic Integrated Circuits (PICs) have become a cornerstone in the realm of modern optics and photonics, revolutionizing the way light is manipulated and utilized. New research shows how light propagates in integrated circuits, offering insights into the miniaturization and integration of photonic elements. This miniaturization is crucial for developing compact photonic chips that carry light with high efficiency and precision.
The integration of PICs into various applications has been disruptive, yet the transition to wafer-level mass production poses significant challenges. Scalable photonic packaging and system assembly are critical hurdles that need to be overcome to enable widespread commercial adoption of PIC-based technologies. The field is rapidly evolving, with innovations such as Photonic Wire Bonding emerging as promising solutions to these challenges.
PICs are set to expand across multiple end markets in the coming years. As such, the industry is prioritizing the development of efficient packaging techniques for photonic chiplet systems. Below is a list of key areas where PICs are making an impact:
- Data centers and telecommunications
- Artificial intelligence and computing
- Medical diagnostics and biosensing
- Quantum computing and information processing
The integration of micro-optical elements, such as polarization beam splitters and ultra-low back-reflection interfaces, is enhancing the functionality of PICs. These advancements pave the way for novel system architectures that leverage the distinct advantages of different photonic integration platforms.
Scalable Packaging Techniques for Commercial Adoption
The commercial adoption of Photonic Integrated Circuits (PICs) hinges on the development of scalable packaging techniques that can accommodate the demands of mass production. Wafer-level mass production has become a cornerstone in the optics and photonics industry, yet the transition from prototype to high-volume manufacturing is fraught with challenges. One of the primary hurdles is the need for active alignment in chip-to-chip and fiber-to-chip connections, which can be labor-intensive and difficult to automate.
To address these challenges, industry leaders are exploring innovative solutions. For example, Vanguard Automation’s decision to rebuild their clean room to tailor packaging processes to customer-specific devices exemplifies the industry’s commitment to scalability. Moreover, the integration of advanced technologies such as the CNN–Transformer interaction model for automatic identification of packaging materials underscores the push towards automation and efficiency.
The following table highlights key scalable packaging techniques and their respective benefits:
Technique | Benefit |
---|---|
In situ 3D nanolithography | Enables hybrid multi-chip assembly |
Automated alignment | Reduces labor and increases throughput |
CNN–Transformer model | Enhances reliability through precise material identification |
As the industry continues to innovate, these scalable packaging techniques are expected to pave the way for broader commercial adoption of PIC-based solutions, ensuring that the benefits of photonic integration can be realized across a spectrum of applications.
Environmental Stability and High-Power Resilience of PICs
The integration of Photonic Integrated Circuits (PICs) into various applications necessitates a focus on environmental stability and the ability to withstand high-power conditions. These factors are critical for the reliable operation of PICs in harsh or demanding environments, such as those encountered in industrial or outdoor settings.
To ensure that PICs maintain their performance over time, several strategies have been employed. These include the use of robust packaging materials, the implementation of protective coatings, and the design of circuits that can tolerate temperature fluctuations and mechanical stress. Additionally, the development of PICs with high-power resilience is essential for applications that require intense light sources or high data transmission rates.
The table below summarizes the key attributes that contribute to the environmental stability and high-power resilience of PICs:
Attribute | Description |
---|---|
Material Selection | Utilization of materials that can withstand extreme temperatures and corrosive environments. |
Protective Coatings | Application of coatings to shield against moisture, dust, and other contaminants. |
Thermal Management | Design features that enable efficient heat dissipation. |
Mechanical Design | Structures that can endure physical stress without degrading performance. |
As the demand for PICs grows across various sectors, the ability to deliver systems that are both environmentally stable and capable of handling high-power applications will be a key differentiator for manufacturers.
Conclusion
The exploration of wafer burn-in processes and their critical role in ensuring chip reliability has highlighted the significance of advanced manufacturing and packaging techniques in the semiconductor industry. Innovations such as POET’s Optical Interposer and Photonic Wire Bonding (PWB) are revolutionizing the field by offering cost-efficient, scalable solutions that address the challenges of conventional photonics. These advancements not only improve alignment and thermal resilience but also enhance the environmental stability and optical performance of integrated circuits. As the demand for reliable micro- and nanomanufacturing grows, particularly in areas like Artificial Intelligence, the importance of robust IC packaging and efficient photonic integration cannot be overstated. The future of photonic multi-chip systems looks promising, with the potential for simplified assembly processes and the integration of diverse platforms. The continuous development of these technologies will be pivotal in meeting the evolving needs of the industry and maintaining the regular functions of manufacturing equipment.
Frequently Asked Questions
What is the purpose of wafer burn-in processes in semiconductor manufacturing?
Wafer burn-in processes are critical for ensuring the reliability of semiconductor chips. They involve testing chips at elevated temperatures and voltages to accelerate failure mechanisms and identify early-life failures, thus ensuring only robust chips are shipped to customers.
How do advancements in burn-in techniques improve chip reliability?
Advancements in burn-in techniques, such as the integration of electronics and photonics with the POET Optical Interposer, enhance reliability by reducing the need for costly components and labor-intensive testing, while ensuring scalable and cost-efficient integration.
What are the key benefits of Photonic Wire Bonding (PWB) in optical packaging?
PWB offers low loss, high bandwidth, and robust mechanical performance at low temperatures, which simplifies the assembly process and reduces alignment challenges. Its compatibility with various operating conditions makes it a versatile photonic packaging technique.
How does PWB contribute to the future of photonic integration?
PWB enables simplified assembly of advanced photonic multi-chip systems by combining the advantages of different integration platforms. Its resilience in environmental stability tests and at high optical power positions it as a key technology for future photonic integration.
What are the challenges in scalable photonic packaging for PICs, and how can they be addressed?
Scalable photonic packaging faces challenges like chip-to-chip and fiber-to-chip connections that require active alignment techniques. PWB addresses these challenges by allowing low-loss coupling with limited placement accuracy, thus promoting commercial adoption of PIC-based solutions.
Why is automated process important for the mass production of photonic integrated circuits?
Automated processes are crucial for the mass production of PICs as they provide high throughput, consistency, and precision, which are essential for scalable and cost-effective manufacturing of reliable photonic devices and systems.